Flex Films International sets up five new plants
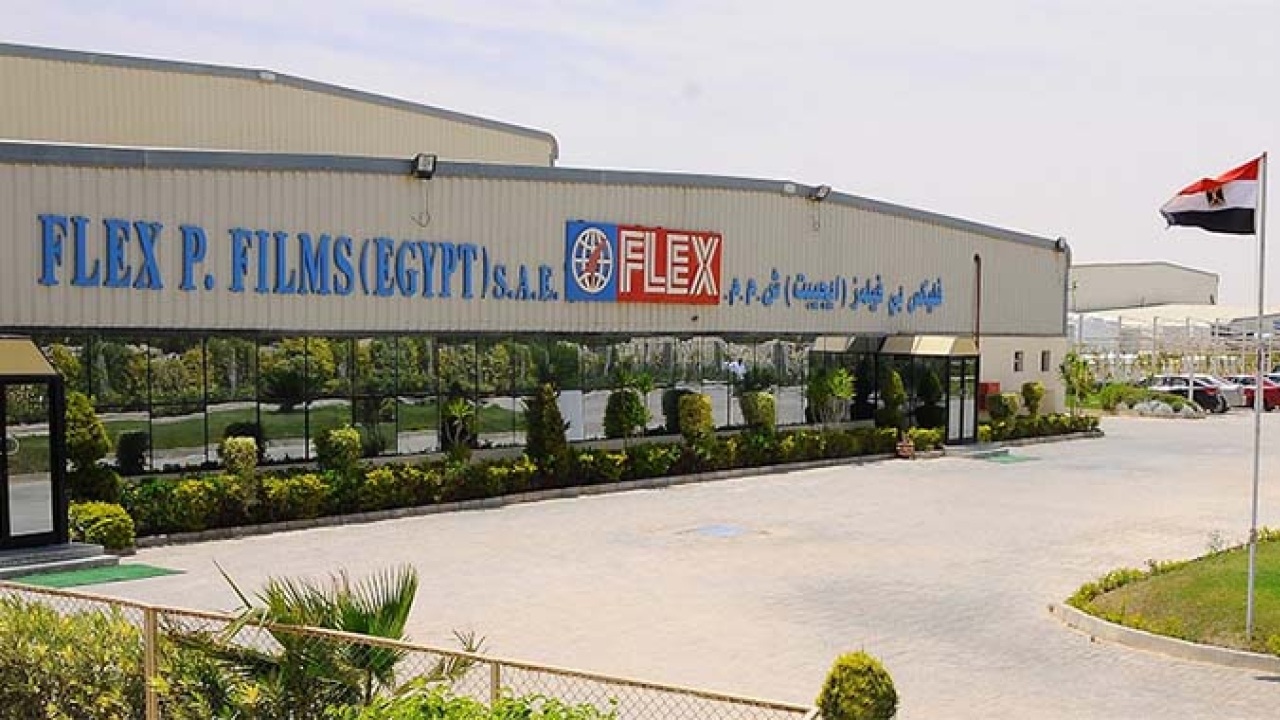
The film manufacturing arm of UFlex, Flex Films International, has set up five new production lines including three new global locations.
‘For us it has been very interesting year of global growth for Flex Films,’ says Anantshree Chaturvedi, vice chairman and CEO. ‘Because even though we are going through the pandemic – which was unexpected by all of us – we had gone into an expansion drive in 2019.’
The company had planned five new lines at international locations including three new global sites – Poland, Egypt, Hungary, Russia and Nigeria. The biggest challenge for the company in 2020 was to complete these projects while ensuring high levels of safety for employees and innovating its way out of the problem of engineers not being able to travel. The company used a virtual engineering assembly system, body cameras and local training to get the new plants up and running.
Flex Films’ strategy has always been to set up small facilities across the globe
‘My prayers were answered when the Nigeria plant was ready by December 27, 2020. If I had missed the 2020 deadline, then I would have missed the deadline of starting all of the facilities within the 2020 time frame. It is one of the things we are extremely proud of,’ Chaturvedi highlights. The construction of the plant in Nigeria has been completed and was commissioned in Q2 of FY2022 quarter.
Flex Films’ strategy has always been to set up small facilities across the globe. This helps the company to be closer to customers, deploy better supply chain logistics, and counter geographical competition.
‘To be honest, this was something we did basically to counter a lot of competition that is coming from South Asia. A lot of giant facilities are implementing 10 to 20 lines at a time – for us, that is not the model that we would like to emulate,’ Chaturvedi adds.
The company has set up a BOPET lines in Russia, Nigeria and Poland; BOPP lines in Egypt and Hungary; and is setting up a CPP line in Dubai, UAE; and a CPP and BOPET plant in Karnataka, India. The BOPET plant in Russia has also been commissioned. The UAE and South India film lines are under construction. The total investment is valued at approximately 450 to 500 million USD. The plants have capacity of 18,000 to 45,000 tons per annum.
The company has commissioned its BOPET film manufacturing plant in the Ogun State of Nigeria with a production capacity of 45,000 tons per annum. Spread over 37 acres, the plant houses 10.6m BOPET film line in Africa and has two metallizers with a total production of 15000 tons per annum.
