Next-gen flexo platemaking explained
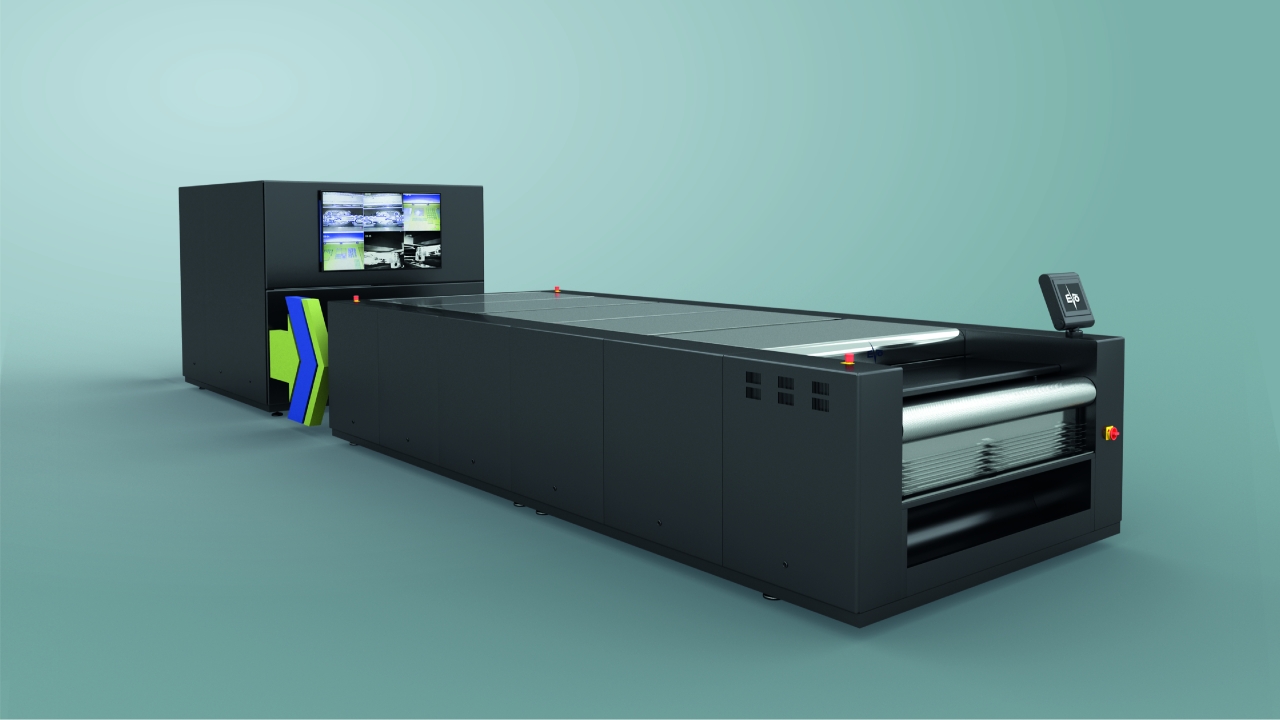
The Fourth Industrial Revolution is being driven by extreme automation and new forms of machine intelligence, and to stay ahead of the curve and turn opportunities into real business, flexographers must consider investment in more automated flexographic plate manufacturing technology that is less and less dependent on the skills of individuals.
In the past 20 years, technology has changed the nature of flexo platemaking. In the old days, flexo plates were all processed with basic electromechanical equipment. When, later, electronics penetrated the industry, flexo platemaking equipment also took advantage of it. Control systems were introduced to regulate processes and reduce the need for human intervention. Embryonic forms of automation started.
Now that computers, software, connectivity and technology have developed further, advanced robotic automation has set new standards for the industry. Advanced and fully automated flexo plate processing lines have been introduced enabling flexographers to produce plates at outstanding speeds and with great repeatability and quality.
Automation is the process of integrating processing equipment to automatically perform a variety of applications such as Imaging, exposing, punching, washing-out, drying, finishing, plate handling, storing, etc, all in one go. This is the fourth industrial revolution in practice – the rise of the flexo platemaking Internet of Things.
