The finish line
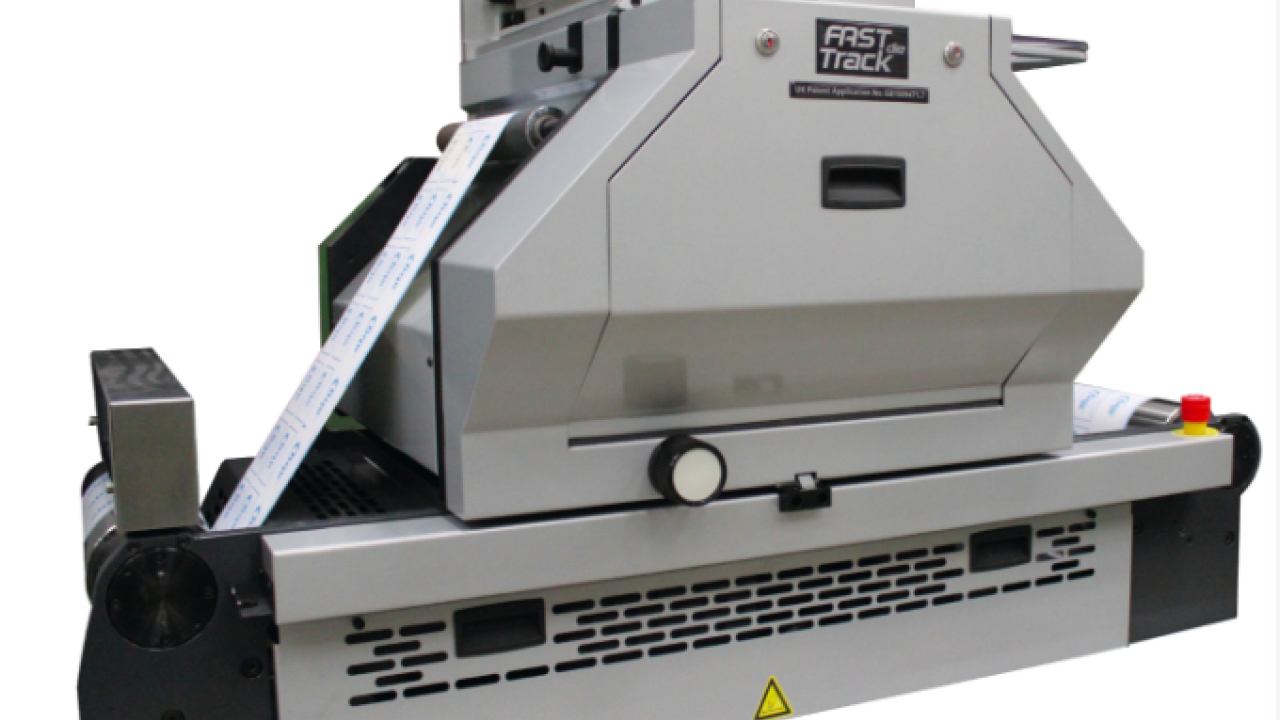
Morten Toksværd, global sales manager at Grafisk Maskinfabrik (GM), says: ‘Converters need constant improvements in the performance and flexibility of their finishing equipment.’
Dietmar Fritz, sales director at Dienes, comments: ‘Industry trends in printing and converting are increasingly moving towards automation, higher speeds, narrower cutting widths and faster format changes.’
Needs
‘Fully automatic production is designed to increase productivity, improve quality and avoid machine downtimes,’ continues Fritz. ‘Today, a modern slitting and scoring system should be designed as a fully automatic slitting system, because every manual intervention has a negative effect on the production speed and production costs, and ultimately determines the price of the end product. This system is able to change cutting widths within seconds, and thanks to a simple job administration the different formats can be called up quickly at any time. Knife holders and knives must be ideally adapted to the materials to be cut. In our in-house slitting laboratory, Dienes determines the optimum combination of knife and knife holder for each customer product.’
Grafotronic’s customers are similarly looking for machines with a strong focus on automation and high speeds, ‘which is of course all about increasing the efficiency, uptime and cutting downtimes to a minimum,’ comments Mattias Malmquist, the company’s vice president of sales and marketing.
