Managing colors by numbers
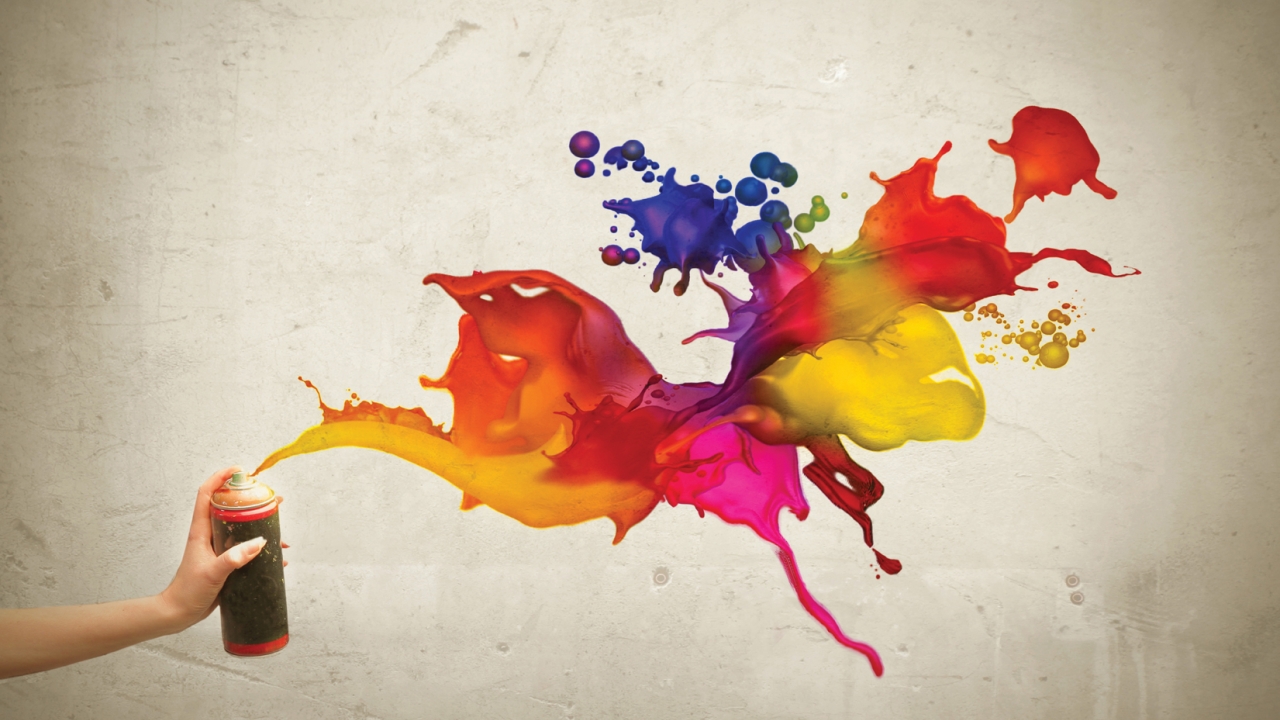
Barry Hunt reports on how spectral analysis and new software tools are radically changing color management for labels and packaging
Color is a complicated and confusing subject. It combines the precision of accurately measuring wavelengths and other spectral data, with the more ambiguous psychology of how humans perceive, feel and respond to color. Of course, when related to packaging and how we recognize branded goods, accuracy and consistency are crucial to printing a brand's spot colors to accepted standards. This form of color management is seeing some notable advances, centered largely on spectral analysis and, in the pressroom, is often allied to the phenomenon of expanded gamut printing in reproducing spot colors. One interesting development is the growing involvement of many major brand owners in the subject.
As David Harris, Esko's UK-based product manager for color and proofing, explains: ‘Packaging has many stakeholders so our challenge is to turn some fairly complex scientific knowledge into an easy-to-use system for everyone in the supply chain to use. There is a growing realization that to be more efficient – that is drive down costs, reduce waste, and gain more speed to market – it is necessary to have in place effective process control and process improvements. These are of course integral to other manufacturing industries, which in the case of color means process control with spectral colorimetry.
