Efficient job planning and production scheduling
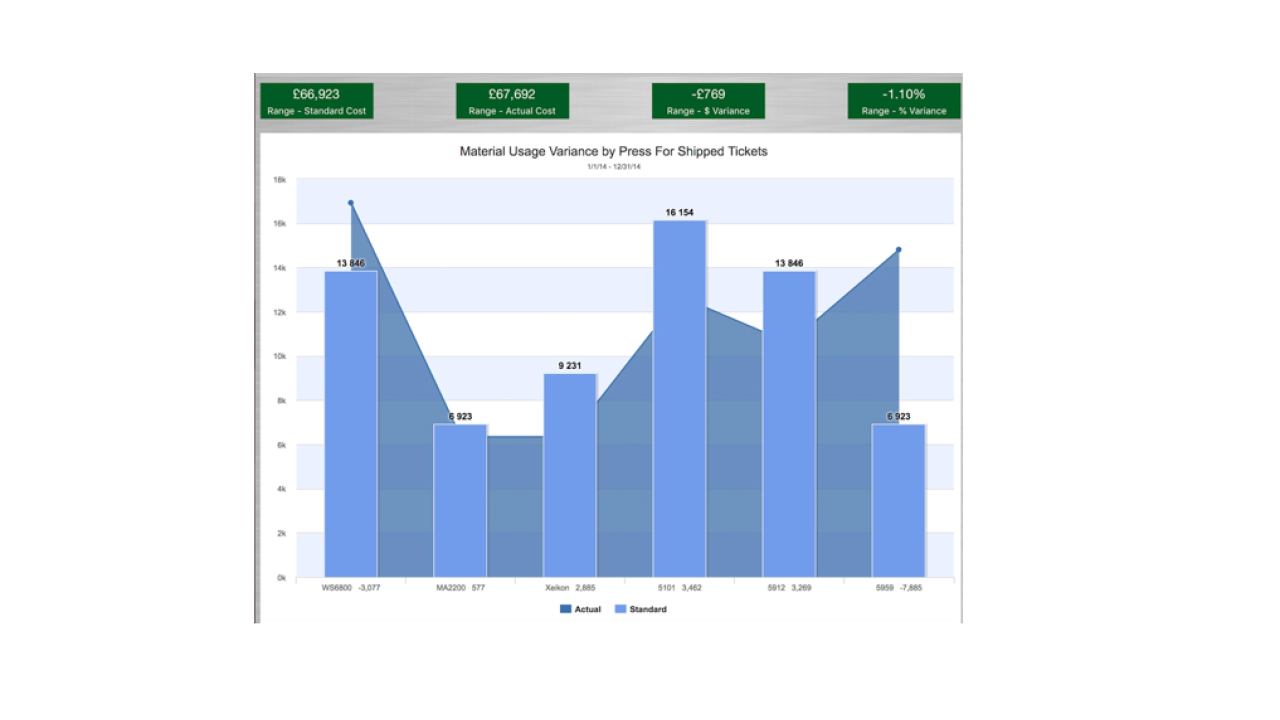
The process of planning jobs and managing their production through a label or package printing plant can be quite complex. The process needs to constantly monitor the changing workload of individual machines and printing processes, complete print production orders to schedule, and maintain accurate staffing levels. Ideally it should also highlight spare capacity, display slippage, spot bottlenecks or problem areas, offer ‘what if’ scenarios and prioritize orders thereby maximizing the company’s technology investment and minimizing machine downtime.
The growing proliferation of shorter runs, the need for multiple versions or variations, a requirement for sequential coding or numbering, jobs with hot or cold foiling, embossing, matt or gloss varnishing, are just a few of the things that can challenge scheduling. Multi- shift and multi-process pressrooms present further challenges. Even pressrooms with just one or two presses and a handful of jobs at any given time, can make effective scheduling tricky.
It is not simply a case of lining up jobs by due date, in the order they were received. Label and package printing has a great many variables to be considered in order to strike a good balance between efficiency on the pressroom floor and shipping the printed jobs when promised. Indeed, the most efficient job sequence is not always readily apparent.
Multiple deadlines, urgent rush jobs, special finishing requirements, delays in ink or paper delivery may all make it necessary to arrange jobs in scheduling sequences that are far from ideal with respect to production efficiency. Batching jobs by material, size, or ink can mean that jobs with due dates that are even days or weeks later may be scheduled to print before those with closer due dates.
Indeed, there are often so many variables, especially those that may occur unexpectedly – employee sickness, press breakdown, damaged plate or cutter, temporary shortages of materials, conflicts with jobs requiring the same plate cylinders, the need to delay one job so that another may be printed on a particular press – that any number of criteria may have to be constantly evaluated in order to determine the order that labels or packaging should be printed in. Ideally, the scheduling system should also be able to block-out recurring or planned maintenance periods where a press or process is unavailable.
