Colordyne unveils second-generation UV Retrofit
Colordyne Technologies has introduced 3800 Series UV Retrofit, a second-generation UV print engine technology redesigned to deliver enhanced usability, quality, and functionality.
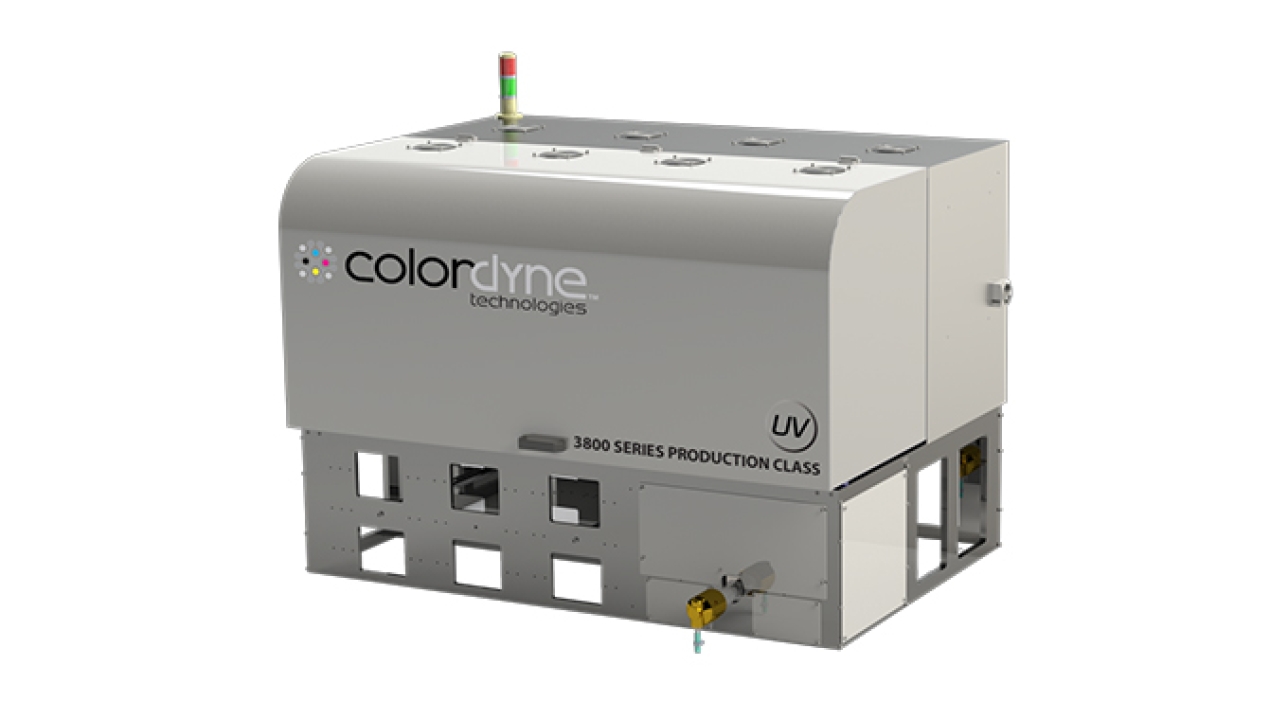
The 3800 Series UV Retrofit is a full-color digital print engine for label and tag production running up to 246 ft/min (75 m/min). The system can be configured for CMYK production with the option to add white, spot, extended gamut, and dual white for higher opacity. The engine is designed for additional color channels, up to seven, to be added at any time. In addition to the legacy equipment print widths of 8.5 inches (216 mm) and 12.75 inches (324 mm), the 3800 Series UV Retrofit is available in 4.25-inch (108 mm) and 17-inch (432 mm) configurations.
The new retrofit transitioned the clamshell chassis design into an automated vertical lift system. This change provides users with more automated functionality, including print positioning and splice detection. Automatic maintenance is another feature that can be added to the retrofit print engine during the initial acquisition or as an optional upgrade after installation.
‘Digital print technology is continuously changing, and Colordyne Technologies’ goal is to help our customers adopt digital print using the latest technology,’ said John Urban, director of engineering at Colordyne Technologies. ‘After nearly four years on the market, we knew it was time to evaluate and upgrade our UV inkjet technology. Using customer feedback, we improved the design and functionality of our 3800 Series UV Retrofit by adding key automation features that make the system easier to operate, reduce human error, and optimize production efficiency.’
To improve print quality, the 3800 Series UV Retrofit uses pinning lamps between each color channel, in addition to the previous model’s final cure lamp. Users have better control with inter-color pinning and receive higher quality results through the prevention of coalescing. Software upgrades to the system allow the operator to control each lamp, pinning, and the final cure, ramp profile, as well as their intensities.
‘We completely re-designed the ink deliver system (IDS) in this engine to deliver superior performance and reliability,’ added Urban. ‘To support the IDS upgrades, we also implemented a standby mode in the software. Together these features simplify maintenance and reduce downtime due to nozzle outs, ink separation, and lengthy morning startup procedures.
‘We are excited for the first installation of this unit, which is happening this month. We know the changes that were implemented will benefit our customers and help them produce high-quality labels and tags. Plus, we were able to execute these enhancements without increasing the cost to our customers, which means converters can continue to retrofit existing equipment at a cost-effective price point.’
Retrofitting allows new and existing analog equipment to incorporate the benefits of full color digital and hybrid printing. The analog system maintains all its original functionality, including flexo stations and finishing equipment already on the press. Benefits of retrofitting include faster turnaround times, on-demand production, and cost-effective versioning.
Stay up to date
Subscribe to the free Label News newsletter and receive the latest content every week. We'll never share your email address.