Actega’s Ecoleaf completes beta testing
As EcoLeaf concludes its beta phase, L&L reports the updates and feedback from the technology
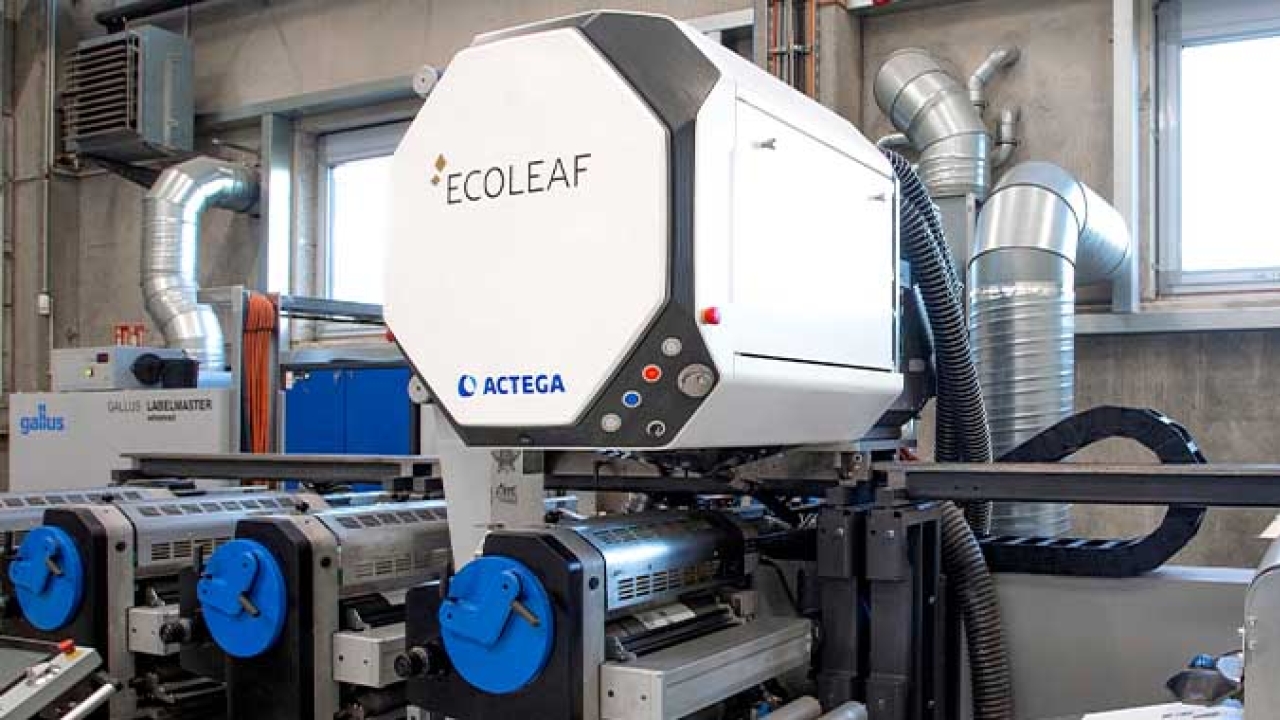
From its inception with Landa to its fulfillment with Actega, EcoLeaf is a technology five years in the making. L&L’s Piotr Wnuk covered the start of beta testing for EcoLeaf technology back in June 2020 and now L&L investigates what progress has been made and the initial feedback from early adopters.
The concept of EcoLeaf, originally called nano-metallography, was introduced at drupa in 2016 by Benny Landa. The highlights of this presentation included that this is a zero-waste technology (because a donor roll bonds to a trigger image with no wasted material), the metallization would be microwavable, and it can be paired with almost any printing process.
In 2017, Altana acquired the metallography technology from Landa Labs, taking responsibility for the remaining development and engineering work. This transfer was not unprecedented. In 2014, Altana and Landa Corporation concluded an equity financing agreement under which Altana pledged to invest 100 million EUR (135 million USD) for a minority stake in Landa Digital Printing. While Landa Labs was not included in the transaction, this investment cemented the relationship between Altana and Landa.
Actega is Altana’s division for packaging and printing, and within Actega the company formed its metal print division in 2017 after the acquisition of nano‑metallography. The company rebranded the
technology as Eco-Leaf and began beta testing in 2020.
Dario Urbinati, then the chief sales and marketing officer at Actega Metal Print, gave a presentation in February 2021 for FuturePrint’s virtual conference where he detailed that in spring 2021 Actega’s beta program had six installations in the EU. After adapting the technology to reflect feedback from beta testers, Actega plans to have commercial availability in the EU by Q3 2021. Commercial availability in the US is set to follow in 2022.
