Pipi Print & Packaging takes press package from Prepress UK
Pipi Print & Packaging, a Leicester, UK-based packaging specialist, has employed the pre-press knowledge and press know-how of the team at Prepress UK as it focuses on color quality and consistency from its pair of B2 Heidelberg sheet-fed presses.
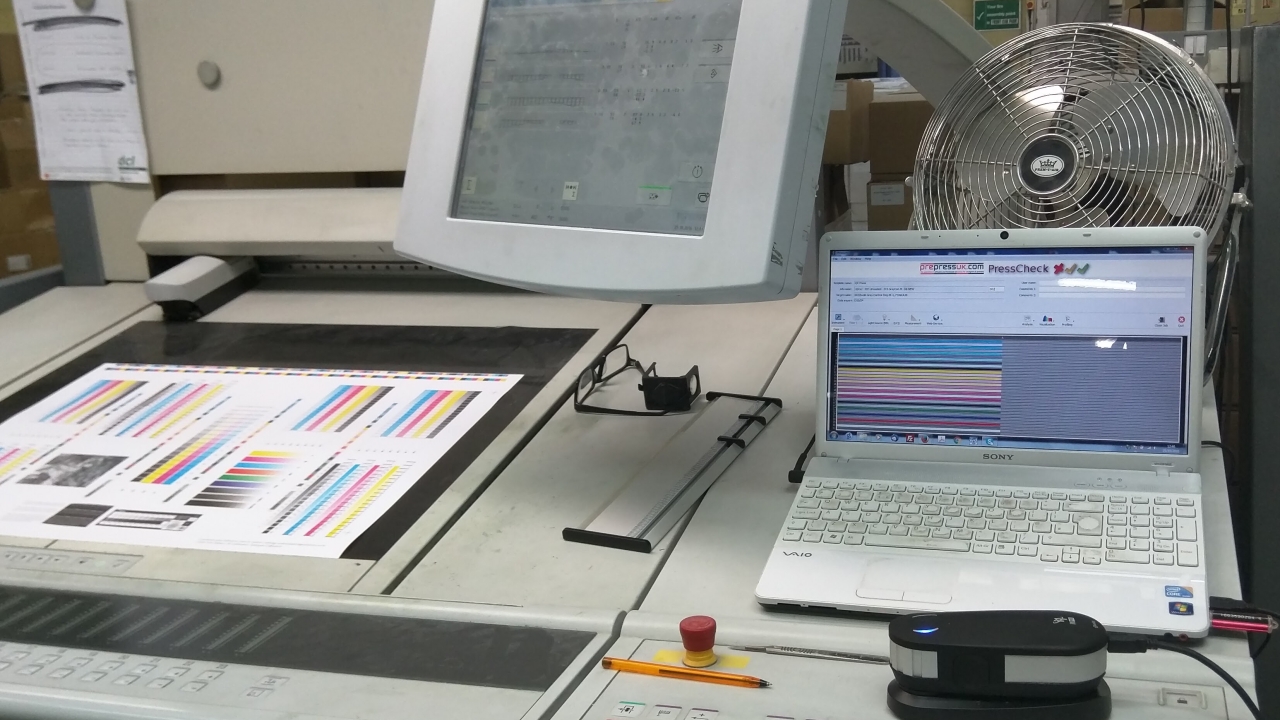
Pipi Print & Packaging is a second-generation family business that was established in 1982 with the aim to become a comprehensive provider of high quality print and packaging solutions at affordable prices. The original investment in one printing press paid dividends swiftly, leading to further investment equipment for carton manufacture, as well as narrow web label printing and decorative print finishing.
Raj Palmer, managing director of Pipi Print & Packaging, added: ‘We are producing packaging product for the pharmaceutical and cosmetics markets, where quality and consistency are critical. It was important for us to be getting the very best out of our litho presses. In addition to that, print runs are relatively short when running multiple images to view on a B2 sheet. That means that job changeover and make-ready times have become ever more critical in ensuring both profitability and efficiency of production.’
Pipi Print & Packaging runs two Heidelberg B2 format presses – a CD74 with image control and an SM74 with axis control. The company was seeking to improve its color accuracy and consistency, as well as improve make-ready times when moving from job to job, and contacted Prepress UK after a recommendation from its press engineer.
Nic Chapman, Prepress UK director, explained: ‘We were able to put together a package of products and services to enable Pipi Print & Packaging to get the best from its presses, improving color reproduction, reducing make-ready times and costs, and improving repeatability, color consistency, and general on-press performance.’
‘The package provided by Prepress UK focused on both of these important areas,’ continued Chapman. ‘We have been very impressed with the results. I would have no hesitation in recommending their services to other printers seeking to find similar improvements.’
Both the image control and axis control packages were not performing as effectively as they should have been, with the manufacturer’s quote for repair of the two color stations ‘prohibitively high’.
Detailing the work undertaken, Chapman said: ‘The package consisted of a press health check and a training package put together by our Heidelberg press demonstrator, including repair and servicing of the on-press color measuring devices. We then added our PressProfiler ink-key presetting system, and included our dot gain calibration service.
‘We began with service work on the presses as the first priority. This helped us to ensure that both presses were printing to a consistently high quality. In practical terms, it meant that we could be confident of the print stability across the sheet and for the duration of the print run. This was followed by a visit from our Heidelberg technician to repair both of the color scanning devices on presses, at a fraction of the cost that Heidelberg had quoted. They were repaired and calibrated and the press operators trained on the correct use of these important measuring tools.’
The combination of PressProfiler, which examines digital files received from any workflow and generates ink-key presetting data, and the scanning stations helps to minimize make-ready time and wastage, and goes on to maintain consistent color throughout the print run. Pipi Print & Packaging already estimates improvements of at least 20 percent in make-ready times thanks to the new package.
Chapman continued: ‘Once the presses were stable, test print runs were performed on both presses to establish the correct ink weights to achieve target solid ink color, followed by dot gain measurement and adjustment to match tone value targets. These enhancements have maximized compliance with the ISO 12647-2 standard.’
Stay up to date
Subscribe to the free Label News newsletter and receive the latest content every week. We'll never share your email address.