Gietz launches ROFO 450 ECO press
Gietz launches its new ROFO 450 ECO press with next generation Gietz machine user interface. The machine focuses on providing a compact and economic solution for label printers and converters from small to large job runs. With this Gietz follows on with its successful ROFO 450 series.
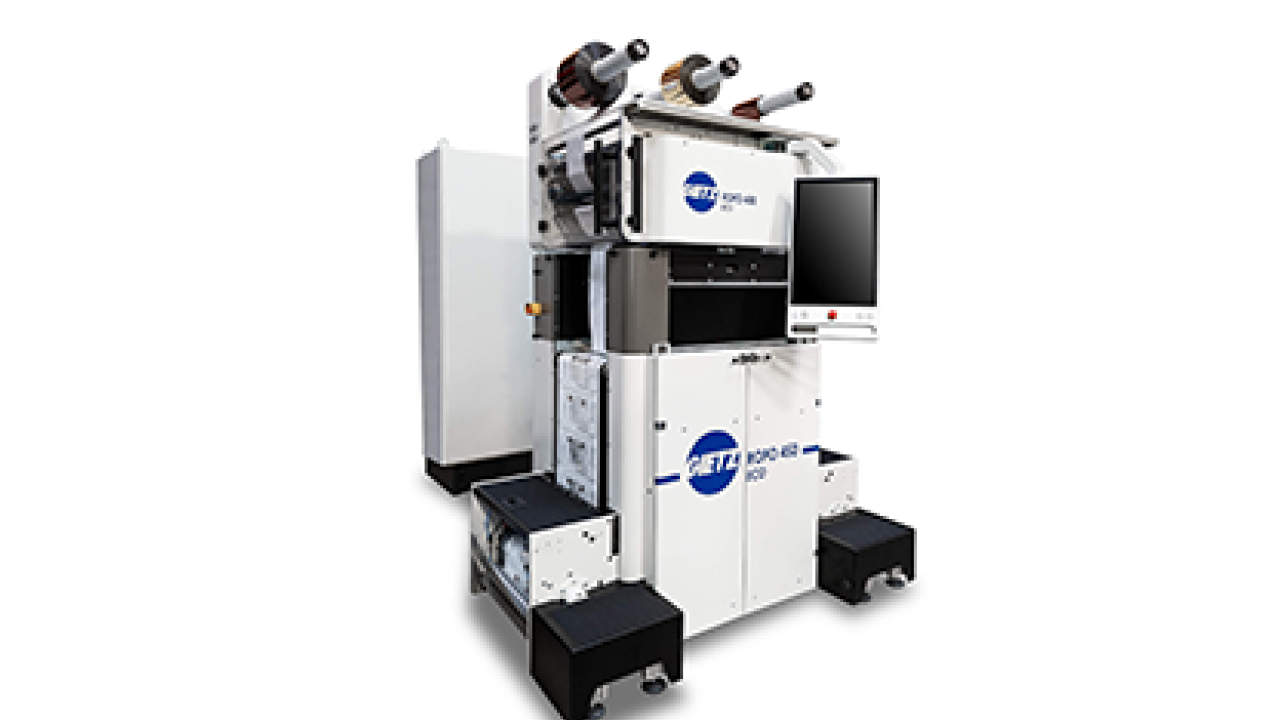
The ROFO 450 ECO is specifically developed as a core model for narrow web embellishment processes of printed and non-printed web substrates. According to the company, this makes it the perfect product for the fundamentals of label production and packaging printing. The ROFO 450 ECO is designed to process pressure sensitive materials (adhesive labelstock), paper, cardboard, plastic film and composite substrates.
History of the ROFO 450 series
The Gietz ROFO 450 hot foil stamping machine series debuted in 2015 at the Label Expo in Brussels. The high-performance flatbed unit was marketed to the high-end customer aiming for a sophisticated and comprehensive hot foil stamping product.
Later the ROFO 450 PLUS was added to the series, being able to present even more competitive output results.
On the contrary, the newly developed ROFO 450 ECO targets print converters and label manufacturers looking for a compact perfect, that meets 90 percent the markets need. It is likewise a good starting point for companies looking to enter the market.
The ECO version still features the well-known key benefits of its predecessors such an unbeatable large stamping surface and a unique stamping force. Moreover, the machine is aimed to have a good market requirement fit.
What makes the ROFO 450 ECO perfect for label production and packaging printing?
Stay up to date
Subscribe to the free Label News newsletter and receive the latest content every week. We'll never share your email address.