Flexible dies face thin liner challenge
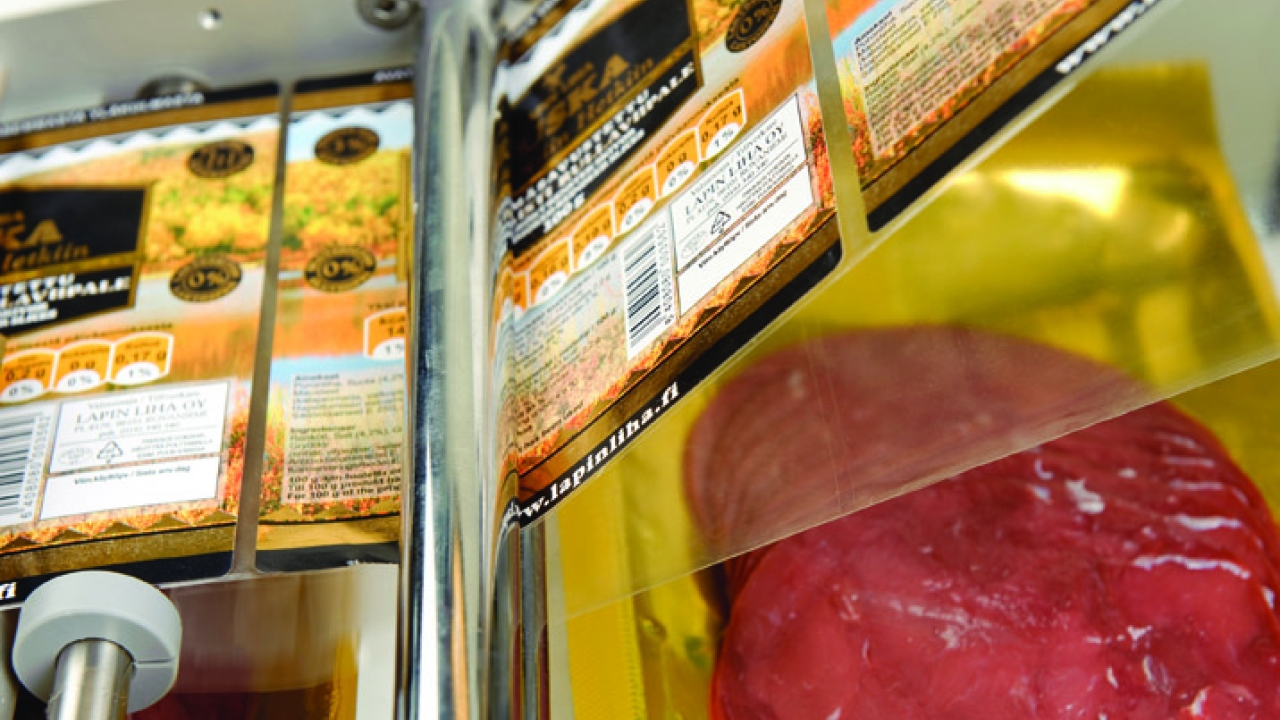
As filmic liners get thinner, die-cutting becomes a bigger challenge, as Herbert Knott at flexible die specialist Electro Optic explains
Under intense cost pressure, glassine liner material has been increasingly reduced in thickness, most recently from 0.065 mm to 0.045 mm. At the same time, speeds in the label processing chain are getting higher, both on press and the applicator line, leading to higher stress on the liner. Consequently the need for an intact liner has never been more important.
Problems have arisen where liner weight has been reduced while maintaining the dimension. The result is a higher compressibility of the liner which raises substantial problems when cutting plastic materials. Furthermore, glassine liners show height differences of 10µ and more, so cutting problems seem inevitable.
Therefore film liners with tolerances of just a few microns, mostly PET/PP, are increasingly being used, especially for film label materials.
But improved stability during the application process is often bought at a high price. Here also, the drive for cost efficiency has meant a reduction in the thickness of the liner (and often the face material), which reduces cost and means more labels on the roll. As a consequence, PET liner thickness has been reduced from 50-55µm to only 30-31µm. Another trend sees liners going to 23µ-20, and there are currently tests with 17µ and 12µ liners. Cost saving, yes! But often at the cost of ignoring the basics of die cutting technology.
How die cutting works
Die cutting in label printing is not cutting in a traditional sense. This is a ‘pressure cut’, which means separating the material by compressing it until it bursts, or is divided. Hard materials, such as polyester, polypropylene or paper, burst. A compression rate through the pressure of the die-cut line of up to 65–70 percent of the material volume leads to a relatively sudden fracture of the substrate.
With soft and soft-tough materials such as PE and PVC, the cutting process is significantly different. Under pressure from the cutting line, the material parts to the side, so a clear compaction process as with paper does not take place. The result: the die line needs to penetrate the liner material much further to achieve the separation of the upper material. The die manufacturer, therefore needs to raise the cutting line a little bit, adapting the cutting angle and the mirror width of the cutting line until it works fine with these requirements. But now the very thin PET liner with a thickness of 30µm or 23µm, comes into play.
Where is the problem?
One could argue that with the flexible die manufactured slightly higher, or where a variable anvil cylinder can be slightly adjusted, the cutting result is as good as with a ‘normal’ PET liner.
Unfortunately, not always. Nothing can be manufactured without tolerances, and there are many variables involved in the die cutting process: upper and lower material, magnetic cylinders, flexible die, anvil cylinder, possibly substructure of the anvil cylinder and the draw rolls. Additionally, the bearings of the magnetic cylinders, the anvil cylinder and their substructure as well as the general stability and stiffness of the cutting unit, are all things to take account of.
And in practice, not only brand-new components are in use. Magnetic cylinder concentricity of 10µm is not uncommon, and out-of-roundness or worn anvil cylinders alter significantly the magnetic cylinder gap of 0.480 mm. If the flexible die then shows height differences between five to 10µm, there is a problem. The reduced dimensions of the 23µm and 18µm PET liner do not ‘forgive’ such deviations like a 30µm liner does.
Tailor made
Basic requirements for label production on thin PET liners are magnetic cylinder and anvil cylinders with 3µm run out accuracy. An anvil cylinder without support rollers also minimizes a build up of errors. Adjustable units must be in absolute mint condition to keep the tolerances. When dimensioning, the 1:1 rule should be respected: The circumference of the magnetic cylinder as well as the anvil cylinder must reach at least the maximum working width of the press. The die lines must be sharpened with a flank angle of 40-75 degrees and tailor-made to the softness, lamination or lay-up properties of the material being cut. They need to be manufactured with the best possible cutting ability at the top of the blade. In addition, a die height tolerance of ± 2µ is a must.
There will be success for the label printer in the use of thin PET liners only when all these die-cut preconditions are optimized.
About the author
Herbert Knott is sales and service manager at Electro Optic. The company’s Gold Line Special Quality dies are machined using the back grinding process to meet the challenge of ultra-thin liners, while the Dura Line Special-C has a resistant back ion coating DLS-C for long life requirements
Pictured: Thinner liners present new challenges for die cutting systems
This article was published in L&L issue 6, 2011
Stay up to date
Subscribe to the free Label News newsletter and receive the latest content every week. We'll never share your email address.