The plant created over 200 direct jobs and will meet the packaging film demand coming from the fast-growing economy of Nigeria, ECOWAS (Western Africa) and USA.
UFlex is also expanding its Asepto liquid packaging plant in Sanand, Gujarat, by 3.5 billion packs annually, taking the total capacity to seven billion packs.
Potential
According to Chaturvedi, the African market holds significant potential for the company. ‘It is going to be a groundbreaking market not only for us as a company, but it reminds me of how I read the American market was in the 1950s. It was in America between the 1940s and 1960s when new industries and entrepreneurs emerged. The emerging middle class in Africa is similar to the dynamics that I witnessed in India between 2002 and 2016.
Speaking of emerging markets, he adds that Russia was the ‘next big surprise’ for the company. ‘Russia as a country is changing so much culturally and from a consumer perspective. Young people are very ambitious and driven to improve their standard of living and that is what drives real growth.
‘As an Indian by origin and an American citizen growing up in Asia and then getting a Western education, everything I learned about Russia was a lie. It is this growing, ambitious nation full of young people who are into technology and want improvement and tremendous exposure. They have amazing STEM (science, technology, engineering, and mathematics) skills,’ he explains.
These are the two markets the company is ‘very excited’ about.
In India, the company is setting up a plant in Dharwad. ‘It's closer to Goa than Bangalore which I am happy about. It's closer to the beach than it is to a big city.’
Construction has begun and production will start around Q4 of year 2022. The bigger project (45,000 tons per annum) is the BOPET line, which will begin production in the last quarter of 2022. The CPP line (18,000 tons per annum) might kickstart production from Q3 of 2022.
UFlex has been posting double-digit growth annually since the mid-1980s. ‘It's been a blessing but also a curse,’ Chaturvedi points out. ‘From the outside it seems like this is constant growth but it's not actually like that.'
Around 15 years ago, the company started its expansion outside of India. Its first international plant was established in the Middle East in Dubai. ‘It taught us how to set up a project outside of your home country and manage it.’
From there, Flex Films expanded into Mexico, Egypt, Poland and the US. The company finished its expansion in the US in 2013 and then took a pause. From 2013 to 2018, it consolidated and took the time to reach full capacity with its existing projects. It focused on fine-tuning and improving its product portfolio. ‘We absorbed local and technical knowledge and used it to capture other markets.’
Within this ecosystem, the company was selling well in the African and Russian markets and realized that there was a growing demand in Europe. ‘So the next phase of expansion that I mentioned previously was a natural thing for us in 2016.’
As a challenge, the company decided to go ahead with the expansion all at once. It did not want to lose market share in Russia, Europe or Africa.
‘It seems like a large investment but if you look at our balance sheet, our EBITDA grew significantly during this time so our debt-to-equity ratio goes down even though we take on more debt for these projects.’
Chaturvedi explains that the company’s strategy worked well during the pandemic. Global logistics were hindered and Flex Films was one of the companies that got unforeseen traction out of it due to its ‘glocal’ (globally local) operations. ‘But the key challenge was to keep our people safe and maintain our safety standards to even a higher level that we usually do, because we could not afford to shut down for even a single day. We were in the “essential industry” from day one.’
The company saw a surge in polymer demand during Covid which Chaturvedi believes is temporary.
Project Plastic Fix
The company has been working on multiple sustainable technology projects to create a circular economy.
‘Sustainability is one of my favorite topics to discuss,’ Chaturvedi mentions. ‘We as a company have been selling these products for the better part of the last decade. But the truth is that the real traction of sustainability only started at the turn of 2018. That is when this conversation about sustainability, about plastics polymers, started taking shape not just in India but globally.’
According to Chaturvedi, polymer has a ‘stock and flow’ problem. There is a stock of polymer that exists. Once discarded, single use plastic adds to the already existing stock. ‘It either goes to landfill or hopefully it goes to a recycler and becomes something else. But if it does not do that it becomes waste. This also includes plastic electronic waste – something people don't even think about.’
The emerging middle class in Africa is similar to the dynamics that I witnessed in India between 2002 and 2016
The second problem is the flow of polymer. New plastic is being made every day. ‘The way to solve this overall is to create a holistic project that we created a couple of years ago – Project Plastic Fix.’
Although Project Plastic Fix was launched in 2019, the technology to recycle mixed plastic waste was invented by chairman and founder of the company Ashok Chaturvedi in 1995. ‘We were awarded for that technology. We were more concerned about polymer waste than anyone else because for us this is our survival. Solving this problem is of absolute acute importance because we don't want to make a product that nobody wants to buy.’
He says that while the technology to recycle MLP waste has been in existence since 1990s, it did not get noticed until the ban on plastic was implemented.
The company is working to establish recycling plants in Varanasi and Bangalore. Similar facilities will also be installed in Poland, Egypt and Mexico. These will be UFlex’s initial showcase facilities and the company will then expand globally. The multi-layered plastic waste will be converted to granules to make more than 10,000 different products.
‘We also want other entrepreneurs to buy this technology from us and set up their own facilities,’ Chaturvedi adds.
