Creativity and efficiency drive Signode India
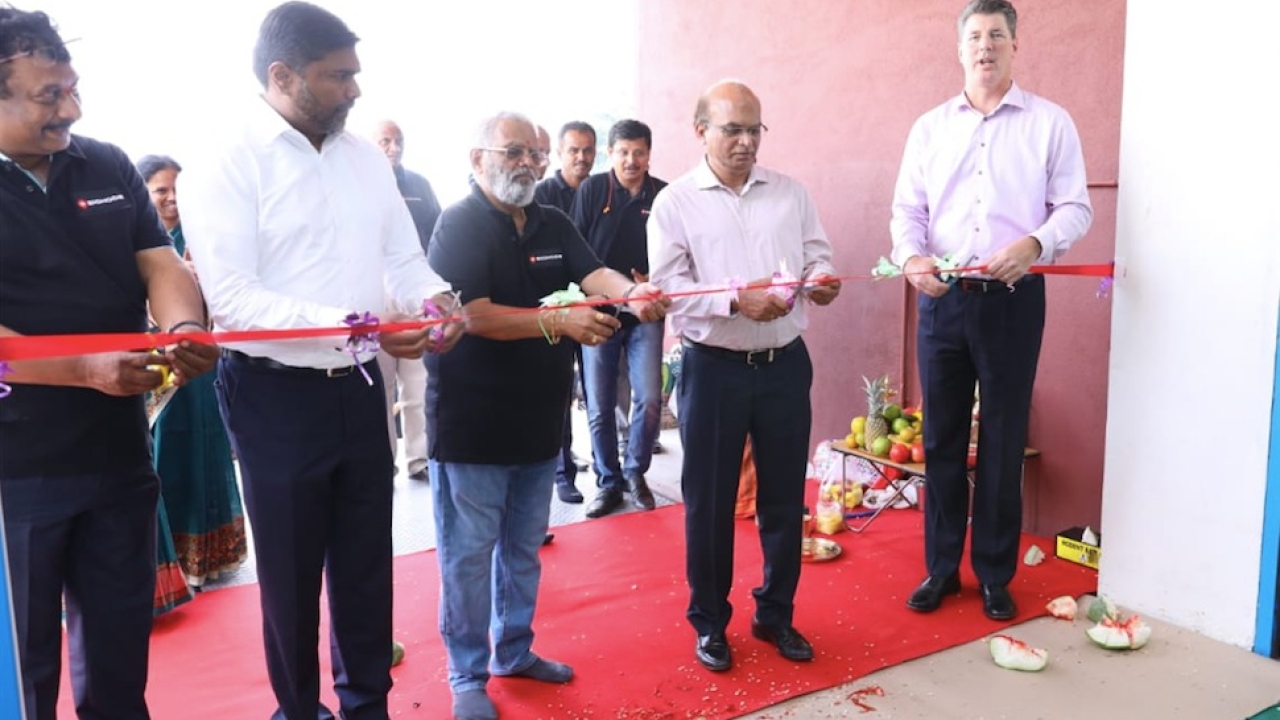
The label printing division of the company, Signode India Wintek Flexo unit, witnessed growth of around 9 percent in the last year.
Lakshminarayanan Parthasarthy, business unit head, Signode India Wintek Flexo Prints, says: ‘Our growth is driven by producing consistently high-quality labels, innovation and improved efficiency. The company will continue to grow in the same direction as the market and is widening its product portfolio to include premium security labels and performance labels for durables.
‘We are evaluating further diversification to include in-mold labels and shrink sleeves as well as short run promotional jobs for beverage companies. Building on our expertise in new product segments, we would ideally like to take high-value, profitable jobs that stand out on the market shelf.’
Story
The company fulfils the premium label requirements of multinational companies primarily in the personal care, FMCG, and pharmaceutical segments. Innovations at Signode India include feature-laden security labels, domed labels, registered lens, cast and cure, three-layer booklet labels, and augmented reality, among others. ‘Every brand has a story and we want to be a median to narrate the story through augmented reality,’ explains Parthasarthy. Augmented reality is a technology that superimposes a computer-generated image or a code in microtext onto a label, that when scanned makes a label come to life engaging the consumer with the brand.
