Eliminating waste from liners
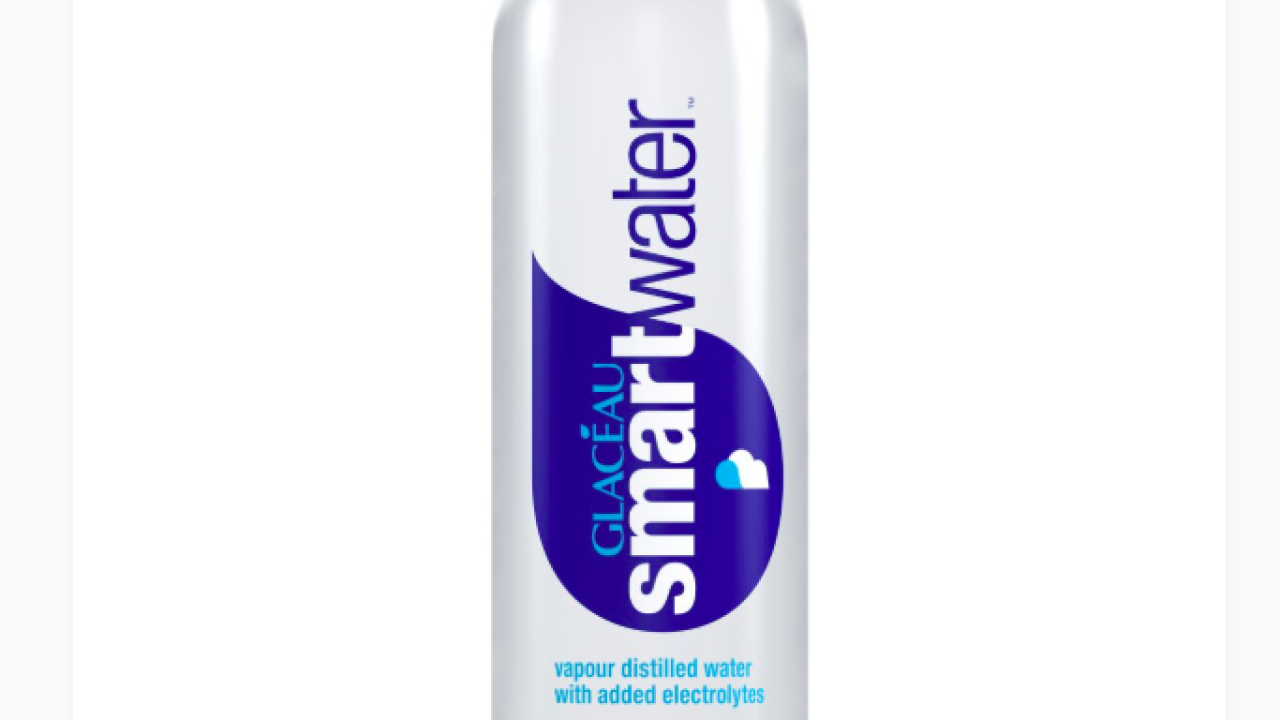
Juha Virmavirta, RafCycle Solutions director at UPM Raflatac, identifies 20-plus percent growth each year in the volume of release liner recycled through the company’s RafCycle program. This he attributes to the supply chain pushing such tools alongside the growing appetite of consumers and brand owners for sustainable options.
‘We clearly see a consistent trend towards stronger, but lighter weight, less resource-hungry solutions and more use of recyclable and renewable materials,’ says Georg Müller-Hof, vice president marketing at Avery Dennison.
Frost’s colleague Cindy White, CEO at Channeled Resources, notes however that release liner recycling is still a subdued topic. ‘Companies want to be sustainable but they also don’t want to spend extra money if that is what it takes to be sustainable.’ Virmavirta agrees, saying there is still a lot of work to do with a large amount of label industry waste being incinerated or going to landfill.
Müller-Hof identifies 60 percent of waste across the label industry value stream created during manufacturing and converting, including 20 percent in converting. Moreover, once the end user applies labels to the final product, nearly half of what they receive from the converter is waste. ‘The majority of that is the liner.’
He continues: ‘The product goes to the consumer, maybe to landfill, and so we concern ourselves with how our labelstock affects the ability of the product to be recycled. The bigger concern at this stage, though, is the liner waste generated during the labeling of the product itself. One of the most important challenges that our industry faces today is how to manage that liner waste in a productive way.’
Viable
To help make release liner recycling a more viable proposition, programs such as RafCycle exist and are being enhanced.
‘At the moment the main challenge is the collection of the materials,’ says Müller-Hof. ‘The liners cannot be “contaminated” with cores, labels and adhesives, and other waste. This means that training is needed on how to segregate the liners from the “normal” waste steam. Technology innovations could also help address this challenge.’
White sees large generators across America collecting truckloads and sending them to paper mills for recycling. ‘The problem is the companies that generate less than truckload quantities.’
Virmavirta says the cost structure needs to be analyzed in each situation, as it is a ‘function of volume, frequency and transportation distance.
‘Logistics play a critical role. We are developing logistic solutions in different markets and partnering with logistics companies to make the process more efficient and as easy as possible. With some partners, we ask if the volume is justified. If so, then we collaborate directly with the brand owners on collection and transportation for recycling. Where the volumes are smaller and more frequent, then deliveries of spent liner are required.’
Future developments
Today, pressure-sensitive manufacturers can access a number of industry-specific programs for recycling and reuse of spent release liner, says Müller-Hof. ‘But, we are convinced there is a shared responsibility for the industry as a whole to find an all-encompassing solution, rather than have individual companies striving for fixes in isolation. On top of liner recycling the industry needs also to address matrix waste.’
The European Union will also soon make a decision on renaming ‘waste’ to ‘bi-products’, which Müller-Hof explains will affect recycling as it could open up the possibility to transport more freely the materials intended to be recycled.
Virmavirta sees PET-based and filmic release liners as a key future development. ‘The volume of PET liner is growing, although still modest and not yet established from the recycling point of view. We welcome more collaboration between material suppliers, brand owners and plastic recyclers to establish a reliable recycling solution for PET liners.’
A previous example of PET liner recycling in action saw Avery Dennison collaborate with Viridor and PET UK to help Coca-Cola European Partners reduce waste, costs and the carbon footprint of SmartWater production in the UK through recycling tonnes of PET waste into a material suitable for making new items such as PET staple fiber, strapping or thermoformable sheets.
Stay up to date
Subscribe to the free Label News newsletter and receive the latest content every week. We'll never share your email address.