LTI invests in more Martin Automatic technology to boost productivity
Family owned Labels, Tags & Inserts Inc. (LTI) has ordered two new Martin Automatic machines to complement the latest Mark Andy P7 Performance Series press due to be installed in August. The new 20 inch (510mm) nine-color Mark Andy flexo line will join a similar P7 press installed in 2015 at LTI’s production facility in Burlington, North Carolina. In all, the company will then have six Mark Andy presses (totaling 37 print units) and brings to seven the number of Martin splicers and rewinders purchased, the latest of which are an MBSF and MLSW automatic unwind/splicers due to be fitted to the
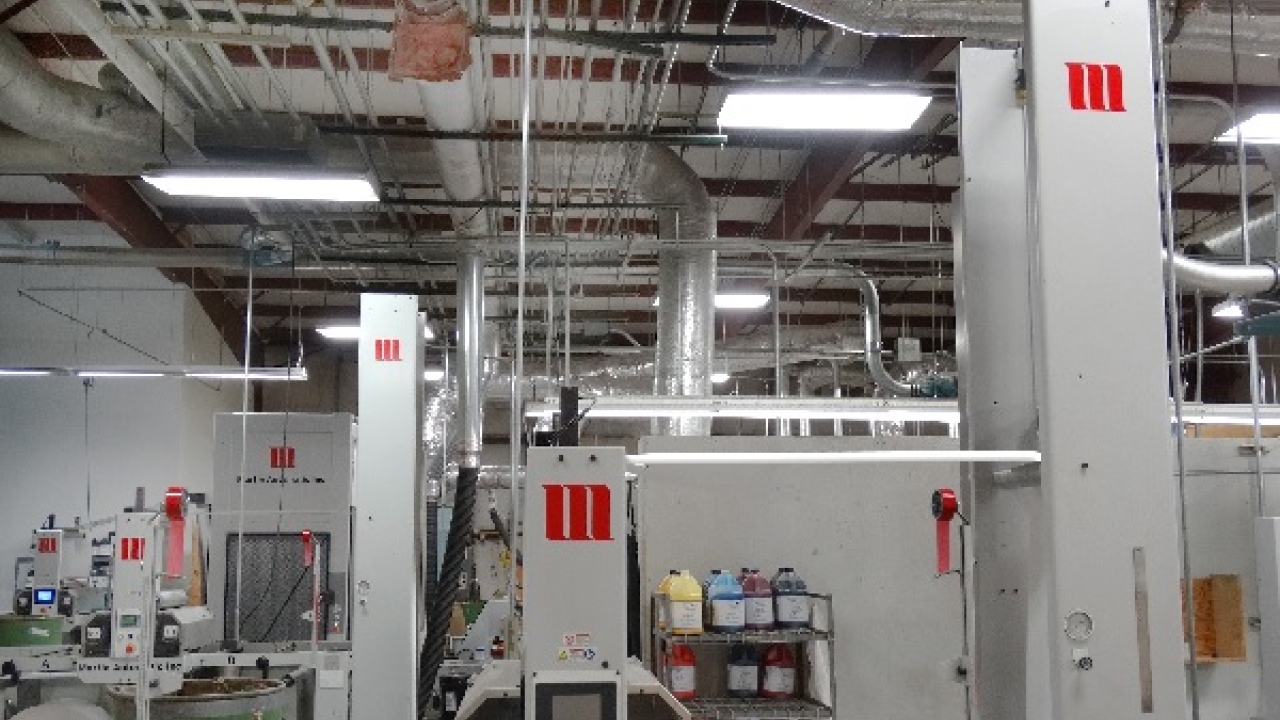
Established in 1994 by Leroy Baker, and currently presided over by his daughter, Rhonda Baker. The company has enjoyed two major growth spurts since 2006, which has seen turnover increase by more than 250 percent to a point where the plant now occupies a 20,000 sq/ft (1,860 sq/m) unit, and employs 27 staff.
Rhonda Baker said: ‘Our business has always been based on quality – quality product and quality service - so investment in the right technology is vital. We see the combination of Mark Andy flexo printing and Martin Automatic unwinds and rewinds as a crucial element in our ability to produce consistent quality, and offer added value products to our customers.’
The latest Martin machines unwind the base substrate on the MBSF butt splicer, while the laminate is unwound and fed inline by the MLSW after the final print unit. The MLSW, for self-wound, is one of a series of machines developed by Martin to automate inline lamination and decoration, including foil stamping. Rather than splitting the press line or bringing the laminate in from 90 degrees, Martin Automatic worked with Mark Andy to develop an integrated inline installation utilizing base press modules to present a more ergonomic product.
The unwind spindles and splice unit extend into the aisle, allowing the operator to load new rolls and prepare the splice comfortably in front of the press, and avoid the dangers associated with using step ladders. The MLSW utilises a driven peel roller for tension control and noise reduction of the unwinding self-wound film. It will also unwind and splice ‘dry’ films for inline adhesive lamination, as LTI plans on using both types of over-laminate processes on the new press.
One of the markets that LTI sees developing fast is for shrink sleeves on beer cans for the craft breweries that are springing up around the country. Lacking the resources and run lengths to justify printing direct onto the metal, the breweries turned to LTI, whose solution offers brighter and sharper graphics on shorter runs, giving a far higher visual appeal on-shelf.
‘High quality pre-press and continuous running are the keys to achieving these new graphics, and the Martins allow us to offer a better value product and more consistent downstream performance. They have played and continue to play a fundamental part in the success of this company,’ Baker said.
Stay up to date
Subscribe to the free Label News newsletter and receive the latest content every week. We'll never share your email address.