Offset opportunity
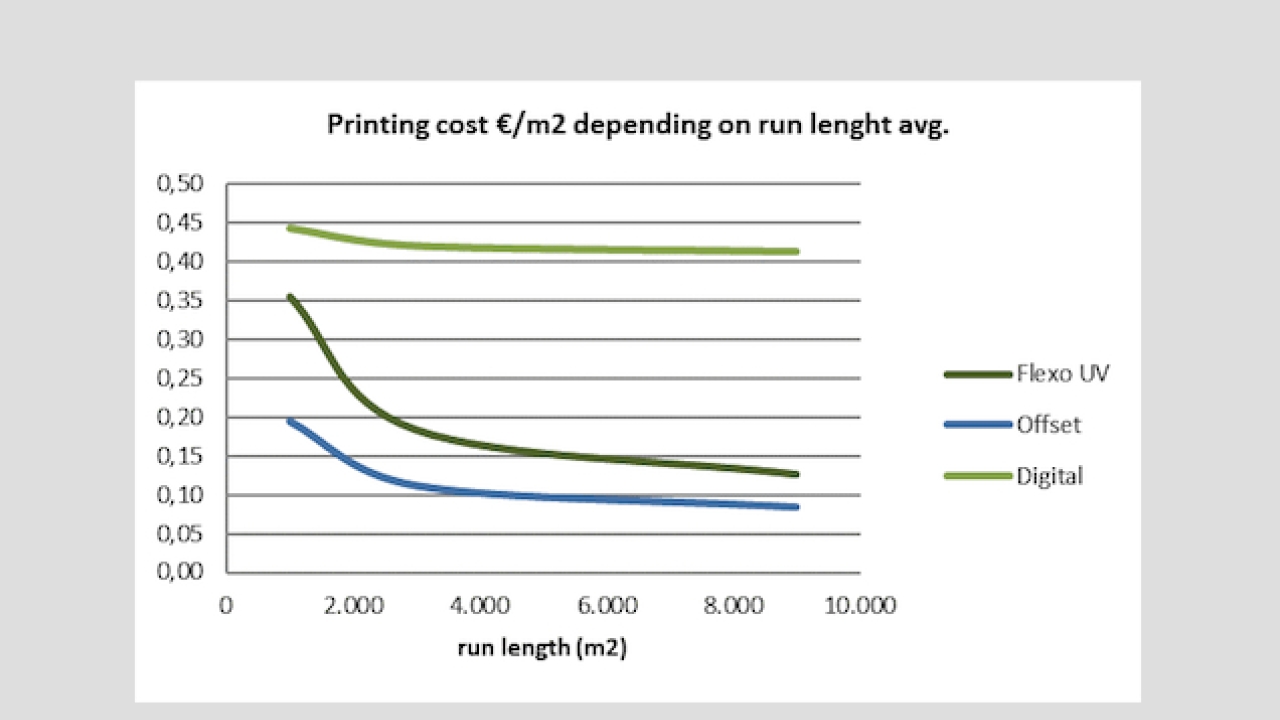
Labels and flexible packaging have similar demands and, on many occasions, provide services to the same customers, brand owners and distributors. Offset has long been at the forefront of print quality and has been used extensively for many years in the labeling industry for applications including shrink sleeves, in-mold (IML), wraparound and self-adhesive labels.
Comexi was the first press manufacturer to bring offset technology to the Central Impression (CI) drum format, and combining it with electron beam (EB) curing for flexible packaging and unsupported label film applications. The CI8 met a requirement for reduced flexible packaging run lengths and was able to handle the kinds of thinner and more extensible films now being specified by end users.
The CI configuration allows wider print widths and increased speed over in-line systems, and allows users to specify from a wide range of off-line finishing systems. Keeping finishing off-line allows the speed advantages of the CI format to be fully utilized along with fast job changeovers.
For converters who also run narrow web label presses, the CI8 press can be fitted with in-line slitting and rewinding, allowing the wider web to be slit down into narrow reels for finishing.
Clearly, a wider CI format will deliver greater speeds and sqm per hour than a narrower width in-line press.
But maximum productivity for shorter runs is best achieved by grouping orders in multiple printing SKUs.
Grouping different orders into a single, multiple SKU printing job is an extremely efficient way of turning many short run orders into an efficient longer print run. For example, combining five x 3,000sqm orders into a single print run of 15,000sqm not only means the print run is five times larger, but both change-over time and waste are also divided by five.
Offset is well-suited to multiple SKU printing due to its low plate costs, which makes for easy grouping, combining and varying of orders. Offset with central impression adds to these advantages by its tight register, even on the thinnest films, which allows the maximum benefits to be obtained from the extended gamut print process, which can be applied to both labels and flexible packaging.
Brand owner demands
A further advantage of CI lies in growing brand owner demands for recyclable flexible packaging, which are now favoring the use of polyethylene (PE+PE) materials. These films have a high degree of elasticity which the central drum impression format is specifically designed to handle.
The relevance of the lower pre-press costs for offset against UV flexo particularly impacts on short runs. The graph displays how the average printed sqm cost of UV flexo rises rapidly as the order becomes smaller, meaning the cost of the plate has to be amortized over multiple print run repetitions. Without these repetitions, the plate cost has a higher impact on the viability of shorter flexo print runs. Additionally, the graph shows a comparison of the total printing cost, depending on run length average, as well as operating costs (energy, labor, maintenance, etc), and consumables cost (materials, inks, plates, etc).
The difficulties faced by digital technologies in being competitive for both flexible packaging and labels include printing quality on a wide range of materials, particularly thinner films. Other limitations regarding this technology are the inks, since approximately 70 percent of all flexible packaging caters to food packaging. Migration tests are mandatory for food packaging, and the requirements can be severe depending on the final application.
Other drawbacks include the exponentially higher ink price, the costs of pre-coating which have to be applied to certain films, and the lower printing speed when 5-7 colors are used.
In this analysis, offset EB inks are more competitive, and approved for use with primary food flexible packaging. This scenario is compared with non-food flexo UV inks. UV low migration inks are higher in price, which makes it more difficult to incorporate them into flexible packaging cost structures.
Electron beam curing technology has sustainability benefits, using fully solvent-free inks at a lower energy consumption, lower ink waste, and less cleaning. Moreover, the capabilities of EB coating allow recyclable packaging systems to avoid the need for lamination. EB technology is a low migration technology which promotes the use of thinner labels and containers.
Taking all these factors into consideration, the advantages central drum offset printing are certainly worth considering.
Stay up to date
Subscribe to the free Label News newsletter and receive the latest content every week. We'll never share your email address.