Labelexpo Europe review: Press technology
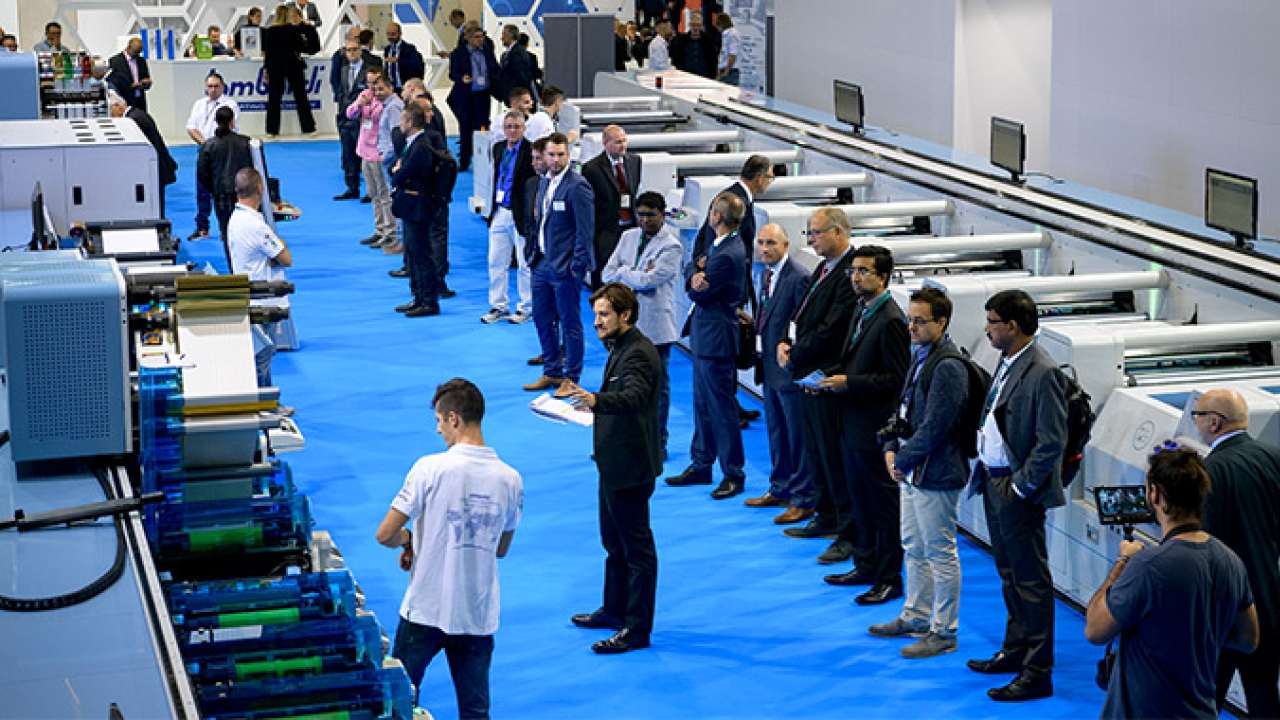
Mid-web for films
A standout trend is the rise of the mid-web press, typically 26in (660mm) wide. These presses meet the need for greater productivity but also the wider format required to produce filmic labels such as shrink sleeves, wraparound labels and flexible packaging.
These opportunities were well demonstrated on the Flexible Packaging Arena, where a Bobst M6 press was shown converting pouch material, alongside the new Xeikon Flexflow digital print and lamination system for the manufacture of stand-up pouches.
Looking in more detail at the new mid-web presses launched at the show, we start with Omet’s XFlex X7. The standout feature was the water-based gravure unit with extended dryer, called by Omet the High Value Rotogravure (HVR) unit. The HVR can be added at any position on the press, with a typical application being first-down white. The unit is easily accessible, with print cylinder and inking tray loaded from the front side on exchangeable tooling trolleys.