‘Signode India is a solution provider and strives to offer cost-effective, yet high quality labels to customers,’ says Parthasarthy. Citing an example, he says that the company aims to increase its market share by printing labels for cans, and recently converted a direct printed tube to high-value pressure-sensitive labels. With highly configured Gallus presses, which feature in-line screen, foiling and a gravure unit among other options, Signode India offers many innovations such as the option of cost-effective labels printed with solvent-based metallic ink instead of foil.
‘The Gallus presses perform extremely well,’ says Parthsarthy. ‘With multiple Gallus presses spread across two plants, we are extremely happy with the service support and the convenience of using tools interchangeably. This not only reduces costs but also saves time and increases efficiency on production floor.’
The company’s label division operates in Bengaluru and Rudrapur. ‘We keep adding capacity to meet market demand and continue to have excess capacity to allow us to meet that demand, with a planned roadmap to get into the right market segments,’ says Parthasarthy.
Factors that drive the company to invest in a new press include optimum equipment efficiency of its existing presses and the need to bring new technology in-house.
Gauging demand by end-users, Signode India has also been manufacturing label applicators since 2017 to further diversify its business. The company either offers applicators on lease to brand owners, while managing the equipment during that time, or sells them in a package which includes after-sale service.
One of the company’s major strengths is its in-house capabilities: pre-press, platemaking, screen-making, printing and finishing, amongst other operations to ensure end-to-end data and product security for customers.
Signode India houses high-speed inspection rewinders with 100 percent defect detection systems. Pre-press includes a fully-fledged Esko suite, DuPont systems for platemaking and an Epson printer for artwork approval. It also houses a 3D virtual studio from Esko as well as color management software integrated on all presses. The company’s ink kitchen is equipped with an ink mixing unit from Inkmaker where pantone shades are made in-house for various jobs. Some of the array of ancillary equipment used includes plate and anilox cleaning machines, and platemounting units. There is storage space for raw material and finished goods, in a factory which operates highly streamlined production.
Sustainability
The new facility boasts an effluent treatment plant, sewage treatment plant and six rainwater harvesting pits. The company uses recycled water in its gardens and bathrooms. The treatment plant ensures the removal of toxins from wastewater before its discharged in the drain. Signode has even ensured the hot air emission from its machines is split in two different directions, to control temperature build-up in any one part of the factory.
On the production floor, Parthasarthy says the company ensures high efficiency with careful evaluation of waste. ‘We perform a weekly analysis of production schedules that brings down running wastages. A team dedicated to job changeovers has reduced this time by 10 to 12 percent. Our key focus in 2020 is to increase optimum equipment efficiency (OEE) and further reduce wastage by two to three percent, which we believe will help us competitively serve our customers.’
The company has in-house targets for sustainability. Working towards achieving the goal, Signode India converts and upcycles all its waste and where possible tries to use FSC-certified material, as well as substrates made out of post-consumer recycled (PCR) waste. ‘We have efficiently converted a 23 micron PCR film with a 23 micron liner. Tension control and die-cutting are two critical aspects of printing on similar substrates. Our customers successfully use these films on PCR cans and other packaging, therefore making the entire package viable for recycling,’ explains Parthasarthy.
The new plant in Bengaluru transports all its waste, both liner and matrix, every week to the Silvassa or Rudrapur plant for upcycling it to manufacture corner protection boards for protective packaging of goods including electrical appliances. ‘Signode India Wintex Flexo Prints has been consuming 100 percent of its waste since 2014,’ says Parthasarthy. ‘We are now trying to engage with end-users to find a solution to recycle liner waste.’
Despite these efforts, the ongoing slowdown in the economy has driven the company to cater to wide gamut of companies and change its business model. ‘The industry has slowed down, as a result of various factors, and it is worrying. Rural purchasing power has reduced and many local brands have come up, which has reduced the market share of multinational companies, in turn affecting our business. Therefore, we have to look at mid- to short-run jobs while being efficient. With both flexo and intermittent offset press capabilities, we can efficiently produce any run length starting from 2,000sqm on Gallus presses and 1,000sqm on the Iwasaki TR2. Therefore, we are ready to cater to all brands and companies with low and mid-sized volumes,’ concludes Parthasarthy.
Stay up to date
Subscribe to the free Label News newsletter and receive the latest content every week. We'll never share your email address.