Boxes on a roll
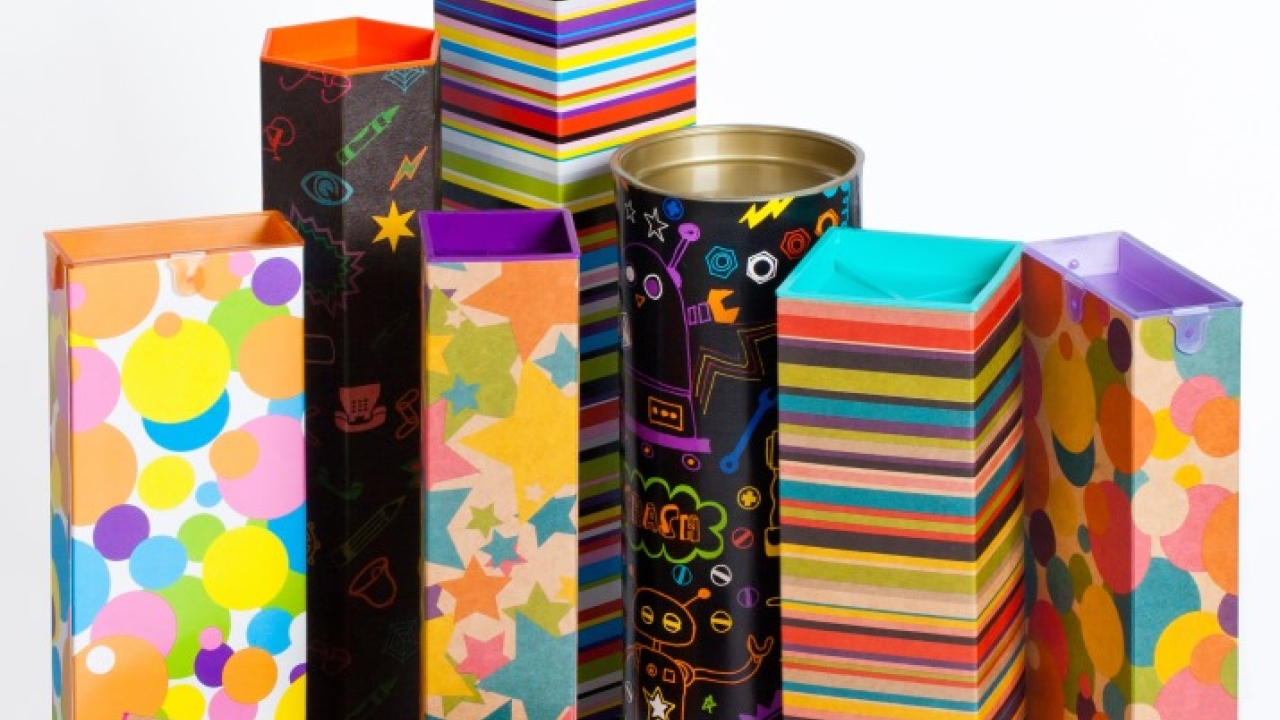
Bell Packaging’s new initiative, Jetbox Packaging, hopes to capitalize on those looking for innovation in boxes. David Pittman reports
Bell Packaging is a well-established manufacturer of plastic packaging under the names Jetran, Petran and Retran.
Established in 1979, the UK-based manufacturer of transparent retail packaging produces these products in continuous reels from PVC, PET and PP at its plant in Luton, UK.
Flat-packaged tubes
From the company’s factory in Luton, Bell Packaging operates the world’s largest production facility for Jetran tubes.
Packed flat, Bell Packaging states that the reels of material are economical to ship and store, and easy to handle. The reels can then be used to create packaging of variable lengths and, using a patented converting process, in a variety of shapes.
This process creates crease lines in the plastic that, when folded and glued, produce packaging of different dimensions, from squares and triangles, to ovals and hexagons.
Jetran is manufactured using PVC and PP in gauges from 100 to 500 microns, while Petran is produced from PET. Visually identical, the properties of the different raw materials make Jetran and Petran applicable for different markets.
For instance, PET produces a glass-clear film with excellent strength that does not turn white when creased, and has a slightly softer feel than PVC. It also requires less energy to produce than PVC, and does not contain any heavy metals or fluorochlorohydrocarbons.
Jetran’s traditional raw material, PVC, offers clarity and strength, and is cheaper to produce than PET.
