Fighting back
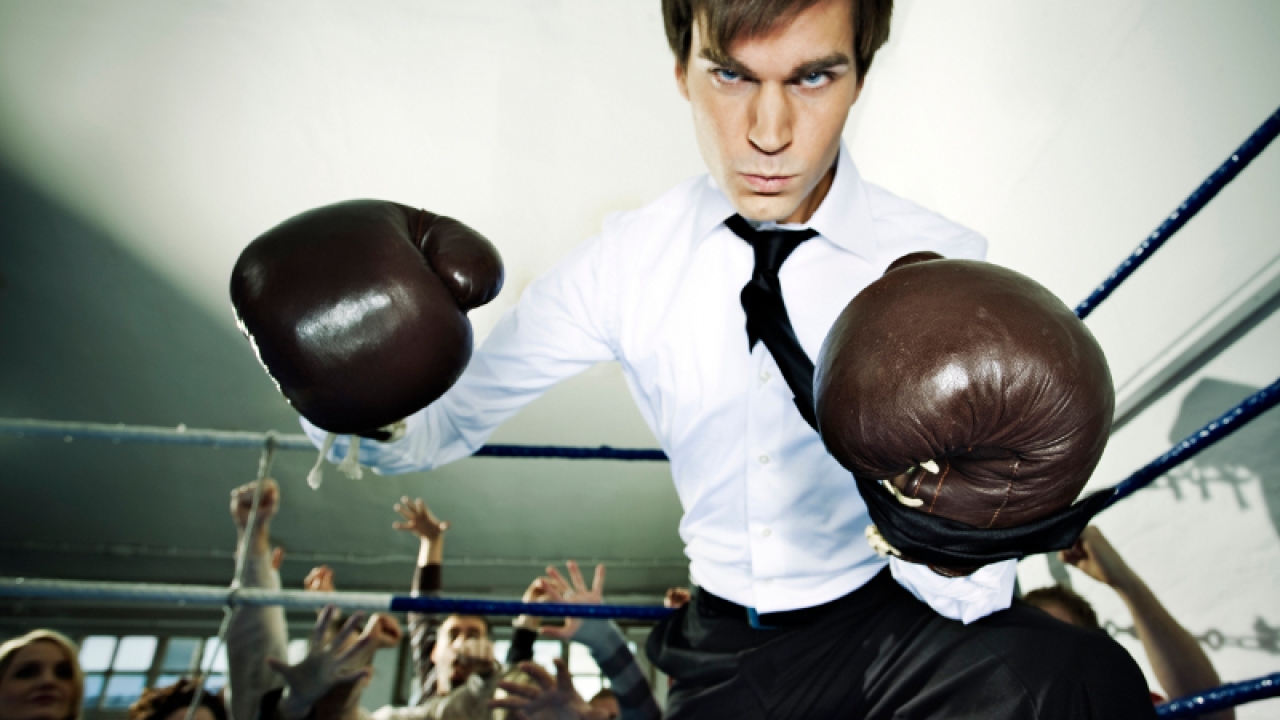
David Lanska, chairman of the FTA Great Lakes Group, reports on the group’s last meeting, which saw suppliers and end users attempt to put the current economic situation into a positive perspective
Adjusting to the harsh reality of a prolonged economic downturn, companies have had to brace for the uncertainty by taking extraordinary measures in their operations. These have included reducing R&D and marketing budgets, delaying or cancelling new equipment acquisitions, slashing benefits and salaries, and ultimately reducing the size of the workforce. And while optimism abounds about the eventual recovery, that optimism has yet to fully transition into confidence.
If you rush from one critical situation to another with cell phones in each hand and a beeper on your belt, it is likely that you are so focused on fighting fires that you miss the bigger picture. If you can’t always see the forest for the trees, you should have been at the December meeting of the FTA Great Lakes Group. Held at Fox Valley Technical College’s Bordini Center, the speakers went to great lengths to put things back into perspective for the audience.
Seeing the plate for the dots
For Tim Reece of All Printing Resources, a key to consistent repeatable print quality is consistent plate quality. Plate quality results from interaction of processing variables including exposure, washout or dry removal times, post exposure and detack. Rather than fighting with the system by guessing, Tim advocates using the clues you are given to diagnose what went wrong and how to fix it. Those clues are measurable quality indicators such as:
- plate thickness and relief
- dot size and uniformity
- box ratio (height of dots divided by width – ideal ratio is 1:1 with +/-10 percent tolerance, while a 1.2:1 ratio indicates elongation or a slurred dot)
- circularity (pixilation vs. smoothness of the radius – ideally .9 to 1.1)
- dot and area percent (physical and optical dot size) – A discrepancy of more than 2 percent indicates an ink transfer problem.
- plate hardness
To control these characteristics, you need to be able to measure them. Everything typically starts with a visual inspection of the plates or print samples. Aided by a loupe or scope, the human eye identifies any obvious red flags that indicate a potential issue. At that point, it is time to break out the tools of the trade.
