Formula for growth
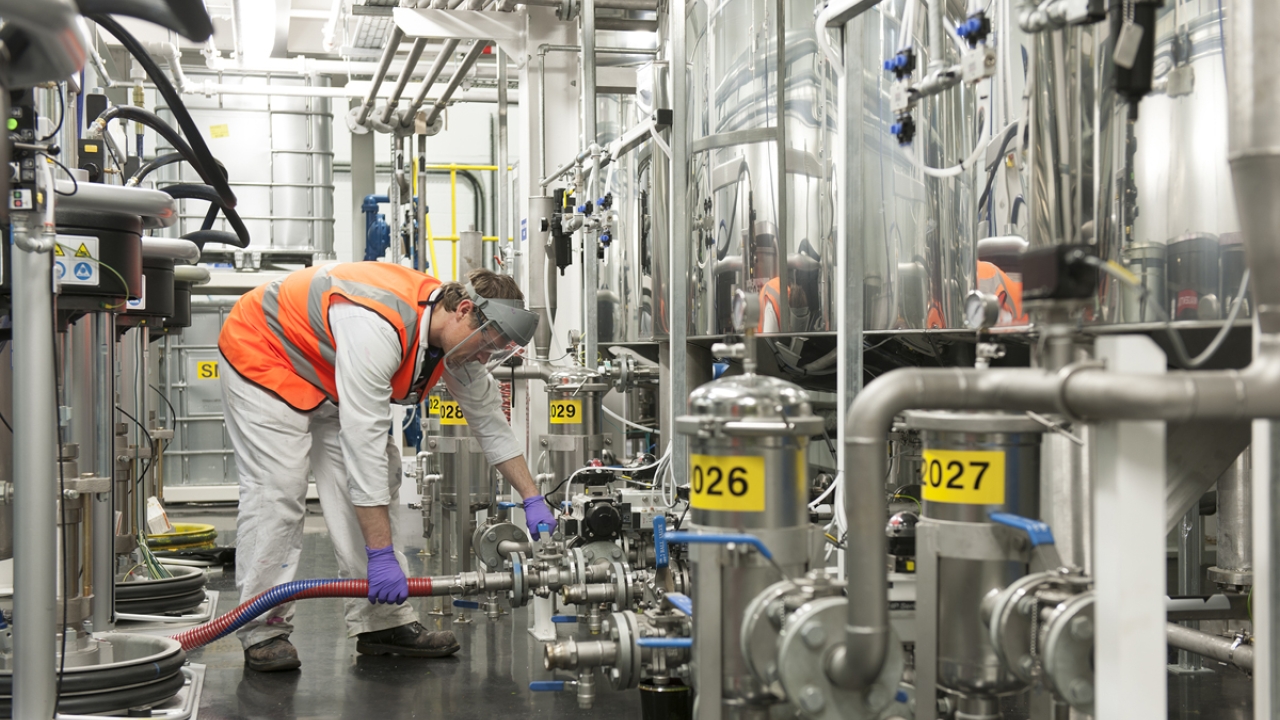
Fujifilm has invested heavily at its Broadstairs, UK site, as it makes a commitment to UV digital inkjet, and wide format, printing.
The new UV digital ink manufacturing facility at the Fujifilm site in Broadstairs in the UK has been two years in the planning, and is the result of an investment of over €4 million.
The new manufacturing facility has a footprint of 1,800 sq m and occupies former warehouse space. It has been built to accommodate a projected annual increase of 56 percent in the production of UV ink at the site, which are distributed globally.
Fujifilm said this projection reflects the demand for its wide format digital inkjet systems, and the success the company has recorded in helping its customers transition to digital.
To fulfill this projected growth, the company took the decision to invest in its digital ink production, which sits alongside the continued manufacturing of screen and flexo products.
Jon Harper-Smith, marketing manager for industrial at Fujifilm, says established products remain a key part of the business but have acted as a facilitator to its investment in digital inks.
‘Screen and flexo products remain a healthy part of the Fujifilm Speciality Ink Systems business, while digital inks will take on a bigger role in the future. Business for our screen inks has declined, as is the trend in the wider market, but the decline has been less than had been expected, while digital and flexo has grown at a faster rate than had been forecast.
‘This environment means we’re able to invest in the future growth of digital with support from our established channels.’