GigaFast is a semi-rotary die-cutting module from Grafotronic for finishing digitally printed labels that can reach a speed of 160m/min. AB Graphic’s Fast Track semi-rotary die can run at speeds of up to 150m/min and be coupled with the Auto Set SGTR glueless turret rewinder to allow labels to be finished onto smaller cores without having to go through another process.
Tony Bell, sales director at AB Graphic, reiterates: ‘Speed is becoming important, and we have been addressing this in our recent innovations, such as the Fast Track die, new screen unit and inter-label gap sensors on our Autoslit scissor slitting module. We also need to handle different and complex substrates, but more importantly our machines need to be capable of producing different and complex finished constructions, such as booklet labels.’
Lemorau CEO Pedro Teixiera sees the main characteristics required of die-cutting units as semi-rotary and rotary mode in register for short and long runs, as well as turret rewinding, lamination and varnishing.
Labeltech owner Gabriele D'Onofrio identifies that the market is moving toward short runs and printers are answering with digital printing equipment, meaning their main need is fast changeover with less waste as possible, both in terms of time and material.
He continues: ‘The most demanded characteristic is quick and precise job set-up and big versatility. Another important feature is the workflow integration of the machine in the production process.’
Equipment designed for digitally printed labels, such as Digital Galaxie and E-Cut Generation III, represent 50 percent of Smag Graphique’s turnover. This has seen the company focus on optimizing the development of its new generation of finishing equipment to match high speed requirements, and offer increased workflow connection. E-Cut Generation III is available in 330mm and 530mm web widths to meet digital printing equipment standards and to double the die-cutting speed of the previous generation E-Cut S330, reaching up to 70m/min. Additionally, Smag has extended its collaboration with the main press manufacturers to propose finishing customization capabilities as standalone or integrated in-line hybrid systems.
‘We see a growing trend towards digital printing and the need for high end finishing solutions,’ confirms Malmquist.
AB Graphic sees finishing, excluding laser, as an analog process and historically being slower to set-up than digital. Bell says: ‘Our goal is to digitalize as many operations as possible, maximize efficiencies and reduce down times. There is a trend that digital run lengths are getting longer, so not only are we providing quicker set-up times, we’re having to provide faster line speeds, coupled with non-stop rewinding. We’ve done this by incorporating our turret technology into our digital finishing lines.’
Teixeira sees more instances of integration of digital printing on finishing machines, as evidenced by his company’s DIGIEBR+ that can, in one pass, print with water-based or UV inkjet, coat, die-cut and rewind.
‘After printing on a digital press, with our finishing line customers can coat labels with varnish or laminate, can add one color more or sport varnish on the flexo unit, and cold foil. Adding a primer onto the substrate before printing on a digital machine could be possible too.’
Modularity
Jannik Müller, product manager at Herzog+Heyman, says: ‘The industry requires products which give them a lot of flexibility to cover more than one specific job. Also, it’s necessary to shorten set-up times and take care of untrained operators. In times of job sharing and job rotation, simplicity is a big topic for us as a machine building company. The machine should be quick and easy to handle.
‘To cover all those points is a tough challenge in matters of quality. The size and formats of substrates, and therefore the machines, mean it’s a different story from customer to customer. The request range of machine and product widths is 16-31.5in.’
As evidenced at Labelexpo Europe 2017, manufacturers of finishing equipment are largely using a modular machine construction to allow printers to maximize the use of their finishing hardware, as D’Onofrio explains: ‘As the modern machine concept is based on modularity, customers will be able to add other features anytime they will be asked for.’
Labeltech’s Stelvio machine can be configured with semi-rotary die-cutting, gap master, varnish, sheeter, inspection, automatic slitter positioning, score and groove cut, and more.
GigaFast is available as a module for Grafotronic’s fully modular DCL2 finishing line, and is available as a retrofit option. Other modules now available for DCL2 include: a laser cutting module, powered by Spartanics; non-stop modules, such as knife positioning systems that set-up the knives in 10 seconds and semi- or fully automatic turrets; printing and lamination module, with several print stations together with a lamination in register for producing multi-layer labels; and a booklet production module that is powered by a Longford feeder.
