Alufoil blister packs: 50 years of service
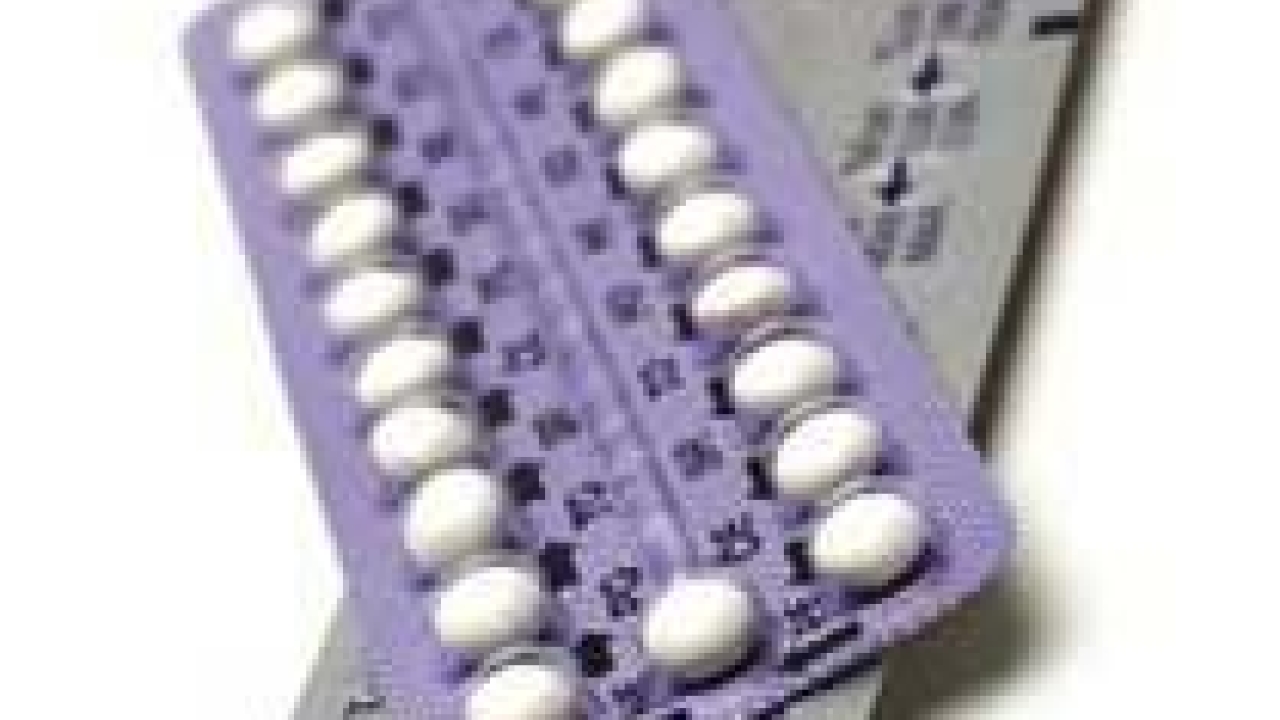
The European Aluminium Foil Association celebrates the 50th anniversary of aluminum foil blister packaging
The first blister pack was introduced to the market 50 years ago. Today it is hard to imagine a world where unit doses of solid form pharmaceuticals are not available in this user-friendly format.
So many advantages for the end-user have emerged and its most obvious benefit is that it is always clear how many tablets have been used.
However the first style of pack to incorporate a cavity and lid was designed for food containers not pharmaceuticals. It took a clear vision of its potential to create the blister packs we know today and to raise the bar on both form and functionality.
New materials and modern engineering have enabled this dynamic form of packaging to become an indispensable part of life; easy to carry; available in a wide range of shapes, sizes and formats; simple to print on and brand; and of course a very secure and protective pack.
The start
But the birth of the blister was far from simple. Indeed it came about because of the need for birth control. When Schering (today Bayer) developed the first birth control pill it needed a pack to aid patient compliance and make it simple to control administered doses over a set time period. The solution came from Hassia, a leading manufacturer of packaging lines, in the early 1960s.
Blister packs had become possible thanks to the development of PVC and later copolymer, which had good thermoforming capabilities. However a vital component was the development of tempered alufoil, known as Springfolie, as a lidding material for the “push through” pack, rigid enough, yet maintaining good adhesion by coating it with special lacquers.
The first machines were quite slow but quickly were able to produce over 400 blisters per minute. Modern machines can run at up to 1,200 blisters per minute. Alufoil’s tensile strength, high sealing integrity and excellent adhesion has enabled these speeds to be achieved. The new blister packs saved more than 60 percent in materials compared with traditional packs, while flat packs were easier to store and took up less space. These features were initially recognized for cost savings, not sustainability issues, but certainly score highly today in that respect.
Two forms of blister packs for pills have evolved. The most common form is the combination of a plastic thermoformed sheet used to make the cavity and, for “push-through” blisters, a sheet of 20μm rigid aluminum foil laminate providing the lidding layer.
Next-generation blisters
The next generation of blisters saw alufoil prove its exceptional value with the development of the coldform or alu/alu blister. No other flexible packaging material can match the all alufoil blister to protect against humidity and gases. So the coldform is ideal for sensitive products and provides a high value image.
A typical alu/alu blister uses 45μm foil laminate for the coldform blister layer and 20μm for the lid. As regulatory and legislative requirements led to demands for greater security both the plastic and alufoil layers developed considerably.
Demands for more child resistant blister packs led to new, stronger alufoil laminates being invented to make the format even safer. Combinations using both soft and hard alufoil from 30μm to 7μm, in combination with a paper laminate, attached to a thermoformed PVC between 250 and 300μm, have added considerably to blister security.
In addition the packs can carry printed information on the alufoil lid to depict the dosing schedule or other important instructions.
Manufacturers
Today’s leading manufacturers of blister foil in Europe are Amcor Flexibles, Aluberg, Ariflex, Carcano Antonio, Constantia Flexibles and Hydro.
Accessibility and convenience for many types of pharmaceutical products has been achieved because of the blister.
In 50 years the format has evolved into an indispensable packaging product and found new applications, even for its original use with foods, such as confectionery and chewing gum.
Read more PPW features here
Read more on packaging substrates here
Read more on foils here
Stay up to date
Subscribe to the free Label News newsletter and receive the latest content every week. We'll never share your email address.