The future of platemaking
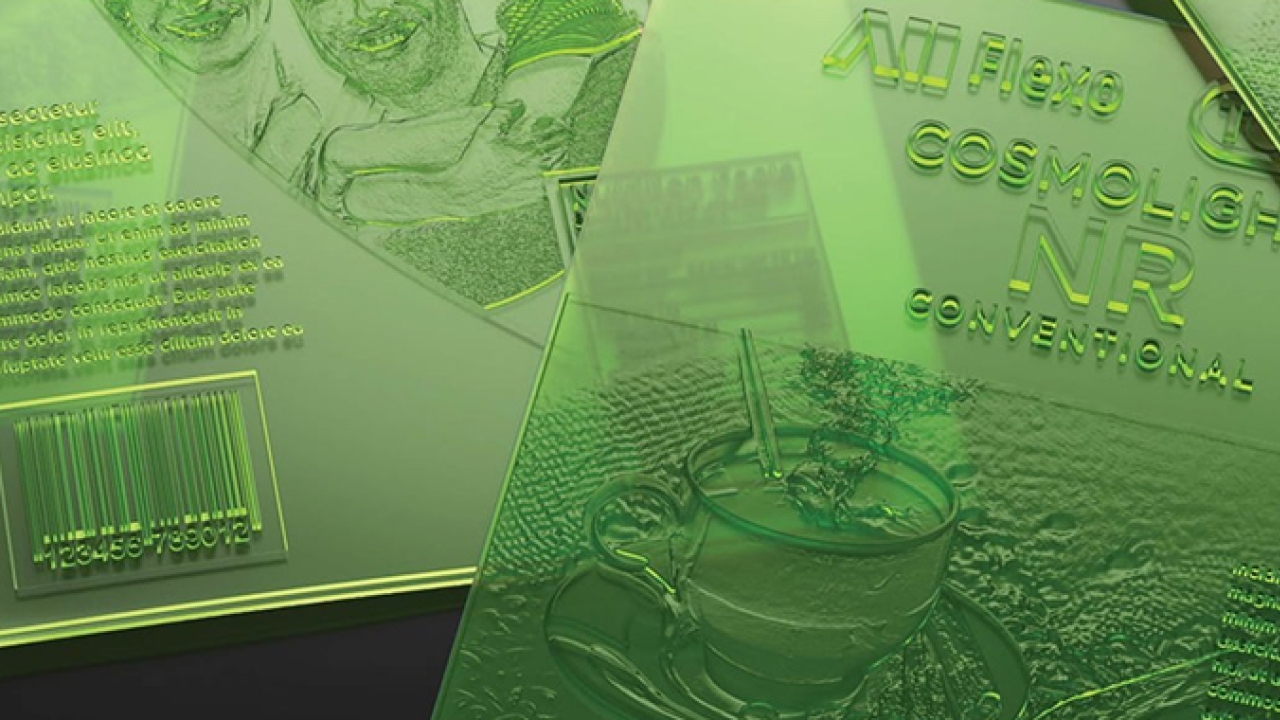
During Labelexpo Europe 2019 several manufacturers showcased their new flexo presses with faster changeover times going head to head with digital technologies in a race for short run jobs. The speed and efficiency of these presses meant growing pressure to reduce the bottlenecks in the platemaking process.
Dr Dieter Niederstadt, technical marketing manager at Asahi Photoproducts, notes that all suppliers are constantly working to find new ways to add value both upstream and downstream from their offerings. ‘This is in response to increased demand by converters for more productive and profitable workflows across the entire product value chain. This includes automation and partnering to create a more inclusive and seamless production ecosystem.’
