How offset punches above its weight
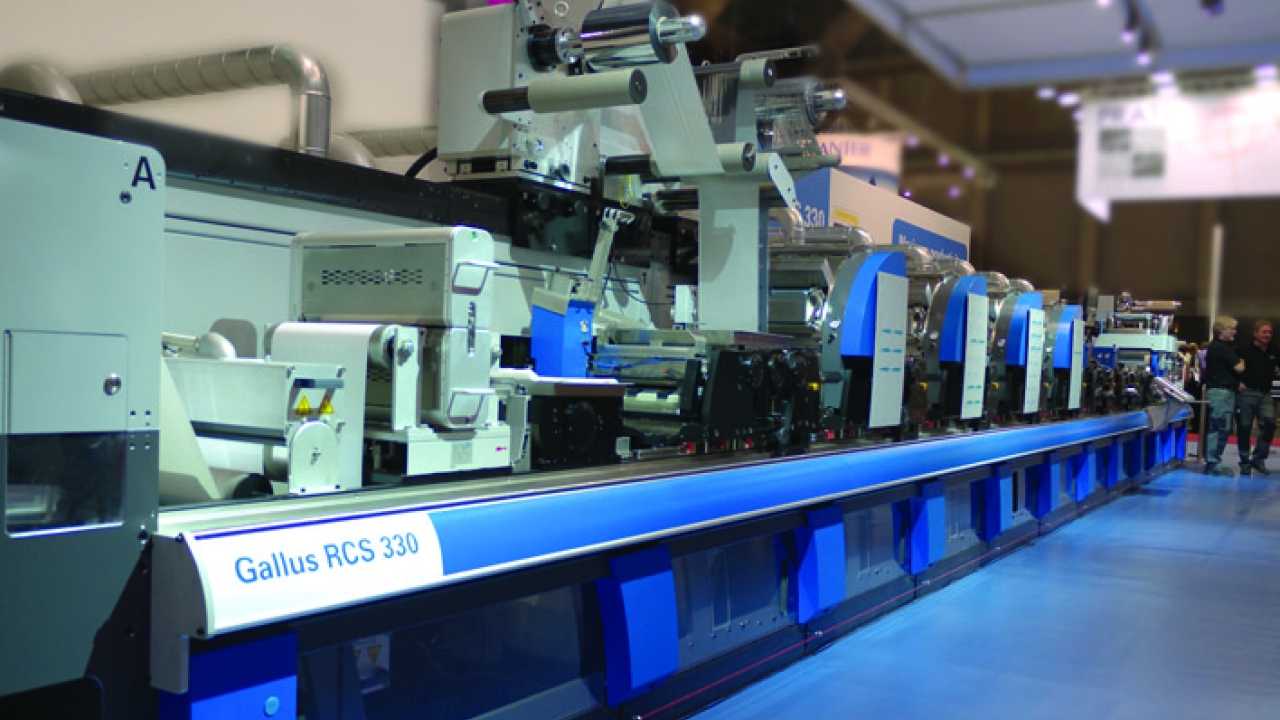
Barry Hunt looks at how recent offset developments meet market demands
Offset's place in a flexo-dominated industry has always been somewhat ambivalent. On one hand it has some firm converts, especially among the larger converting groups, while for most converters it remains a closed book. Nevertheless, activity among some narrow/mid-web press manufacturers has increased, as was evident at Labelexpo Europe. As with other processes, the accent is on achieving fast set-up times and quicker job changeovers to handle larger volumes of short-run jobs. These carefully refined objectives have changed the dynamics for all production processes, due largely to the remorseless influence of the international brand owners and own-brand retailers.
Of course, print quality is a given, along with consistency. Offset has a head start here because it works with proven, globally-recognized quality standards. Operators can quickly achieve accurate color measurements and precise control over ink settings during set-ups and the print run. The reproduction of highlight details allows consistent, pin-sharp halftones with minimal dot gain. This produces good flesh tones and vignettes of the type associated with labels for the cosmetics, toiletries, healthcare, spirits and wine sectors. The best of flexo, or indeed high-end digital printing, can approximate these effects, but offset achieves them more easily and more quickly. Furthermore, as its name suggest, offset printing is an indirect process using precision-made rubber blankets to transfer the image to the substrate. This allows a wide choice of printable substrates, ranging from thin unsupported films to textured or uncoated paper grades.
