The automated label plant of tomorrow
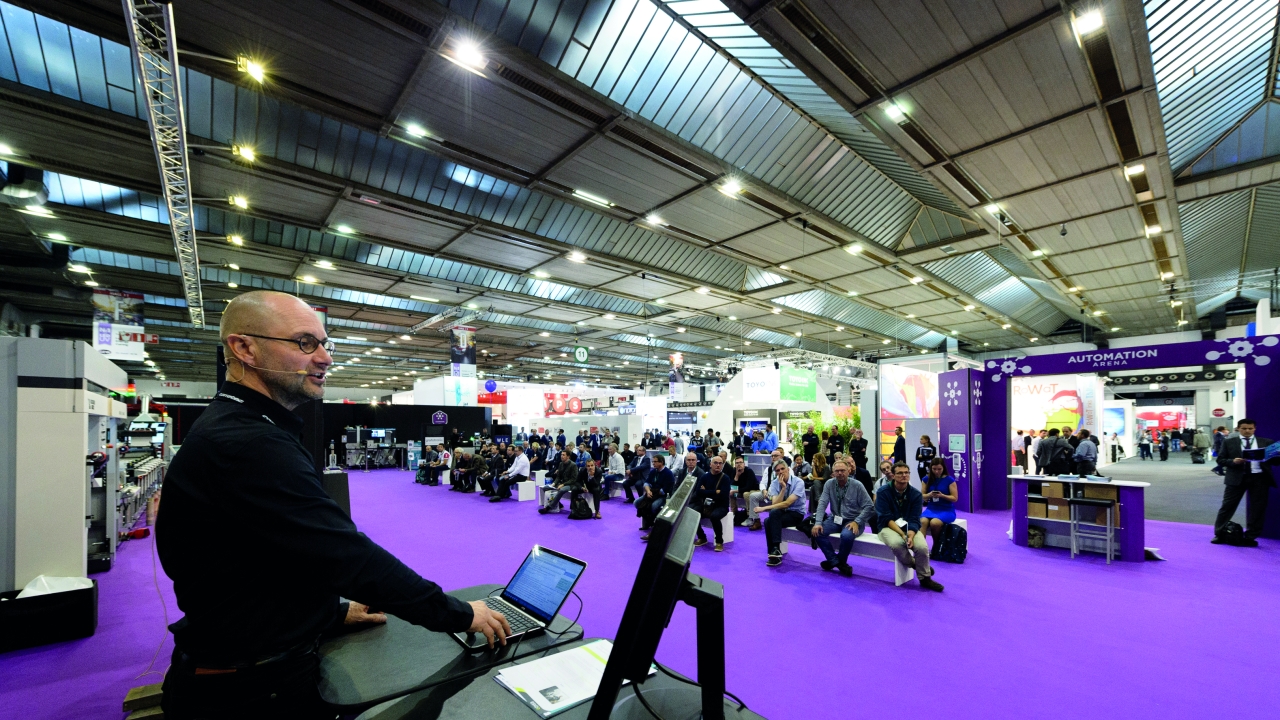
In a 30 minute demonstration, an audience member ‘customer’ selected both a digital and conventional repeat job label design and was able to follow these through all the necessary automated job management, pre-press, print production, inspection and finishing stages, waste removal and warehousing and, finally, through to job delivery and invoicing. Indeed, the whole automation feature was designed to present the printing plant of tomorrow with a level of automation and profitability never before attempted. From its initial concept, the overall aim of the Automation Arena was to convince converters that with the latest workflow technology it is now easier than ever to automate and process more jobs in the same through-put time, with fewer errors, with 100 percent quality and barcode inspection, incorporate automated press and finishing set-up, and all with the same number of employees.
Automated workflow
As the central hub of the Automation Arena, a Cerm MIS processed and managed the whole automated workflow, integrating with an Esko Software Platform supporting the end-to-end label workflow to change the selected digital label design and personalize with the customer’s name, create rules for inspection, and initiate a proof for customer approval.
Once approval of the label and barcode was received back from the customer, files were sent to a Xeikon 3300 with a Xeikon LDU laser die-cutting unit integrated with a Xeikon Vectorizer for step and repeat and printing, together with AVT inspection files, job identification and die-cutting and finishing barcodes for the in-line laser die-cutting, slitting and turret rewinding.
Meanwhile, the MPS EF 430 operator read his MIS-generated job ticket on screen, checked that plates, tools, inks and substrate had been delivered, changing the roll using a Kocher+Beck UR Precision U440 butt splicer. Each roll loaded was scanned and became fully traceable throughout the process, interacting with the Cerm system in order to provide real-time production values. A Cerm inspection command was also sent to AVT’s automatic 100 percent print inspection system, which registered any defects during printing – but at this stage did not act on them.
A Matho EM-180 waste management system on the MPS press captured, cut, transported and collected the production waste into a waste disposal system, while cores for both presses were cut on a Wasberger WLE fully automatic core cutter following the specifications provided on the job ticket.
All finished rolls from both the Xeikon and MPS presses incorporated an ID barcode which, when scanned, enabled electronic instructions for the automatic set-up of cutting knives on a Grafotronic high-speed inspection slitter rewinder. An AVT camera automatically stopped the Grafotronic when a defect was detected so that a repair could take place. Final rolls were scanned into a warehouse location, a picking list prepared through the MIS, a delivery note printed, an email sent to the customer and invoicing launched.
Did the Automation Arena fulfil its promise of presenting the label plant of the future? Well, more than 1,000 visitors sat through demonstrations, there were over 250 media posts, and there were in excess of 1.26 million impressions on those posts. Participating suppliers were almost overwhelmed with the number of enquiries received from companies now looking to consider automating their operations. An undoubted key to the success of the Automation Arena was most certainly the collaboration between all the participating companies, managed in turn by the Cerm MIS.
In an era of ever decreasing run lengths, production bottlenecks, shorter lead and delivery times, multi-versions and variations, it seems certain that increasing automation of tomorrow’s label plants will become a necessity for successful performance and profitability. Hopefully the Automation Arena provided an important showcase of just what is now becoming feasible.
This article was first published in L&L issue 5, 2017, and is available here
Stay up to date
Subscribe to the free Label News newsletter and receive the latest content every week. We'll never share your email address.