Kuresa opens new factory
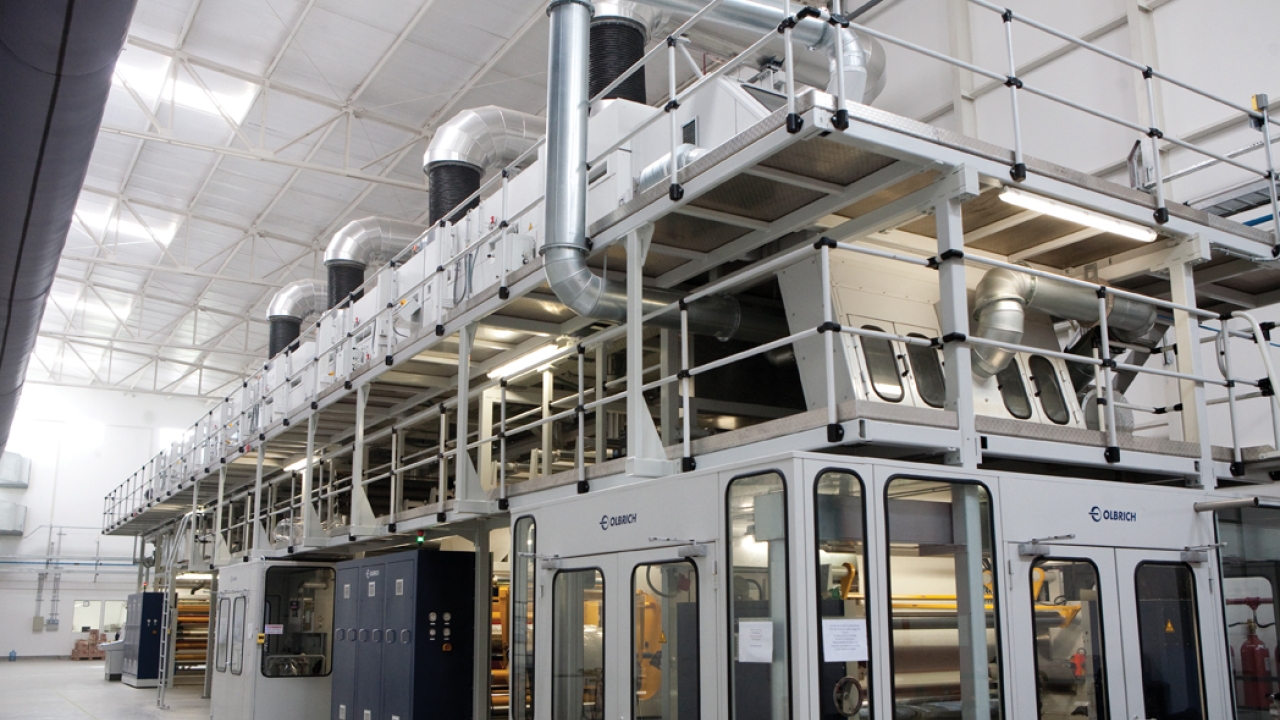
Peruvian label and adhesive tape converter Kuresa inaugurated its new 23,000 sqm site in November. James Quirk reports from Lima
Kuresa welcomed 377 visitors – including representatives from the Peruvian government – to the inauguration of its new facility in Lima in late November 2011. The event marked the completion of a three-year project into which the company has invested some $25 million dollars.
Among the guests at the ribbon-cutting ceremony were Salomón Lerner Ghitis, Prime Minister of Peru, Dr Kurt Burneo Farfán, minister for production, and Dr Daniel Blansjaar, Kuresa’s chairman. Seventeen countries were represented among the attendees, including Argentina, Italy, Canada, Chile, Colombia, Germany, Japan, Mexico, Venezuela and the US.
The 23,000 square meter site, which was purchased in 2007, is located in Centro Poblado Santa María de Huachipa, in the district of Lurigancho in Lima, the Peruvian capital. Construction began in May 2010 and was completed in around 12 months.
The $25 million dollar investment covered the purchase of the land, construction of the facilities, investment in new machinery for adhesive tape and prime label production, new warehousing and offices, as well as safety precautions and other infrastructure. The company claims the plant is now the best of its type in the Andean region of South America.
The new facility houses a new adhesive coating machine from German manufacturer Olbrich – the company’s largest ever single investment at USD 9.5 million – which will benefit both Kuresa’s label printing and adhesive tape divisions. A fourth Ilma letterpress machine, for production of prime labels with which Kuresa serves the cosmetics, personal care, food and beverage markets, is another new addition. Prime label production capacity is estimated at 5 million sqm per year.
The move to the new plant will generate 100 new jobs, taking the total number of employees to 350.
Swiss precision
In his speech to mark the inauguration of the new facility, Jaime Yoshiyama, Kuresa’s managing director, thanked the attendees for their presence, outlined the company’s history and paid tribute to his employees.