All these requirements and pressures lead to a need for an efficient and easy way of conveniently presenting and viewing jobs that need to be printed in some form of job planning or scheduling system. A system that provides an easy-to-view means of sorting, grouping, controlling, planning and viewing the sequences and steps of production on possibly an hourly, daily, weekly, shift, machine or personnel basis as required. It can also be valuable for the scheduling system to undertake capacity analysis over a defined period to determine potential future bottlenecks.
Modules used for job planning and production scheduling in the label or package printing plant are today an essential element of a MIS workflow system and can provide full visibility of machine capacity, both short and long term, and offer detailed scheduling of each production step of the job, from customer approval right through to shipping. Depending on the software it may also be possible for press operators to consult their work schedule on their press or feedback what they are actually doing. A change in schedule can be automatically seen on the shop floor.
Increasingly, MIS systems offer real-time feedback of shop floor activity to the scheduling board or screen via job tracking terminals or JDF capable systems. Others may look to define the current running efficiency of a resource for new operators, or identify machine faults to automatically adjust running time of operations. Some can provide an out of sequence alert, indicating jobs started early or not as planned, and so alerting the scheduler.
So let’s look at some of these production scheduling systems in more detail.
Production scheduling systems
Production scheduling systems or tools come in a wide variety of formats and systems starting from spreadsheets generated on a PC screen or printed out onto paper, and ranging through White Boards, Magnetic Boards, Card Planning Boards, Adhesive Strip Boards, right up to sophisticated production scheduling software incorporated into the latest MIS systems.
All of the above systems, sometimes used in combination, can be found in the industry. Why? Because, while computerized production scheduling systems have definitely become an essential planning tool, they frequently only provide a limited view of the production schedule, failing to provide a planned ‘big picture’ or total production schedule overview that everyone can see. Constant scrolling or passing round instantly outdated printouts can be of limited help to busy production departments who must have a complete overview of the rapidly changing production schedule to make any informed amendments.
A guide to some of the main types of production scheduling boards and computerized systems that are available to the label and package printer are therefore briefly outlined below:
- Magnetic planning boards: Magnetic production planning board kits provide a wider format picture enabling a complete production schedule to be viewed at a glance. They can be rapidly updated, give an overview of production and presses, and may be operated as stand-alone scheduling boards or alongside software systems.
- Card planning boards: Card Planning Boards are an ideal system for when a large amount of job information is required to be stored and shown. A range of different card capacity sizes and heights are available. Card boards are ideal for production, project and personnel planning and are available in one or two week systems.
- T-Card production planning boards: Job information is written or printed onto a T-shaped job card (T-card) body with the ‘at a glance’ information onto the visible card shoulder. Information can be handwritten or transferred directly from a computer printer or photocopier using perforated job card sheets.
- Printed white board production planning boards: Magnetic whiteboards printed with production and project planning grid designs provide an economic planning/scheduling alterative. A dry wipe surface enables data to be easily written and erased.
- Adhesive channel strip boards: An inexpensive solution that uses adhesive backed channel strips that firmly adhere to a backing board so as to hold job card strips, so creating an individual planning/scheduling board.
- PC with spreadsheet software: Spreadsheet software can provide an effective means of scheduling using functions such as cutting, copying, inserting, pasting, formatting, coloring text, sorting, and filtering of records so as to provide spreadsheets on which all print jobs can be easily seen on the computer screen (or printed out), rearranged, sorted and displayed by press or process, order or job number, run length, delivery date, customer or any other requirement.
- MIS production scheduling modules: MIS modules used for production scheduling in the label and package printing plant are available to provide full visibility of machine capacity, both short and long term, and offer detailed scheduling of each production step of the job, from customer approval right through to shipping. Depending on the software it may also be possible for press operators to consult their work schedule on their press or feedback what they are actually doing. A change in schedule can be automatically seen on the shop floor.
It is also possible to reserve production slots for jobs that are expected, view milestones for scheduled jobs as well as schedule in planned maintenance, down time or holidays. When necessary, a scheduler can move a job up or down the queue, or even split-run the job, part now and part later, or perhaps run in parallel on different presses. A good system can also indicate how much and when overtime will be required. It is also possible to optimize make-ready times by grouping or ganging similar labels or labels with different shapes together, especially if they have the same substrates, colors or cutter tooling.
With some of the more sophisticated MIS systems data can be sent direct to Esko’s Automation Engine for pre-press, proofing and automated step and repeat. More and more digital presses today also come with built-in software to create step and repeat.