Smag’s Digital Galaxie Generation III is a modular platform featuring options such as flexo, high speed flatbed screen, high speed flatbed foil and embossing, and laser and semi-rotary die-cutting. E-Cut Generation is similarly built on a modular platform and is pre-equipped to receive additional features such as web treatment, inkjet printing, inspection, laser die-cutting, sheeting and more.
MEBR+ is a modular finishing machine from Lemorau that can be configured with several options and modules. All of GM’s machines are modular and flexible, while DPR offers all-in-one systems that unwind, laminate, laser die-cutting, strip, slit and rewind, such as the Taurus roll-to-roll system. SEI Laser’s roll-to-roll system, Labelmaster, has options including laser die-cutting, semi-rotary die-cutting, rotary/semi-rotary flexo varnishing, semi-rotary hot stamping and overlamination.
Herzog+Heyman machines can be added to with any of its single units, with all parts height adjustable and combinable. Herzog+Heymann’s transport system, 091.1, can be equipped with tools to produce different jobs. Possible applications can be plough folds, window patching, gluing (hot melt, cold glue), parallel folds and card application.
New products
Due to the various factors defining the future of finishing equipment, product innovation has and is taking many forms.
Spanish machinery manufacturer Enprom is targeting consumer demand for easy-open packaging with eSRC 60, a hybrid converting machine configured with unwinder, label insertion to register, cut to register by semi-rotary die or laser, slitting unit and a two-shaft rewinder. In-line inspection is available as an option.
GM’s latest products include EB30 with electron beam curing, DC350, DC330Miniflex and SmartLam.
Labeltech’s Lavaredo automatic slitter positioning system for both rotary and razor blades can be set-up in as little as 30 seconds, with placement of eight slitters and counter slitters, Labeltech claims. ‘As manufacturer of the first 100 percent servo motorized slitter rewinder, the long experience with this technology give us a solid basis to develop devices always at the top for performances and reliability.’
At Labelexpo Europe 2017, AB Graphic launched the quick change mandrel option for the AuoSet glueless turret rewinder, available as a module on the Digicon Series 3 or as a standalone Vectra turret rewinder. ‘Now, in addition to the turret being set in seconds, the mandrels can be changed without tools in a similar timeframe,’ explains Bell. AutoSet is also now available as an option with AB Graphic’s SRI slitter inspection rewinder, offering an increased automation of production and all its associated benefits.
Dienes has developed the automatic knife positioning system, Label slit 4.0, engineered especially for labels in order to enable minimal set-up times and provide perfect cuts. The system can be used in printing and coating systems, as well as in processing machines, such as finishing and control machines. A compact design and high compatibility, it can be integrated into new or existing machines.
Mounted in a cassette construction, Label slit 4.0 can handle a maximum web width of 915mm (36in), and works at a web speed up to 610m/min (2000ft/min). A change of format can be completed in 10 seconds. The system features a stable bar design with linear rails, a pneumatic expansion shaft/glass hard countershaft. Pneumatic knife holders allow shear, razor blade and crush cuts.
‘The Label slit 4.0 slitting cassette ideally meets today's requirements for a precise cutting edge, minimizing set-up times and reduction of rejects,’ explains Fritz. ‘The use of pneumatic knife holders means that knives no longer have to be reground in sets, which reduces costs and the number of unproductive knife changes when slitting a wide variety of materials.’
Toksværd identifies Industry 4.0 optimization as of further importance to the future of finishing, alongside a focus on the shortest possible, and easiest, make-ready time to provide optimum profitability.
Grafotronic’s Malmquist states: ‘Our machines are prepared to connect with most business management systems and you can set-up your job with the information from a QR code.
‘Online service is also an important feature today. We support all our customers online and are constantly connected to the machine to help with advanced settings whenever needed.’
Malmquist concludes: ‘Perfect results are required and the key is to be able to run faster with more complex materials and still keep very tight tolerances. We are involved in the Automation Arena at Labelexpo which goes hand-in-hand with what we believe is the future for finishing equipment.’
Stay up to date
Subscribe to the free Label News newsletter and receive the latest content every week. We'll never share your email address.