While there are exciting new projects for EcoLeaf, conventional hot foiling is still needed for many applications
Alongside the beta program, Actega has been developing EcoLeaf Digital. According to the company’s September 2020 newsletter, this is a modular printbar equipped with Ricoh Gen 5 inkjet heads which will allow digital metallization for print widths from 330 to 520mm with 1,200 DPI resolution. According to the company, ‘the print bar and the EcoLeaf Metallization Unit can be installed into any conventional, hybrid or digital printing equipment.’ The first EcoLeaf Digital system has been installed on an A B Graphic web transport system in Actega’s Competence Centre in Lehrte, Germany.
German print specialist Kolbe-Coloco Spezialdruck was the first company to invest in EcoLeaf in March 2020 and completed its beta program in spring 2021. Actega used the company’s feedback
to improve the EcoLeaf unit. ‘All new EcoLeaf systems now feature a cover that offers user friendly functionality, superior durability and a style that reflects the cutting-edge nature of the technology,’ says Actega.
EcoLeaf units are now being sold by A B Graphic International (ABG) in Europe, either installed on Digicon Series 3 digital finishing machines or retrofitted to existing presses in the field. ABG will
handle direct sales, marketing and customer service for EcoLeaf in the EU and UK.
German printer Vollherbst was the first company to purchase an Ecoleaf Unit from ABG after the partnership with Actega was announced. The EcoLeaf unit was installed on the company’s A B Graphic Digicon Series 3 converting machine. L&L sat down with Matthias Vollherbst, managing owner at Vollherbst, to get his feedback as an early adaptor of EcoLeaf.
Interview with Vollherbst
L&L: What types of products are you decorating with EcoLeaf?
MV: We decided to closely collaborate with our key clients during EcoLeaf’s beta phase in order to allow the highest transparency, direct feedback and a high speed of learning. These close contacts of ours mainly operate in the wine and spirits sector. While to date we have been using EcoLeaf for wines and spirits, we are not limited to it.
L&L: You previously estimated a return on investment in six months. Has that proven to be the case?
MV: My statement regarding a six-month return on investment never referred only to the financial benefits. It is based on a wider view on investing. As an organization, we learned an incredible amount from the EcoLeaf beta phase and were able to build new customer relationships. In particular, the learning payoff we have seen after six months makes EcoLeaf a good investment for us. For me, as an entrepreneur with a long-term perspective, these are the real benefits from investing in such a new technology. Financially, the investment will pay off by mid-2022, when major projects that are currently starting up will be realized.
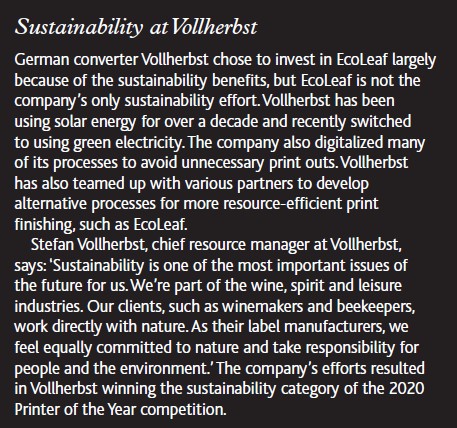
L&L: What was the learning curve for using this technology?
MV: Our team, and especially our machine crew, were motivated to the hilt at the beginning. They were happy to finally have a new challenge to dig deep into. That is an essential part of our corporate culture. Accordingly, the first successful implementations were also available very quickly. Of course, with the first hurdles came the first set of dampers. Learning that there are still one or two limitations to using EcoLeaf was difficult, because our operators have the expectation and willingness to always deliver an absolutely perfect result.
Sustainability has to be thought of in an absolutely holistic way and doesn’t just start with the printer, but already with the designer
At the same time, we knew that this process is completely normal and the Actega team also quickly had a solution for every problem. Today we know that a new technology needs some adjustments and workarounds. We also got confirmation once again that while there are exciting new projects for EcoLeaf, conventional hot foiling is still needed for many, many applications. The one-to-one comparison is just completely wrong. It is just a completely different technology and application.
L&L: What machine are you using to print the trigger image?
MV: In the wine and spirits segment, we work almost exclusively with very open-pore uncoated papers. We have found that we achieve the best results there when we apply the trigger image with the screen unit on our A B Graphic Digicon.
L&L: What feedback are you receiving from your clients regarding EcoLeaf?
MV: We are seeing more and more customers asking for alternative, sustainable solutions for their labels every day. EcoLeaf is one of the solutions we offer them in this regard – among many others. Customers understand the benefits very clearly and find the new technology very exciting. But they also understand that there is a different look and feel than the one they know from hot foil and embossing. This is where we do important educational and advisory work, because there are simply projects where we have to continue conventional finishing – for sustainability and visual reasons – and in other projects you can go for new technologies like EcoLeaf. But there is no one-size-fits-all solution, which is why it is important to take a highly individualized approach to each customer project.
L&L: Can you talk about the sustainability benefits?
MV: EcoLeaf’s sustainability principle is clearly based on avoiding waste. After all, the idea is to metalize with pinpoint accuracy and not produce waste resulting from the fact that full-surface metallization is used for the finishing process, of which perhaps 10-20 percent is necessary for the design. This sounds very complicated, but the principle becomes very clear in the case of a gold frame, for example. For a gold frame around a label, a hot or cold foil has to be placed over the complete label and the inner part is waste.