Both are suitable for printing, and applicable for food contact applications, as is PP, which also offers a softer feel than both PVC and PET can be supplied with a range of surface finishes and colors, and is 30 percent lighter, but is traditionally not as transparent as the alternatives.
Extension of the brand
Retran is an extension of the Jetran line, made from post-consumer plastic waste. It contains approximately 70 percent post-consumer waste, including soda bottles and sandwich cartons that would normally find their way to landfill.
Alongside the plastic tubes, Bell Packaging has developed and patented closures to help protect the products and add additional rigidity to the structures created from Jetran, Petran and Retran.
This includes end caps, themselves available in different colors and shapes, and biodegradable versions to complement the environmental credentials of Retran. After use, these require constant contact with other biodegrading materials, such as those commonly found in home composting, commercial composting, landfill and any areas where the end caps will be buried or in contact with soil. Whilst in these conditions the plastic end caps will biodegrade and become some of the soil's organic components within a period of 1-5 years, which compares favorably to a traditional plastic carrier bag which take between 20-80 years to degrade.
Bell Packaging’s latest development in this area has been Jetlok, a staple-free end cap system that can be secured to Jetran tubes without the need for any staples, rivets or self-adhesive labels. The locking mechanism on the cap gives total security until the pack is opened, and after use the Jetlok cap can be refitted, resealed and the finished pack reused. As an added feature, hangers can be fitted to the top caps.
Bell Packaging’s recent history has also included growth in international markets, notably India, where it has had a footprint for nearly 15 years. It recently extended its market position by partnering with Globe Print n Pack, and has recorded double-digit sales growth in the years since starting to work with the Mumbai-based packaging producer. Bell Packaging also has customers across Europe, the US and in China.
Sustainable growth
Bell Packaging’s managing director Peter Lennie says he realized the potential for the established Jetran manufacturing process to be used with fiber-based material after investigating ways to capitalize on growing environmental concerns.
This led to the creation of the Jetbox Packaging brand, which delivers fiber boxes on a reel, which, as with the PVC, PET and PP versions, are converted to allow them to be shaped in a variety of different ways.
‘Some people need a product that falls between a rigid box and a folding carton,’ says Lennie. ‘We’re seeing a lot of interest in it, as the packaging market is looking for new environmental initiatives.’
Jetbox is currently manufactured in a 350-micron thickness from both virgin and recycled grades, and Bell Packaging is working on producing thicker versions, up to 700 microns.
The board is receptive to any printing process, and Bell Packaging works with a network of partners to add print to the Jetbox material. Bell doesn’t have print capabilities in-house, although does carry out foil printing to add detailing to its plastic products, so works with converters like Bridger Packaging in Letchworth, UK, which specializes in folding carton production and operates KBA presses.
One of the key markets for Jetran packaging is in the display and retailing of DIY products, such as curtain poles and blinds, and fluorescent lightbulbs. With Jetbox, Lennie highlights the confectionery gift market as one that could benefit from the product. Noticeably present in retail environments around special occasions and holidays, such as Christmas and Easter in Western markets, consumer product groups often offer their main confectionery brands in larger, multi-pack tubes and cartons manufactured in heavier board stocks.
Presentation boxes for spirits and beverages could also be favorable towards Jetbox, Lennie said.
‘Jetbox opens the doors to new markets for us, and offers Bell Packaging big opportunities. ‘It is a new concept for the market, so we need to educate it on the product and process, and get the market to buy into it.’
Secondary use
For all the products Bell Packaging produces, a secondary use is key to Lennie. From Jetran plastic tubes to the new Jetbox range, he sees it as vital that packaging is designed with a secondary use built in, such as a container after the main product has been consumed or used.
For instance, Jetran can be combined with a printed insert to create the high-value printed appearance associated with conventional cartons and tubes, but this can then be removed to create an unbranded, see-through container for various items.
The use of Jetlok, which can be opened and resealed, means that these containers then become secure devices for holding foodstuffs through to homewares.
‘Secondary use is key, particularly when it comes to plastic packaging. We need to be doing what we can to stop packaging going to landfill, and offering consumers the opportunity to reuse cartons and tubes is a primary way of doing this.’
Read more features from Packprint World here
Stay up to date
Subscribe to the free Label News newsletter and receive the latest content every week. We'll never share your email address.