Some of the latest computerized production scheduling and control systems used in the printing industry actually look and feel like traditional production board and are very easy to use. Indeed, time indicators moving across T-cards as a job progresses can be realistically used to drive a large wall-mounted plasma screen.
It may additionally be possible for a production scheduling and control system to also handle multiple user sites, a wide variety of plant, shift and overtime patterns, schedule multiple component and sections and handle large amounts of digital jobs as easily as conventional analogue printing. Move an item on one screen and it moves on the others. These systems can work standalone or live to the rest of the system by using shop floor data capture and networked machine monitoring.
Scheduling as a control system
Production scheduling, whatever the type of system used, can perhaps be defined as a control system that becomes part of the larger, more-complex label and package printer’s manufacturing planning and control system. The overall production scheduling system needs to be considered as more than a schedule-generation process, whether it is manual or automated. It is not just a piece of software, but should ideally be a system that interacts with all departments and provides information that all managers and supervisors need for other planning and supervisory functions. Sub status reports can also be shown to provide information on items such as:
- All artwork approved for a job
- Whether there will be enough material in stock on the scheduled production date
- Whether tooling is available
- Whether the order has been confirmed to the customer (to define priorities).
When looking at materials availability, it is important to be aware of possible materials shortages. It should be born in mind that poor production control and scheduling can undoubtedly be a recipe for disaster. If scheduling is inefficient and not managed properly, then the production floor does not know what to print and when, and machine efficiency can quite quickly fall through the floor. Customers don’t get orders filled on time, operators don’t get materials when needed, bottlenecks occur – all of which may spell trouble.
Production scheduling is at least as important as any other part of the production loop, and can be the cause of a company’s worst nightmare if not handled efficiently and correctly.
A well-ordered and managed planning and scheduling module will undoubtedly provide for and increase the transparency and visibility of a company’s production plans, help to manage and control progress and capacity right across the business, enabling each department to prioritize and manage their own workloads.
It is also invaluable in determining whether delivery dates can be met and can identify predictable downtime for maintenance schedules. A proper production schedule also gives production and other personnel a detailed statement of what is expected and in order that supervisors and managers can measure productivity and performance.
Other advantages include minimizing WIP (work in process) inventories, set-up times and overall lead times as well as maximizing machine and production personnel. A good production schedule should also be able to identify resource conflicts, control the release of jobs to the production floor, and ensure that all required raw materials – such as blank product and correct ink colors – are purchased and received on time. Additionally, better coordination will increase overall productivity and minimize operating cost.
Label and package printing production environments may often change dramatically from one day to another, one shift to another, or even hour by hour. This means that the system needs to respond to the unexpected and quickly be able to identify backlogs and to modify existing production or press schedules. Flexibility in a system is therefore paramount. Keeping it simple makes scheduling manageable. Fast and responsive production scheduling is one of the major keys to successful supply-chain management, in some cases even linking customer’s and supplier’s schedules together.
Effective and efficient production scheduling today is an essential element in controlling and managing a label or package printing plant, and in providing profitable results.
Production scheduling – the work steps
To understand how the production scheduling process works within an MIS system, Cerm has kindly supplied a screen shot to explain the necessary work steps involved. As can be seen, there are four columns on the screen – Description, Status, Scheduled and Waiting time.
- The Description column shows the job order details, followed by the order date, proof date, plates, press, rewinding, finishing, shipping and delivery.
- In the Scheduled column, every work step is allocated a calculated time.
- In the Waiting time column, every work step is allocated a waiting time (queuing time needed to go to start the next step).
- Based upon delivery date and transport time, the MIS system calculates backwards (Status column) to determine the start of every step necessary: rewinding, printing, plate-making (depending on the complexity of the job) the allocation of resources and the sequencing of timing and tasks necessary to produce the printed products and as indicated in the illustration, MIS production scheduling is an automated system for dealing with related services.
Easier decision making
In summary, production scheduling using one of the latest MIS systems will make the key work steps in label and package printing decision making easier and simpler, in particular:
- In releasing jobs for production
- By prioritizing jobs that require resources (spot colors, special tooling, stamping foils, and so on)
- By assigning resources (people, presses, inspection machines)
- In reassigning resources from one job to another (similar jobs)
- By determining when jobs should be started (to meet deadlines/delivery dates)
- By halting a job that can be stopped to make way for another more urgent job (a rush order).
Today, a sophisticated MIS system is more than a nice-to-have tool; it is becoming a necessity.
Stay up to date
Subscribe to the free Label News newsletter and receive the latest content every week. We'll never share your email address.