Indian entrepreneur masters different label printing technologies
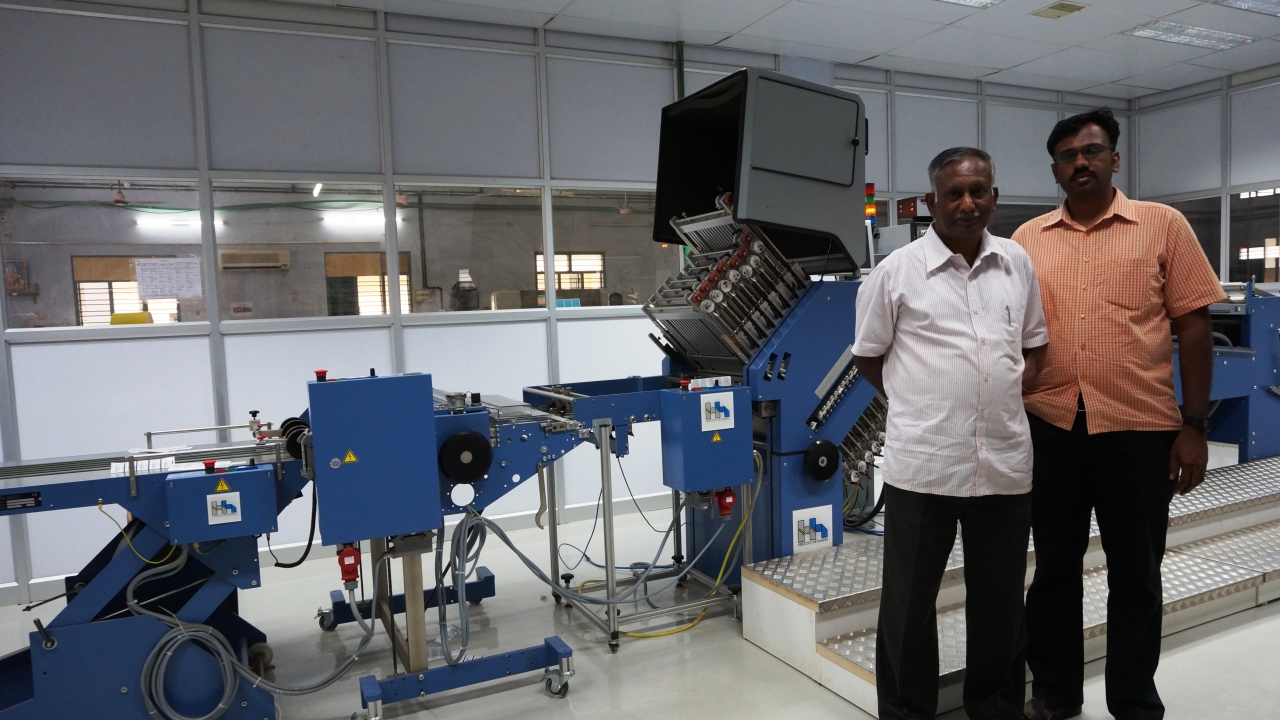
Sel-Jegat, a family business, is a leading pressure-sensitive label manufacturer based in Sivakasi, south India. The company is growing at 15 percent per annum and is planning to diversify into printing of shrink sleeves as well as in-mold labels at its 80,000 sq ft factory.
Increasing demand for small-volume shrink sleeves and in-mold labels catalyzed the need for Sel-Jegat to cater to these requirements from its customers. The company started partnering with a local rotogravure printer who gives them short run jobs for printing shrink sleeves. The company is now in the process of investing in an inspection slitter rewinder that will be used for shrink sleeves, self-adhesive and wraparound labels.
Another investment, still in the pipeline, will include a 430mm width machine for printing labels and packaging products. The premises already houses an IML punching machine from Iwasaki.
Today, Sel-Jegat is one of the few label printing companies in India that masters multiple technologies such as offset, flexo, letterpress and screen, and also prints pressure-sensitive labels. The company houses pre-press facilities for all the above technologies from Esko and a Glunz & Jensen flow line processor. A digital workflow streamlines pre-press, press and post-press works through PDF references.
Early days
Now a printing house to reckon with, success did not come overnight to Sel-Jegat. V S Raveendran, a chemical engineer by qualification, started with a proposal to start a pigment manufacturing plant in Sivakasi. He joined his uncle Arumugasamy to run the first Shiki label printing Japanese machine imported for manufacturing of non-adhesive labels. With this Sel-Jegat started its journey in 1980 to become one of the most respected label printing houses in the country.