‘We see continued focus on improving productivity and also continued focus from brand owners on driving a more sustainable world,’ says Chris Payne, CEO of Miraclon Corporation. ‘Flexo is moving up the quality and productivity curve and is taking share from gravure and offset segments. I see all of these trends continuing in the future.’ Plate mounting specialist JM Heaford sees three important trends on the converter’s side. ‘In general, we are finding that customers are choosing higher specification machines with additional options to do more on a single piece of equipment. For example, specifying tape applicators and knives to make tape mounting more efficient and safer,’ says David Muncaster, director at JM Heaford. ‘In many areas, there is also an increasing requirement for automation or for a simplified manual mounting process due to skills shortages in the industry. Another current trend is the fact that more new press purchases are sleeve-based, which is leading to increased demand for sleeve dedicated mounters or for sleeve exchange units that allow customers to mount plates for their new sleeve presses on their existing cylinder mounters.’
‘Our customers have an increasing need to differentiate their packaging graphics to brand owners who need product differentiation to attract more consumers,’ adds Ken Pavett, owner of Flexografix. ‘Relating this to our Flenex plate, our customers are requiring plates to competently handle the complex screening required to reproduce today’s increasingly complex supplied digital files. Our color science and applied expertise are also in demand. Yesterday’s jobs printed digitally, or on offset presses, are now required to appear the same when printed with our plates on flexo presses.’
Dr Uwe Stebani, general manager of Xeikon Prepress, is convinced that digital printing will continue to drive innovation in conventional printing. ‘With digital printing knocking on the doors of the packaging printing industry, a lot of players have realized that automation will be key also with conventional printing techniques. However, this is only half of the story. We also need reliable processes in platemaking as well as smart plate processing equipment with high uptime and easy maintenance. That is why we follow a holistic approach with a combination of new equipment, software integration and tailored flexo plates – Industry 4.0 at its best.’
Without a doubt, since Labelexpo Europe manufacturers have been working hard to bring down the time it takes to image, expose and process a finished plate while reducing the need for a skilled manual operation, integrating technology and tackling the sustainability angle for good measure.
Race against time
Japanese manufacturer Toyobo has been developing water-based products to improve working environments and enhance printing productivity. ‘Our newly developed Cosmolight Z series offers significant improvements in handling of unprocessed and processed plates while maintaining a production time within one hour. Moreover, the series features impressive ink-transfer performance, but with less ink-filling. This supports printers to maximize productivity with less downtime and minimum ink usage,’ says Kyozo Kotani, general manager of Toyobo.
Dantex, a long-time proponent of water-based processing, has also been hard at work developing further improvements for its AQF Aqua in-line processing system. According to Jürgen Wessa, managing director of Dantex in Germany, the company has been able to reduce plate processing time in the Aqua system to only 30 minutes. ‘This system allows very easy handling and maintenance,’ says Wessa. ‘Our Aquaflex plate is a high quality, high performance analogue and digital alternative to solvent and thermal flexographic plate production and naturally forms a flat top dot and is HD Flexo and Esko certified. The whole system is very environmentally friendly and very fast, delivering highly cost-effective processing and high-quality printing plates and printed results.’
Continual efforts to further improve the Fujifilm Flenex flexo plate resulted in a new photopolymerization technology allowing for improvements in processing, durability and final print quality, according to Jon Fultz, packaging product manager for the Americas at Fujifilm North America Corporation, graphic systems division. ‘The Flenex FWL2 technology reduces the industry’s already fastest platemaking times by 50 percent for wash-out and 40 percent in exposure from the previous L version. Dot stability was significantly improved, providing for easier handling and durability, especially in regard to isolated highlights dots. Improved tonal reproduction provides for smoother gradations and improved final print quality.’
Can automation speed things up?
Asahi Photoproducts has seen a significant increase in automation of platemaking, including the ability to start the production of the next plate in as little as 15 minutes. ‘This helps position flexography even more competitively against gravure, offset, and digital,’ says Dr Dieter Niederstadt. ‘We have also seen advances in software, both for controlling the platemaking process and for file preparation. Plus, with water-washable plates and the ability to recycle water used in the plate making process, as well as improved plate quality resulting in less waste, we see flexography moving into a top position of harmonious and sustainable plate production.’