Similar quality criteria apply to short-to-medium run flexible packaging applications. As is happening with flexo, wider and more versatile presses are opening up opportunities for producing shrink sleeves, sachets, pouches, wraparounds, tube laminates, as well as small folding cartons. Production flexibility is essential, which helps explain the increased interest in offset-based combination/platform presses. So while the process colors are offset printed, typical press lines may include one or more UV flexo and rotary screen units for printing large solids, varnishes and opaque white backgrounds. Other options include gravure units with forced air drying for printing metallic inks, heavy solids and some coatings, as well as hot/cold foiling with embossing, and inkjet for variable data.
Offset units normally have two-cylinder inserts (plate and blanket cylinders), with a fixed impression cylinder, to allow variable size changes without web breaks. Sleeve technology takes this a stage further when changing plates and blankets. The sleeve carriers are easy to handle and store being made from lightweight materials, such as polycarbonates and similar synthetics. Gallus and Nilpeter both use aluminum carriers, which are said to retain their dimensional stability over a machine's service life and are ideal in situations requiring heavy impression pressures. The actual wrap-around offset plates are conventional metal types offering good offset quality with minimal dot gain. Working practices must take into account a non-printing gap, usually of two to three millimeters, which rules out wallpaper-type designs. Blankets sleeves can improve the inking/damping performance even at high press speeds.
Even when sleeve cylinders replace costly conventional cylinder cassettes, offset combination/platform presses still cost about half as much again as comparable UV flexo presses. Offset requires more complex inking trains with several forme rollers to transfer the higher viscosity inks to the blanket and, except with waterless offset, must include alcohol dampening systems to achieve a good ink/water balance. The counter argument is that over the longer-term, as a quality-driven process, offset is more economic and offers good productivity benefits. Industry-standard color management tools allow users to create certain Pantone colors from the process color set. What may require six units on a flexo press is achievable with four on an offset press. Furthermore, automatic controls over the main functions ensure that operators can quickly achieve good quality and maintain it with minimal attention. Importantly, pre-press costs are far lower than with flexo. The plates are not only cheaper, they are durable over long runs and take less time to make using in-house computer-to-plate systems. Benefits like these appeal to printers of wet-glue and in-mold labels wishing to augment their sheet-fed offset presses with variable size offset presses. Where feasible, this introduces the efficiencies of reel-to-reel or reel-to-sheet printing and converting, backed by existing pre-press facilities.
Technology highlights
Offset combination technology began with Nilpeter, when in 1994 it introduced the 330-mm wide M-3300 with the help of OEM suppliers. Despite initial skepticism, the company has since sold hundreds of offset-based presses all over the world. The current fourth-generation MO-4 platform press appeared in 2007. Designed for short-to-long runs, it uses aluminum-based sleeve technology and has a web width of 406mm. At Labelexpo, Nilpeter introduced the Press Management Center (PMC). Its three 17-inch touch screens allow operators to control UV-curing rates, electronic registration and remote inking. Other features include error diagnostics backed by an online service function, job management data and online customer information. The PMC's functions are compatible with the international CIP3 operating standard.
MPS's new EXL 410 Sleeve-Offset combination press has roots in the EO (Effective Offset) series, also from 2007. The patented, bearer-less sleeves for the plate and blanket cylinders give variable repeat sizes of 18-25 inches. An overhead rail allows the free positioning of a compact flexo unit. Short runs are facilitated by MPS's Automatic Print Control (APC) system. It covers the inter-related settings governing forme rollers, plate sleeve, blanket sleeve and impression cylinder, including print gap control, for storage and retrieval from the job memory function. The EXL-Packaging is a UV flexo version with webs up to 660mm wide and a top print speed of 300 m/min.
