Plates for the label industry
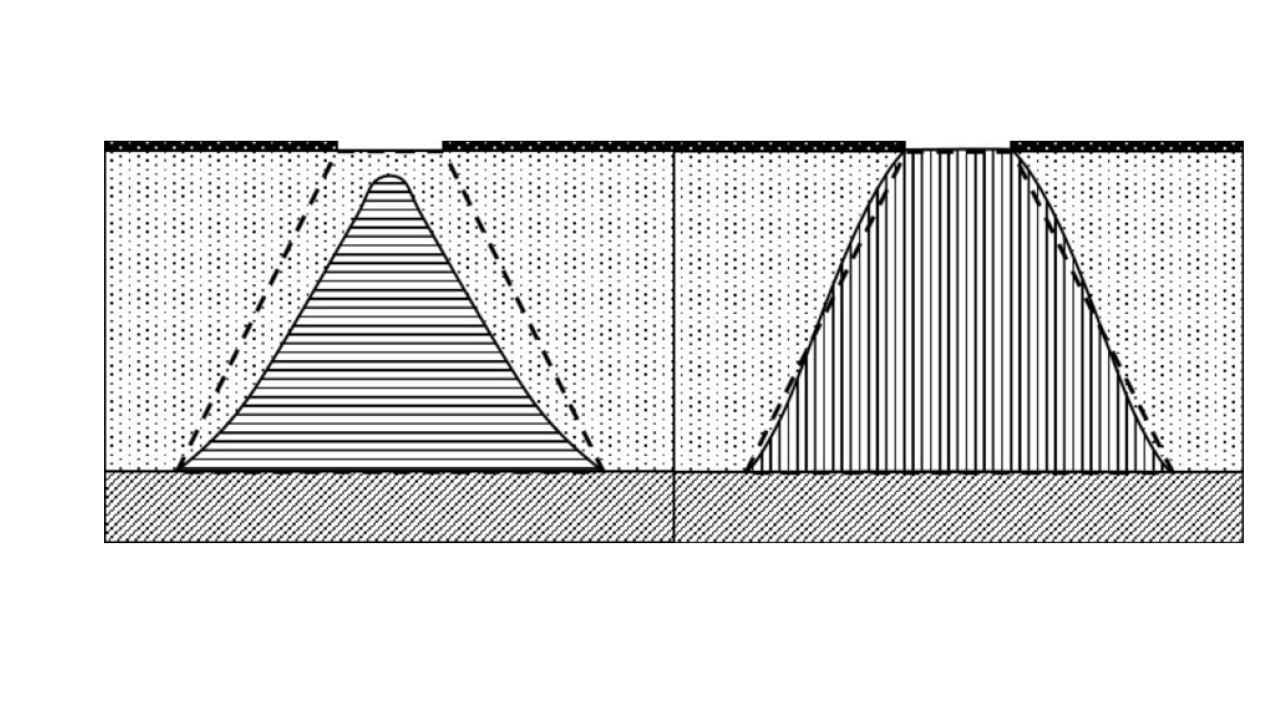
Flexo
The importance of the plate in this process is absolutely paramount and cannot be ignored. It is the final frontier before the ink is deposited on the paper or film. In the early days, all the plate had to contend with was whether water-based or solvent-based inks were being used. Today, however, there are many more considerations thrown into the melting pot, including UV and LED curing, low migration inks and special varnishes. The main processing technologies do not appear to have changed too much – apart from exposure and processing machines being more automated.
Several flexo plate technologies are available from the major plate manufacturers. A summary of the different techniques shows how each manufacturer has approached the problem of producing the finest dot definition with ease of processing. In addition, a wide range of shore A hardness plate surfaces are available according to the final application, with around 60-65 being the average hardness except for printing on soft substrates or corrugated stock when a Shore A of around 55 would be acceptable. A plate thickness of 1.14mm is fairly standard in the label and narrow web industry. Once the ink regime has been agreed, selecting the right plate begins with choosing the right Shore hardness for a particular application. Several of the manufacturers offer a capped flat top plate which is claimed to reduce significant dot gain or a round top plate to give shaper dots, with or without a micro grained surface for extra ink transfer.
Traditionally, photopolymer plates have been processed using aggressive solvents containing high quantities of VOCs (volatile organic compounds). Over the years, safer solvents have been introduced to make the workplace safer. At the same time, water processed plates have appeared on the scene. In this article we examine some of the technologies available, including laser exposed plates with and without an ablation layer. Recently, thermally processed plates have been introduced which do not use any solvents. Most manufacturers supply a plate suitable for solvent processing.
Thermally processed plates
Thermally processed plates do not need any solvent- or water-based processing solutions and are completely dry. The system works by removing the unexposed polymer on a developing roll. After finishing with UVC radiation, the plate is ready to use in under one hour. Plates can be digitally imaged using a laser or exposed in a conventional exposure frame.
MacDermid has recently introduced its Lux ITP Epic plate, which provides capped flat top dot capability straight out of the box. The plate surface has a unique micro-rough surface which, the company claims, delivers great ink transfer characteristics. The result is a 1:1 reproduction image capability from the digital file allowing a smaller dot to be printed. The medium Shore A hardness of this material is ideal for fine detail label printing. The plates can be processed in either in a solvent or Lava thermal processing system. The compatibility of the plates includes water-based and alcohol-based inks, while a special low swell plate UVR is available for UV inks.