‘Spectral data allows brand owners to define their colors,’ he adds. ‘There is an “ideal” brand color reference (which probably never changes) and then there are achievable references based on real print on real substrates. We call them dependent standards. They may evolve over time, for example when new substrates are introduced.’
As we know, artwork studios and prepress departments depend heavily on special software tools and monitoring devices to calibrate the individual color profiles, or gamut, of their display screens, scanners, and proofing printers. Proofing itself reflects the limitations of the human eye in defining colors. It is better at matching two or more colors when placed side by side, whether buying paint or matching furnishings. In print production an able-sighted person can usually detect quite small differences in the hue, brightness and saturation of a specific color, whether derived from a CMYK process set, or a Pantone spot color, when comparing run-of-press output with an approved contract color proof, preferably under standardized illumination conforming to a specific ISO standard.
Scanning and hand-held densitometers are ubiquitous, simple-to-use devices when it comes to measuring color densities. Setting a target density value for any combination of printing ink and substrate is essential in package printing, unfortunately density values do not allow us to uniquely define a color. A far more objective method is to use spectral analysis to measure the relative intensity of either transmitted or reflected light as part of the visible spectrum using a spectrophotometer. Typical models take up to 31 measurements in 10 nanometer increments in a range from around 380 to 740nm. This process renders colors into standardized numerical values to allow us to accurately measure and maintain the absolute value of a particular color within a proscribed gamut, or range.
As widely known, CIE L*a*b* values based on the ISO 12647 standard are a key component in obtaining a so-called colormetric view of what a color will look like. They basically define the color space measurements for a particular output device. Here, L* represents luminance, or lightness, while a* and b* are respectively the red/blue and yellow/blue axis of the chromaticity depictions. CIE Lab also includes Delta E color values as a standard to show calculated deviations of an image's highlights and shadows.
Up in the clouds
The recent arrival of cloud-based technology in respect of brand color management is an interesting development. The most notable example is PantoneLive from X-Rite Pantone. Esko has adopted this subscription-based service as a component of its Suite 12 update, with Color Engine 12 providing an integrated method of accurate color management across the packaging and supply chain. Esko's latest ink model defines color from the PantoneLive cloud. Using spectral analysis, the technology produces an inkjet proof that simulates the printing of spot colors on the press. X-Rite Pantone software tools prepare a job's ink formulations and establish on-press quality control parameters. The workflow also allows printers to integrate the Color Engine with online 100 percent web inspections systems. X-Rite's CxF (Color Exchange Format) holds all the associated color metadata, based on spectral data, for sharing within the supply chain.
PantoneLive is said to eliminate the need to fingerprint possible press combinations to achieve accurate color expectations right from the beginning of the process. Users therefore obtain a ‘color by numbers’ reference for every available Pantone color – and overprint combination – applicable for widely-used paper or film substrates printed by different print processes. In a related move, X-Rite Pantone introduced the hand-held i1Pro 2 spectrophotometer. Bundled with the new i1Profiler software v1.3, it comprises four different upgradable products. The pressroom version has touch-and-swipe operation allowing press operators to take quick and easy color measurements based on ISO standards. The i1Pro 2 platforms include the X-Rite Graphic Arts Standard (XRGA) for digital printers. It also allows them to adhere to ISO standards in achieving reliable and repeatable CMYK and spot colors.
X-Rite Pantone sees brand owners as potential users of PantoneLive. As described in Issue 2, pp 49-51, the UK-based subsidiary of H J Heinz was an early adopter. Using digital inkjet proofing it allows the company to assess the characteristics of different substrates, print processes, inks and light viewing conditions, and confidently predict how a Pantone spot color will interact and overprint on the press. As an 'open system' within the color workflow, PantoneLive supports plug-ins that allow brand owners and their designers to use programs like Adobe Creative Suite or Adobe Illustrator to manage their color branding via a database and distribute them to all their partners in the supply chain.
