FPLMA conference promotes Industry 4.0 vision
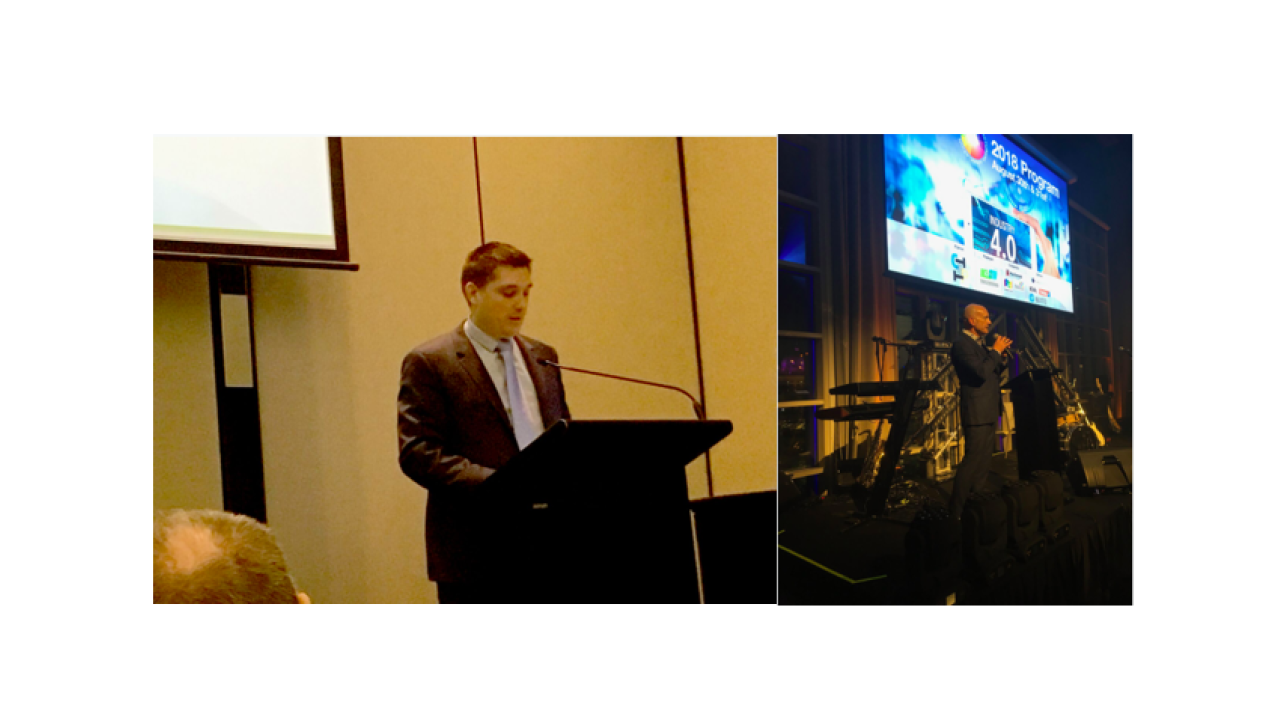
The term ‘Industry 4.0’ refers to the fourth industrial revolution, which applies automation and data exchange to manufacturing technologies, where ‘Cyber-physical systems’, the Internet of Things and cloud computing combine to create a ‘smart factory’.
Although this may appear rather abstract, we can already see its practical implementation in the label and package print converting industries and the exciting – and disruptive – shape of things to come.
A succession of speakers emphasized that the ‘smart factory’ concept is developing in separate ‘pools’ which then combine into wider systems which exponentially increase overall efficiencies. ‘The integration of these technologies in our industry crosses paths with our direct customers and their MIS systems and that demand will only increase,’ said FPLMA president Mark Easton.
Eric Hoendervangers, director at MPS, helped to spell out what this means in practice for press manufacturers and converters. MPS has been at the forefront of pushing automation in the narrow web sector, working closely with Tarsus Group and a range of industry suppliers to put on the Automation Arena at Labelexpo Europe and Americas. The key, said Hoendervangers, is to build systems that have open interfaces and ‘hooks’ to other suppliers’ software.
‘Automated machines will in the future “live” in a digital world,’ Hoendervangers told delegates. ‘This is already happening in the automotive industry, which has moved beyond simple automation to where every car produced can be unique. Aviation is a sector focused on 100 percent guaranteed safety, and this could not be achieved without automatically processing a mass of data knowledge to allow automated and centralized decision making.’
By contrast, the narrow web industry is still living in the ‘craft’ era with very little automation or integration.
‘Pre-press is only involved in making plates. It is the operators who make choices of which tools to use and which press settings. On the average label press there are 40 adjustments the operator has to make manually on every job. Rewinding and post-press have hardly any connection. This now has to change.’
Hoendervangers said in the future the whole operation would be driven from pre-press.
‘The pre-press operator and department will decide all the different elements which go on the press, in which order and for what purpose. This will be a real time connection with no more job tickets. Pre-press will decide on platemaking and ink mixing and machine settings like tension and corona setting, UV and hot air.
‘The print units will determine which set of tooling goes into which print station.’
Within this ‘circle of connection’ the master PDF file would drive the 100 percent inspection camera.
For management, real time data on all aspects of the factory operation is available on connected mobile devices, along with all KPAs. ‘And when you connect machinery to your MIS you can also connect to the press manufacturer. He has all this data and knowledge and will know which part will break before it does. So you will develop an agreement on which activities are to be done pro-actively, and how.’
