Beiersdorf invests in Domino labeling technology
Skincare manufacturer Beiersdorf, whose brands include Nivea, Atrixo and Eucerin, has brought its re-packaging services in-house, following the installation of four Domino M-Series print and apply labelers.
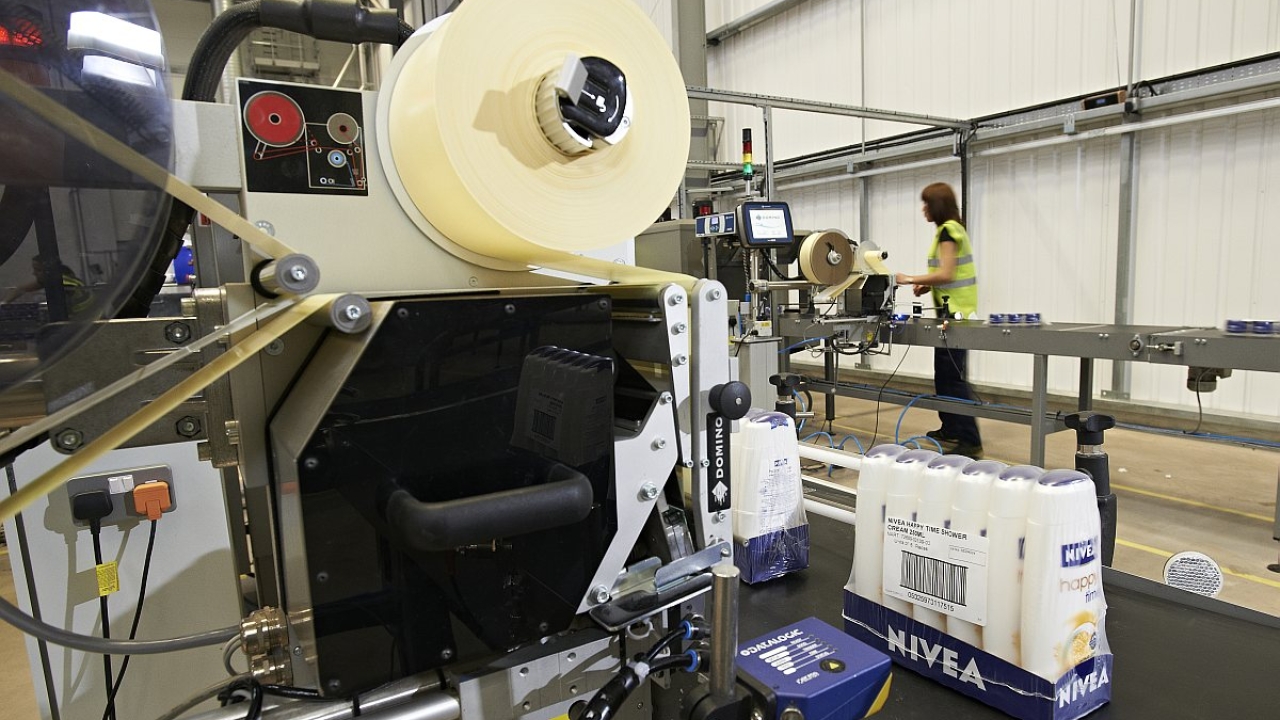
Beiersdorf UK invested in four M200 print and apply labelers for its new retail ready packaging (RRP) lines as part of an extension of its warehouse and logistics facility. As a result, the company has increased automation and operational cost savings, improved its environmental credentials as well as gained greater flexibility in responding to customer demands.
Part of the worldwide Beiersdorf Group, Beiersdorf UK handles the re-packaging of its global brands into shelf-ready containers for the British retail market.
The decision to invest in the Domino technology was taken by Mick Clipston, Beiersdorf's packaging technologist who has managed the program to bring RRP operations in-house. ‘Prior to this, we were outsourcing all our re-packaging, he said. ‘In terms of logistics and the associated costs alone, this just didn't make any sense. It required us to transport our goods from the warehouse to our contract packers, then back to the warehouse again, before being shipped off to their final destination.’
Following the extension of its new warehousing facility at Holford in the Midlands, Beiersdorf UK took the opportunity to address its logistical challenges. By bringing its RRP in house, the company was able to introduce a system that brought about cost savings and environmental credibility to its operation by reducing road traffic. Goods are now re-packaged, to the retailers' specifications, into smaller quantities of cardboard shelf-ready trays, before being shrink-wrapped and labeled prior to shipping to the supermarkets.
Clipston said: ‘Now that we're handling our own re-packaging on the premises, we've been able to reduce our logistics and transportation requirements. Not only does this represent a significant cost saving to the business, it has also enabled us to reduce our environmental impact in the process. In addition, the new M200 print and apply labelers have introduced a greater degree of automation to the process by both printing and applying the labels onto the packages. This has meant less manual intervention and greater production efficiencies.’
To print and apply the required labels, Clipston was looking for a technology that could print both high-resolution bar codes, text and graphics for supply chain compliance, and automatically apply the labels onto the outer cases of the re-packaged shrink-wrapped packaging.
The new M200 print and apply labelers are installed onto electronic height adjustable stands that receive the re-packaged goods on a conveyor directly from the shrink-wrap heat tunnel. The labelers print GS1 labels comprising date, product and batch identification data and barcodes that are scanned for improved traceability and supply chain management.
‘We reviewed a number of different print and apply solutions before opting for the Domino's M-Series,’ said Clipston. ‘The M200 models not only came in at the right price, but provided the production speeds we were looking for and could easily handle the different variable data requirements with excellent print clarity. We were also delighted with their ease of use, as our operators can simply change applications at the touch of a button, reducing downtime between jobs.’
Stay up to date
Subscribe to the free Label News newsletter and receive the latest content every week. We'll never share your email address.