Derschlag installs Bobst Master M6 inline press
The investment in a new Bobst Master M6 Inline press is part of a large expansion at the German company’s site in Bad Berleburg, North Rhine-Westphalia. The nine-color UV flexo machine was chosen in expectation of ongoing growth in demand for flexible packaging and new sustainable materials.
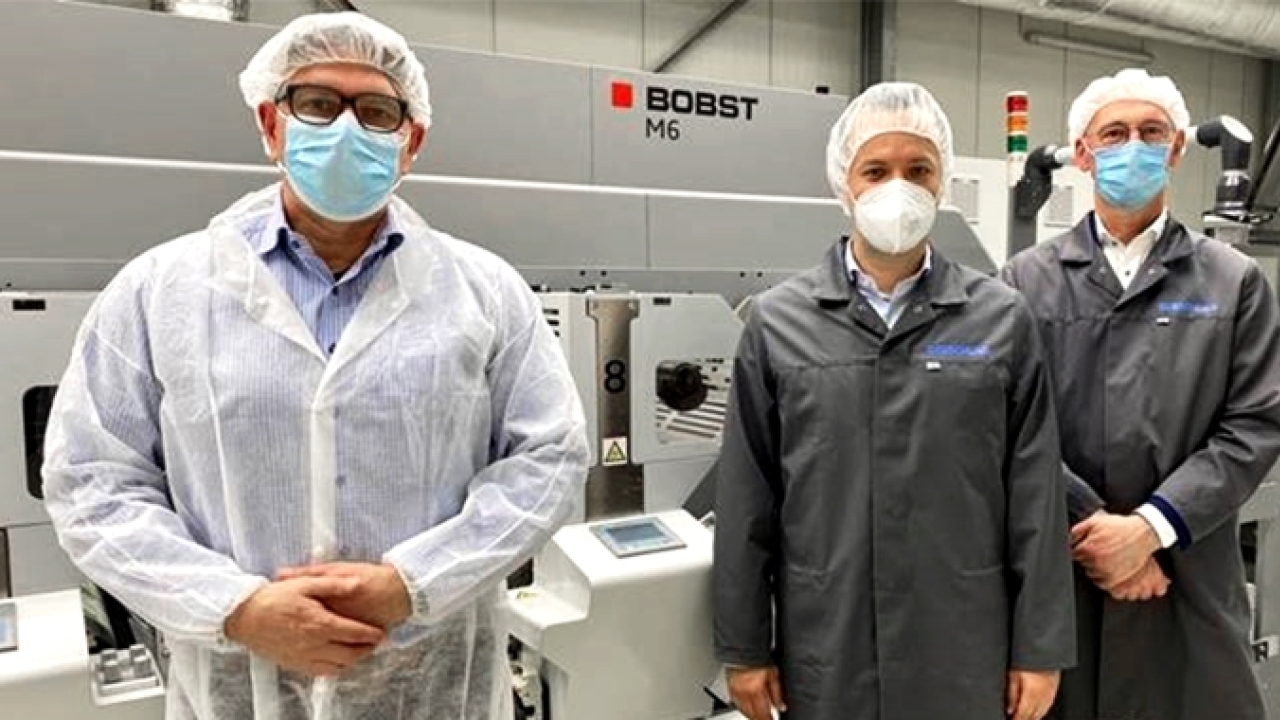
Derschlag is a family-owned packaging manufacturer providing aluminium foil and plastic film products to the food, dairy, cosmetics and pharmaceutical industries, and traces its roots back to 1957.
‘We have worked with Bobst since 2011, because we trust their products and we know we can rely on their local support and service,’ said managing partner Michael Scholz Jr., ‘As a manufacturer, Bobst is very experienced in different printing technologies and they always consider the customer’s requirements carefully when finding the right solution.’
The new Bobst Master M6 press was installed in 2020 along with additional die-cutting and converting machinery, while a brand-new production facility with more warehousing is also in progress.
As customer demands have changed to short and mid-size orders, Derschlag looked for technology that will enable it to respond faster to requests for new designs or other changes. The company chose the Bobst Master M6 UV Flexo press. The press handles all types of substrates for labels, flexible packaging, or folding carton, and can be fitted with multiple printing and inline finishing processes, including screen and gravure printing. When configured for flexible packaging, unsupported films from 12-micron PET and 18-micron BOPP can be printed, as well as PVC shrink films, alu-foil, lami-tubes and light cartonboard up to 300 gsm.
‘We did a lot of market research before making our final investment decision, but for our specific needs, we found that Bobst offered the best solution with regard to the technical possibilities,’ said Mr. Scholz. ‘The Master M6 was the right choice, because of the reduced set-up time and the possibility to print a wider range of different substrates. The machine has also increased the process stability and it is very operator friendly.’
The Master M6 can be equipped with DigiFlexo registration and pressure adjustment and oneECG color management for non-stop production through a fully digitalized press operation. Job changeovers can be performed in less than one minute with only a few meters of waste.
‘The high productivity and low running costs of the Master M6 will translate to a very competitive TCO for Derschlag,' said Maurizio Trecate, technical sales director, Bobst Firenze.
Stay up to date
Subscribe to the free Label News newsletter and receive the latest content every week. We'll never share your email address.