Challenges and opportunities in pharma
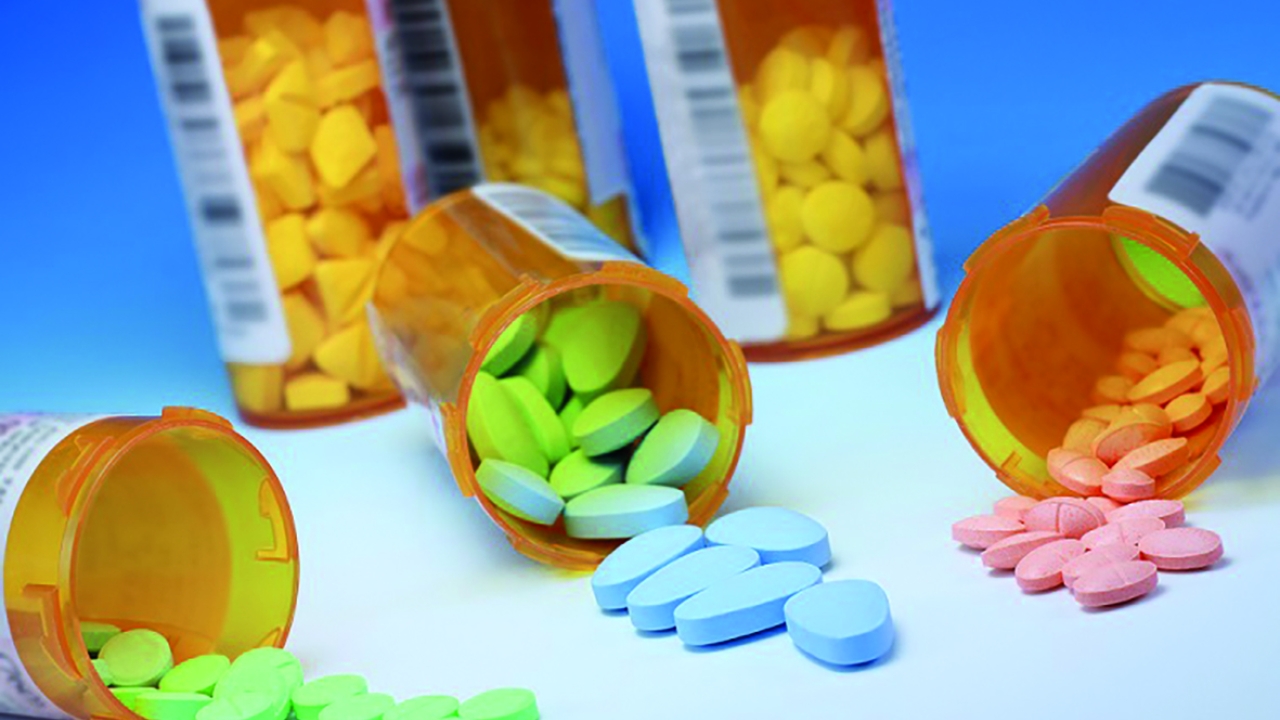
Laura Johnson, life sciences expert at enterprise labeling specialist Loftware, adds that the picture is complicated further by the global nature of the pharmaceutical industry. Then there is a trend towards progressively smaller batch sizes, while manufacturers are legally required to provide more and more information about the product. ‘Country- or market-specific information is often provided by means of labels,’ explains Nägele. ‘Moreover, many legal standards, such as regarding tamper evidence, can be easily and very efficiently fulfilled by means of labels.’
As such, he sees self-adhesive materials and labels playing a crucial role in the pharmaceutical industry. However, Steve Wood, president and CEO of Covectra, notes ‘a real need for a more secure label than currently exists’. Counterfeiters, he says, are able to replicate a label with a barcode that is legitimate and GS1 compliant, and to replicate the same legitimate barcode many times over, with detection in the supply chain taking a long time.
Regulatory compliance
An evolving regulatory landscape continues to be a big talking point for the industry. In a recently published white paper, Avery Dennison states that all manufacturers of pharmaceutical packaging have to meet the challenges posed by new regulations and stronger packaging guidelines. A recent survey on the state of label management in the pharmaceutical industry, undertaken by NiceLabel, reveals that 80 percent of respondents list compliance as the number one driver when selecting a label management software.
The Falsified Medicines Directive (FMD) comes into force in Europe in 2018, while in the US, enforcement of the Drug Supply Chain Security Act (DSCSA) has been delayed by a year. Dave Harty, head of professional services in the Americas at Adents, sees postponing enforcement, rather than delaying the official compliance deadline, as a ‘deliberate and very clear signal’ from the FDA that the law remains in place and is not going to go away or suffer multiple further delays.
‘After all, the law is intended to make the drug supply chain safer and, ultimately, save patients’ lives by protecting them from counterfeit medicines. It is more than likely that this suspension of enforcement for 12 months will entail a complete zero-tolerance approach in 2018 as anyone not in compliance would technically have been in violation of the law for a full year.’
However, he says: ‘A delay in the enforcement date will provide invaluable time for pharmaceutical companies and contract manufacturers to look beyond short-term compliance needs and consider long-term solution viability.’
In addition to compliance with DSCSA, there is also the FDA’s Title 21 of the Code of Federal Regulations (CFR) Part 11, which provides guidance for electronic records and eSignatures to streamline workflows.
Products
Research and product development play a key part in allowing the industry to achieve these requirements, especially when other considerations are taken into account, such as cost pressures and label application, and guidelines on plastic immediate packaging materials, medical devices and blood bag labeling. The speed of pharmaceutical packaging lines, for example, means ‘labels must achieve reliable adhesion within fractions of a second, on products which are often round with very small radii,’ says Nägele. ‘This results in large elastic forces affecting the labels.’
