Kumar Labels switches to LED UV
Kumar Labels has switched to UV LED inks from Siegwerk for its flexo presses and plans to expand it to its screen and letter presses in the future at its plant in Greater Noida and an upcoming plant in Indore, India. The decision is in line with its ‘Sustainability Goals for 2022’ when it aspires to become the country's lowest energy consumer per label
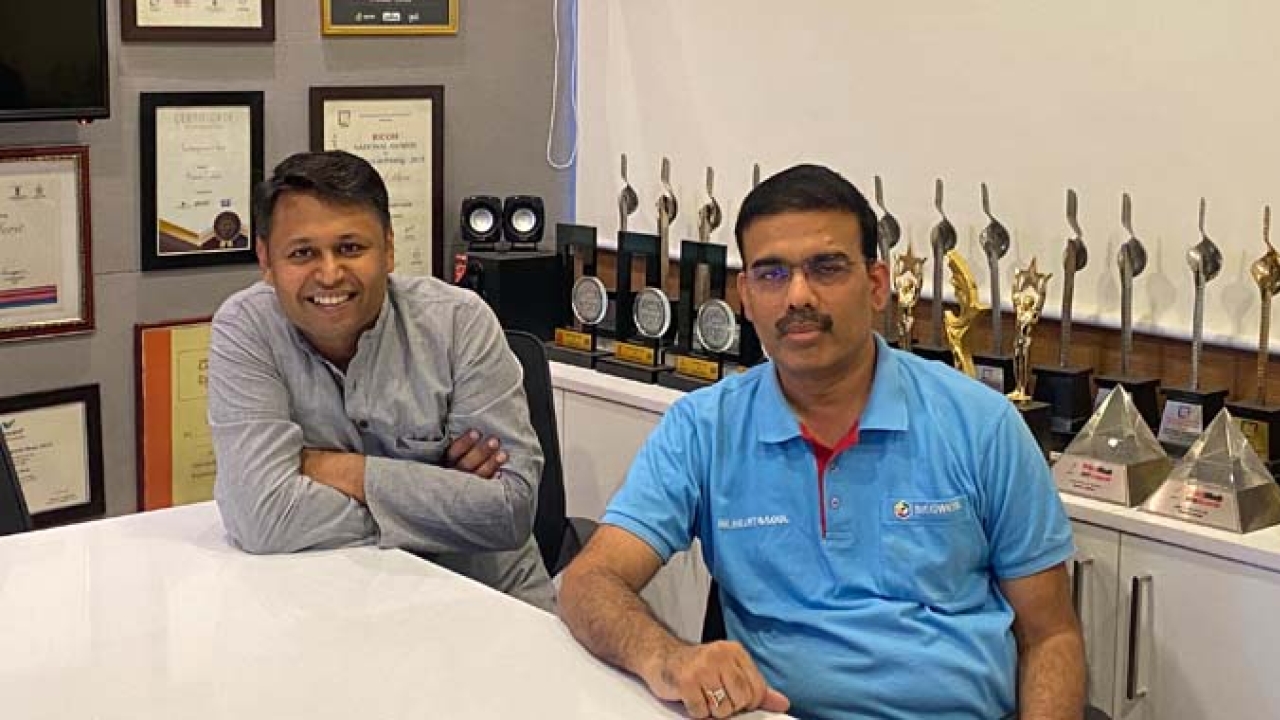
‘While our customers often demand sustainable labels, we thought the first priority is to make our plant as less energy consuming as possible. Our key differentiator with sustainability is that we don't talk; we aggressively execute the task,’ says Anuj Bhargava, founder of the company.
In a bid to be self-reliant, the company has developed labelstocks and equipment such as label applicators in-house.
Bhargava conducted the first UV LED trials in 2017 with a Korean system.
‘We didn’t know which frequency would be right. We tried 365, 385, 395 and we got a hybrid lamp and tested it. We got inks from multiple sources. We were able to run the press at 120m/min without any concerns. That was the very first positive realization that this was the right technology for us. Power consumption was less than 30 percent at similar speeds, so it was an absolute no-brainer for us to switch to UV LED.’
The converter has 640 kVA power line installed at its plant. It made more sense to switch to LED UV inks to save power instead of expanding the power capacity as it expands production.
In 2019 December, Bhargava visited Labelexpo Shanghai and noticed that ‘every single flexo press on display had UV LED.’