The direct-driven unit can print front and reverse and is equipped with integrated chill drum and front and reverse angle doctor blade. ‘We believe the HVR will disrupt the way printers achieve special print effects on shrink sleeves and flexible packaging materials,’ said Amerigo Manzoni, director of R&D at Omet.
Further decoration possibilities are opened up by the new Flexo Vertical unit, operating in either front or reverse printing mode. The Flexo Vertical unit has an extended drying tunnel and is configured for dual UV – typically used for ‘Soft Touch’ finishes – water-based or solvent-based coatings. Also new for this press is a 670mm-wide rotary screen unit.
The XFlex X7 will handle flexible packaging and shrink sleeves down to 12 microns. Automation features include plate pre-registration, multiple-camera registration adjustment and automatic adjustment of print pressure depending on change of speed, substrate thickness and repeat length.
New from Lombardi is the Invicta i2 press, with a 36in (1m) repeat length and web width up to 43in (1,100mm). An advanced automation system includes sleeve pre-positioning depending on the change in print format - meaning there is no need for mechanical sleeve adaptors following a format change. Once set, the sleeves are held in place with a pneumatic locking system.
Print pressure is automated with servos on both plate and anilox cylinders, with an additional servo driving chill drum rotation. Doctor blade pressure is automatically adjusted by Lombardi’s Hi-DynamiX system. To keep the press running efficiently the ink chamber can be changed without changing the anilox. Other automation features include auto-register and servo tension control optimized for extensible materials.
Nilpeter was showing a 22in-wide FA-Line machine optimized for flexible packaging, incorporating both UV lamination and UV LED drying. The company was also previewing its forthcoming FA-26, a 26-in wide press optimized for short run flexible packaging and shrink sleeve production. The first press – a 10-color with LED-UV and EB lamination – will be shipped in March 2020, and Nilpeter hopes to have an 8-color machine in its demo room at the end of November. Print speeds will be up to 250m/min and repeat length 12in to either 25 or 32in. Screen, cold foil and various kinds of lamination will also be available.
Automation
As we have already seen, automation of the flexo process was a key theme at Labelexpo Europe 2019.
Automation has perhaps been taken furthest by Bobst, which showed fully automated changeovers on its Master M5 and M6 press lines with no operator intervention. Automated exchange of print cylinders, first seen in prototype form at last year’s Labelexpo Americas, is now a production reality, with a 7-color job changed in one minute with less than 10 meters of waste. The next job can be set up while the current one is running, and once the new plate cylinders and positioned and locked, print and die-cutting pressure and registration are automatically set and maintained.
Also demonstrated on the Master M5 press was Bobst’s new IOD (Ink-on-demand) technology, where ink is delivered directly to the anilox by a pipe, meaning there is just 30g of ink in the print unit at any one time and eliminating the need for ink pans and doctor blades.
IOD is the delivery method for Bobst’s new Highly Automated Liquids (HAL) system, an off-line ink mixing station for producing Pantone colors from 14 basic inks. This means the press is configured both for ECG (CMYKOGV) and ECG+Spot color. Inks are now available to the press as a light and dark shade, and these are mixed and delivered to the press in real time with closed loop feedback from new DigiColor system, which monitors color to a specified deltaE.
A notable new entrant to Labelexpo Europe is China-based press manufacturer Spande, which has created a stir with its highly automated flexo and hybrid press designs. Here, the company launched its S7 flexo press, which has a 200m/min printing speed and is available in 370mm/445mm/515mm web widths.
The press has eight servos in each printing station. Servos are also used in ‘i-Pressure’, a system to automatically adjust printing pressure. The ‘i-Vision’ intelligent registration system uses two cameras to ensure registration accuracy at each printing station, independently.
Semi-rotary format
Another trend worth noting is the continued demand for semi-rotary offset presses. The combination of high print quality, cheap plates, in-line decoration and tight integration with pre-press and standardized color matching options has kept the format very much alive, particularly in areas like premium food, wines and spirits. It is an area where Chinese manufacturers are making an increasing impact.
