Software success in South America
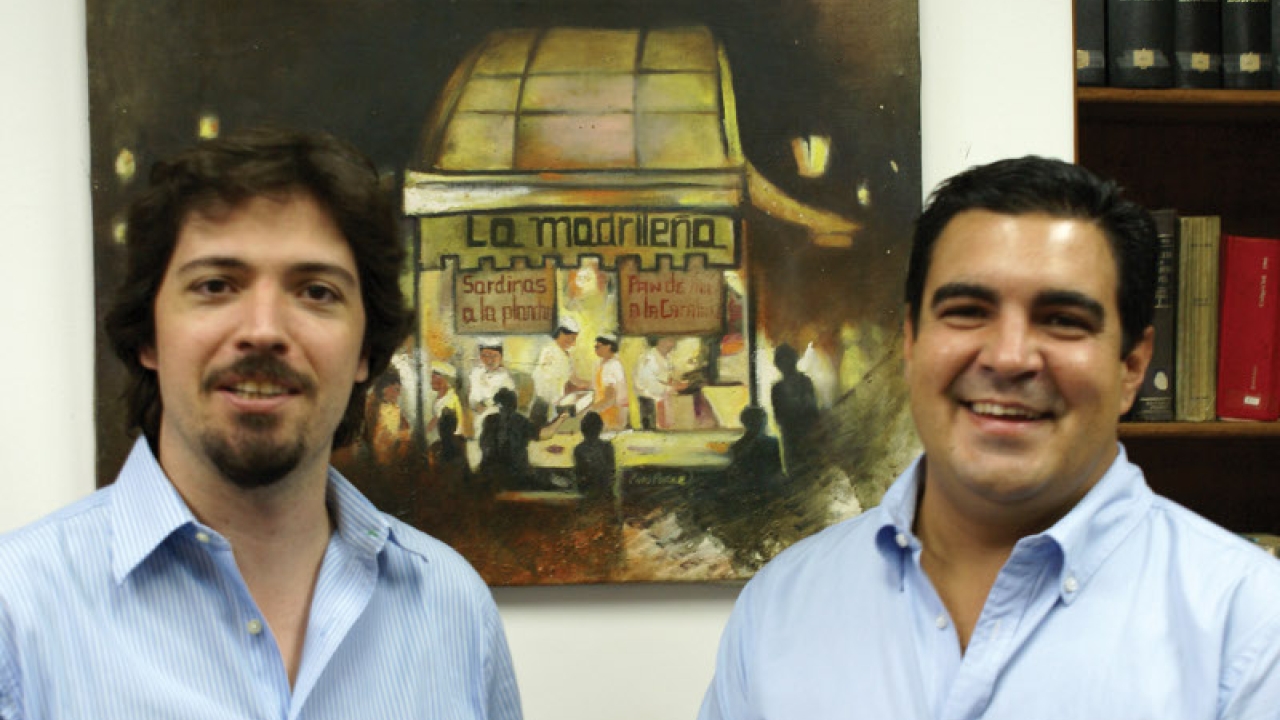
UpSoftware Argentina is experiencing an increase in sales amidst changing attitudes towards workflow software in Latin America. James Quirk reports
In a region where workflow software historically has had little presence, UpSoftware Argentina is experiencing increasing success with a system that appeals to multinational enterprises and smaller family-run print shops alike.
The Buenos Aires-based company has installed over 50 of its SisPro workflow systems in eight countries around Latin America since its foundation in 2006. The bulk of its clients are in its local market of Argentina, with other customers in Mexico, Costa Rica, Ecuador, Chile, Paraguay, Uruguay and Brazil.
If workflow systems from the industry’s leading international suppliers are increasingly all-encompassing and complex, UpSoftware Argentina’s SisPro returns to the core principles of the idea – collection of useful data, simple presentation and effective analysis.
The effectiveness of the system with regards to these core competencies is reflected in an impressive installation base. It counts many of Argentina’s leading label printers among its customers, including Artes Gráficas Modernas, one of the region’s largest integrated converters, and Autopack, an advanced self-adhesive label printer serving high-end brands in the food, cosmetics and pharmaceutical industries. Multilabel has the system installed in its facilities in Argentina and Brazil, while Impresores, a sheetfed offset converter which prints the labels for Quilmes, the country’s most popular beer brand, is another user. Among its international clients is a leading Mexican converter which has the system linked to some 20 machines.
UpSoftware Argentina also counts many smaller print shops among its customers, and sales director Gonzalo Tagliabue believes previously sceptical attitudes towards software are changing. ‘Historically, there has been little use of software in Latin America. There’s a view that it is an expense as opposed to an investment. But as the generations change, so do attitudes. Often it is much easier to sell to the son than the father.’
Information exchange
UpSoftware Argentina’s system contains two applications, one of which facilitates the programming of production (SisPro) and the other which controls production (SisPro Terminal). The two systems are linked, allowing information exchange between them. SisPro also connects directly to a company’s existing database and can automatically extract data from the scheduled jobs and portray tasks in the form of bars in a Gantt chart.
