Mid-web automated flexo press competes with gravure
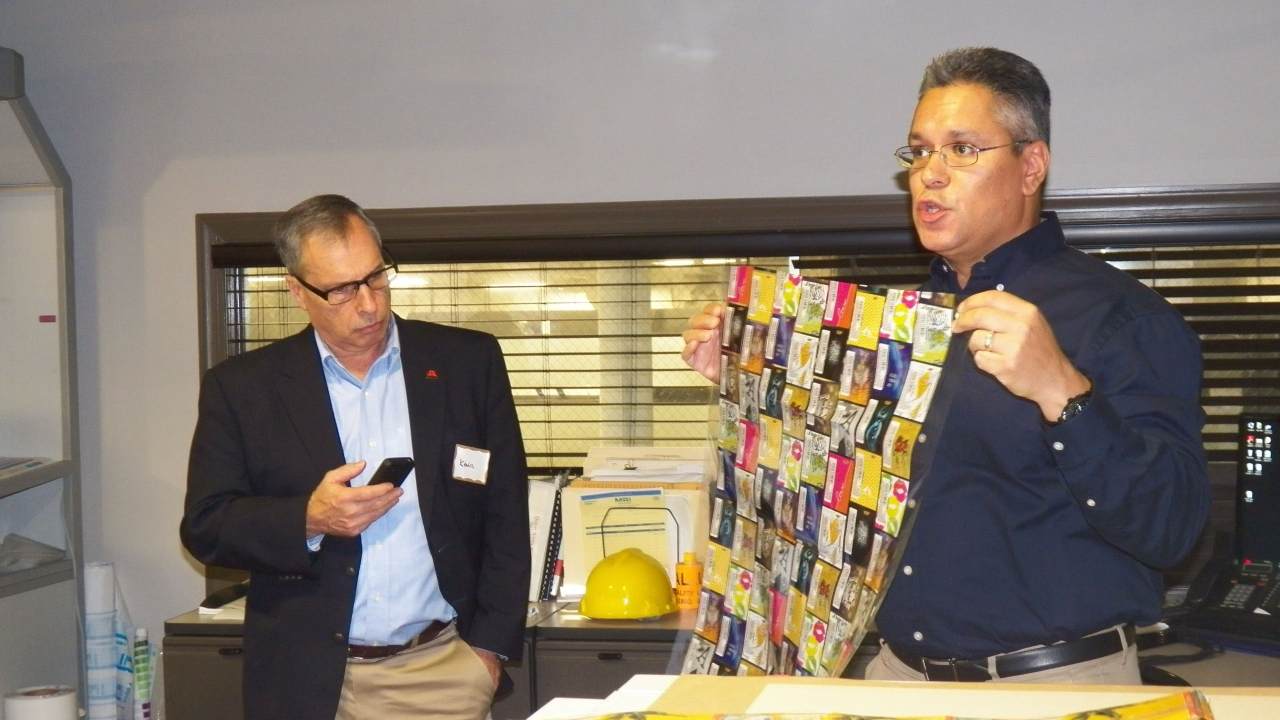
Leveraging years of experience in research, designing and engineering technology for imaging graphics, Eastman Kodak launched its digital printing plate system for flexography – Flexcel NX – nearly six years ago at Drupa 2008. Today Kodak has installed more than 300 of its Flexcel NX Systems for use in the manufacture of labels, cartons and flexible packaging.
Distinctive technology, controlled installation and process education has two of Kodak’s Pennsylvania-based users – a mid-web converter and a pre-press house – growing their business because of the quality return on their investments.
Emma Schlotthauer, global packaging marketing manager for Kodak says: ‘The Flexcel NX System gives users a technical competitive edge and delivers a compelling value proposition for the entire packaging supply chain. Brand owners will find more quality, consistency and predictability with suppliers that choose Kodak Flexcel NX technology.
‘The advanced process removes the traditional constraints of flexo printing giving designers more freedom to deliver the kind of pop and impact on-shelf they would normally expect from gravure printing.’
Distinctive Technology
The Kodak Flexcel NX System incorporates Kodak Squarespot imaging technology, taken from the offset CtP world, where Kodak has 16,000-plus devices installed on the commercial printing side. Combined with high resolution materials and a unique lamination process, the system generates Kodak Flexcel NX plates with exactly the intended image reproduction. It can also hold extremely small copy fonts in reverse.
The properties of the image-carrying mask have a great impact on the performance of printing plates. Kodak technology images a high-resolution, dye-based mask rather than the carbon mask, which is used in competitive digital plate production.
A unique lamination process eliminates the presence of oxygen in the platemaking process. This ensures a faithful reproduction on the plate of exactly what was on the mask, unlike competitive systems. The resultant tonal range is wide, delivering smooth image reproduction without the hard breaks often associated with flexo.
Additionally, the wide tonal range, combined with higher print densities allows printers to eliminate some spot colors and find efficiencies in reproduction with more process colors.
Imaging technology and unique plate surfacing technology is what really allowed the tech to move into flexible packaging market.
Dr John Anderson, Kodak’s packaging sales and product marketing director, explains that ‘the unique dot structure and the micro textured plate surface of the Flexcel NX Plate is what has driven the advancement of flexography as a printing process, and is what has allowed the technology to truly break into the flexible packaging market.’