Codimag has been a long-time player in this sector, and unveiled productivity improvements to its established 420mm-wide Viva 420 Aniflo (short inking) press, with a new web drive increasing maximum speed to 85m/min. A new integrated digital workflow linking to prepress was launched, allowing fast Pantone color matching and decreasing the minimum run length to compete strongly with digital.
Miyakoshi, another sector veteran, showed its enhanced MLP-C semi-rotary offset press, equipped with UV dryers and chill rollers. New features include Cold Start to save waste substrate, and Automatic Plate Change to improve timings on changeovers.
Chinese press manufacturer Wanjie now has its own European technical support base in Spain, and showed the WJPS-350D/450 semi-rotary offset press, incorporating flexo varnish and die-cutting stations as standard but expandable with rotary hot foil stamping, silkscreen and embossing. The press features an auto lubricating system and optimized ink feeding with 18 inking rollers per unit.
Zonten Europe is another Chinese manufacturer to establish a European support base, and showed its ZTJ-330 intermittent offset label press. The ZTJ-330 offers 50m/min printing speed on a 320mm printing width and 100-350mm printing repeat. The inking system has 23 inking rolls and four large diameter form rolls.
Guangzhou Nickel Printing Machinery demonstrated its FS350 semi-rotary offset press incorporating a PMAC motion control system. Each print unit consists of 19 inking rollers and four water rollers configured to prevent ink streaking and ghosting. Each print unit has an automatic positioning system with an inspection camera allowing vertical, horizontal and skew register to be adjusted without stopping the machine.
Weigang showed its ZX semi-rotary offset press, incorporating five offset printing units, rotary hot stamping, flexo varnishing, flat screen, flatbed embossing / hot-stamping and die-cutting.
Semi-rotary flexo is a relatively niche narrow web press format, and like semi-rotary offset has the advantage of no cylinder change between jobs. Iwasaki has been leading the charge here with its IF330 semi-rotary flexo press, demonstrated at the show.
Hybrid
With the bewildering number of different ways digital printing was integrated with conventional (flexo) printing, decoration and converting units at Labelexpo Europe, the term ‘hybrid’ is becoming more and more difficult to define.
When Bobst launched its first hybrid press, the company’s Federico d’Annunzio said he ‘hated’ the word hybrid because it ‘suggests a compromise. This is a digital label press printing ECG plus spot colors.’
Bobst’s new Master DM5 press fully integrates the company’s ‘digital flexo’ system with Mouvent’s ‘Cluster’ inkjet engine technology. The press operates at speeds up to 100m/min at 1200 x 1200 DPI resolution.
As with the Master M5 press, the DM5 press carries out job changes on-the-fly, including flexo, digital, die-cutting and stripping processes. All analogue tools – print cylinders and flexible dies - are changed automatically. Waste stripping is also fully automated. Ink-on-Demand (IoD) will be an optional extra for the ‘DigiFlexo’ print units.
Another key hybrid machine launch was Canon’s 16in Canon Océ Labelstream 4000, displayed in a single-pass hybrid label conversion line with speeds up to 75m/min, including flexo stations, cold foiling and semi-rotary die-cutting.
The major conventional press manufacturers all showed the latest updates to their established hybrid lines except Nilpeter. Company CEO Lars Eriksen said this is because Nilpeter is waiting to integrate the newly upgraded Screen print engine.
Lombardi launched its first hybrid press, the Digistar, using a Domino N601i print engine and Synchroline flexo and converting units. The new press incorporates electronical register and format control, a fixed magnetic cylinder with automatic format correction and the possibility of adding a wide range of units including flatbed screen, flatbed hot stamping and embossing and semi-rotary hot stamping with foil saver.
MPS focused heavily on the launch of a wider, 17in/430mm version of its established hybrid MPS EF Symjet press, developed in partnership with Domino. The new Domino N617i print engine is based on the company’s proven N6-series inkjet product range, but was designed exclusively for MPS, and integrates with the MPS EFA flexo platform.