A black and white transmissive densitometer used in laser set-up ensures it is operating at peak performance. Laser setup is based on several factors: plate thickness, focal length, type and reflectivity of the black mask material, cleanliness of the lens and aggressiveness of the laser. Using a loupe and the human eye, a visual inspection of a 50 percent Euclidean screen shows a perfect checkerboard effect. If the laser is running with too much power or the drum is turning too slowly, the laser ablates more material than you want. In this scenario, a 10 percent dot will be much larger than a 10 percent dot. If, on the other hand, the laser is running at too low of a power setting or the drum is rotating too fast, the laser will not ablate away enough material and the 10 percent dot will be smaller than desired. Tim recommends verification of laser performance on a weekly basis.
Micrometers measure plate thickness and relief. Variation in plate thickness or variation from standard both point to a probable drying issue. Excessive relief - as indicated in the box ratio - results in slurred dots, particularly on fine highlights, as the shoulders do not properly support the peaks. The plate analyzer measures a number of variables including box ratio, circularity and dot percentage.
Plate relief is important for several reasons. It is desirable to have a deeper plate relief for solids than screens. You may want significant plate relief such as .03 if you are running solids with reversed-out type. If, on the other hand, you are imaging a screen, you want less relief to ensure proper support for the highlights.
Measuring raw material ensures it is consistent in thickness across a given plate. You may also want to measure it because the material is subject to normal process variation from batch to batch. Material that comes in at .068 thickness may be labeled as .067 material. If it comes in to your facility at .068, that is its optimum thickness. That tells you that when it comes out of the drier at .068, it is properly dried. Additional drying at this point only wastes time and could be detrimental to the plate material. Material that comes in at .066 would not be properly dried at .067 and would require additional drying time.
Handheld micrometers are cheap, but hard to use and direct contact can affect the reading. A bench micrometer is limited to the distance of the throat so cannot take readings across a wide plate. An optical micrometer is non-contact, but is more expensive and accuracy is subject to operator variation.
Plate analyzers are useful in measuring dot quality, which has become much more important as digital imaging has begun to proliferate. The flat top dot is much easier to measure than a rounded or pointed top of a digitally imaged plate. As such, the defaults for instruments measuring dot area are not in agreement. Tim says that if you have multiple locations, it is more importation to be consistent than precise because you are not going to have inter-instrument agreement. For this reason he encourages use of the same type of device in all facilities.
Plate analyzers don’t measure plate thickness and relief and they can’t tell you if your exposure units are set up or operating properly, or if plates are properly exposed. What they will do is measure dot size and determine if those dots are uniform. If there is less than 10 percent standard deviation of the dot size, the plate is considered to be good. If there is more than 10 percent deviation in dot size on the print, you can work back from plate to mask to file in order to identify where the issue is occurring. Once identified, you can make adjustments to laser power or drum speed, or simply clean the lens. Plate analyzers also identify circularity issues. For instance, good circularity on the plate that does not show up in the print indicates a dirty plate or an ink transfer issue that could result from inadequate drying, unbalanced driers, or inadequate detack.
A durometer gauge measures the hardness of the plate. Durometer readings affect how the material prints: impression, halo, ink release capabilities, the hardness, durability and tackiness of the plate, as well as the affinity of the plate to pick up the ink and its ability to release it. UV-A and UC-C light meters take measurements to ensure proper crosslinking of monomers, elimination of tackiness, and to compensate for declining bulb efficiency over time.
UV-A meters ensure proper operation of UV-A lamps for optimum crosslinking of monomers so plates hold up to long press runs. Reduced output can be compensated for with added exposure time. UV-C meters verify the performance of UV-C lamps to ensure they properly remove tackiness.
Armed with readings from each of these measurement instruments, the operator is no longer shooting in the dark. Readings provide clues to the source of problems. Adjustments made on a timely basis reduce make-ready waste, defective finished product and unnecessary premature replacement of plates.
Seeing print from the CPC’s perspective
To give a point of reference for what is important today, Allen Marquardt from Kimberly Clark Corp. put it into a historical perspective. Thinking back just 10 years, virtually everything was analog with either a round AM or FM dot. Presses were running fast if they get up to around 900 fpm (30m/min). 6-8 hours was pretty routine for a changeover. 133 line screens were cutting edge and 'light – standard – dark' press approvals were common.
Just 10 short years later, digital is everywhere. Dots have taken on many new shapes with plate screens often exceeding 175/in. Presses can exceed 3,000 fpm (100m/min) although they rarely approach those speeds in production.
Oh, and one other little detail: the spectrophotometer has replaced the human eye for critical color control. It is amazing how far we have come in such a short time. Gone are the days of eyeballing the color, as the human eye is an inaccurate judge of color. The press-side 'Dixie cup magic' has been replaced with agreed-upon color specs verified by a color measurement device.
Even the mechanical systems have improved dramatically. With cartridge style press stations, rail systems and cantilevered sleeve mounting systems, it is now possible to be setting up the next job while the current one is still running. Robotics reduce setup time and allow for a safer, faster and quieter pressroom. Automated color control is being combined with vision systems to ensure proper impression and registration and identify defects on the fly. We have even gotten to the point where reactive spectrophotometers are stationed on-press and linked to auto-feedback and adjustment mechanisms. All of these help reduce setup times from hours to minutes, while improving consistency and driving out waste.
