French label printer boosts productivity with ink management
5SeptÉtiquette, a flexo and offset label converter based in Courthézon, France has reduced its lead-times and ink waste with the installation of GSE Dispensing’s Colorsat Match Dispenser and GSE – CERM integration software.
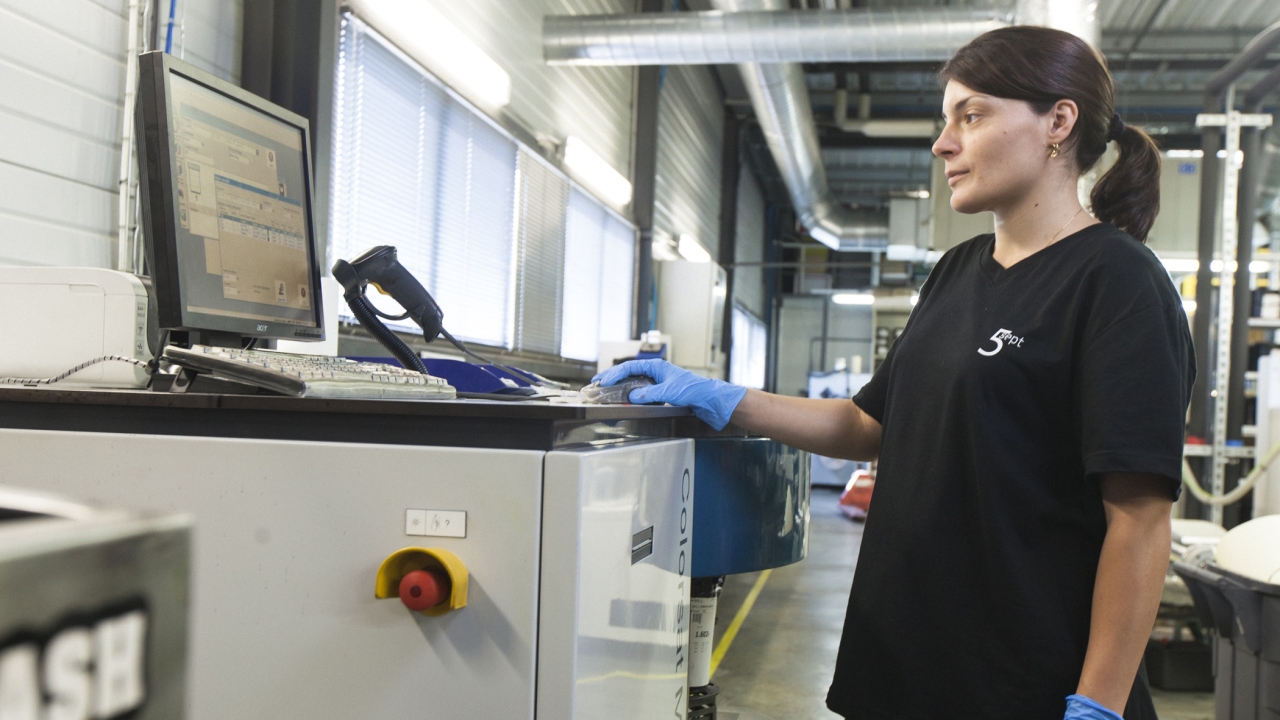
The company can also now provide shorter runs and regular supplies of labels on a just-in-time basis.
The majority of 5SeptÉtiquette’s orders increasingly fall between 2,000 and 4,000m and design lifecycles have become shorter because of the need for short-lived promotional messages.
And with lead-times typically at 24 hours, the laborious, labour-intensive and unpredictable manual method of ink recipe formulation was no longer suitable: automation became a necessity because there was no room for error and resulting remakes or production bottlenecks.
The GSE – CERM instalment provided a smooth ink logistics solution for its flexo printing division, which comprises two Nilpeter FA4s, one six-color and one eight-color.
‘With the GSE dispenser, we are able to mix the exact quantity of ink necessary for the job and have closer control of the quality of the colors,’ said 5SeptÉtiquette managing director Patrick Wack.
‘We meet the customers’ needs for high-standard, unique colors to an accuracy of within 1ΔE. This accuracy is vital to ensure a product has high impact on the retail shelf. For example our organic produce clients want specific and eye-catching greens for effective brand positioning.’
GSE’s ink management software (IMS) allows the printer to store a database of commonly used, complex ink recipe formulations and offers standard integration with other IT packages, giving the production manager real-time data about recipe availability.
5SeptÉtiquette’s new recipes are developed with a spectrophotometer and formulation software from X-rite. The new recipes are then exported to GSE’s IMS software, which in turn interacts with IT management software from the Belgian company CERM. Using CERM MIS software, the user creates a library of printed products and describes the colors of each. When the customer service team enters an order for a product or a group of products with the same substrate/tooling/cutting requirements, the ink requirements are exported to the IMS.
The CERM software then calculates the number of labels and instructs the GSE software which recipe is needed, and in what quantity. IMS calculates how much base inks are required and dispenses the ink batches for the order. Inks that return from the flexo press after the job is printed are weighed in and are subtracted from the order’s ink consumption. This information is then exported to the CERM software, giving operators a real-time view of ink costs per order. Furthermore, with the IMS-CERM connection, production management can see in real time which recipes are available, to enable Quick Response Manufacturing.
‘Each job is perfected due to the exchange between GSE software and the CERM business management program,’ said Wack. ‘We are developing what we think is a very interesting “digital flexo workflow”, working on the creation of a color database and the connection of this database with our MIS and pre-press system. The GSE system’s ease of connection with the IT software was an important selling point. The two software platforms have enabled us to accurately work out the ink costs per job, giving us greater control of our prepress budget.’
Anne Lourens, managing director at GSE Dispensing, added: ‘It is vital that label and packaging printers implement a lean management system. Reducing ink waste from the work-flow enables printers to achieve a high level of accuracy at lower costs and ensures quality consistency.’
Stay up to date
Subscribe to the free Label News newsletter and receive the latest content every week. We'll never share your email address.