The Symjet press was equipped with five flexo stations, digital cold foil, a Kurz cold foil unit for single images and optical effects, lamination and die-cutting. The press will still be available in its 340mm/13in variant as well as the new 430mm/17in width.
Mark Andy’s Digital Series HD made its Labelexpo Europe debut, and the company has extended the format size to 17in (430mm) as a better solution to the high demand for digital hybrid shrink sleeve label production. Mark Andy also announced the introduction of Stitch AI, automated print head redundancy technology designed to minimize press downtime and maximize quality material throughput.
Omet showed the XJet hybrid press, which combines Omet’s flexo technology with the Durst Tau RSC print engine. The ‘XJet powered by Durst’ offers a wide range of in-line multiprocess technologies including cold foil, hot foil, embossing, varnishing, peel and seal, delam/relam – as well as converting systems such as Monotwin-Cut variable size die-cut, Twist easy-change die and Rock’n’Roll matrix stripping. XJet is suited to short run work, though its speed of 78m/min combined with low ink laydown means it can also cater to medium runs. It prints at 1,200 x 1,200 DPI.
Pigment-based aqueous
In a significant move, MPS announced a partnership to incorporate Colordyne Technologies’ new 3600 Series AP pigment-based aqueous digital print module into the MPS EXL-Packaging product line, primarily for mid-web flexible packaging applications.
MPS’ Eric Hoendervangers said: After the successful experience of offering hybrid solutions for the narrow web market we strongly believe that the hybrid technology will also be part of the future for the mid-web packaging market.’
Colordyne’s module is based on Memjet’s new DuraLink aqueous pigment printhead technology, and the MPS announcement came as Memjet took its first booth at a Labelexpo show, clearly signaling its intention to become a major player in the label and flexible packaging space. Memjet’s aqueous pigment technology offers longer printhead life and enhanced durability through greater water fastness, light fastness and rub resistance.
Colordyne’s 3600 Series AP digital print engine was shown on the Kao Collins stand. Colordyne says the technology offers longer printhead life and prints with a resolution of 1,600 x 1,585 DPI with print speeds up to 668ft/min (204m/min). The pigment inkjet is compatible with a greater number of substrates, both coated and uncoated, than dye-based inks.
At the show, Inkjet Solutions was announced as distributor for Colordyne’s aqueous pigment print engines in the UK, India, Canada and UAE. Inkjet Solutions will offer retrofits to existing equipment, or can offer a standalone system through its partner Daco Solutions.
Digital presses
Evolution not revolution was the theme in the digital print engine sector, with manufacturers concentrating on consolidating their technology and increasing its efficiency. Notable trends in inkjet were wider press widths and growing use of low migration inks. On the electrophotography side key trends include fully embracing the flexible packaging world and the continued development of embellishment and workflow eco-systems around the press.
• Inkjet
Durst launched a new version of its Tau label press, the Tau RSCi, which builds on the existing RSC but with a new more modular design. The press incorporates automated nozzle compensation, which uses a camera to detect missing print and automatically remaps the image to working nozzles. This can be retrofitted to older RSC machines. Jumbo winders and chill rollers are now standard.
Print speed of the new press is 100m/min (328ft/min) at 1200 x 600 DPI resolution and 80m/min at the maximum 1200 x 1200 dpi resolution. It will be available in wider 420mm (16.5in) and 508mm (20in) widths as well as the existing 330mm (13in).
Also announced by Durst was a new high opacity White Print Mode for all the Tau RSC printers and a High Speed White Mode that allows the RSC printers to run at up to 80m/min for all colors including white. Durst also has a new low migration inkset that is compliant with EUPIA and Swiss Ordinance regulations for food and pharmaceutical packaging.
Bobst demonstrated the latest production prototype of its Mouvent water-based inkjet press, which is expected to be available in Q1 2020. Speed is currently at 50-60m/min but Bobst says the final version will print at 100m/min in 6-colors. The press will require specially coated materials, but Bobst Mouvent division is also working on a primer and inks, including an 80 percent opaque white. Actega is developing the varnish.