Herma 63Mps is a special adhesive for pharmaceutical applications based on the company’s multi-layer technology, and with a strong initial tack coupled with migration levels, even through thin PE films, below the limit of determination. This is identified as highly relevant for the pharmaceutical industry with HDPE and LDPE plastics increasingly used to replace glass containers. HermasuperPerm (63S) is a one-layer adhesive with final adhesion said to be so high that sealing labels equipped with the adhesive cannot be removed from lacquered pharmaceutical packaging, as well as many other polar and non-polar surfaces, without destruction of the label or the packaging surface.
Avery Dennison has developed several pharmaceutical labeling adhesives that follow and adhere to the various guidelines mentioned above, and their associated regulations, including S2000NP, S692NP and S717P (plastic immediate packaging materials), S692NP and S717P (medical devices), and AL171, C2020P and S2060NP (blood bag labeling).
UPM Raflatac’s latest development sees the introduction of RPMD (Raflatac permanent medical device) adhesive range to further expanded its range of guaranteed, globally available, and compliant pharmaceutical and healthcare label materials for the medical device and healthcare industries. Combining selected paper and film face materials with an RPMD adhesive ensures adhesion with a tight mandrel hold on glass and plastic, as well as sterilization resistance and migration safety.
StellaGuard from Covectra and Schreiner MediPharm’s Flexi-Cap for Clinical Trial Supplies (CTS) evidence yet more areas where innovation is taking place. StellaGuard is a security label featuring a random pattern of holographic symbols embedded in the proprietary label film when it is manufactured. Flexi-Cap for CTS has been developed for the specific requirements in clinical trials, such as a reliable blinding and first-opening protection.
Software
Software also plays an important role in ensuring production of accurate, compliant labels. The NiceLabel survey shows the importance of a single, centralized platform for label design, change control, printing, integration and management. Document control, integrating label management systems with ERP/MES and other systems, web printing, and scalability are identified as the most common challenges in an increasingly complex and fragmented production environment that often involves managing multiple products, locations and markets.
Ken Moir, vice president of marketing at NiceLabel, says: ‘Only 14 percent of those surveyed have achieved 100 percent integration with their MES/ERP system. Over 34 percent are still using separate systems to manage their labeling and marking printers. Having disconnected systems makes it extremely difficult to update and maintain label databases, and it means pharmaceutical manufacturers are missing out on the productivity and quality gains that can come from a fully-integrated label management solution.’
Another survey, conducted by Loftware, found that 47 percent of 200 manufacturing professionals, including many from the pharmaceutical industry, indicated they were experiencing costly downtime due to labeling disruptions. The reasons cited for these delays included dealing with customer-specific labels, product-specific labels and slow label printing speeds.
‘When you add up all of these isolated labeling issues occurring across different segments of your supply chain, you’re looking at hundreds of thousands of dollars of lost productivity, severely impacting your bottom line,’ says Johnson. ‘An automated process allows companies to achieve significant printing performance gains, allowing labeling to keep up with production.
‘A centralized approach to labeling allows companies to integrate the labeling process with their existing ERP, PLM, or other validated environments to drive data from “sources of truth,” which offers greater control. By using a central database, companies can avoid the need to replicate data, which reduces errors and offers improved labeling consistency for deployment to other plants and distribution partners internationally. This ultimately provides a new level of consistency, simplifies troubleshooting and streamlines labeling, helping to drive greater supply chain efficiency. When labeling is integrated with the enterprise business processes rather than in a stand-alone system, processes are simplified and non-value added activities, such as regulatory updates, are reduced.’
Antares Vision, a provider of serialization-based track and trace options for the pharmaceutical industry, launched Quick Compliance Program, claimed to enable serialization compliance within 10 weeks from the project start. The program is based on preconfigured modules in concert with a standardized package of software, documentation and services. As well as a Reel 2 Reel module, an off-line labeling printing station to produce reels of serialized labels suitable for bottle labeling, the program runs Antares’ GTS Plant Manager software, which generates or imports serialization numbers and stores all data while interfacing with Level 4 repositories.
Continues Johnson, ‘Labeling is complex; today’s pharmaceutical organizations are faced with a range of evolving requirements that complicate the process, and leave many companies accepting outside changes and regulatory updates to the process as a cost of doing business.
‘But it doesn’t have to be. Labeling can make a huge difference, enabling IT and supply chain decision makers to overcome challenges, and provide their company with a distinct competitive advantage.’
Future-proof
Investments in technology support R&D and new product development going on in the supply chain.
Herma is investing heavily at its headquarters in Filderstadt, Germany, including an all-new coating plant that will be used to produce self-adhesive materials and prepare them according to customer requests. Also in Germany, August Faller has invested in digital printing to meet growing demand for shorter runs and delivery times in the pharmaceutical market (see boxout). Spain’s Etiquetas Adhegraf, where 80 percent of production is dedicated to pharmaceutical products, has commissioned a Screen Truepress Jet L350UV digital label press for its repeatable print quality and precise accuracy. US printer Dion Label has invested in new digital and servo-driven flexo presses, as well as color management systems, hardware and document control software to ensure precise color standards are met and procedures followed.
‘For Dion, it’s about investing in the right equipment along with the best team to ensure we are providing the highest quality products for our customers while maintaining compliance,’ says a spokesperson for the printer.
‘We are looking forward to new challenges, which will come from the pharmaceutical market’s dynamic development regarding labeling, as many new legal requirements are being added throughout the world,’ concludes Nägele.
Stay up to date
Subscribe to the free Label News newsletter and receive the latest content every week. We'll never share your email address.