Supply chain connectivity
Sajid Malik, VP sales for Asia-Pacific at BST Eltromat, explained how mining data from the substrate supplier using Industry 4.0 technologies could change the way we set up jobs on the press. For example, moisture information from the paper manufacturing process can help the converter solve ink transfer-related quality issues.
‘Say there are four different reels with different moisture profiles in each reel, those different moisture levels affect print quality.’ On a water-base press blistering might occur because the drying temperature of ink does not match the moisture profile of the reel.
‘But now we can get that moisture profile from the manufacturer, we can decide to use, say, reels 1 and 4 with the same moisture profile and then 2 and 3 in order to ensure that changes required on the press are small as possible.’ In addition, in-line spectrophometric measurements taken at the paper production stage could be sent to the converter to help color management.
‘What is required to make this work is a standardized way of collecting data,’ said Malik. ‘To use information from the substrate manufacturer they must be using the same measurement parameters. There are exactly the same problems in measuring gloss, moisture etc.’
Although JDF has proven a robust means of communication between pre-press and press, Malik said JDF is rather complex and unwieldy. ‘XJDF is the next step and we are part of that group. XJDF will make it easier for companies to use the data we are collecting.’
Artwork automation
Yoav Lotan, HP Indigo labels business manager for Asia-Pacific and Japan, stressed the importance of automatic processing of masses of production data to give the converter a rapid and accurate insight into manufacturing efficiency. ‘You might call this Fitbit for manufacturing.’
The key measure is Overall Equipment Effectiveness (OEE), which measures the elements surrounding the press and shows in a simple display when a machine is actually productive.
‘For example, using OEE one converter realized they were spending too much time fetching substrates from a remote area, so now they keep materials by the machine. In another case a proper maintenance schedule solved an issue which the converter thought was due to spending too much time on set-up.’
Lotan looked at automating artwork creation, referencing HP’s Mosaic software. On the hardware side, HP is going down the route of fully digitized, tool-free print and decoration, with one file incorporating print and embellishment layers which is RIPped inside the DFE. Smart, automated ganging of multiple jobs on press reduces waste and printing time by efficiently using all the real estate on the press.
End user perspective
Jason Goode of Simplot Australia looked at the potential of Industry 4.0 automation from the brand owner’s perspective. Many of Simplot’s brands, such as Birds Eye and John West, are manufactured on a global level, which makes managing packaging requirements a Herculean task. A key issue is that different retailers have different data requirements. ‘We have 600 products and made 8,000 label changes in the last six years covering materials, ingredients labeling, carbon footprint, nutrition information, GMO and ethical sourcing,’ said Goode. ‘And as retailers move products online, that same information has to follow.’
Industry 4.0 could help tackle many of these issues. ‘I will know that the right label is on the right packing line and providing all necessary information to customers for each product.’ The approval cycle would also be shortened.
The growing consumer focus on packaging recyclability is also having an impact. ‘People now want to know, or could ask for, the provenance of every component.’
Simplot was a founding member of REDcycle, a Melbourne-based project which encourages consumers to return their flexible packaging to retailers such as Woolworths and Coles. Up to two million units of Birds Eye flexible packaging have been returned since the project launched.
‘There are well over 100 recycling symbols, so we are looking at developing simplified symbols like “film, return to store”,’ said Goode. ‘But the lack of standards across the supply chain is the problem. We need to find ways of sharing information more efficiently.’
Automating LCA
Robert Taylor, director of sustainability at UPM Raflatac, explained how life cycle information can be automatically generated using UPM’s Label Life tools. ‘Although the label is only 5-10 percent of the pack footprint, its overall impact can be great.’ Label Life takes account of a wide range of up and downstream factors including sustainable forestry, post life of the label and raw materials saving from down-gauging.
‘The problem is that brands are using different data systems – so how can we get our information into their systems?’
Taylor also looked at the challenges of collecting process waste including trim and matrix as well as glassine/filmic liners.
‘Label waste is typically small volume and geographically scattered. With Rafcycle the user scans a QR code which tells us how much waste is available, and when a certain volume is reached UPM Raflatac collects it all and it goes to the recycling plant. We already have 120+ partners and are now rolling the program out to the Americas and APAC.’
Taylor warned about marking packaging as ‘compostable’ where there are no industrial composting systems available.
Pre-press automation
Speakers from Esko and Hybrid Software looked at automation of the pre-press process including the key approval cycle.
The approval cycle is a complex process involving multiple actors – packaging engineer, legal, R&D, marketing and printer, and in multiple languages. The standard way of handling these is by email and sending proofs is hugely inefficient.
Automation of the process not only cuts approval time dramatically, but also adds a complete edit trail with central synchronization of files, so there is no scope for misunderstanding.
‘Currently we have ‘islands of automation’ rather than true end-to-end integration, creating multiple possible points of failure.’
Trevor Crowley, general manager ANZ Digital Solutions Xeikon, looked at the ‘shape’ of an automated workflow, which includes optimized color management, standardization of substrates, grouping of orders based on substrate and finishing specifications.
Crowley stressed the importance of separator labels for better integration of finishing.
‘Generation of set up labels is also automatic and sets up the following processes such as die-cut or foiling.’ Header and footer labels are also generated automatically.
‘By minimizing set-up times in finishing, waste can be reduced by 30 percent.’
Stay up to date
Subscribe to the free Label News newsletter and receive the latest content every week. We'll never share your email address.