Globally, it is estimated that about 500 fully automated flexo platemaking lines will be installed before the end of 2020, with a current global market value estimated at around 500 million USD.
Investment considerations
Depending on the scale of operation, advanced robotic automation may or may not be a good fit. Optimally, it should be an operation with a larger facility with several operators on the shop floor processing medium-to-large quantities of plates per day. Low mix/high volume and high mix/low volume runs are another discriminating factor, with automated processing lines allowing a high degree of production flexibility.
A successful automated platemaking line will be fully modular, characterized by standard functional units equipped with built-in interfaces that can be joint together to build automated systems in different configurations by simply upgrading the software.
Always collaborate with a specialized integrator, using their expertise to discuss your plate processing system, the raw plates you are using and your expectations and requirements.
Understanding the advantages
There are many advantages of automation. At the simplest level, the plate processor automatically defines the wash-out parameters.
But by linking all the units and plate processing phases to each other, a whole range of manual tasks are automated, like reconfiguring the processing equipment (exposure, wash-out, dryer, etc) and transporting the plates from one unit to the next, which all waste a considerable amount of time and space.
A fully automated system decreases production time, gives better repeatability and less human error. In addition, fewer employees are required, and with lower skill levels. And skilled employees are freed up to concentrate on improving the customer’s experience.
There are also health and safety benefits. Solvents used to process flexo plates are organic chemicals that have a high vapor pressure at ordinary room temperature. That causes volatile organic compounds (VOCs), which can be eye and respiratory irritants. That is why adequate ventilation must be provided in the areas where processing solvents are used.
In any solvent processor, the plate absorbs solvent like a sponge. When the operator takes the plate to the dryer, the plate leaks solvent, inevitably releasing VOCs in the air. This potentially exposes operators to a hazardous situation. As a minimum, safety glasses or goggles and gloves should be worn when handling such plates and a face mask would also be indicated.
It is clear, therefore, that if a processor is physically connected and hermetically sealed to a dryer and stacker there will be much less VOC emission in the platemaking area.
Technology components
A key difference with traditional platemaking processes is the level of closed loop control. Traditional methods for recording process parameters to meet regulatory compliance relied on the manual set-up of electro-mechanical devices – motors, fans, heaters, etc. Each of them had multiple points of embedded mechanical and electrical potential malfunction. Today, devices can be sensed, measured and controlled from the PLC, using algorithms to optimize the whole process.
It is even possible to mount an inspection camera that offers a clear view inside the machine and other hard to reach areas normally hidden from sight, even for on-site technicians. With a solvent fume and scratch-resistant tempered glass lens and with high pixel resolution, specialized engineers sitting in a remote control-center at the equipment manufacturer can easily view all the critical processing steps for instant analysis and diagnosis.
Special attention should be paid to the physical installation of the network and its configuration to optimize data throughput and security. The use of commercial or industrial-grade network devices is highly recommended. Most consumer grade devices, such as wireless access points and routers, do not have the range, throughput, or security features typical of industrial-grade devices.
Another key benefit of modern advanced equipment is the embedded capability to ‘learn’ by interacting with the skills of human operators. It does not just expose, wash-out, dye and finish flexo plates, the system has the potential to learn how to optimize process parameters on the fly, a process called ‘evolutionary learning.’
In essence, advanced robotic automation enables trade shops and printers to minimize process tolerances, improve safety and quality standards, reduce mistakes, cut down on costs, and provides quicker payback of capital invested.
It became apparent that the true focus for benefit of advanced robotic automation is increasing the speed at which plates are processed, and making staff involved as efficient as possible. Multi-tasking and automation can easily increase productivity by 35 percent when compared with stand-alone devices (source :empowerims. com users’ market study and Flint Group ‘Automation & Standardisation’ publication). The ‘surprise’ benefit was that automation doesn’t mean trading speed for accuracy, as many suspected
This opinion article was printed in L&L issue 2, 2017
Stay up to date
Subscribe to the free Label News newsletter and receive the latest content every week. We'll never share your email address.