MPS invests in Bobst Novacut
Multi Packaging Solutions (MPS) has invested in Bobst die-cutting equipment to meet the increasingly demanding requirements to serve the pharmaceutical market.
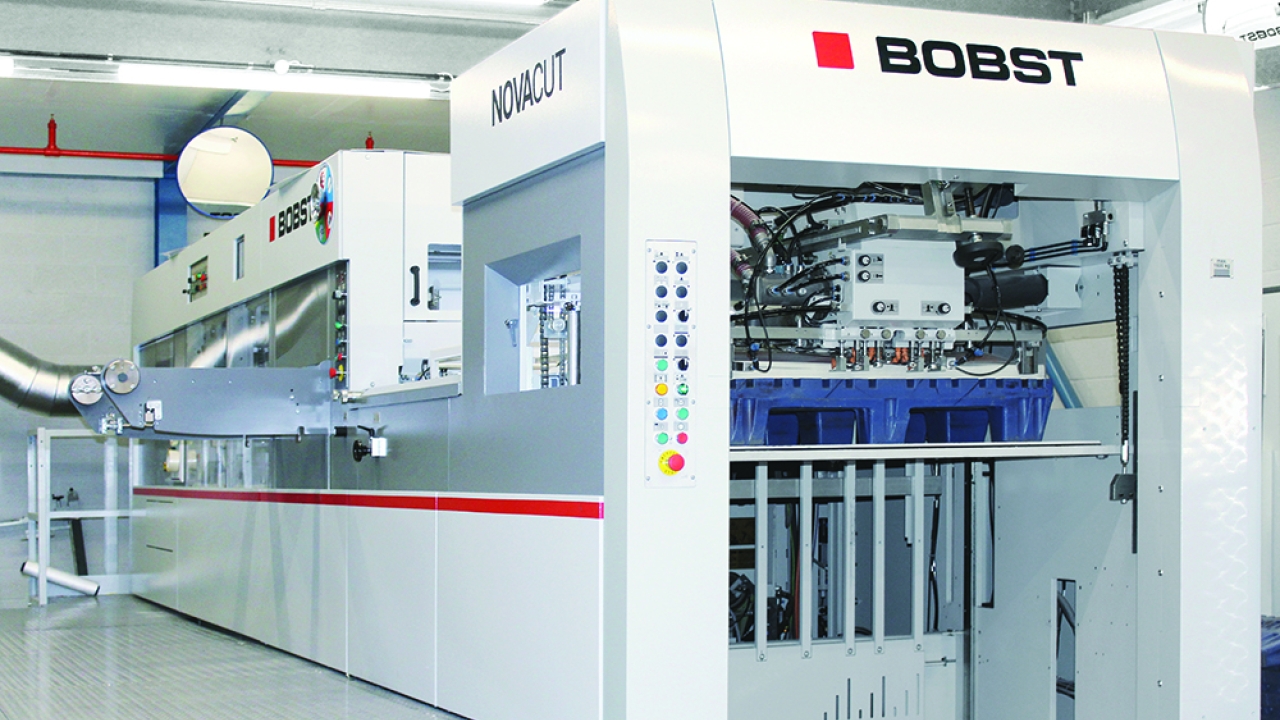
The MPS plant in Leicester, UK has installed a Bobst Novacut 106 ER Autoplaten die-cutter as part of a print de-risking strategy.
MPS Leicester designs and prints folding cartons, labels, inserts and rigid packaging for the branded and healthcare market sectors. As such, it places great emphasis on accuracy, security and staying ahead of the counterfeiting market.
Mark White, operations director at MPS Leicester, said: ‘Packaging converters face great challenges when supplying the complex and fast-moving healthcare sector and the risk of getting it wrong can be high. Pharmaceutical packaging is becoming more complex and increasingly consists of shorter runs with additional functionality, graphic or tactile effects, as well as new legislative requirements.
‘This is making the printer’s job more demanding, so we need our technology to meet these emerging needs. The Bobst Novacut 106 ER machine is therefore critical to our operation, minimizing make-readies and driving efficiency.’
The recently installed machine drives flatter, more consistent blanks straight into the finishing process. It has removed the need for hand stripping and blanking for all but the smallest jobs. As well as de-risking, this drives productivity and has significantly increased the number of jobs that can be run at full speed.
Craig McGowan, Bobst area sales manager, added: ‘At MPS we see a machine running at the speeds promised, being used for large format as well as short-run jobs down to less than 1000 sheets, and still achieving set-up times of around 30 minutes. This means the Novacut is in continuous use and adding 5-10,000 additional cartons per hour to the gluing lines – enabling great service for the shorter run, higher frequency demands from customers.’
White concluded: ‘Our expertise and in-depth understanding of our customers’ needs, from speed of turnaround to security, traceability, specific pack data and information requirements, allows us to make continuous operational improvement. We are committed to investing in future-proofing our production and ensuring 100 percent compliance at all times, and the systems and technology we have in place at Leicester, with scanning capability on every station, ensure we are going the extra mile to de-risk our business.’
Read more about challenges and opportunities in the pharmaceutical market in L&L issue 5, 2017, and here
Stay up to date
Subscribe to the free Label News newsletter and receive the latest content every week. We'll never share your email address.