Morancé Soudure invests in Comexi press
Flexible packaging specialist Morancé Soudure France has invested in a Comexi F2 MC 10-color flexo press to reduce setup times and costs by changing multiple SKUs.
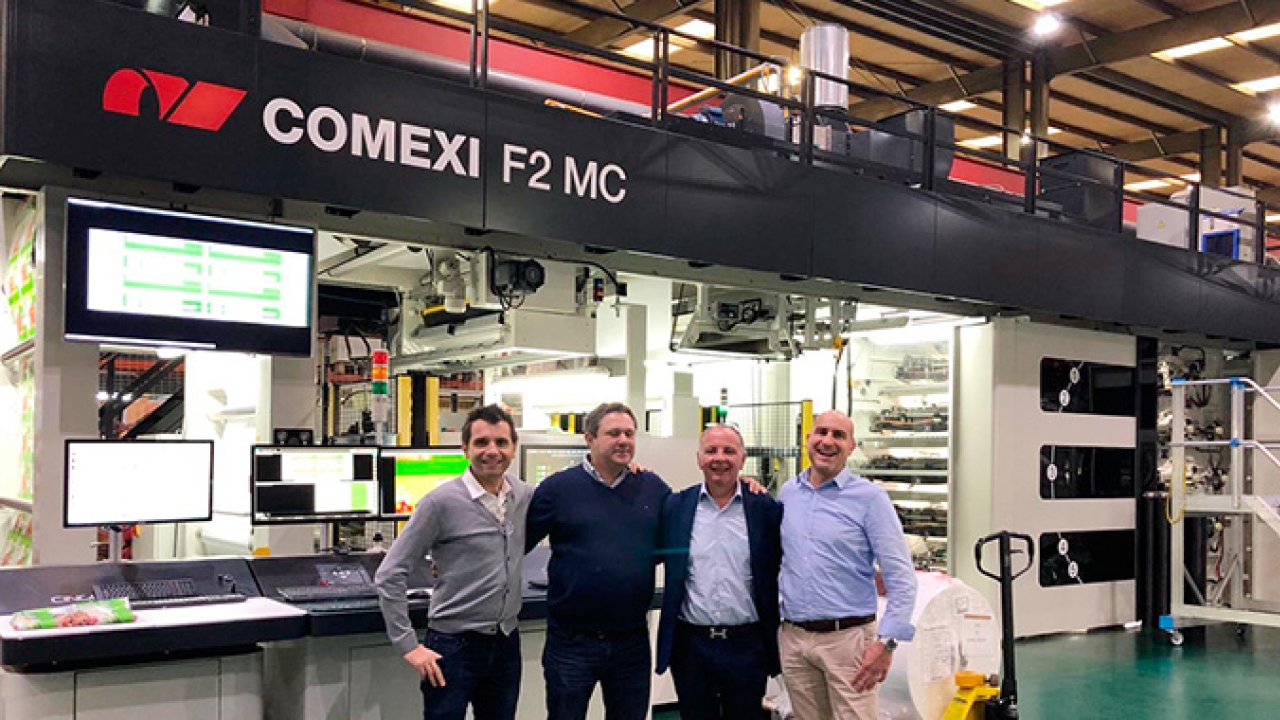
The French company, established in 1975 making freezer bags in a garage, was created by Jean Pierre Barbier, president of Morancé Soudure France. For over 30 years, it has primarily exported products to North and West Africa. The company currently has more than 80 workers at its production plant located in Villefranche sur Saône (Rhône). With the new Comexi F2 MC 10, Morancé Soudure France will print flexible packaging for foods, pet foods, frozen foods, garden centers, and nuclear products.
‘We have decided to invest in a Comexi F2 MC 10-color press for various reasons. Firstly, to renew our fleet of flexographic machines. We had two old machines from another company; the Comexi F2 MC 10-color will largely replace the production of both these machines. Secondly, we were looking for a flexo machine with extremely short setup times in order to reduce our costs due to the ability to change multiple SKUs. Furthermore, the re-print system is a huge asset, and this will be our first 10-color flexographic press,’ commented Olivier Fedel, CEO of Morancé Soudure France.
The Comexi F2 MC press has been designed to offer a robust design along with state-of-the-art electronics, minimizing impacts and vibrations and allowing converters to achieve excessive speeds without bouncing. The new drying system reduces the required energy, while inking and doctoring have been optimized through three patents. The collaboration with top suppliers of video and inspection systems creates a complete automatic pressure and register system with minimum waste.
The latest acquisition is an additional purchase to the Comexi S1 DT slitter, which the French company acquired in 2020.
‘We are extremely satisfied with our slitter. It has enabled us to optimize the productivity of our flexographic projects, as we no longer use the process of inline die-cutting with our printing machines,’ concluded Fedel.
Stay up to date
Subscribe to the free Label News newsletter and receive the latest content every week. We'll never share your email address.