Package print processes – Which is the right one to choose?
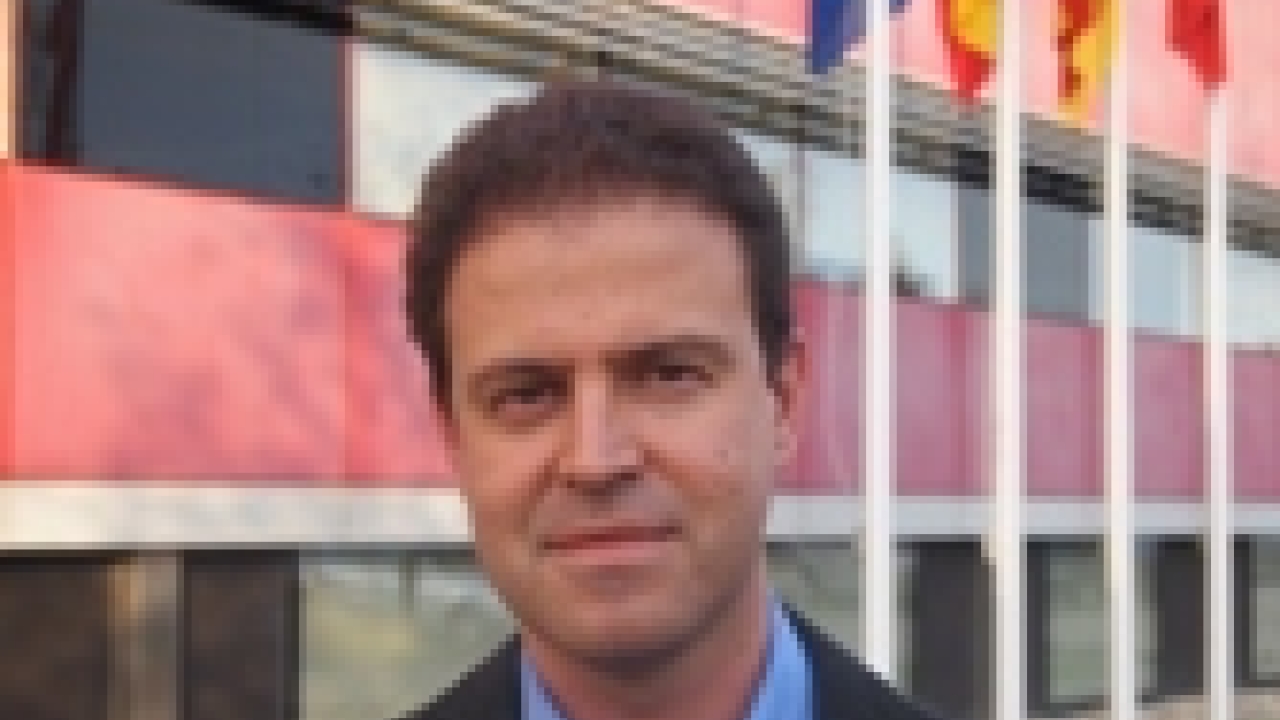
Agusti Combis (pictured, left), marketing director of the Comexi Group, looks at the differing requirements and relative merits of print processes, and assesses the effects of new technology
From a global perspective, packaging is a multi-billion market, consisting of metal and glass packaging, corrugated packaging, flexible packaging, folding cartons and labels. Current estimates put the value of printed packaging globally, excluding glass and metal, at approximately US$55 billion.
Research indicates that flexible packaging will become the market leader for growth in the years to come, mainly as a result of the population growth and changes in living standards and lifestyles of those in the emerging countries like India and China.
For this market application, CI flexo technology is considered the best suited for short-runs and light gauge material, which are shown to be the clear trend. Self-adhesive, wrap-around and shrink labels are best suited to in-line flexo technology.
Additionally, flexo presses can sharply reduce the emissions of VOC, using the new flexo electron beam (EB) inks, and are far more environmentally friendly, with drastic reductions in energy consumption.
However, offset and gravure also play an important role in this sector. Offset technology focuses principally on folding cartons, paper packaging and certain types of niche labels. It is considered the finest printing technology in terms of quality, with associated low costs of printing plate manufacture. The big debate is over its printability potential for flexible packaging, produced on non-absorbent materials. There are well-documented instances in the industry, where converters and machine manufacturers have attempted to switch into flexible packaging without the essential experience in this type of print production. The results have, in most cases, been disastrous.
The adoption of UV and EB inks however, have brought very good results, and are now well proven technology in the paper packaging and folding carton markets. Gravure printing also has an excellent reputation for high-quality.
Broadly speaking, it is mostly used in the flexible packaging market, but is facing severe environmental concerns regarding VOC emissions, which must be seen as one of its weakest points. Brand owners, however, like it, and currently consider it to be one of the best printing technologies when it comes to quality. In recent years, flexo printing has reduced this quality gap considerably, largely as a result of the breakthrough made in flexo press technology, flexo plates and anilox rolls.