A new range of thermally processed plates has recently been introduced by Flint Group. The nyloflex Xpress thermal plate range includes flat top dot plates – nyloflex XVH and XFH digital – with or without a textured surface, which gives improved ink transfer in solid areas and greatly improved dot reproduction. Round top dot versions are also available – nyloflex XPH and XPM – for use with flat top dot exposure for further tailoring to meet specific needs. After exposure, the developing material in the thermal processor effectively removes all the unexposed polymer leaving a clean area surrounding the dots. A recently introduced feature of the nyloflex Xpress thermal processor is the use of a targeted short wave IR pre-heating system which only heats the surface layer of the plate, thus saving up to 88 percent electricity consumption and meaning that a chiller or vapor handling system is not required. The plates, which give a result at least equal to solvent-produced plates, are ready for use within 45 minutes.
DuPont is marketing its range of Fast thermal workflows which includes, for example, the Fast Easy EFX plate which has a built in flat top dot and a smooth plate surface which allows bespoke micro screening of solids and high density ink transfer values along with minimal dot gain. The flat top Fast EFE plate, with an engineered surface, has a completely new polymer giving improved ink transfer and higher resolution. The DFUV plate is designed to be used specifically with UV inks. The plates are given a back exposure before digital imaging and then following processing, finished using conventional light finishing. The new Cyrel Fast 1001 TD thermal plate processor has been redesigned and streamlined offering up to a 63 percent reduction in energy consumption. The improved thermal management system and a multiple heated roller design deliver a consistent clean out of unexposed polymer, a clean relief depth and a clean and uniform plate floor.
Water washable
Asahi attacks the environmental issue with its Clean Transfer water wash technology. It incorporates Pinning Technology for Clean Transfers (originally Pinning Top Dot) which provides a simple way to improve print quality. This is achieved by using a lighter impression pressure allowing finer dots – less dot gain – and consistent print quality to be achieved, the company claims. High print quality and excellent press performance are just two of the advantages claimed by Ashai. A recent improved version of the AWP-DEF plate, the AWP-DEW brings even more improvements in print quality. Because aggressive solvents are not used in the processing of the plate, the company claims, excellent plate stability is achieved in under an hour. The plates can be used with UV inks on a wide variety of substrates. With the wider introduction of fixed color palette printing in flexo eliminating the need for spot colors, the company claims that the AWP-DEW plates are ideal as they offer a stable print quality over the complete production run.
Fujifilm introduced the Flenex FW water washable plate some time ago. The plates are compatible with many flexo LAM CTP devices and with many water-wash processors on the market. The plate contains a special rubber-based coating which is not oxygen-sensitive, minimizing the effect that oxygen can have on the final shape of the dot. This means that a flat top dot can be achieved easily with, the company claims, reduced dot gain and improved durability. Washout is achieved by using water and a mild detergent which means minimal plate swelling. Plates can be produced in about 40 minutes and are press ready. All versions of the plate can be used with any UV, water-based or solvent-based inks.
Offset litho
Another widely used technology used in the label industry is offset litho. This technology uses aluminum plates where the image is in the same plane – in other words flat – which means that the substrate used in litho printing must be relatively flat. The process works on the principle that ink and water do not mix. Conventional offset printing plates have an image which attracts ink and a background which rejects ink. The background of the plate is kept damp by a series of rollers applying a fountain solution and the ink is applied by another set of inking rollers, the balance between the inked image and the background is crucial and needs expertise to maintain that balance.
However, the offset printing industry has enjoyed the introduction of waterless offset printing, which does away with the requirement to maintain that balance. This is achieved by the application of an ink resistant silicon rubber coating. Although waterless litho has been around since the mid 1970s, many developments over the years have meant that today’s plates are capable of producing high-quality printed images. Toray’s waterless plates requires a temperature-controlled ink duct to enable the silicone coating to function correctly at a constant temperature. A thermal CTP unit is required and special dedicated UV/oxidative inks. A Toray or approved waterless plate processor is essential.
A typical plate from Toray is the new Imprima LJ plate, which is compatible with UV-based and oil-based inks. A key advantage is that the plates do not need post-baking, a technique for improving the run length of plates which dates back to the 1970s. The Imprima SD plates, imaged using a thermal layer, can be used to reproduce FM and AM screening images.
Over the past ten years or so, UV inks have become widely used to replace solvent-based inks in the label industry. Kodak (the flexo division is now renamed Miraclon) has therefore been developing new offset plates that can be used with these UV inks. The introduction of LED curing UV inks has revolutionized this ink technology and widened its scope considerably. Traditionally, offset plates need to be baked to withstand the effect of these aggressive inks. Kodak’s newest plates, including the Electra Max thermal plate, have efficient resistance to the solvents without baking. The Kodak Sonora XP and UV Process Free plates eliminate the need for water processing, thereby adding considerable environmental benefits to the plate processing segment as the plate is cleaned on the press. Using laser CTP imaging technology, the Kodak Squarespot system offers, the company claims, improved dot control throughout the entire print run.
This has been a snapshot of the current plates which can be used in the label industry. It is not exhaustive and new editions of both flexo and offset litho plates will be exhibited at the upcoming Labelexpo Europe in Brussels in September.
Stay up to date
Subscribe to the free Label News newsletter and receive the latest content every week. We'll never share your email address.