As an OEM supplier, Goebel manufactures the ink/water system for the EXL 410. The Darmstadt-based group also has links with DG press ServiceS (sic), which in 2009 emerged from the wreckage of Drent-Goebel as a spares and service provider. Drent-Goebel's Vision series of web-offset presses featured the VSOP (Variable Sleeve Offset Printing) system, developed by rotec Hülsensysteme (now with the Flint Group). DG press ServiceS recently launched the Vi-SOP, based on the 520-mm wide Vision, with interchangeable plate and blanket sleeve cylinders. The servo-driven impression cylinders are separately driven from the plate and blanket cylinders, while the web tension system is arranged in such a way to print thin aluminum foils in perfect register, as well as unsupported films and carton board, in relatively small print runs. Vi-SOP is available as an upgrade package for existing Vision presses to allow flexible packaging applications.
DG's renewed VSOP connection followed the ending of an agreement in September with Muller Martini. It acquired the VSOP patents after Drent-Goebel's demise to incorporate the plate and blanket sleeves in its VSOP-badged presses. They come in widths of 520mm and 850mm and run at up to 365 m/min and were developed from the Alpina 52V and 74V offset/flexo combination presses for labels and packaging. (At Labelexpo the company promoted the use of electron-beam curing to produce safe foodstuff packaging printed with low-odor and low-migration EB inks.)
The Gallus RCS 330/430 modular platform presses can support up to eight offset units and a further four from a choice of flexo, rotary screen, UV gravure or hot foil processes. The servo-driven units are freely interchangeable without the need to separate the web. The offset units use Heidelberg's Alcolor dampening system, originally developed for sheet-fed presses, coupled with an automated start-up method with a low idling speed to reduce material waste. The company's Flying Imprint feature allows the changing of flexo-printed text and logos without stopping the press.
Gidue's Xpannd M7 platform press comes in widths from 370mm to 630mm. It allows quick changes between Gidue's existing Xpannd offset towers and its 'Flower' flexo print units. The platform supports rotary screen, gravure, hot foiling, embossing and die cutting, allowing different configurations for day-to-day needs. New features include the Offset Cube, a compact unit with easy accessibility to remove and store in front of the press on the Organizer. The unit uses the Xpannd inking system, integrated with the new camera-based Digital Offset technology for automated control over inking and register. Also new is the Mini-Cassette, said to offer comparable costs to offset print sleeves, and also removable for storage on the free-standing Organizer.
Omet has developed a quick-change offset unit for integration within the X-Flex X6. Variations can also integrate with the gearless VaryFlex F1 340, 430 and 520 platforms, along with a choice of gravure, screen, cold and hot-foil, as well as UV flexo. An independent drive allows very slow set-up speeds to minimize waste, which is essential when processing unsupported films.
Rotatek's press range includes the 520-mm wide Universal. The multi-substrate offset press is targeted at flexible packaging printers. It uses quick-change sleeve technology for the offset and flexo units. The sleeve carriers are fitted with ring bearers to allow high printing pressures.
Stop-go, stop-go
Semi-rotary UV offset presses – also letterpress – obtain variable repeat lengths through their intermittent, or translative, web movements. Top speeds are only 70m/min or less, but fast set-ups and job changeovers make them economical for handling short-to-medium label runs with minimum wastage. Aided by localized distribution patterns, this helps explain why many family-owned label printers in Asian and Pacific Rim countries remain big users of such presses. Asian manufacturers also tend to supply rotary and flatbed screen, hot foiling and rotary and flatbed die cutters as part of package deals.
Outside of Asia, the main users tend to be converters serving the wine, healthcare and cosmetics sectors. Some companies are known to install these presses as economic alternatives to high-end digital label presses, especially since they offer the flexibility of combination printing and come complete with in-line finishing. A maximum width of 330mm is the norm. The fact that there are no format-dependent accessories to slow down job changeovers is a further bonus.