He told how the company was founded 46 years ago with a small coating machine for adhesive tapes, which was nicknamed ‘the bicycle’ because of the simplicity of its technology. Over the years, the company grew its Pegafan tape brand into one of the biggest in the country, beginning to invest in modern equipment in the late 1970s.
At the beginning of the following decade, a shift in government policy towards importation saw the arrival of foreign tape brands in the local market. This, said Yoshiyama, encouraged the company to rethink its strategy and sow the seeds for the growth that would eventually see Kuresa arrive at its new facility.
The company began to search for a technology supplier, modernized its production facilities and invested in the training of its workforce. ‘This is how technology was acquired from Swiss company Cellux, whose president is here with us, and who is now president of Kuresa,’ explained Yoshiyama.
‘When Dr Blansjaar and his engineers arrived at Kuresa in the 1980s, the performance of our machinery and the quality of our products began to improve enormously. Because of our lack of technical knowledge at the time, the existing machinery has not been used efficiently. The addition of Swiss precision to the enormous practical talent of the technicians and mechanics from Peru quickly gave Kuresa a strong competitive position.
‘Kuresa’s workers played a key role in this transition. It was not so difficult for them to master the new techniques, and furthermore served to illustrate the innate capacity that Peruvian workers have to adapt foreign sophisticated technical concepts to the materials and instruments of Kuresa.
‘Since then, more than 30 years have passed. Kuresa, in the meantime, has expanded its product range. Since the late 1990s we are engaged in self-adhesive label production and are printing labels of the highest quality – we can say without any doubt that the quality of our products has nothing to envy of any label produced in Europe. Our clients in this market are multinational companies with international operations.
‘When you visit places like Colombia or Ecuador, or the Central American countries, and you enter a supermarket, you will see that many of the products of household care, personal care, beverages and food carry labels printed by Kuresa, on sophisticated narrow web machines using diverse printing techniques.’
Dr Daniel Blansjaar – a Dutchman who has lived for many years in Switzerland – spoke of his conviction in Peru’s ‘enormous potential’ and described how he had made some 50 visits to the country over the years. He spoke of the ‘exemplary relationship’ between Cellux and Kuresa, with technicians from the Peruvian company travelling to Switzerland every year for training.
Salomón Lerner Ghitis, Peru’s prime minister, said: ‘I am very happy to see such investment in Peru.’ He spoke of having known the Yoshiyama family for many years and even worked alongside the company in its early days. ‘It is a great honor to say that Kuresa now has the facility that it deserves and is a role model for label and tape manufacturing.’
Solvent recovery
The Olbrich adhesive coating machine, which runs at 150m/min with a 1,600mm web width, brings Kuresa’s annual production capacity to 80 million square meters of adhesive tapes. At 40 meters in length and 7m high, it runs at ten times the speed of the Kuresa’s previous coater, and will also allow the company to produce its own specialty self-adhesive label material. A thermal oxidizer prevents solvents from being released into the atmosphere.
The tape manufacturing facility counts on a dedicated area for slitting and packing the different types of adhesive tapes produced by Kuresa – which include office, packaging, masking and specialty tape products. The prime label printing facility includes a dedicated pre-press department, label printing press shop, laboratory for quality control and separate warehousing.
Label production is carried out on four letterpress machines from Ilma. Each of the presses has flexo, silkscreen, reverse printing and hot and cold stamping capabilities, and can print variable data for promotional applications. They are equipped with inspection systems from BST, web cleaning equipment from Teknek and Kelva, corona treatment and lamination. Proofing and mounting equipment comes from JM Heaford, while finishing is handled by Rotoflex machines.
Kuresa is in the process of being certified to ISO 9000 and its products pass through exhaustive quality control and adhere to global quality standards. Yoshiyama was keen to emphasize the environmental credential of the new facility. ‘A particular aspect of the production process which we want to highlight is that the factory minimizes its impact on the natural environment,’ he said. ‘In the fabrication of adhesives, benzine solvents are used. In a traditional plant, when a tape is coated, the solvent is released into the atmosphere and contaminates the air. In our case, this solvent is recaptured and reused, avoiding contamination, and also permitting a substantial saving in costs.’
Kuresa, as well as being the leader in its local market, exports its products to Chile, Bolivia, Ecuador, Colombia, Venezuela, Central America, Mexico, Holland, the UK and the USA.
During 2011, the company experienced growth of 18 percent compared to the previous year, mainly due to increasing sales in foreign markets. Some 75 percent of Kuresa’s sales come from products manufactured in-house, while the remaining 25 percent come from imported products, such as the Japanese brand of office supplies, Pilot, which are imported from Japan and sold in Peru.
According to Yoshiyama, the new site allows six times the production levels of the previous factory.
Pictured: The adheshive coating machine from German manufacturer Olbrich
This article was published in L&L issue 1, 2012
Stay up to date
Subscribe to the free Label News newsletter and receive the latest content every week. We'll never share your email address.