But while we are enamored with all this technology, Allen is quick to point out that we cannot overlook the fundamentals. While presses may be to the point that they almost run themselves, there still exists a critical need for a highly skilled, well trained workforce. To avoid what he sees as degradation of print on the shelf, we have to stave off the erosion of technical understanding in our organizations. Training is crucial, especially when the top press operators are promoted up the ladder. As operators are replaced, there is all too often an erosion of technical understanding in the ‘backfill of talent’. New operators don’t understand how to troubleshoot graphics and that lack of understanding shows up in the print.
Allen said he would rather work with a company that has well trained talent, even if their equipment is thirty years older than someone with state-of-the-art equipment whose operators don’t understand the process or know how to troubleshoot graphic issues. When you are ‘pushing the limits of physics’, which everyone seems to be doing these days, you can’t afford to have the operators’ understanding limited to where the start button is located. If the goal is to get more ink down faster with better placement control, getting it to dry without plugging up plates or anilox, using front and back print on multiple layers with built-in security features and so on, the way to achieve that goal is through training.
If the goal is simply to put down the correct amount of ink predictably and repeatedly, you need to ‘run by the numbers’. Allen strongly advocates implementation and adherence to the Flexographic Technical Association’s FIRST (Flexographic Image Reproduction Standards and Tolerances) program as a means to faster setups, reduced waste and greater consistency.
Speaking as the voice of the customer, Allen says he is not impressed when print shops rush to ‘look busy’, making adjustments on press when he walks in. He is impressed when he asks the operator specifics about press settings and spectro readings and the operator knows the answers. He would rather see the press running in control with a knowledgeable staff sweeping the floors to keep busy. It is simple. If you ever needed a perspective on what’s important to your customers, Allen nailed it in thirteen words: ‘I come in with a signed proof. You match it. I buy it’.
A perspective on sustainability
While waste reduction was an integral component of Allen and Tim’s presentations, sustainability involves more than reducing waste. It also involves doing something productive with the waste that is generated. By finding new uses for waste materials, they are diverted from landfills and become a renewable source of raw materials. And the trend today is for brand owners to place more and more pressure for sustainability on every part of the supply chain.
Rolando Sanz-Guerrero of Greenwood Fuels discussed generating power from the waste byproducts of the printing industry. When coated and laminated papers and films, as well as matrix waste, are formed into fuel pellets, these have adequate density to produce power comparable to that achieved from burning coal. The pellets comply with stringent air quality regulations, burn cleaner than coal and require no major retrofit to burn in coal-fired equipment.
Calvin Frost, CEO of Channeled Resources, said his plant in Marathon County generates nearly 1,000 tons per month of ‘byproduct’ (fuel pellets) and the company is 98.5 percent landfill free.
Dave Robinson, also of the Channeled Resources Group, says matrix waste is a major component in fuel pellet production as the adhesive materials help bind the pellets together while the paper products produce good amounts of heat energy. Other materials include pressure sensitive paper, poly-coated paper, polypropylene, polyethylene and polyester films, packaging materials and non-woven products, as well as waste paper, carbon paper, tapes and other materials. Materials typically come in compacted or bailed. All materials are tested for qualification purposes looking at btus, metals and sulfur content and elimination of materials that would give off chlorine.
The primary suppliers for the pellet raw materials are label and flexible packaging producers. Dave said the printers do pay a dumping fee similar to what they would pay at a landfill, but they are diverting material from the landfill and generating a renewable energy source. He said the cost for transporting the material to Greenwood Fuels depends on the distance it needs to be hauled. For those companies near a Greenwood facility, recycling is either cost-neutral or slightly cheaper than disposal. He said, though, that for printers/converters that use this approach, the benefit comes as a differentiator and selling point in their being able to state in the context of a sales presentation, that their company diverted (for example) 100,000 pounds of waste material from the landfill to renewable energy in a given month. This is a great alternative for people that are already paying to get rid of these materials, but with an unsustainable approach. As landfill costs continue to rise, and pressure for sustainability continues to grow, clean fuel will become an even better choice.
As Chairman of the FTA Great Lakes Group, it is a pleasure to put these meetings together. I would like to personally thank our speakers. Each meeting, we are privileged to hear from some of the top experts in the flexographic industry. I would also like to thank our hosts, in this case Fox Valley Technical College, for providing such fine facilities for our meetings. We greatly appreciate our food sponsor, Actega-WIT, and the door prizes provided by Harper Corporation of America, Flint Group, All Printing Resources, Mekelburg Consulting LLC, D.J. Lanska and Associates LLC, Tesa Tape, MacDermid, and the FTA. Your contributions made for another enjoyable, entertaining and informative holiday event.
This article was published in L&L issue 2 2011
Stay up to date
Subscribe to the free Label News newsletter and receive the latest content every week. We'll never share your email address.