Labelexpo Europe review: Plates and platemaking
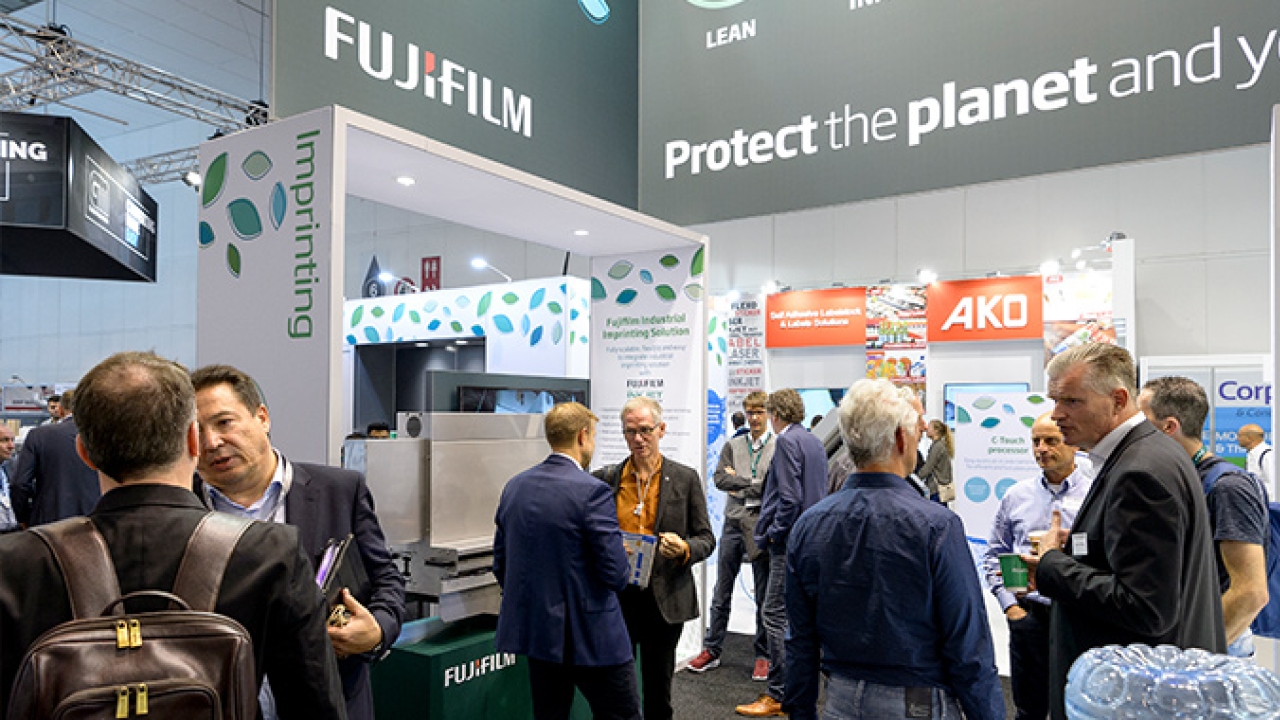
Miraclon, the new home of Kodak Flexcel plate systems, launched in the European market its Flexcel Ultra technology. Still based on the core Flexcel technology, Ultra is a solvent-free, VOC-free, water-based processing technology which can produce a press-ready plate in under an hour. It is paired with the new Flexcel NX Ultra plate and Kodak Ultra Clean technology developed by Miraclon. The all-in-one processing system combines exposure, washout, drying and finishing in the same system with automated cleaning cycles. Flexcel NX Ultra flat top dot plates are available in thicknesses of 1.14mm and 1.70mm. The first product available is the Kodak Flexcel NX Ultra 35, which can produce plates up to 35in x 48in (889 x 1219.2mm) in size.
Esko demonstrated how flexo platemaking can be brought closer to the press with the launch of its CDI Crystal 4835 XPS flexo imager with PlateHandler, working in tandem with Print Control Wizard flexo platemaking and screening software. The XPS Crystal 4835 automates the plate imaging process. Following digital imaging and simultaneous LED-UV exposure main and back, the plate is sent automatically to the processor.
Print Control Wizard takes account of critical print parameters and variables, including substrate, anilox, press type, inks and tape to automatically generate bespoke screens and curves for each job.
Flint Group announced a strategy to integrate the imaging and plate systems from the Xeikon Prepress and Flint Group Flexographic sides of its business. This builds on ThermoFlexX thermal imaging technology, Woodpecker Nano screening and the nyloflex plate range. The ThermoflexX Catena-E80 LED-UV main and back exposure unit and can be added to a ThermoflexX 80/60 imaging system via the Rover bridge to create a fully automated system. Nyloflex thermal printing plates are available in both flat top and round top digital versions.
MacDermid continued to push forward its thermal platemaking technology with the first European showing of the new Lava NW-M thermal processing unit, shown alongside the expanded Lux ITP flat-top dot plate range, now including the Lux ITP Epic.
DuPont showed the latest generation of Cyrel Fast thermal processors and launched an upgraded version of its Cyrel Easy plates for the paper segment. The mid durometer digital plates feature a built-in flat-top dot structure and are designed for both coated and uncoated paper applications.
Continued elimination of VOCs and solvents was a key theme at the show, not only in thermal platemaking but also in water-based plate technology. As well as the Miraclon launch noted above, Asahi Photoproducts showed its AWP-DEW water-washable plates, the first to use the company’s CleanPrint technology which reduces the surface energy of the printing plate, enabling better ink transfer to the substrate and reducing ink filling-in the mid-tone area, leading to fewer cleaning intervals and less press downtime.
Dantex, a long-time proponent of water-based processing, demonstrated its latest AquaFlex 920F processor, designed to work with the new RapidoFlex filtrationfree UV flexo plate. FujiFilm demonstrated its Flenex FW water washable plates and flexo processors, while Jet Europe showed its Aguagreen water-wash flexo plates, available in both analogue and CTP formats, and LSL water-wash letterpress and UV flexo plates.
Hamillroad Software has made a major impact with its Bellissima DMS (Digitally Modulated Screening) for flexo, and the latest version was demonstrated at Labelexpo. Bellissima DMS rasterizes the input and determines the correct shape and size of dots to use, as well as determining where the dots need to go on the plate according to the image being printed. The halftone dots are small enough to be invisible to the naked eye, but large enough to withstand the rigors of the printing process. The dots are positioned to support each other on the plate, providing strength and stability.
Stay up to date
Subscribe to the free Label News newsletter and receive the latest content every week. We'll never share your email address.