Printed electronics revolution
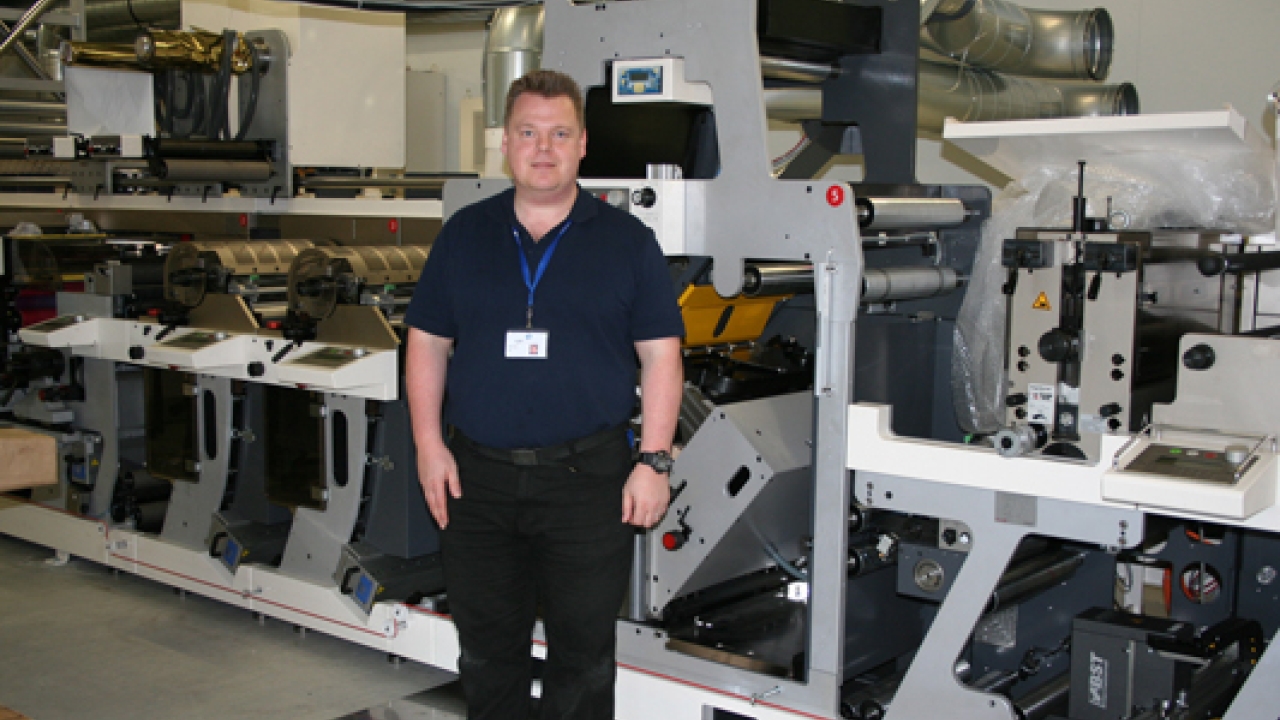
A technology innovation center in the UK is demonstrating how converters can create their own smart label operations using standard narrow web equipment. Andy Thomas reports
The Centre for Process Innovation (CPI) has installed a custom-built, multi-process narrow web Nilpeter as a test bed to develop printable electronics for a variety of applications including labels, cartons and flexible packaging. The press will form part of the Integrated Smart Systems line (ISS) which will enable electronic components to be integrated with printed circuits.
Although electronic circuits are already being printed on flexible webs, these are often located in dedicated and expensive clean room operations using bespoke equipment. The project at CPI aims to demonstrate that any label converter using commercially available equipment can be part of the Integrated Smart Systems supply chain through printing of conductive inks in a standard pressroom environment.
The Nilpeter press is a 16in wide machine specified to handle paper, cartonboard, films, foils and label stocks with thicknesses between 25-370 microns. The modular machine includes two MO4 offset units equipped with UV curing stations; two FA4 flexo units able to run water-based, solvent and UV inks; two screen units for UV inks; and a solvent gravure unit. The press operates in both reel-to-reel and reel-to-sheet modes, and can re-register from unit 1, allowing CPI to simulate larger presses with multiple print stations. Auxilliary processes include de-lam/re-lam, UV lamination, cold foil and die cutting/sheeting.
The process of manufacturing Integrated Smart Systems pieces starts with printing the label or carton's graphic elements, followed by printing 'large area' electronic circuits. After sheeting, the pieces are coated with conductive adhesive on a flatbed DEK screen press with a print accuracy of 10 microns. A commercially available pick & place unit used extensively in the electronics sector then positions miniature components - which might include chips, flexible displays, batteries or even tiny loudspeakers - onto the printed circuit tracks.
The sheets are cured in an oven to bond the components to the printed circuits, forming both a structural and electrical connection. As a final stage, the ISS sheets are converted into short runs of finished labels, flexible packaging or cartons. Finishing equipment includes an Esko Kongsberg i-XE 10 digital cutting table to cut & crease boxes and kiss cut labels. A Trotec CO2 laser handles fine cutting, engraving and ablation of circuits. The operation is also supported by CPI's wide range of sophisticated analysis equipment to measure material, ink and structural properties.
CPI team
Running the platform is ISS program manager Bela Green, supported by technical print manager Neil Porter. Porter draws on a wealth of narrow web print operator experience at leading converters including the Clondalkin Group (formerly Harlands Labels).
The CPI team is looking for partners from across the supply chain to take the ISS project forward, from brand owners and designers to suppliers of inspection equipment, substrates, inks and pre-press equipment. The ISS line at CPI is available for development work, prototyping, scale-up and pilot production. A key task will be assessing the performance of the conductive inks. 'We need to get total uniformity of ink coverage and no pin-holing or scratches on the printed surface if we are to achieve the required levels of conductivity,' says Neil Porter. 'So scuff and rub testing will be critically important, particularly when the label is on the applicator line. We will be evaluating print inspection systems to see if they are adequate to detect these kinds of flaws. It is more a question of uniform coating than high print resolutions. Another issue to be researched is how to clean conductive inks in each print process.'
If successful, the Integrated Smart Systems line at CPI could mark a watershed in the history of label production. For the first time, label converters of any size will be able to start up their own smart label operation, tapping into leading edge research into micro-electronics to create entirely new applications for designers and end users across the supply chain.
Pictured: CPI technical manager Neil Porter in front of the multi-process moduler Nilpeter press
Stay up to date
Subscribe to the free Label News newsletter and receive the latest content every week. We'll never share your email address.