The second part of the project is Pyrolysis, which Chaturvedi says is popular in emerging countries. It is conversion of polymer waste into energy. ‘Our process converts it into furnace oil and diesel fuel. The process does not emit any greenhouse gas or carbon monoxide. We have kept a filtration system such that it does not have any negative impact on the environment and is a complete clean transition into clean fuel.’
The company is also working to develop biofuel from plastic.
‘The third part of the project which I'm really proud about is Asclepius, which was created by my team in the US.’ The process involves converting plastic into up to 100 percent post-consumer recycled film. The company uses collected plastic waste and converts it back into original films for packaging.
‘We have showcased studies that we did with one of our customers, UPM Raflatac, in the US. We have created a circular economy which actually works as opposed to a circular economy that only works in theory.’
Addressing the ‘flow problem’ Chaturvedi says: ‘What do we do when consumer buys a package and is careless and leaves it in the garbage or tosses it on the streets? That is where our product Flexzyme comes into place.’
Flexzyme is a biodegradable technology which turns discarded plastic into sugar glucose molecules. ‘Human beings in general are unaware of the fact that problems such as greenhouse emission, population and climate change are very hard to solve. But plastic is a solvable problem. In the long run, consumer demand combined with government regulations is going to drive this change, but right now we are very far away from that. Because now, things are driven by profitability and buying organic green plastic is still going to be more expensive than buying oil-based plastic. There is an efficiency that has been set up in the petrochemical supply chain of raw material to the polymer industry. The cost of organic plastic will become negligible with economies of scale, so you have to hit those economies of scale. Until you hit those economies of scale you will have the chicken and egg story.’
Flex Films is seeing growth in volumes of PCR and biodegradable films.
The company is testing its biodegradable packaging with Haldirams, a popular food brand in India. Some of the brand’s SKUs are 100 percent biodegradable using Flexzyme.
Chaturvedi adds that customers in the US are also using 100 percent PCR films that are not fossil fuel-based polymer and reduce emissions by 75 percent.
He points out that sustainability will be a huge trend in labels. ‘Because in label manufacturing you are discarding a lot of polymer right from the B2B stage. So from a global perspective sustainability will make huge traction in labels. That's why our key customer in the US is a label manufacturer. They went ahead of the curve and started with our 90 percent recycled film and now our 100 percent recycled film.’
This trend is yet to catch up in the Asian market. ‘But in the US and Europe, almost all kinds of labels are being manufactured with some kind of PCR, biodegradable-based polymer – and really biodegradable not oxo biodegradable.’
Digitalization in packaging
One of the other key trends that Chaturvedi sees is digitalization of packaging. He says that it is currently not being prioritized and today's consumers want their packaging to communicate. The industry is yet to fully explore its full potential, he believes. QR codes have begun appearing on packaging to provide information about the product along with website and video links.
He says that this trend is taken up by product segments where the consumer really cares what is inside that package, such as baby products, pet food, high-end consumer goods, cosmetics, nutrition products and pharmaceuticals. He adds that this will change how packaging uses ink, adhesive, printing technology and colors.
Digitalization of packaging is also going to be driven by e-commerce becoming a big space in the packaging sector, especially driven by the pandemic. Consumers in the Indian diaspora have become used to ordering groceries. Different delivery mechanisms have emerged that are driving diverse needs for packaging.
Our EBITDA grew significantly during this time so our debt-to-equity ratio goes down even though we take on more debt for these projects
‘That's the evolution. Different printing and processing mechanisms will be needed for preservation of these goods while they are being transported, sold and allocated. The convenience of having e-commerce deliveries come to your doorstep and the fact that so many people have adapted to it is not going to go away easily. So that is one other emerging trend that I see.’
A third trend that Chaturvedi highlights is digital currency linked to waste. ‘This is a trend that is more in the Western world because the West is not policing this mechanism as much as it is being policed in the East.’
Bitcoin – pegged to a certain tonnage of waste, including BOPP, glass and aluminum – is gaining popularity in the US and Europe.
‘A different category of waste will be allocated to digital currency which will transform into an actual dollar value and real monetary system that can be used today.’
However, he says that India has not yet adapted to digital currency and Bitcoin. ‘China's digital currency is doing well but is controlled by the government. It is policed and is not a fully formed independent digital currency.’
Digital currency could make waste to wealth a seamless process by cutting out the middleman. ‘The process of buying waste off the street goes through five or six hands and then ends up at the recycler. The recycler then creates some value and puts it back. All that value gets eroded just by the people who are handling this waste in the middle. They are just doing logistics by getting the waste from one place to another. All that will go away – it will just translate straight down to a core rag picker or the person who is collecting it. Hopefully they will get a majority chunk of it and with few intermediatory steps, the value of waste might remain the same. It will be a published value and nobody would be unaware of it.’
But the biggest shift that Chaturvedi sees is the global population increase. As the number of consumers grows globally, it drives demand for food and water, which need packaging.
‘That's why you see these global capacities increasing and is the reason why all this investment is happening in this space. Packaging demand is driven by population.’
Stay up to date
Subscribe to the free Label News newsletter and receive the latest content every week. We'll never share your email address.