Capacity boost
The extended facility now has the capacity to manufacture 6,000 tonnes of digital ink per year, which will be produced in a variety of packs from 250ml RFID-tagged pouches and cartridges, up to 10-litre packs for high-productivity, wide format printer platforms.
This includes the ability to manufacture ink in four-tonne batches, as opposed to the previous one-tonne capacity, with four new tanks fed directly from the raw material storage silos, and controlled from a single workstation to centralize and streamline management of the process.
The investment in production machinery includes a host of new and upgraded units, such as a new high-capacity mill to help achieve the dispersion characteristics which Harper-Smith says are paramount in inkjet inks, through to a highly automated packing line, which speeds up bottling.
As the Fujifilm digital business grows, so the manufacturing space allotted to such products will be able to grow further, and house further equipment such as additional mills, with the new facility able to expand into areas currently used to produce “legacy” products. Colin Boughton, operations director of the Broadstairs Fujifilm Speciality Ink Systems site, says: ‘We have planned everything meticulously over the last few years, recognizing that to stay at the forefront of digital ink technology with our range of Uvijet inks, we need to work with state-of-the-art equipment and have the ability to increase production and packing volumes.
‘Our vision is to remain at the forefront of this technology and to re-invest every year in order to maintain that position. For instance, we have worked closely with a specialist company to develop next generation dispersion equipment for our inks, and this will allow us to reduce particle sizes to less than 100nm – true nanotechnology.’
Boughton adds: ‘Further investments in equipment will take place during 2013, keeping Fujifilm at the cutting edge of UV digital ink manufacturing and packing technology.’
Research and development
Manufacturing growth will be supported by research and development (R&D) carried out at the site, in which Fujifilm has also invested heavily, with upwards of €2 million spent as part of the Broadstairs development.
Research and development director Rob Fassam says the investment in R&D at Broadstairs follows consistent spend in that side of the business over several years, which will be followed by further expansion in the footprint of the space dedicated to research at the site.
The R&D carried out the site uses small batches of ink produced specifically for testing, which includes: physical tests, such as abrasion and lightfastness; analytical tests, like chromatography; jetting; and temperature testing using freezers, chillers and ovens to investigate the performance of formulations in a variety of environments.
R&D spend has also gone on people. Some 60 staff are currently involved in R&D at the Broadstairs site, while in the past year around a dozen additional employees have been recruited.
Fujifilm is also investing in tomorrow’s R&D professionals, with several members of its laboratory staff attending a day-release degree program at a nearby university. The staff play a key role in its current R&D work, but will also help shape the future.
Employees
In total, more than 340 employees work at the Fujifilm Broadstairs site, and over 80 percent of these are involved in the R&D and manufacture of digital ink. Fujifilm looked to include its workforce as much as possible in the development plans for the new digital ink area, with over 80 employee ideas being used in the final design of the facility.
The involvement of employees extends across the site, with all invited to come forward with ideas to improve productivity and make efficiency gains as part of an overall drive to make manufacturing at the site as lean as possible.
Feedback is given on all ideas, and rewards are presented when employees have reached a specified number of submissions.
Award-winning
Fujifilm Speciality Ink Systems has already received praise for its work at the Broadstairs site, which won the Best Process Plant Award at the 2011 Best Factory Awards as organized by the Cranfield School of Management and Works Management magazine.
Awarded long before the new digital ink facility was opened officially in January 2013, finalists were initially selected after a full documentary examination, which was then followed by an audit of the manufacturing site.
Fujifilm Speciality Ink Systems was shortlisted along with 14 other finalists, and Harper-Smith says entering the award process was initially done as a way for the site to benchmark its activities against other manufacturing facilities in the UK, although it ended up winning.
The judges from Cranfield School of Management were impressed how Fujifilm Speciality Ink Systems is transitioning its manufacturing operation from analog screen inks to digital inkjet inks, as well as its “right first time” efforts, which reached 100 percent over the course of a week in early March for the first time, and the 5S housekeeping program throughout the plant.
At the time of the award, Boughton said: ‘We must not rest on our laurels. We need to sustain our achievement and strive to improve, especially in the areas where we know there are opportunities.’
Fujifilm hasn't rested on its laurels, as the new digital ink manufacturing facility shows, and its plans for further growth and investment should mean Boughton’s hope for Fujifilm Speciality Ink Systems to remain at the forefront of digital ink technology are achievable.
Read more features from Package Print Worldwide here
Stay up to date
Subscribe to the free Label News newsletter and receive the latest content every week. We'll never share your email address.