The first year, however, was tough, as Raveendran recalls. He visited drupa in 1982 where he observed the increasing focus on self-adhesive labels. He was determined to try something new, so bought a Heidelberg Platen hot foil stamping machine, the first in south India. Hot foil stamping was still done manually at that time.
To market the business, the Sel-Jegat team would go door-to-door to sell the hot foiling concept to offset printers. Eventually it was carrying out all the hot foiling jobs for most of the offset printers in Sivakasi. As demand increased, the company bought several Heidelberg Platen machines and cylinders to do the work for other printers.
In 1993, when then finance minister Manmohan Singh opened up the economy, the company invested in its first new Heidelberg GTO offset printing machine and started printing liquor labels on the single-color press and decorate them with hot foil stamping. There were few self-adhesive labelstock suppliers at that time in the country so Sel-Jegat was printing mostly wet-glue labels.
For self-adhesive label printing, the company associated with Iwasaki of Japan and started investing in its first series of VSD machines as well as RUH semi-rotary presses. Today, Sel-Jegat houses six Iwasaki presses.
When Raj Srinivasan, the first chief executive officer at Avery Dennison India, heard that Sel-Jegat was printing self-adhesive labels in Sivakasi, he visited the factory and advised Raveendran to invest in rotary roll-to-roll printing machine. Sel-Jegat evaluated some presses and started full rotary flexo printing on a Mark Andy 2200 in 2001.
The second flexo press, again a Mark Andy 2200, was installed in 2004 along with its first inspection slitter and rewinder machine. Raveendran says, ‘The Rotoflex VLI was the first machine in India with AVT inspection camera. At that time, only AVT offered a 4k inspection camera for defect detection which we needed for inspection of pharmaceutical labels.’ Subsequently two more AVT camera systems were installed on Prati slitter rewinders.
Sel-Jegat now houses two scanners to compare the first printed sheet with customer PDF for text, color, barcode, pharmaceutical code and other aspects using a Nikka camera from Germany. Two more Nikka camera systems were installed in two bi-directional machines first in 2007 on a Rotoflex and another one on Prati in 2014. Another two Nikka camera systems were installed in printing machines to check the printed labels with customer PDF files for all parameters and to implement digital workflow. The company implemented an ERP system in 2012 that has improved its workflow.
Sel-Jegat also houses India’s first Prati Sun Bidi, a sale announced at Labelexpo India 2014. The machine features bi-directional web inspection and uses a Nikka high-resolution camera featuring modular apps for 100 percent print inspection such as color measurement, PDF-to-print verification, barcode and 2D code verification, ISO grading and statistical data collection.
Investment
Raveendran’s elder brother Jegatheesan always insists on investment in new technologies. After reading an article on intermittent letterpress in Labels & Labeling magazine in 2008-09, the company chose to invest in a 6-color Iwasaki LR3 instead of a digital press. ‘It made sense to invest in the technology for short run labels and to invest in highest automation with GMI ink control. When a repeat printing order comes, the earlier ink feeding data saved is retrieved to reprint the job and thus make-ready time and wastage is reduced. We can run the machine even at five to six meters a minute to do make-ready and match the Pantone colors. However, we will invest in digital printing when our variable data printing increases.’
In 2016, Sel-Jegat invested in offset label printing with an Iwasaki TR2 press. Raveendran says, ‘We wanted to go into offset label printing technology four years ago but at that time we did not have volume to print on full rotary offset press. The Iwasaki TR2 intermittent offset press allows us to offer high quality litho printed labels in short to medium runs. With the lowest cost of origination for offset, the intermittent process offers unlimited repeat sizes and low set-up web waste. We find this process a complementary technology to our flexo presses and it helps us compete against short run digital work as well. The ability to print on textured substrates is also a great advantage in many markets.’
The company supplies labels to different types of industries including pharmaceutical, food and beverage, cosmetics, electrical and electronics, and automobile. More than 45 percent of production goes to the pharmaceutical industry. The company is audited and approved by several leading pharmaceutical companies. Sel-Jegat is in the process of creating a separate facility that will only cater to that sector.
The company also works on innovations with raw material suppliers. Recent product additions include manufacturing of booklet labels, bottle hanger labels, multi-layer labels, and wet wipes labels for larger pack size. Most of the labels printed are deemed exports. Sel-Jegat focused on direct export in 2016 and received an encouraging response. However, to cater to the market overseas, Raveendran feels that the company needs to increase its production capacity.
The younger generation now working at the business is interested in specialty label printing using modern technology.
Stay up to date
Subscribe to the free Label News newsletter and receive the latest content every week. We'll never share your email address.