Major Japanese manufacturers include Miyakoshi, once widely known for its continuous forms presses. It manufactures the MLP Series in three widths for label printing. The modular presses typically run with five UV semi-rotary offset units, a UV flexo unit, hot foiling with embossing, and two die cutters. Shiki Machine Supply Corporation supplies the FX Series in web widths of 270mm and 400mm, usually with six offset units. The servo-driven Sanki SOF-330 from the Lintec Corporation is similarly configured, with optional flat-bed die cutting and hot foiling in a stand-alone unit with re-registration. The rollers keep revolving during stoppages to avoid roller marks on start-up, while a single blanket is used for all repeats to reduce downtime. Iwasaki's highly automated, servo-driven TR 2 press includes a roll lift on the unwind, vacuum loop box to avoid scratches behind the label web, pre-set temperature control for the recirculating water system, and video web monitor to check registration and any faults. Options include rotary die cutter, flexo varnish unit, and reverse-side printer.
Taiwan is another major center for such presses. The RS-350PS from Labelmen International combines full rotary and semi-rotary printing. It features the CNC One Touch make-ready system, the Ani-Print inking system for consistent inking with fast set-ups and fine tuning of the ink/water balance. Orthotec's upgraded CFT 3536 press includes a chilled water circulation system as part of the four-segment, servo-controlled inking system to maintain consistent ink viscosity. Register is adjusted through a touch screen register and the blanket cylinder is now engaged/disengaged automatically. The press also incorporates a second pass scanner/dampening system, as well as a plate dirt removal function. Smooth Machinery offers the shaftless SPM 450-OR with multiple servo drives for the main functions.
Several Chinese manufacturers of flexo presses and finishing equipment now offer intermittent offset presses. They include Zhejiang Weigang which recently introduced the six-unit ZX-320. Zhongtian Machinery Works' ZTJ-330 has individual servo drives on each print unit. Three-way adjustment of the print cylinder for on-the-fly register adjustments, a sliding touch screen control unit, and high levels of automation point to a fairly sophisticated specification.
A long-standing European example is the TCS 250 from Gallus. Its modular design, with expansion up to 12 units, allows a choice of printing and finishing options, including Gallus's Rotascreen system. The 265-mm wide press carries a high level of automation, with touch-screen control from a central panel. Users can combine the flatbed die cutter with a flatbed relief embossing unit.
Rotatek targets the semi-rotary market with the Brava S 330, a shaftless combination press employing semi-rotary offset, flexo and screen units. It was derived from the wider Brava 420, which unusually combines both rotary and semi-rotary offset modes. New features include an embossing system with gap master regulation and an inline screen printing unit.
Codimag is unique among European narrow web manufacturers in offering waterless offset, which eliminates the conventional water or dampening system. Based on Toray's platemaking technology, the system uses silicone-coated plates and highly viscous inks with an integrated temperature control system. Four years ago Codimag developed Aniflo, a keyless anilox offset technology, for the Viva 420. Aniflo replaces the conventional inking train with four cylinders of equal diameters. An anilox roller delivers a constant ink film to a forme rubber roller, which transfers ink to the plate, with silicone layers for non-image areas, and then to the blanket. Esko color management software gives an extended gamut printing. At Labelexpo it launched a new version of the Viva 340, also fitted with Aniflo, again aimed at printers of short-run premium labels.
Notwithstanding its dominance of commercial printing, UV-cured offset is now firmly rooted within certain levels of labels and packaging production. Rotary offset is no longer confined solely to long-run applications. Its many quality and production-led benefits allow it to compete with UV flexo at the top, value-added end of the market. Several developments from leading press manufacturers bear this out. As mentioned, the strength of semi-rotary is largely determined by regional market demands and global trading patterns, while simultaneously carving out niche, high-end applications all over the world. Both formats, it could be assumed, punch above their weight.
Pictured: The Gallus RCS330
This article was published in L&L issue 6, 2011
Stay up to date
Subscribe to the free Label News newsletter and receive the latest content every week. We'll never share your email address.