Mark Andy added two models to its entry-level toner-based digital press line-up, each with a print speed of 77ft/min (23m/min) on a 12.5in print width. The Digital Pro 1 is supplied as standard in roll-to-roll configuration with upgrade options for flexo print station and converting. The Digital Pro 3 includes a multi-purpose flexo station for in-line embellishment and a DFE that supports variable data printing and versioning. It can be configured with a single slot die station or with a semi-rotary die module with a standard 19in magnetic cylinder. Current Digital One press owners are eligible for a Digital Pro engine upgrade, increasing printing speed by 70 percent.
Epson showed its latest L-6534VW UV inkjet press in-line with a GM DC330 finishing system. The press, which can run at up to 50m/min in-line with the GM finishing system, features Epson’s high-opacity white ink for printing on clear and metallic substrates. In-line digital varnish can be printed to give a gloss or matte effect, either overall or as a pattern or spot varnish. The Epson remote monitoring system (ERMS) allows engineers to provide remote diagnostics of print performance. A new in-line spectrophotometer designed to ensure consistent color output on all printed media, was also presented.
Screen introduced an upgraded version of its established digital label press, the L350 UV SAI. There are four variants starting with the entry-level CMYK L350UV SAI E printing at 50m/min (30m/min if an optional white is added), going up to the L350UV SAI Z variant with print speeds up to 80m/min and seven colors – white, orange and blue.
There is also an LM model using low migration inks and nitrogen inerting chamber for indirect food contact applications.
Space for an additional head is available inside the press and Screen is currently evaluating functional fluids. The press can also be configured with twin high-powered UV lamps for final cure, allowing new coating applications to be developed. The press web path has now been center-aligned to allow for easier in-line integration.
On its stand Screen was demonstrating a stand-up pouch application on a ‘+’ model press, printing at 60m/min with two additional colors. LM has nitrogen chamber.
Xeikon introduced its new Panther DuraCure UV curing system, which combines LED and mercury technologies to optimize curing of the company’s PantherCure UV inks. UV LED pinning of the white stops bleed into the CMYK inks and pinning after the black ‘freezes’ all colors across the image and maintains a uniform optimal color brilliance and gloss. It is the controlled mixing of LED curing deep into the ink layers combined with HG or mercury curing for lightly curing the surface of the UV ink. Haptic effects can be generated by controlling the cure using a new module in Xeikon’s X800 front end.
• Dry and liquid toner
HP Indigo majored on a complete line for digital printing, laminating and manufacture of stand-up pouches, building on a Labelexpo-wide trend towards short run flexible packaging which HP itself has pioneered. The system consists of an HP Indigo 20000 digital press with Pack Ready Lamination and the Karlville pouch-making machine.
HP also showed an HP Indigo 8000 printing at 262ft/min in-line with the ABG Fast Track die and an HP Indigo 6900 with the new durable Pack Ready for Labels system. Michelman developed its DigiGuard 901 specifically for Pack Ready for Labels, a strengthener for HP Indigo validated UV OPVs used with Michelman’s in-line primers, which enables enhanced water, chemical and thermal durability.
Turning to hybrid digital embellishment systems, HP Indigo demonstrated its ElectroInk Silver which metallizes the color gamut; the HP Indigo GEM UV inkjet embellishment system; and an HP Indigo 6900 digital press connected in-line with the Kurz DM-Jetliner for printing colorful metallic effects in-line.
HP also showcased its brand protection and security offering including HP Indigo ElectroInks invisible yellow and blue coupled with software and cloud-based systems that allow ant-counterfeiting marks, and protected track and trace systems.
In terms of workflow, HP demonstrated its latest online web-to-pack system and the latest HP Production Pro for Labels and Packaging, which allows for a faster rip and better connectivity through the cloud.
