Flexolahti invests in Esko hardware and software
One of the leading Finnish packaging reprographic services and flexographic plate providers, Flexolahti, has improved plate consistency and overall productivity after investing in the latest Esko hardware and software.
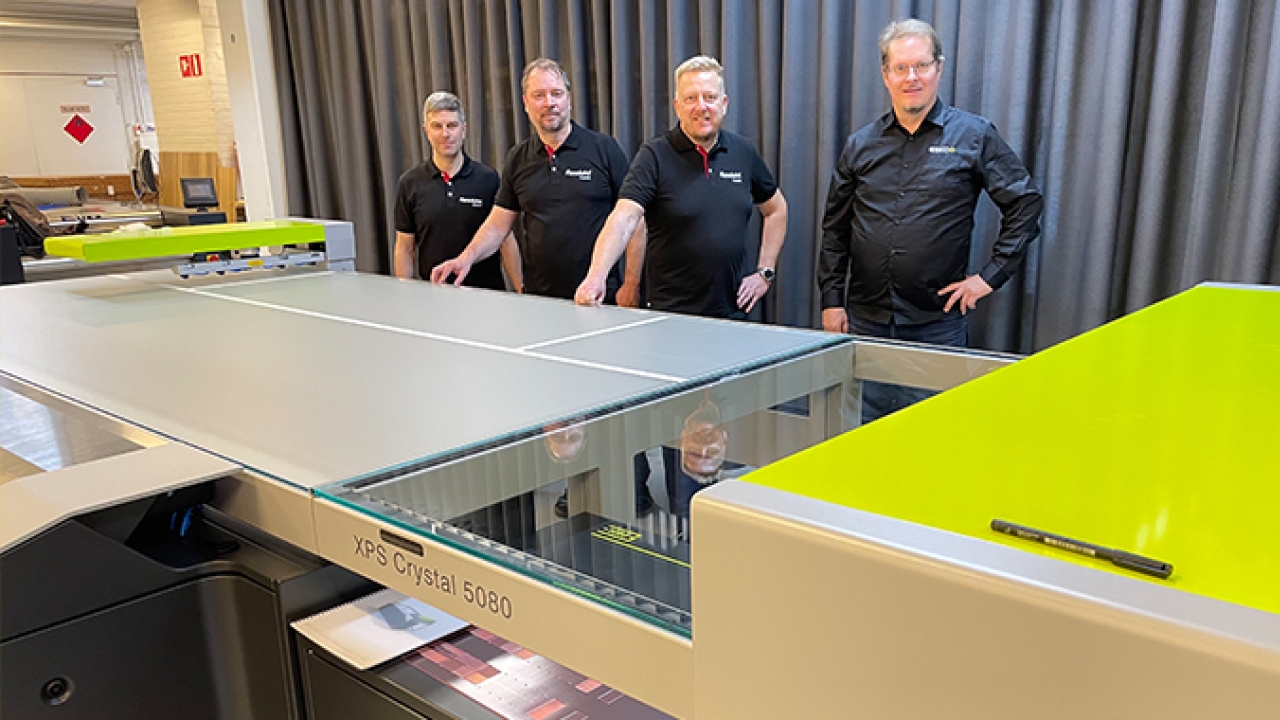
The award-winning company has complemented its existing Esko workflow by adding a CDI Crystal 5080 XPS with PlateHandler to its platemaking facility in Lahti, in Finland’s southern region.
‘Flexolahti is a business renowned for pushing the boundaries and investing in the latest technology to deliver the very best service to its customers,’ said Ishu Khurana, Esko territory sales manager for the Nordics region. ‘Adding our innovative plate imaging and exposure hardware to an already impressive setup now enables Flexolahti to increase its productivity while ensuring the quality of the plate and resultant print quality is maximized. Using the latest technology in terms of improved simplicity and optimized quality, they also enjoy the added benefit of full Esko support in training, maintenance and troubleshooting.’
Flexolahti serves a growing number of printing houses and brand customers across the Nordic region and further afield, with ever-changing customer demands that require a fast response and accurate results.
‘With the new CDI Crystal XPS technology from Esko, the platemaking process - in terms of imaging and exposure - is now much less complex and has significantly fewer steps,’ added Khurana. ‘The integration of our workflow solutions and hardware technology means that the Flexolahti team is now completely in control of the quality and performance of their plates and subsequent print consistency.’
Combining UV main and back exposure, the Esko XPS Crystal exposure unit uses LEDs that do not require warm-up time and emit consistently stable light. Further driving productivity is the Automation Engine Automated Flexo Platemaking module, which removes the need to crop and extend LEN files manually and enables a fully-automated platemaking workflow, from a ripped LEN file to the exposed flexo plate on the CDI.
‘Flexolahti has also installed the new Esko PlateHandler, a robotic device connecting the CDI Crystal imager with the XPS Crystal exposure unit,’ said Khurana. ‘The PlateHandler removes the need for an operator to manage multiple devices to produce a plate. It reduces the number of operator touchpoints, removing the risk of human error and freeing up to 50 percent of their time. For Flexolahti, this means the operator can attend other more value-adding tasks such as quality control, plate storage, and plate mounting.
‘As well as the latest platemaking technology, the team is also using Esko ArtiosCAD and ArtPro+ in the job design and editing stages, with Automation Engine and WebCenter automating the workflow and further boosting productivity and efficiency. They have a full Esko ecosystem in operation, producing consistently high-quality plates. Not only that, but the company uses Esko Studio 3D Store Visualizer software for dynamic print visualization. This means their customers are able to see a wide range of substrates, printing and finishing effects in real-time, and can also view packaging designs in ultra-realistic 3D.’
Kai Tornikoski, managing director of Flexolahti, said the company’s continued investment in cutting-edge technologies is part of planned development and commitment to using innovative technology to deliver the optimum service to its customers.
‘We have been working with Esko solutions for many years, ensuring that everything from structural design to prepress editing is handled as efficiently as possible while delivering the best results for our customer base. This latest investment not only ensures we can continue delivering plates of the highest quality but also enables us to increase our productivity, producing more plates in less time and having the flexibility to respond to the ever-changing needs of our customers,’ said Tornikoski. ‘This will, of course, be particularly valuable to us with regards to meeting the demands of those urgent, short runs with shorter lead times, but also on longer runs where consistency is key. With our complete Esko ecosystem of integrated solutions already in place, we are delighted to have been able to install the CDI Crystal 5080 XPS into our platemaking setup.’
Stay up to date
Subscribe to the free Label News newsletter and receive the latest content every week. We'll never share your email address.