Sappi to use rebuilt PM 2 for product development
Sappi has celebrated the successful conclusion of a project to rebuild its PM 2 papermaking machine at its Alfeld Mill, and said it will allow the company to continue to develop new products for the release liner, flexible packaging and label segments.
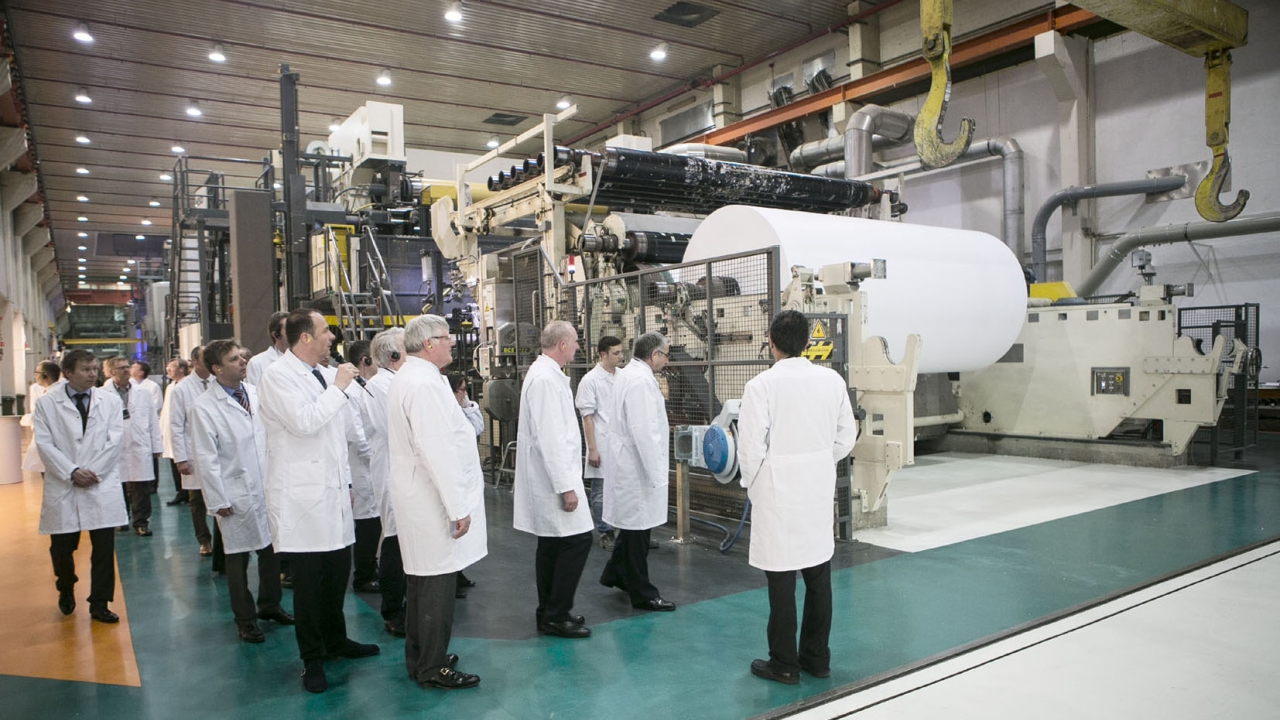
Sappi’s ambitious 60 million EUR transformation of Alfeld Mill’s PM 2 was concluded on schedule with the quality exceeding expectations, it said, and was celebrated with more than 200 customers, partners, officials and suppliers in attendance at an event on March 27.
Sappi said the project has created probably the largest, most innovative and versatile papermaking machine, which is producing one-sided coated specialty papers in-line.
The new papermaking machine delivers a very smooth top-side surface, greater dimension stability and lower penetration of pigments. This improves the overall quality of the grades manufactured on PM 2, enhancing their converting capabilities.
The transformation involved the use of Europe's largest crane to drop in place a 135-ton MG cylinder with a diameter of 6.5m. In addition to the new MG cylinder, rebuilding PM 2 also included installation of a new head box with dilution system and pre-dryer section as a single tier arrangement.
‘The entire project was completed in an extremely short time frame,’ said Dr Stefan Karrer, mill director at Sappi Alfeld GmbH. ‘We have already received very positive customer feedback on the high quality achieved, and we were excited to be unveiling the results to a larger audience at this celebratory event.’
Sappi Alfeld will continue to develop new products for the release liner, flexible packaging and label segments utilizing the new capabilities and capacity made available by the transformation of PM 2.
Rosemarie Asquino, sales and marketing director for specialty papers at Sappi Fine Paper Europe, added: ‘Among the first grades to be produced by the new machine were Fusion, Parade Prima, Algro Finess and Algro Sol. We have been able to achieve remarkable print results, top dimensional stability and excellent flatness which we know will help our customers achieve high quality results. The higher capacity guarantees customers paper availability in the future.’
Stay up to date
Subscribe to the free Label News newsletter and receive the latest content every week. We'll never share your email address.