Focus on food packaging safety
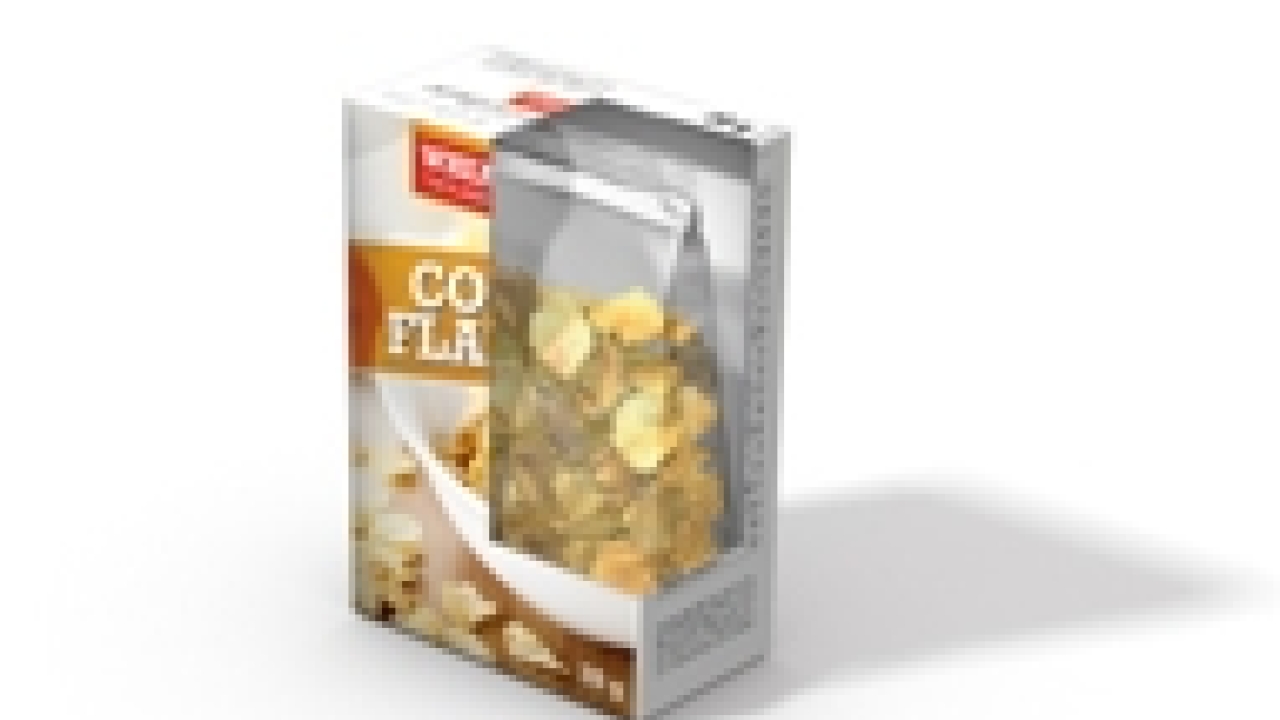
With an increase in food packaging migration alerts highlighted by several high profile product withdrawals from supermarket shelves, the issue of designing and producing compliant food packaging has become a hot topic, writes Felipe Mellado, CMO, Sun Chemical
Migration from food packaging refers to the transfer of unwanted substances from the packaging to the packaged foodstuff itself.
These changes are not always picked up by odor or taste tests, and are usually found by chemical analyses. The migrating substances can come from a variety of sources including the packaging substrates, inks, coatings, adhesives, the printing press itself or the environment in which the raw materials, work in progress or the finished printed pack are stored. The use of good packaging design and good manufacturing practices are therefore critical to reducing the risk of unwanted migration of packaging components.
In Europe, packaging that is intended to come into contact with food must meet the requirements of EU regulation (EC) No 1935/2004. The guiding principle of this legislation requires that food packaging should not transfer materials to the packaged goods in quantities that bring about a change in nature, substance or quality of the food and must not be injurious to health. In addition, producers must operate using Good Manufacturing Practice (GMP) as defined in EU regulation (EC) No 2023/2006. More recently, the Swiss Regulatory Authorities have introduced an Ordinance, which specifically outlines lists of raw materials that can be used in food packaging inks. Each listed substance has a migration limit against which the downstream stakeholders are expected to assure compliance.
Whilst legally this Ordinance affects only the inks and packaging within Switzerland, its effects are felt throughout Europe and beyond. In fact, many customers and brand owners outside of Switzerland expect inks and coatings to comply with these requirements. At the start of 2011 the German Authorities also declared their intention to implement their own National Ordinance on inks for food packaging. Both sets of legislation are fully anticipated to form the basis of an EU-wide legislation in coming years.
As a responsible and leading player in setting the standard for good practices in the packaging industry, Sun Chemical takes its product stewardship role in the packaging design and production workflow very seriously. The company strongly advises the industry to adhere to all published guidelines and regulations covering food packaging and to use only appropriately selected inks and other consumables. It has always been committed to anticipating changes ahead of time as well, and complies with regulations relating to the chemical industry at large.
Printing compliant food packaging is often seen as a minefield of complex legislative decisions. However, the brand owner, print specifier and print converter have some simple choices to make. A risk assessment should always be completed at the initial stage of pack concept design. If a migration risk is anticipated, then the pack either needs to be tested to prove its migration performance and appropriate steps taken to reduce the risk, or low migration inks and coatings should be used to avoid any worries. If the testing route is chosen, and it is proven that appropriate barrier performance is provided by the substrate, then the designer has a choice of using standard inks and coatings or intermediate migration solutions.
If unacceptable migration is present, then either a designed-in functional or absolute barrier to migration, or low migration inks and coatings are required. It really is that simple. The economics of the choices are another matter though. Weighing up which route is the cheapest can be complex, but the bottom line is that the whole of the packaging supply chain, from brand owner to packer/filler, needs to work together to ensure safe packaging for the consumer.
The company has worked for many years on understanding the factors affecting migration and has developed a complete portfolio of low migration inks and coatings to support the packaging chain across a range of print processes and technologies.
Mostly, printing and converting companies are expert in selecting appropriate procedures and practices in line with good manufacturing practice in the production of suitable printed food packaging. As a result, the packaging industry has a first class reputation for the production of high quality and safe food packaging. By continuing to strengthen our advice and guidance to printers and converters, in line with the inks and coatings industry association EuPIA (European Printing Inks Association) and Good Manufacturing Practice guidelines, the company hopes to further minimize the risk of migration problems arising in the future.
It is company policy to make best practice advice available to its customers in all aspects of the use of printing inks and coatings for all applications. The company has found in the past that some printers were not using practices and procedures that would minimize contamination during production, and as such it was felt that there was a need for better information and awareness, which the company’s latest best practice guide provides.
In 2004, Sun Chemical introduced the first edition of ‘Print for Packaging – A Printing Low Migration Best Practice Guide’, which has proved to be a very useful and popular document for printer converters and end users alike. Some 5000 copies of this document have been distributed to date. The guide was last updated in 2007 and a third edition is now available that reflects the current packaging market situation, including the impact of the new Swiss Ordinance legislation and REACH. This new guide was officially launched at Interpack in May 2011, and like its predecessors, is proving to be a popular reference book.
Stay up to date
Subscribe to the free Label News newsletter and receive the latest content every week. We'll never share your email address.