Luminescent colors: a special challenge for quality control
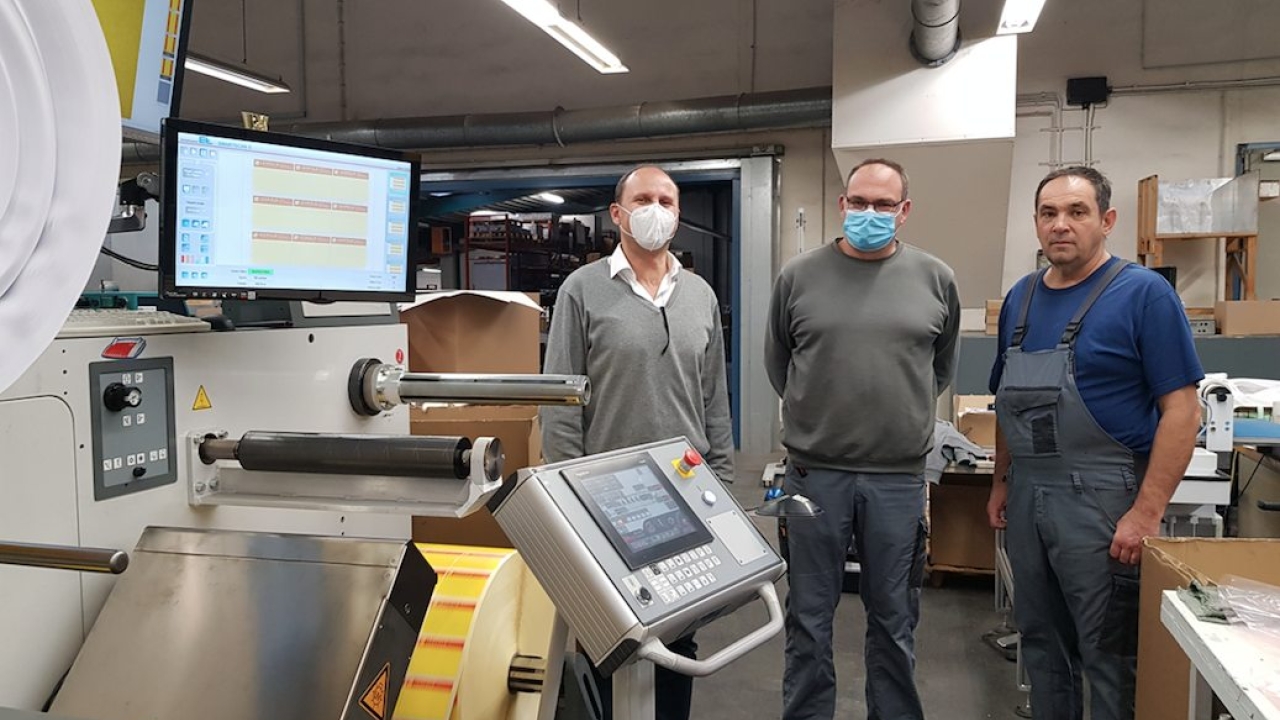
This question occurs when luminescent colors or varnish are applied to the web during the printing process. Whether a classic safety print for pharmaceutical applications or to refine products, UV applications are becoming ever more common. But how can the converter guarantee that the printing corresponds to the customer’s wishes? That the position, completeness or simple presence are correct? This was a question that German converter Oscar Mahl set out to answer.
Oscar Mahl, from the Schwäbisch Hall area of southern Germany, is a medium-sized company in the ownership of the Mahl family for over 100 years. With its own pre-press and a wide range of printing methods including flexo, offset and digital, the converter can cover a broad spectrum of printing challenges. Some time ago, Oscar Mahl determined that 100 percent testing of the print was required to comply with its quality assurance program. It uses camera systems for 100 percent inspection both on presses and finishing machines. However, until now, this was limited to visible print applications. By contrast, UV applications represent a special challenge.
The greatest problem with print image inspection systems is usually the choosing of a specific illumination method. Usually, it is necessary to choose between white light and UV light illumination variants: white light to illuminate standard colors or film applications; UV light to make those colors, varnishes and adhesives visible that react in ultraviolet light. Simultaneous use of the two lighting variants is usually insufficient, or no solution at all, as the different brightness levels have a negative influence on each other. The main reason is that the brighter white light component completely outshines the UV light component.
Sufficient excitement of the UV particles is thus not possible, or only to a limited extent.
Knut Schulzke, head of production in the web-fed printing division at Oscar Mahl, found his answer with inspection specialist Erhardt+Leimer’s ‘200 percent’ inspection system SmartScan. The technology of the ‘200 percent’ inspection was not unknown to Schulzke. For some time, two systems have been used on printing machines for daily quality control. Even in the standard version, these offer the benefit of inspecting the web with changing illumination methods. In this way, besides classic printing errors, errors in the material can also be detected - something not possible using a purely incidental light inspection source in a 100 percent inspection application.
SmartScan UV
SmartScan UV also uses the ‘200 percent’ technology to inspect the web using the two illumination variants, LED white light and UV LED light, in parallel. The web is differently illuminated in sequence at full speed. The camera saves a reference image of each illumination variant, the so-called Golden Template. During the inspection run, the live images are compared with the corresponding reference image and checked for defects. Detected defects are saved in the corresponding illumination sequence and displayed to the user. In addition, besides automatic defect inspection, the system also offers the machine operator a full-quality viewer, which shows the print image on the monitor using the appropriate illumination method.
The camera works with a resolution of 4,096 pixels transversely to the web. Errors can be zoomed in on directly on the monitor using the intuitive touch control. The separated illumination method shows the UV applications at optimum contrast levels.
‘This was exactly our expectation for a camera system,’ says Knut Schulzke. ‘According to requirements, we use the classic 200 percent check with incident / transmitted light illumination, or we switch over to combined LED white light / UV light operation. This technology finally gives us the necessary quality control.’
It was also important to maintain the simplicity of the system. Even with the SmartScan UV, single-button operation remains at the forefront. A single press of a button and the system is ready to go.
‘We have spent a lot of energy in the handling of SmartScan, in order to ensure that anyone can operate the current systems with the minimum of training and without major prior knowledge,’ explains Alexander Thomalla, product manager at Erhardt+Leimer. ‘We want to continue to focus on this user-friendliness to give the machine operator space to go about their daily business.’
Stay up to date
Subscribe to the free Label News newsletter and receive the latest content every week. We'll never share your email address.