Xeikon’s major launch at the show was the Flexflow in-line digital printing and pouch making system. This takes a digitally printed roll from a Xeikon CX500 press and passes it through the LCoat500 thermal laminator to construct the stand-up pouches. The Xeikon CX500 QB-toner has been designed specifically for food labels and takes upcoming migration regulations into account.
Also shown was the Discovery Package, an entry-level system consisting of a Xeikon 3030 digital press and Dcoat digital converting line with varnish, semi-rotary die-cutting, and rewind.
Konica Minolta launched the AccurioLabel 230 digital toner press, running at up to 23.4m/min on a wide range of materials now including PP, PET and synthetic papers. Print width is adjustable between 250 and 300mm. An overprinting option allows the AccurioLabel 230 to print on pre-printed media. Makeready times have been reduced thanks to the fuser being kept warm for up to 30 minutes. Developed and manufactured in Europe with GM, the AccurioLabel 230 has been built on Konica Minolta’s own AccurioPress engine technology.
It is interesting that Konica Minolta also owns the MGI digital inkjet embellishment technology, and a project is now underway to develop a fully digital hybrid system with the 230. MGI is already integrating Konica Minolta color engine technology into its embellishment lines, which are capable of depositing high build varnish up to 230 micron along with digital foiling and variable print.
Benchtop systems
Designed for in-house print operations and label printers setting up bureau-type services, a wide range of benchtop digital label systems was launched at the show.
Astronova launched the QL-300, a 5-color, CMYK+White toner-based table-top printer designed for production label printing. The company also launched the QL-120X on-demand digital color label printer using dye-based inks.
Bixolon introduced the 114mm-wide XT5-40 desktop thermal transfer label printer system. It is available as XT5-40 (203 DPI), XT5-43 (300 DPI) and XT5-46 (600 DPI) print resolution media options. The printer’s standard model (XT5-40) supports fast data processing and print speeds up to 14ips (356mm/sec). It supports a media roll diameter up to 203mm, ribbon length up to 450mm, and features adjustable printhead pressure.
Epson launched four new ColorWorks on-demand digital label printers targeted in-house label users.
GoDex unveiled a new high-speed thermal transfer printer, the ZX1000Xi with print resolution up to 300 DPI print and speeds up to 14in/sec. Options include cutter, Bluetooth and wireless LAN connectivity, external label rewinder, label dispenser and internal rewinder.
OKI showed its 5-color (CMYK+White) desktop label printer, the OKI Pro1050, handling a wide range of media including textured papers and synthetics with white, clear, opaque or colored substrates. It is suited to industrial labels intended for harsh underwater environments and the toners are resistant to UV fading.
Printronix Auto ID presented the T4000 compact industrial thermal printer with a print speed of up to 8in/sec on label thicknesses of up to 0.28mm. Also on display, Printronix Auto ID’s fully integrated thermal barcode printer and validator, ODV-2D, can now additionally validate QR codes as well as 1D and 2D barcodes.
Primera Technology debuted the LX610 all-in-one color label printer, developed for proofing and prototyping.
TSC Auto ID launched a new digital label printing system that includes the dye ink CPX4D and pigment ink CPX4P.
UniNet introduced the iColor 540 toner-based digital transfer A4/letter sized printer, printing full color combined with white overprint and underprint capabilities in a single pass; the iColor LF200 compact digital die-cutter and laminator; the UniNet iColor 200 desktop inkjet printer for continuous roll-to-roll printing with either dye- or pigment-based ink; and the iColor 700 digital label press using low fuser temperature technology to print on film-based substrates.
VIPcolor displayed the VP750 digital print-on-demand color label printer using water-resistant ink technology for producing colored labels for applications such as chilled food and other moisture-exposed products. The VP750 prints at up to 18m/min with a resolution of 1,600 x 1,600 DPI on a printable width of up to 215.9mm.
Additional information by Yolanda Wang.
Stay up to date
Subscribe to the free Label News newsletter and receive the latest content every week. We'll never share your email address.