SisPro allows the user to track visually the use of different resources, such as machines and labor, in order to maximize efficiency when planning work schedules. The user can follow the progress of each task in real time and determine exactly how long each job will take. The system allows the user to visualize several days or even months of production; modify the printing schedule quickly and easily; and share information between different departments, such as sales, production and logistics.
Data entered into the system is processed and transformed into useful information displayed in reports that can be printed, emailed or exported in different formats. Data can be filtered in different ways (by sector, task, job number etc) in order to obtain the desired information.
For added security, SisPro and SisPro Terminal have levels of access that can be customized for each user. In addition to limiting access to menus and functions, the system can restrict access to specific tasks, sectors and functions within production. A mobile phone application and wireless network allows access by authorized users when outside of the factory.
‘It’s a very visual system which brings everything and everyone in production together,’ says Tagliabue. ‘Graphics clearly show how long a machine is busy for, and when it is free for another job. It is also highly flexible: it can be tailored to each machine or cover them all.
‘The system shows you when decisions need to be made. The figures and analysis can justify an investment that might not have been thought necessary. After a few months of use, very often a client will be shown where efficiencies can be made. For a company that uses the system well, it is a gift. It basically becomes free after a short time of use.’
Tagliabue cites the example of Buenos Aires-based Impresores. ‘It’s an enormous company, with fleets of Heidelberg sheetfed presses. They had a problem with paper sometimes being delayed in getting to a machine. The SisPro system saves them around half an hour each day in this area, and if you times that by weeks and months, serious time and cost savings can be achieved.’
Increasing reach
In 1998, Sergio Perez Camps, co-founder of UpSoftware Argentina and Tagliabue’s business partner, was approached by a local printer which was seeking automation for processes such as budgets and billing. He began development and within three years had secured orders from Artes Gráficas Modernas and Impresores. In 2005, Gonzalo Tagliabue joined and the pair officially founded the company shortly afterwards.
The system is updated every 3-4 months, often with suggestions from clients. One customer wanted jobs that had missed their delivery date to be flagged up, a feature that has now been incorporated. A new touch screen interface is currently under development, which will offer additional information and ease of use to the operator.
Tagliabue says that the company is now actively seeking distributors in different parts of the world. Negotiations are currently under way with a company in Spain, which will provide first entry into the European market. Mexico, which outside Argentina has the highest number of SisPro users, is a key focus. Good leads were established in the country when UpSoftware made its Labelexpo debut in Chicago last year. The company focused purely on the event’s high number of visitors from Mexico and the rest of Latin America.
Proimplas, an Argentina-based supplier of consumables for the plastics industry, has already been appointed as a distributor and has helped the system reach a new market. Currently available in Spanish, English, Portuguese and Italian, the system’s language file can be extracted and translated and can therefore be used in any part of the world.
Happy customers
Two leading Argentine converters which use UpSoftware’s SisPro system are Autopack and Multilabel.
Autopack, a self-adhesive label printer serving the food, cosmetics and pharmaceutical industries, installed the system in 2007 and has it connected to four printing presses. Production manager Jorge Almaric cites control of production as the key benefit brought by the system. ‘We have been able identify the problems causing a machine to stop, whether they be mechanical idiosyncrasies or issues with the press,’ he says. ‘By then acting on this information and resolving the problems, we have improved our productivity.’
Multilabel installed the SisPro system five years ago in its plants in Buenos Aires and Brazil. Company president Luis Maria Garcia says that the system has been integrated into all areas of Multilabel’s business, including budgeting, sales and job programming. ‘All printing machines are connected to the system, as are the sales and pre-press departments, which feed into the system information about job preparation and material purchasing,’ he says.
‘It has helped us with our job programming by allowing us to make urgent changes without having to start from scratch. It allows us to know the actual state of a given job at a given time. The graphics help us to make crucial decisions about how to get the most out of machines and reduce downtime. It allows us to know exactly the production cost of each order, in terms of the amount of machine time it requires, the speeds of the presses, changeover times, and a great deal of data that was previously estimated or registered manually.
‘Thanks to all production being digitalized and controlled, we have been able to detect weaknesses and failings in our processes which were making us less competitive. By making adjustments and resolving these issues, we have received benefits that effectively mean the system pays for itself.
‘SisPro also has the flexibility to be able to attach itself to or integrate itself with the company’s other management systems, which makes it an important work tool. We are very happy, not only with the system itself, but also with the post-sales service with which we are provided.’
Pictured: L-R Gonzola Tagliabue and Sergio Perez Camps of UpSoftware Argentina
This article was published in L&L issue 1, 2011
Click here for more stories about UpSoftware Argentina on L&L.com.
Stay up to date
Subscribe to the free Label News newsletter and receive the latest content every week. We'll never share your email address.