We learned that it’s better to match each job repeat length. So, now all new EcoLeaf units are equipped with variable size donor rolls, ensuring that all customer’s job sizes can be matched
With EcoLeaf, we can only metallize the gold frame and do not produce this waste n the inner area. Here we see massive sustainability benefits by using EcoLeaf. In other cases and for other designs, however, other technologies may have similar or better sustainability benefits. It all depends on the design and the metallization set-up. You can see from this, that sustainability
has to be thought of in an absolutely holistic way and doesn’t just start with the printer, but already with the designer.
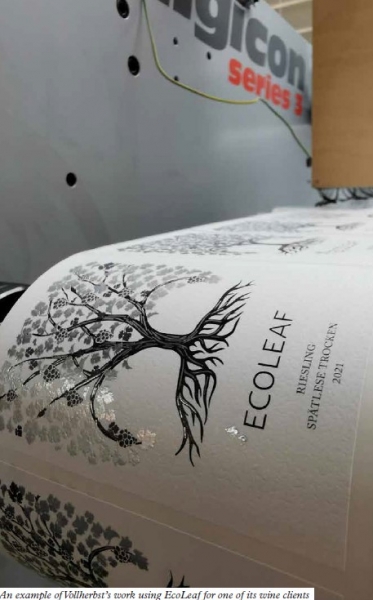
Interview with Actega Metal Print
L&L also sat down with Paolo Grasso, sales director for Actega Metal Print, to see what insights the company gathered from the beta testing process.
L&L: Could you comment on how the beta testing went?
PG: Beta testing has gone very well. As you know, one of our customers [Kolbe-Coloco Spezialdruck] has already completed the process and is producing high quality, saleable commercial work that their customers love. And importantly, our other beta customers are also providing very positive comments, as well as constructive feedback that we use to further refine the system – this is the purpose of the beta process, and it has been invaluable. We head towards commercialization and series ramp-up in great shape, but as you would expect, we still have lots of work still to do.
L&L: As the beta testing process is completed, what comes next for EcoLeaf?
PG: While Kolbe-Coloco has completed its beta program, we have many other customers that are still in the process. But as you suggest, we are making great progress and as is the nature of R&D
teams across the Actega business, we are constantly developing new innovations to either extend the capabilities of EcoLeaf, or other exciting things to come. For any business like us, but especially
in the graphic arts, it’s so important that we continue to innovate to ensure that our customers have the sharpest competitive edge and the most sustainable solutions available.
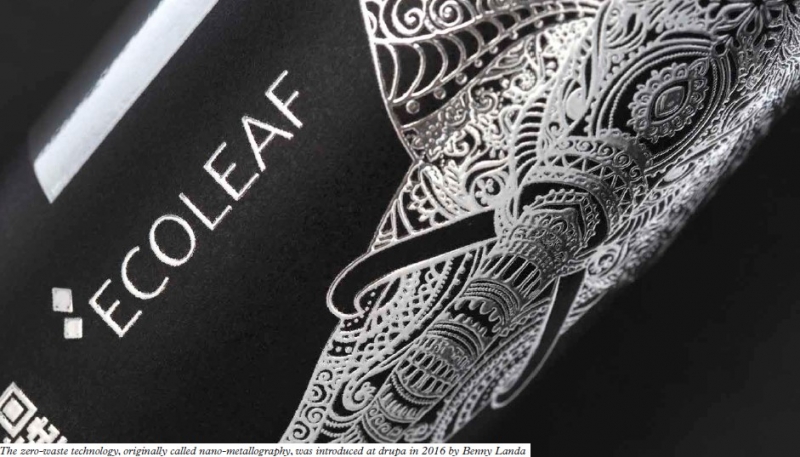
L&L: Are you still on track for commercial availability in the US in 2022?
PG: Yes, we are. But as you know, nothing is for certain right now as we all continue to manage the impact of the pandemic.
L&L: Why did you choose ABG as your partner for EcoLeaf?
PG: ABG is a great partner for us. They have over 65 years of print finishing expertise in the label industry, with some 11,000 product installations and 2,500 customers. They not only see a big opportunity with EcoLeaf, but they share our vision for a more sustainable print market too – so there are some great synergies between us.
L&L: What are some of the changes being made to the technology as a result of the beta testing feedback?
PG: Well, there were many. However, one of the key learnings we made was that it´s better to match each job repeat length. So, now all new EcoLeaf units are equipped with variable size donor rolls, ensuring that all customer´s job sizes can be matched – this also makes the system even more user-friendly. Of course, there will be other changes and innovations that we make over the coming months and years, as our aim is to continually evolve the solution and enable it to support different market segments in the future.
Stay up to date
Subscribe to the free Label News newsletter and receive the latest content every week. We'll never share your email address.