Gravure quality flexo
MRI Flexible Packaging is based in Newtown, Pennsylvania, a suburb of Philadelphia. The converter produces stretch sleeve labels and polyethylene film wrap around labels for private label bleach, other household, beverage and industrial products, dairy and cat litter bottles. It also prints and slits large shrink wrap labels for big beer brand player Miller Coors and more.
Richard Speeney, managing director and co-owner of MRI Flexible Packaging, says: ‘Most of our growth has come from the shrink sleeve market, which, in the past, had chosen gravure. Using the Flexcel NX, we compete at gravure quality with the benefits of flexo. We’ve experienced double digit growth year-on-year these last few years.’
Kodak technology offers a more dimpled pattern on the top of the plate through the screening software Digicap NX. This helps greatly in the solids and tonal range through the highlights of the print, key elements required to play in the flexible packaging market.
Will Vasquez (pictured in second image on the carousel), senior project manager at MRI, says: ‘The plates offer pixel for pixel reproduction with outstanding ink transfer and surface patterns. The solid ink density prints stronger, more vibrant colors. We can print at a high line screen – 133, 150, 175 – to provide quality that matches the gravure world. The plate technology truly makes our shrink and other film labels stand out from the rest.’
The plate life of Kodak Flexcel NX has proven to extend beyond the plates MRI had used prior to the investment. Says Speeney: ‘Our old plates would swell after running and the fine vignette would disappear from the print. We’d be required to make new plates around 250,000 impressions. Now we’re able to use the plates for three times the impressions.’
A typical MRI customer requires more than 40 SKUs with eight or more colors. The converter averages around 15-16 changeovers per day, sometimes two in one run, and it preys on short-run gravure work.
In April 2012, MRI purchased the first Bobst F&K 20SIX central impression flexo press sold in North America. The 10-color, 1300mm (1.3m) wide machine allows MRI to run over 20 job changes per day. A 12,000 ft job running 1,000ft/min on the Bobst press takes 12-15 minutes to complete, including make-ready time.
The 20SIX is equipped with Bobst’s smartGPSTM. The GPS technology scans the print sleeve with the plate applied to create a topographical map by evaluating and recording the high and low spots on the plate. It automatically reads and writes the information that it obtains into an RFID chip embedded in the print sleeve. Once the sleeves are loaded, the press reads the chip to set registration and impression as directed.
This is extreme process automation. And this automated production extends through the front and back-end with a non-stop feed splice and non-stop unwinding system, and a self-cleaning ink system.
MRI’s older presses are 22in wide, just half the size of the new machine. With the Bobst, the converter is able to run two across.
Vasquez adds: ‘The technologies together give us more consistency throughout the press run and has helped us to knock some of the spot colors out of jobs. Our efficiency is greatly improved. We’ve eliminated traps with four-color process and are reviewing expanded gamut potential.’
Not to mention, the pre-press cost for flexography is a fraction of gravure. Also, the advancement in flexo technology serves as an opportunity for print to be more comparable to the widely adopted Indigo print, and does not require compensation for dot gain.
Speeney continues by saying that ‘these steps forward in flexographic technology arms us in the fight against gravure printing.
‘Many buyers see the cost opportunity and want to make the switch to flexo, but their marketing teams want to see print quality proven. We’re busy educating our customers on our advanced capability.
‘The gap between gravure and flexo gets smaller and smaller. Having the new Bobst press and the Kodak plate system allows us to make that gap non-existent.’
Plate house perspective
Jerry Toepfer is the president at Imageworx in Levittown, Pennsylvania. Toepfer gained his experience in the industry working as a technical rep for Dixie Graphics.
Imageworx is a pre-press house that produces digital printing plates for flexography and letterpress processes. It uses an Esko CDI Imager for DuPont and Asahi plate materials, and a Kodak Flexcel NX System to produce the Flexcel NX plate material.
Toepfer says: ‘Overall the weak link that narrow web printing has is their plates. The quality is a step behind from what it should be. We have a lot of relationships with the premier narrow web press companies.’
They key piece is understanding the differences between plates; a conventionally exposed photopolymer plate versus a Kodak plate. Toepfer explains that ‘you automatically make a bump curve in the old way of making plate.
‘If you send a file with 50 percent coverage, then you’re getting 36 percent. There’s a big difference in the out of file result that you get with a Kodak plate.’
Imageworx’ output break has already moved to be 85 percent Kodak with the hope of expanding into corrugated markets with a new wider Kodak imager.
Certification
Both Kodak customers agreed that the company has implemented a ‘flawless installation program’, ensuring reliable support with on-press issues from install through mature production. Kodak has also established a certification program for Flexcel NX clients. This proves that the plate maker is producing plates to the Kodak global standard, which makes production consistent and predictable.
To receive the Kodak Flexcel NX Certification mark, the plate producer must also have endorsements from the end customer. Already 60 of the 300 installations are in the process of achieving certification, while 20 customers are already certified.
This certification process insures that users are using the technology in the right way and is just one of many value added services with which Kodak support their customers
Imageworx achieved Kodak Certified Partner status just before the New Year. Toepfer says: ‘The Kodak system makes everything that happens with the plate making process easier and more consistent. You get an excellent result every single time.’
MRI’s Vasquez concludes: ‘It is a simple system. When you follow the procedures, you’ll make a great plate. It is an easier and more consistent workflow than other workflows, and it has improved our business.
‘The gap between gravure and flexo gets smaller and smaller. Having the new Bobst press and the Kodak plate system allows us to make that gap non-existent.’
Stay up to date
Subscribe to the free Label News newsletter and receive the latest content every week. We'll never share your email address.