GMG offers a modular cloud-based color management service named CoZone.Collaborate. It is aimed at both large and small companies within the entire packaging/label supply chain. For example, users can track project status and efficiently manage the production processes. Currently its supports the approval of PDF or image documents, followed later by support for multimedia and web file formats.
It already supports OpenColor, a new spot color proofing tool for labels and packaging that analyzes each ink color and substrate, and applies them to a specific printing process. The tool adds process-specific information, such as ink rotation and trapping. Adding additional overprint readings increases accuracy. OpenColor supports up to 15 colors and is compatible with Esko's Equinox expanded gamut technology, which like similar hexachrome systems use ICC profiles to calculate Delta E color matches. GMG says that while multicolor printing can reduce the number of press units required for spot colors, an ability to accurately simulate spot color overprints remains a major challenge for label printers.
ColorCert from Nelison Consulting includes ColorCert Master. It uses editing modules to create the initial color and quality requirements, including profiles for inks, spot colors and on-press dot gain adjustments. Pressroom Tools also includes a separate module to control report generation and MIS links. Proofing Tools handles certification in respect to proofer checks and sharing color standards with designers and artwork suppliers.
After generating standardised 'scorecards' users can upload them to a SQL database for retrieval at a web front-end, as a printable file for a corporate FTP server, or as an email attachment. ColorCert's network allows input from brand owners, designers, and artwork suppliers to meet color library requirements, define and maintain quality standards, and create jobs using one or more package printers. They in turn work to the certification standard with job reporting, such as roll or pallets reports, which are included in the Pressroom Tools module.
MeasureColor uses servers to obtain color standards that govern references, spot colors, job reporting and color tolerances. Networks support customized color libraries, proofing certification, MIS/JDF order administration, as well as production standards based on external spectrophotometry. The latest MeasureColor Series 3 Packaging suite for multiple or single users covers digital and conventional printing. The ChromaPlus option allows users to not only analyse a color's spectral behaviour, but also to correct a specific color. It links closely with the company's Printability Test function to obtain an exact color correction for any substrate and ink combination. This includes the precise dry-back values of wet printing inks.
New software options from Cambridge, UK-based FFEI provide comprehensive tools for labeling and packaging print service providers. Its RealPro workflow system includes RealVue 3D Packager for creating visual prototypes of folding cartons. FFEI recently appointed CGS Publishing Technologies International as a global distributor. The company's ORIS color management system – used widely among North American printers – includes Press Matcher for producing accurate, consistent color on digital presses including wide-format printer/cutters.
Inspection with spectral analysis
Spectrophotometric analysis based on CIE L*a*b* values is now an option for 100 percent inline web inspection systems for critical printing operations, including pharmaceutical packaging. Modules that can accurately monitor and report spectral data - originated in studios and prepress departments - greatly enhance converters' real-time quality control operations. Data analysis can take place at multiple locations, both in the running direction or across the web, for early detection of color variations without stopping the press. Depending on the system, operators can take measurements from either sides of a transparent web.
Advanced Vision Technology offers SpectraLab as an add-on spectrophotometer for its Helios II series of inspection systems. It measures and reports absolute color and density values to aid the matching of brand owners' colors at press speeds using selected sampling points from five mm x five mm upwards. (At Labelexpo AVT was presented with the Label Industry Award for New Innovation for 2012 for SpectraLab.)
Amir Deckel, VP of corporate marketing, says attitudes among brand owners have prompted growing interest in spectral color control and that AVT has made several presentations to QA and print technology teams: ‘They are enthusiastic about color management and some now request that their printers make frequent and reportable absolute color measurements. Although they are not willing to pay more for the product, they still demand it. Printers face a tough choice. Should they invest in this technology and enjoy the continued business or let competitors get the business?’
