Automation Arena looks into the future
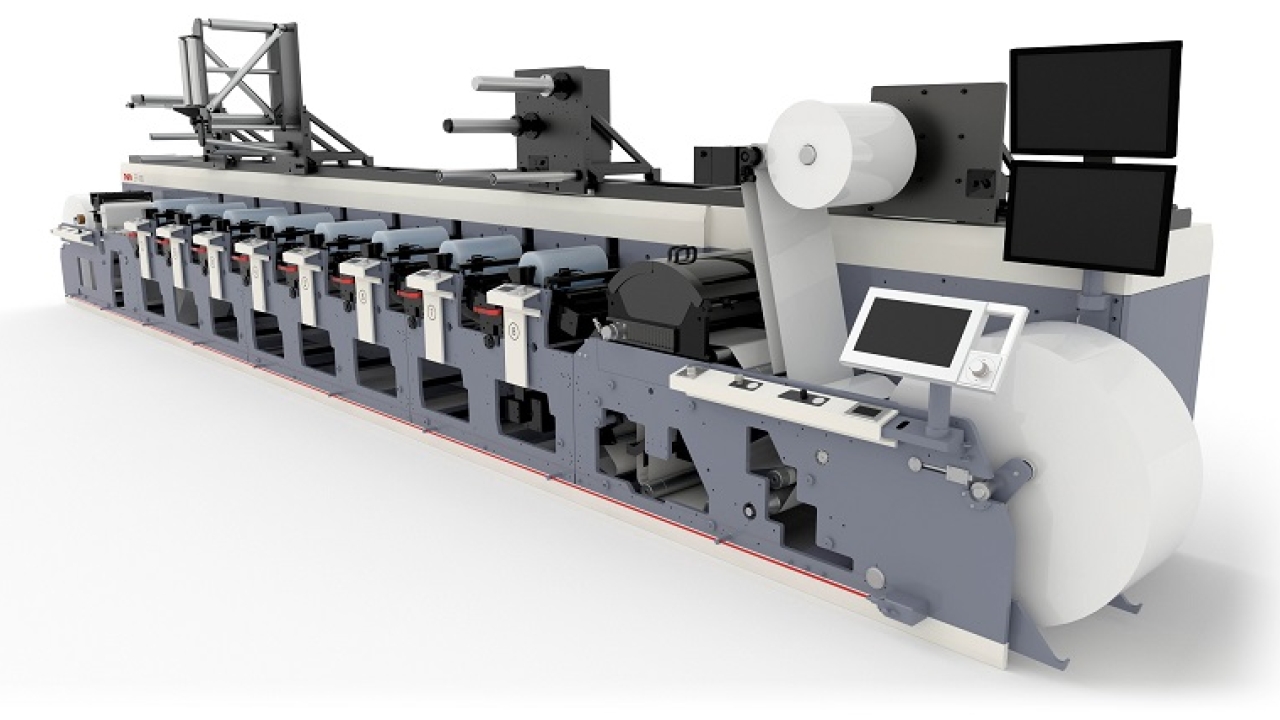
Automation is rapidly changing the way that label and flexible packaging companies are managed and how printed products are produced, changing every stage of the production process ‒ from order taking and job creation, through pre-press and printing – to delivery and invoicing of the finished job.
The integration of ever-more sophisticated MIS modules with business and production workflows, software for design, pre-press and color management, the latest digital and conventional press set-up solutions, automated inspection systems, laser die-cutting, intelligent unwinding, slitting and rewinding and now, for the first time, taking automation into shrink sleeve seaming and inspection, are all offering converters increased productivity, reliability, traceability, quality performance, reduced waste, and improved profitability.
All of this is being demonstrated in the Automation Arena at Labelexpo Americas 2018, with thirteen leading industry hardware, software and materials suppliers collaborating in live demonstrations of two automated press lines – between them digitally printing and converting several different self-adhesive label and conventionally printed shrink sleeve designs – and all centrally managed by a Cerm MIS.
At the start of the live demonstration, an audience member ‘customer’ will be asked to choose selected labels from a digital repeat ‘Get Set’ energy drink label design and a choice of conventionally printed ‘Alcis’ Sport woman’s fragrance shrink sleeve graphic designs, and will then be able to follow these through all the necessary automated job management, pre-press, print production, inspection and finishing stages, waste removal and warehousing and, finally, through to job delivery and invoicing.
From its initial concept, the aim of the Automation Arena has been to show converters that with the latest workflow technology it is now easier than ever to automate and process many more jobs in the same through-put time, with fewer errors, with 100 percent quality and barcode inspection, incorporate automated press and finishing set-up, and all with the same number of employees.
A centralized hub and pre-press platform
At the central hub of the Automation Arena is a Cerm management information system (MIS). Cerm has teamed up with key industry partners to develop end-to-end automation for self-adhesive labels and shrink sleeves that covers the entire value chain.
Whether for digital or conventional print, the Cerm system includes modules that support each step in the integrated workflow, from estimating, shop floor data collection, final printed job delivery, through to invoicing. The modules provide specific features and functionality that drive efficiency and improve profitability.
During the demonstrations, the Cerm MIS will be seen processing and managing the whole automated workflow, integrating with an Esko software platform supporting an end-to-end label workflow. This platform will firstly change the selected digital label design that will be produced on Avery Dennison Spec # 79100 Fasson 2 Mil White Top Coated/ S7000/40#BG self-adhesive labelstock on a Xeikon CX2 digital press – and personalize this with the customer’s name, create rules for inspection, and initiate a proof for customer approval – and then call-up the shrink sleeve graphics and plates for printing on an MPS EF 430 UV flexo press.