Massimiliano Merlo, global marketing and sales director at Vianord, asserts that automation in the flexo platemaking department offers a significant increase in productivity, a reduction in costs related to low added value work tasks and a reduction in waste due to human errors. ‘Obviously there are economic parameters to consider in order to make investments in automation attractive for everyone,’ he says. ‘But if we think that from 1995 to 2010 around 30-35 automated plate production lines were installed (worldwide) and from 2010 around 100, this is clearly an established trend in the market.’
Dantex is continually working to streamline its systems, making them faster and simpler to operate. ‘Dantex Aqua is an in-line system where the plate is automatically transported, washed and dried. It offers adjustable surfactant dosage and water flow rate, double wash head with programmable speed together with a very user-friendly interface,’ says Jürgen Wessa.
‘Today, almost all offset printing companies are making their plates themselves,’ adds Dr Dieter Niederstadt. ‘If the plate making process can be simplified by software and machine automation aids, we can expect the same trend in flexo, too. We foresee almost “push button” simplicity in plate making being available in the nottoo-distant future which will further drive this transformation.’
Esko, Fujifilm’s technology partner, released Print Control Wizard (PCW) as an upgrade within its Suite 18 platform. It automates the screening optimization and single curve selection of Flenex plates. Prior to PCW, this process was completed manually, through a visual evaluation of pre-printed samples. ‘This automation technology offers our customers visually noticeable screening improvements, coupled with the objectivity of intelligent software,’ says Ken Pavett. ‘I expect the need and demand for this type of automation to continue. Brands have an increasing need for shelf-differentiation. With that need, digital files are increasingly more complex. The industry is benefitting from tools to automate - in this example - the competent integration of these advanced screening technologies within the pre-press departments of our customers’ facilities.’
Let’s integrate – Industry 4.0
With the recently launched Catena product line, Xeikon Prepress offers a technology that integrates and automates several processes. Pre-press data in TIFF or LEN format is transferred to the ThermoFlexX unit which images digital LAMS flexographic printing plates. The company’s Woodpecker software allows surface microstructures to be created to optimize quality levels on film and flexible packaging materials. After imaging, the flexo plate is automatically transferred to the Catena-E exposing unit, which, thanks to UV LED exposure, enables significantly reduced exposure time. This means that exposure does not become the bottleneck of processing.
With the help of a robot arm, the exposed plate is transferred to the new Catena-W solvent washer with automatic punching. From there it is transported through a washing zone followed by drying and post-exposure sections. Thanks to an extremely compact design, the total length of the system is limited to 13 meters (40ft).
Dr Uwe Stebani adds that all platemaking data is collected and stored in a database where it is accessible for quality checks and efficiency improvements.’
Asahi Photoproducts’ latest machine developments also make Industry 4.0 reality. This includes remote access to the human-machine interfaces (HMI) with the latest processor, the AWPTM-DEW 4260 PLF. ‘This new machine concept includes lowmaintenance pumps and easy access pipe layout. It also features smart glass access as an option,’ says Dr Dieter Niederstadt. ‘This allows our technical support team to connect with the customer machine from any location for first level maintenance support. During our evaluation time we saw that 60 percent of the causes of all machine-related service issues can be traced with this support. This is how Industry 4.0 is in action today, and how it is benefiting both suppliers and customers by improving productivity and reducing costs.’
Massimiliano Merlo thinks that ‘people have to devote themselves to carrying out tasks with high added value. Industry 4.0 contributes to increasing the efficient exploitation of machines, reduces production times – in some cases eliminating overtime – and allowing employees to dedicate themselves to other tasks.’
Sustainability at the forefront
Along with the race against time comes the race towards achieving sustainability goals, which are no longer just the domain of substrates, inks and adhesives. The pressure for environmentally friendly production has been passed down the supply chain to the plates and platemaking department.
For Fujifilm environmental stewardship is nothing new, where the company’s Corporate Social Responsibility commitments include addressing climate change, promoting recycling of resources, addressing energy issues towards a non-carbon society and ensuring product and chemical safety. ‘In the Americas graphics and converting market, we are seeing the influence of Millennials and Gen Z driving CPGs and retailers to seek more conscientious solutions as it relates to substrates, colorants and printing technologies,’ comments Brent Moncrief, vice president of strategic marketing and brand management, at Fujifilm North America Corporation, Graphic Systems Division.