He adds that this pressure to ensure color consistency essentially favors inline operations: ‘Gone are the days when brand owners settled for color measurements at the beginning and end of a roll. They require much more frequent color measurement and that entails, obviously, much closer control of the color by press operators.
BST International developed the modular QCenter.Spectral in partnership with X-Rite Pantone. Aimed at flexo, gravure and narrow web label and packaging printers, it is described as a new approach to press color control that simplifies quality control workflows during production runs. Operators can use both inline spectral measurements and offline hand-held spectrophotometers to deliver comparable results. Operators can integrate multiple cameras, image analysis functions and additional lighting from a central user interface. QCenter automatically chooses the appropriate hardware and software tools depending upon what part of the web the operator needs to examine, and what level of detail. A large high-definition touch-screen monitor allows control over zooming, selecting fields of view, viewing the web width and other quality control tasks.
Color targets
X-Rite-Pantone also works with QuadTech, a developer of on-press color control systems mainly for commercial, newspaper and wide-web packaging printers. In partnership with ColorConsulting in Italy, it has introduced a system that uses customer-defined color targets, as supplied from a standard Pantone color library, an X-Rite CxF file, or basic color samples. An X-Rite SpectroEye device manually evaluates these targets offline to obtain a spectral color curve for uploading into X-Rite's InkFormulation software. A color database from the Huber Group provides quality-checked data to a machine's ink dosing device for preparing the ink for the press.
Operators load the color targets into QuadTech's Color Measurement System using its SpectralCam web inspection module to measure printed color data from either paper or unsupported films at full press speeds. The color target data is obtained simultaneously with live color measurements taken at full press speeds. Any color deviations are automatically captured and reported in ∆E values. A new color CxF file can be sent back to the InkFormulation software.
While several 'big press' technologies have filtered down to narrow/mid-web presses, John Cusack, product manager, says in this case market demand rather than technical limitations is the main issue: ‘We can go down to 180mm field of view (FOV) per camera. While 180mm is the smallest FOV we support, optics to allow for narrower FOVs are possible. However, there has been no such need so far. It really comes down to required system resolution. QuadTech’s inspection systems cater for the widest packaging web widths. We use a proprietary extruded light design which we are currently supplying in lengths up to 3 meters. We can custom design longer lengths if needed. So, the return on investment and/or performance requirements tend to determine FOV rather than the technological barriers.’
This possibly applies to a wider use for QuadTech's Accucam system which eliminates the need for color bars. Using prepress image files to create L*a*b* target values, a proprietary six-channel spectral sensor measures the printed web and calculates the color values of the entire image. The system brings the printed image to the specified target values and automatically maintains the color quality throughout the production run.
The widening ubiquity of color management services now includes the specialist repro and platemaking houses serving the packaging industry. Some offer design services for brand owners, while promoting HD flexo platemaking and expanded gamut printing. These extended ink sets are proving a practical way of reducing the number of flexo units when printing spot colors. As an example, the UK firm of Creation Reprographics uses Esko's Equinox expanded gamut software for this purpose, but uniquely combines it with Asahi's new AWP water-washable flexo plate technology. It claims to achieve gravure-like quality with CMYK flexo plates.
Overall, the potential benefits of using the latest color management tools extend beyond meeting the demands of key accounts – and perhaps keeping them – and go some way toward assimilating the extra expense involved. As a form of accurate process control, such systems should help raise pressroom productivity supported by automated feedback. For example, staff can formulate spot color inks and make dot gain adjustments ahead of press start-ups. Also, removing the trial and error of color matching should noticeably reduce start-up waste and make-readies times, while reducing downtime during production. Systems can also support software plug-ins to generate roll reports and aid on-press troubleshooting. So while color can indeed be complicated and confusing, the logic behind 'managing colors by numbers' to help reduce costs appears
a far simpler proposition.
This article was published in L&L issue 5, 2012
Stay up to date
Subscribe to the free Label News newsletter and receive the latest content every week. We'll never share your email address.