Packaging in the future
There are a few general trends that need to be considered when looking to the future. For example, the general consensus is that flexible packaging, produced mainly from plastic-based material, and a clear reduction of the package size, are going to be the main issues in the years to come. Basically, the drivers for these are the needs of the emerging countries, which favor small size packaging, and concerns over emissions, which is one key area of advantage that flexible packaging enjoys compared with other materials.
High barriers films and eco films will gradually take the place of standard material, although films like polypropylene, polyester and polyamides will continue to feature highly in the demands of the brand owners during this period of transition. The pathway to this more eco-friendly packaging embraces not just the films, but also the inks, the converting processes and the logistics.
Inks will also have an important role to play. This is based on concerns over VOC emissions and food contamination from certain components of the ink. There is a definite trend towards curable inks in the flexible packaging market, and while UV inks are broadly used in the label and folding carton markets, there are concerns regarding food contamination caused by the photo initiators. Not surprisingly, therefore, the food industry is quite wary about their usage for even indirect contact with the food.
If UV inks have problems, one should consider EB inks, which have superior print quality. Consumption of EB curable ink is less than half that of solvent-based equivalents. This is simply because no solvents or water have to be evaporated and therefore do not need to be added during production. The savings are considerable. Additionally, the enormous energy consumption of hot air dryers, incinerators and VOC abatement systems are not part of the EB curing process
Market drivers for the print technologies
Regarding quality, it is generally acknowledged that offset printing is at the top level, however, there are serious concerns about the feasibility of using offset for printing on flexible packaging substrates. Gravure printing, however, performs far better with standard flexible packaging materials, and is also superior in quality to flexo printing.
Time to market is another key issue, and another example of where offset printing is outperforming gravure and flexo, thanks to the capability of manufacturing plates in very quick time.
Flexo technology is not far behind this now, but it still needs more time to carry out the same process. Gravure cylinders in general, especially in the western markets, come last in terms of time to produce. There are instances of short delivery times in gravure-oriented countries, like China and Japan, where their huge industrial capacity allows them to carry out the process faster than in Europe or USA.
On the cost side, we include the price of the substrate, the price of ink, the cost of the image transfer (plate or cylinder), the waste cost and, of course, the investment cost as the most important parameters that affect the price per sq m. Taking all these factors into account, offset printing is considered the best from the image transfer price (plate cost) point of view. Flexo printing has a positive impact when the investment, cost of inks and waste cost are considered.
Unfortunately, gravure printing does not excel in any cost parameter compared with offset and flexo.
Eventually, the environment is going to be a major driver. Currently, it is not considered as the key factor, but this will change. Thus, from the sustainability point of view, offset printing has a good reputation and has demonstrated its commitment with UV and EB inks. EB flexo inks will also play an important role. On the contrary, UV flexo inks are leading in label printing and are widely used in the industry. Up to now, gravure printing makes the worst contribution to the environment owing to its VOC emissions with standard solvent inks.
Defining terms
If you Google the words ‘productivity’ and ‘efficiency’, you get the following results:
Productivity is the relationship between output from a production process and the resources used to obtain that very same output. It can also be defined as the relationship between results and the time used to obtain them; the shorter amount of time needed to obtain the expected result, the more productive the system is.
Efficiency is defined as the capability to have someone or something at your disposal in order to achieve a certain effect.
Efficiency is the relationship between the results obtained (profits, goals fulfilled, products, etc.) and the resources used (manhours, capital invested, raw materials, etc.). If we search for the connection between the two terms, we find that efficiency in productivity is achieved by applying new concepts to get the same results in less time.
Based on this, new classes of flexo presses need to be manufactured. They should incorporate all the requirements that, as a general rule, improve efficiency and solidity (stability and reproducibility) on short, medium and long runs. In addition, with improvements made to ergonomics, they will take efficiency to its purest state. One of the hardest challenges involved with efficiency is maintaining it over a period of time, or in other words, in daily production throughout the life of the press. It has been proven that productivity decreases with time, and thus they are inversely proportional. This concept seems contradictory bearing in mind that the longer a machine has been in production, the more experience the printers and assistants have in handling it.
The real situation, however, is that the longer a machine has been running, the more inefficiencies appear in changeovers, which take longer, and the average running speed decreases. This is mainly due to poor maintenance, which renders some of the supporting technology non-operational.
There is no perfect solution for producing the printed packaging of tomorrow. Like most processes, improvements tend to be evolutionary as opposed to revolutionary, but if we are to create a world of package printing in which all interests are best served, we need to continue to invest in research and development so that the technology continues to raise the benchmark.
Stay up to date
Subscribe to the free Label News newsletter and receive the latest content every week. We'll never share your email address.