UFlex Chemicals plant adopts Zero Liquid Discharge Technology
UFlex Chemicals production unit in Noida is now a Zero Liquid Discharge (ZLD) facility. ZLD is a strategic waste water management system that ensures that there is no discharge of industrial wastewater into the environment. UFlex Chemicals plant has started saving close to 20 kiloliters of water a day using the technology.
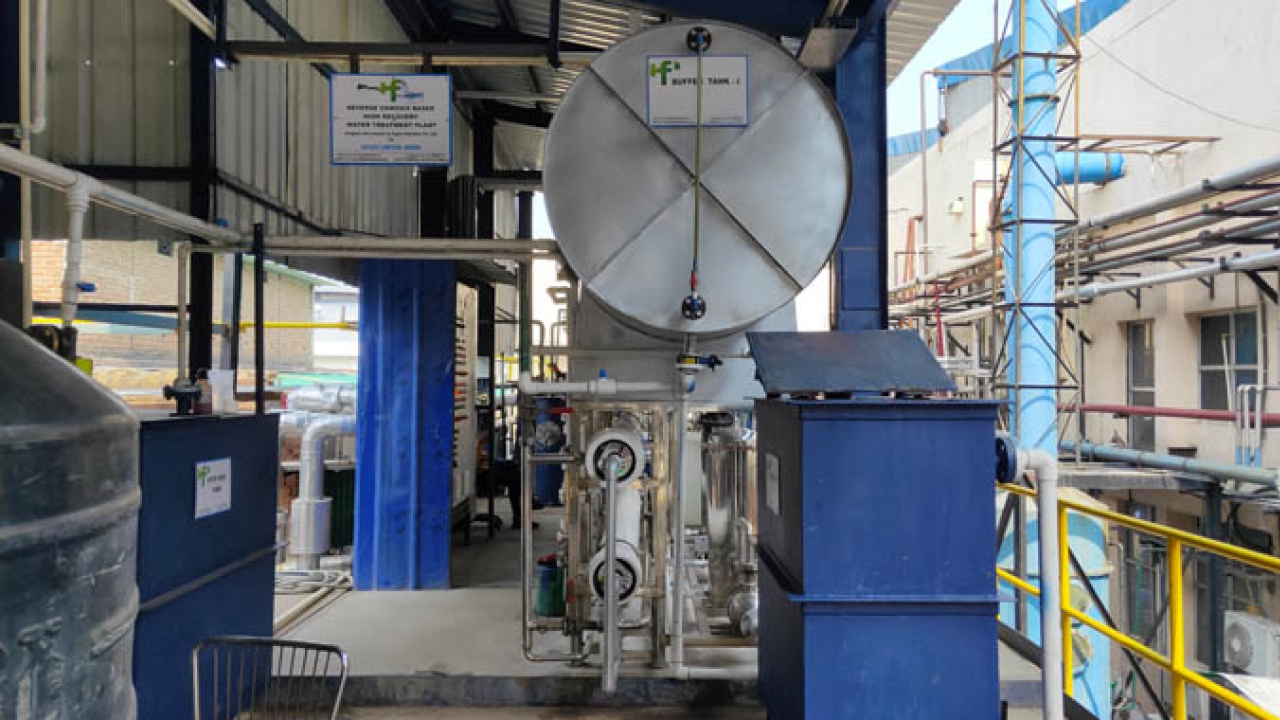
UFlex Chemicals business claims to develop eco-friendly, sustainable and food-safe compliant inks, adhesives, coatings and biodegradable packaging such as primers, barrier, gloss and heat-seal coatings. With the implementation of ZLD technique the plant has ensured that no liquid waste is eliminated apart from bringing down water usage while developing its products
The zero liquid discharge Chemical plant uses a 100 percent supply of effluent treated water of sewage treatment plant (STP) as well as effluent treatment plant (ETP). It is subsequently treated through the combination of technologies such as Membrane Bio-Reactor (MBR), Reverse Osmosis (RO), and Agitated Thin Film Dryer (AFTD). The permeate good quality water which is the final product derived is re-used in boiler feed, cooling tower makeup water and fume hoods without being discharged into the municipal sewer thereby putting the discarded water back to use. The rejected water is converted into solid waste residue via evaporation process which is in turn discarded as hazardous waste (as per the regulatory norms).
Rajesh Bhasin, joint president, Chemicals Business at UFlex commented: ‘At UFlex Chemicals, we are proud to announce that our Noida production has achieved the status of a Zero Liquid Discharge facility. We have adopted this technology to contribute positively to the environment by considerably reusing and recycling waste water in order to save groundwater consumption and is a big move for us in reducing our overall water consumption and ensuring that wastewater does not get discarded into the environment.
‘We are working hard to follow the circular economy model at our facility and systematically implement means that are environmentally conscious so that we can conserve our natural resources for the future. Progressing further, we look forward to implementing the ZLD technology in our other production facilities as well, in order to contribute towards a sustainable future.’
Stay up to date
Subscribe to the free Label News newsletter and receive the latest content every week. We'll never share your email address.