‘Many converters are now considering switching to inks and substrates which have less impact on the environment, such as solvent-based inks to water-based, conventional UV inks to low migration, and use of substrates manufactured with recycled materials,’ comments Kyozo Kotani. ‘Plate manufactures must follow these requirements while achieving gravure-like printing quality.’
Friedrich von Rechteren, global commercial vice president of Flint Group Flexographic, thinks that local solvent handling regulations and customers interested in offering a solvent-free production environment are creating more interest in thermal plate processing. ‘People purchasing our nyloflex Xpress Thermal System benefit from less waste in developer roll, device energy savings and very low VOC compared to solvent plate making,’ he says. ‘The benefits include 30 percent less waste, up to 88 percent reduction in electricity, and a plate processing time of only 45 minutes, which results in reduction of operating costs, improved productivity as well as the same excellent print quality known from solvent plates.’
At the same time, manufacturers of solvent-based processing systems are also focused on reducing environmental impact. Flint Group, for example, says the automation and integration of the Catena system results in higher consistency across the process and produces less plate waste. ‘While driving the cost curve of flexo plate making down our system also sets new standards concerning VOC through encapsulation of critical parts.’
But, says Jürgen Wessa, ‘large discount supermarket chains no longer want to read the word “solvent” in their supply chains. Our flexo printing plates are processed without any solvents. Dantex only supplies water-washable plates, some of which do not even require surfactant for wash out.’
‘Everyone is talking about how to minimize the environmental impact of label production and the entire label life cycle,’ says Dr Dieter Niederstadt. ‘Our sustainable AWP technology is ready to go. We need to see if after the coronavirus pandemic, we will have a change of mindset as we move to a “new normal” or will it be back to the “old normal”? Converting to production processes with less environmental impact will initially lead to an increased cost. We are not sure if the focus on sustainability is only talking or actually represents the intent to implement new environmentally balanced solutions. We hope it is the latter. While there are costs associated with such a conversion, we believe the long-term benefits will outweigh the short-term financial impact.’
What the future holds
Kyozo Kotani believes flexo printing will stay attractive with its high print quality and low running costs, and process automation at each printing and converting stage will speed up. As for plate processing, the whole process line from plate ablation to mounting will be automated in the future.
‘Environmental protection is another key factor and it will become increasingly important when determining an investment, encouraging investment on solvent-free processing such as water-wash. Following these trends, we are developing new products suited to an automated plate-making process and that have lower environmental impact not only for being water-wash, but also with a complete recycling system for wastewater,’ he adds.
When asked about the future, Brent Moncrief has no hesitations. ‘No surprise here – shorter runs, faster turnarounds and unique effects to differentiate products on shelves or on screen. Our customers are increasingly seeking ways to extend the useful life of their capital investments, for example by retrofitting LED curing lights or adding inkjet imprinting to their current flexo printing presses.’
‘We expect to see ongoing growth of hybrid printing featuring different combinations of print processes to exploit the inherent advantages of flexo, offset, gravure and digital, as well as a continuing increase in expanded gamut color,’ says David Muncaster. ‘There has been some reversal to SKU proliferation during Covid-19 but this will no doubt pick back up again in the near future driving reductions in average run lengths which leads to closer focus on set-up times and efficiency. This in turn will drive increased attention to mounting accuracy – especially automated mounting – as the need to minimize set-up times and costs becomes even more compelling with the increasing complexity of work.’
Asahi Photoproducts is betting on increased automation. ‘It will be one very strong trend in both print and plate making,’ says Dr Dieter Niederstadt. ‘We also expect continued development of new materials and processes with lower environmental impact, but we need the support of the brands, converters/printers and even the end consumer to gain traction in the marketplace as we would expect to see some increased costs initially. However, the mindset and willingness to make the entire label life cycle more sustainable is there. Now we – as an industry and community – just need to act.’
Stay up to date
Subscribe to the free Label News newsletter and receive the latest content every week. We'll never share your email address.