The Esko platform is a comprehensive set of software for design and pre-press, workflow automation, color management, and supply chain collaboration for the label, shrink sleeve and flexible packaging industry. With a focus on cost control and productivity optimization, the platform supports an end-to-end workflow with hyper realistic 3D viewing, also on mobile devices, web collaboration, PDF editing, content management, and quality assurance tools all providing a sophisticated user experience.
Digital production and inspection line
Once approval of the label and barcode is received back from the selected ‘customer,’ files are sent from the Esko software platform to the Xeikon X-800 digital front end, in turn integrated with a Xeikon LDU laser die-cutting unit that is able to ‘needlessly’ switch over between two jobs. Xeikon’s flagship narrow web label press, the 3300 excels in productivity and high quality digital label and packaging printing. The Xeikon LDU will apply a Flint Group Digicoat GP gloss varnish, laser die-cut, slit and rewind labels, enabling frequent job changeovers with limited or no set-up time. The laser station can kiss-cut and perforate if required. Integration with the Xeikon Front-End via the Vectorizor module provides step and repeat and printing, and with AVT 100 percent automation inspection files, job identification and die-cutting, and finishing barcodes for the in-line laser die-cutting, slitting and turret rewinding. The finished rolls off the press are barcoded for roll identification of the finished product. This all ensures smooth and automated label production.
A Matho Cuttobag CB-100.1 waste management system on the Xeikon press will be used to cut, transport and collect the production waste into a waste disposal system, while cores for both presses will be cut on a WLE fully automatic core cutter The cutter reads a barcode from a label that is printed on a label printer close to the cutter. This requests job cutting instructions from the MIS. Cutting can be done and the label is re-used to identify the cores per job.
UV flexo sleeve printing
With the Xeikon press set-up and running, the MPS EF 430 operator is by then reading his MIS-generated job ticket on screen, enabling him to check that plates, tools, inks and substrate had been delivered, and changing the unwind roll using a Kocher+Beck UR Precision U440 butt splicer. This highly innovative technology features a fully servo-driven unit with intelligent Data Link communication features, providing non-stop press operation and increased throughput.
ach roll loaded is scanned and becomes fully traceable throughout the whole process, interacting with the Cerm system in order to provide real-time production values. A Cerm inspection command is also sent to AVT’s automatic 100 percent inspection system on the press, which registers any defects during printing – but at this stage does not act on them.
Especially designed for labels, sleeves and flexible packaging production the MPS EF press in the Automation Arena features UV, hot-air and LED drying technology, enabling users to print on a wide variety of substrates including thin film, paper, carton board, shrink sleeves, in-mold, tubes and flexible packaging. It will be printing on Klockner Pentaplast’s Pentalabel Rigid PETG 50 micron, using Zeller+Gmelin’s 32 Series Nuvaflex range of UV flexo inks developed specifically for sleeve production.
Next to ‘standard integrated’ machine automation, the EF also offers an automation package for further extended (additional) print automation: the APC Package, provides automated servo control of all relevant press settings. The package can be configured for the ultimate in print setting control to increase productivity on the EF press. Thanks to APC, press settings and controls are easy to operate and replicate through job memory, resulting in virtually no set-up waste for initial and repeat jobs.
Automation extends to sleeve seaming and finishing
Printed rolls coming off the MPS press will be identified with an ID barcode which, when scanned, enables an electronic instruction file to automatically set-up shear slitting on a Grafotronic high-speed inspection slitter rewinder, as well as provide the location for any bad products according to AVT scanning instructions.
An AVT camera on the Grafotronic will then automatically stop the machine whenever a defective label is detected in the printed reel so that any necessary repairs can take place. The final, ‘clean’ and slit roll is then rewound and a barcoded label applied to the reel. As this roll transfers to the Accrapl ASFC fully continuous forming and seaming
machine, the barcode is scanned and the instruction file from the code will be read and used to automatically set-up the forming and seaming operation. After set-up, forming, seaming and rewinding of the, now, lay-flat shrink sleeve web, the Accraply ASFC writes a log file and creates a barcoded label which is applied to the lay-flat seamed roll coming from the seamer. This barcode is, in turn, then used to identify and provide file information as the seamed roll is transferred to an Accraply DM12 Shrink Sleeve Inspector, a compact vertical seaming inspection machine used for lay-flat quality checking.
The DM 12 inspects for seam integrity, solvent presence, lay flat and for any splicing/flag detections, enabling any bad sleeves to be thrown out before rewinding the lay-flat ‘clean’ web. At the end of the quality check the Accraply system provides a printed report for each roll that will give the customer all the necessary QC information required.
Final rolls carrying barcoded identity information, whether from the Xeikon or the MPS/Accraply production lines, will be scanned into a warehouse location, a picking list prepared through the Cerm MIS, a delivery note printed, with an e-mail notification sent to the customer and invoicing launched.
In an era of ever-decreasing run lengths, production bottlenecks, shorter lead and delivery times, multi-versions and variations, increasing automation of tomorrow’s label and shrink sleeve plants will become a necessity for their successful performance and profitability. The Automation Arena will provide an important showcase of what is now feasible.
Stay up to date
Subscribe to the free Label News newsletter and receive the latest content every week. We'll never share your email address.