‘And this was different from what we saw in Labelexpo Europe. We saw that China was converting to UV LED much faster than Europe and America.’
Bhargava then visited a UV equipment supplier’s installation at one of the largest label printing facilities in Shanghai. The Chinese converter was using 12 Mark Andy presses and two other Chinese presses, all running on UV LED since 2014.
‘Here we were talking about it, and the world is so much far ahead of us.’
‘We have been a leader in taking risks of being the first ones to do many things. From the very first machine we installed to what we do today. We have never shied away from being the first ones to do crazy things,’ he says.
Kumar Labels converted all its flexo presses to UV LED and plans to go the same route with its screen and letter presses.
The converter and its family companies have been working very closely with Siegwerk since the beginning, so it was an obvious decision for Bhargava to go with the manufacturer of UV LED inks.
‘And, of course, Siegwerk was kind enough to help us out by bringing the stocks, conducting trials in time.’
Bhargava says that converters generally hesitate to adopt new technology in India. In addition, the high price of new technology further adds to the hesitation.
‘It is a chicken and egg story; you will not use LED inks because you don’t have lamps, and lamps are too expensive,’ he said. ‘Someone has to take the lead. We broke that chain.’
UV LED inks are compatible with conventional UV systems. Bhargava recommends converters planning to switch to UV LED not to wait for a UV LED system and start using the inks on the existing setup for at least three to six months before fully investing in the technology.
‘So theoretically, we should have switched to inks much before we did. We started only when we had the LED lamps. It led to both the inks being in the system in parallel, which then also led to problems wherein sometimes we put a conventional ink in the LED system and later figured out the problem.’
It has been a year and a half since Kumar Labels switched to the technology. The converter’s power consumption has dropped by 50 percent with the new inks. Other issues such as extracting ozone, heat and the need for blowers and air conditioning were reduced in the press room due to the LED technology. Unlike conventional lamps, LED lamps do not require heat up and cool down time. The converter claims to have gained press time of 30 minutes daily with the new lamps' instant on and off feature.
‘Beyond that, because of the way the technology is built, your curing is faster and deeper. Because of that, you can run your presses faster, so I would say a good 20 percent increase in speed is absolutely achievable. After calculations, with the power savings and throughput increase, perhaps the system has already paid for itself,’ Bhargava explains.
Siegwerk support
Siegwerk supported Kumar Labels with the transition from making samples available from different parts of the world, arranging raw materials, and blending the inks to visiting the facility for multiple rounds of tests. The manufacturer stocked inks for the converter despite low demand in India.
Ajit Singh, CFO of Siegwerk India, says: ‘We support not only Kumar Labels but for all their family businesses in other segments as well, which made by default choice partners.
‘At that point in time, there was no LED demand in India except from Kumar Labels. Naturally, we do not have that kind of inventory buildup and imported most of our raw materials and inks from our group companies either from China or US. We ensured that even if it is a 2kg requirement, it would not be a problem for Kumar Labels.’
Siegwerk India’s main plant is in Bhiwadi, about two hours away from the Kumar facility. It also has a warehouse in Noida to stock raw materials, which makes supply easy for Siegwerk. The company’s technical team also works in the Bhiwandi plant, which is readily available for Kumar.
Singh highlights that Indian label converters are still hesitant to switch to LED UV due to the high costs and reliability of the supplier.
‘But as ink manufacturers, we are pushing LED into the market. And just like Kumar Labels, we believe in taking risks.’
Siegwerk stopped using toluene in its factory five years ago, which was recently banned by the government in India.
‘We could not target the toluene-free ink market for four years because of no demand. And our toluene-free ink was certainly a slightly higher rupees per kilo than the toluene inks. We lost some of the market share we could have gained. But being an ethical, forward-looking company, we stuck to our decision,’ Singh explains.
The company has now converted all its mineral oil ink to mineral free. Singh says there is no pull from converters for these inks in India for safe inks yet.
Singh echoed Bhargava’s point that the conversion rate from conventional to LED UV is quite high in the developed market such as USA and China than in India.
He says that LED inks offer several benefits. ‘In our internal calculation, we have found that in a year, you can save almost 30 tons of carbon dioxide and which is equivalent to a car running for 200,000kms.’
And the life of conventional lamps is around 2000 hours in contrast to LED lamps which offer a life span of over 50,000 hours.
Siegwerk plans to develop more products as demand for its LED inks grows. Singh says the cost of the inks will come down as market demand grows.
‘Similarly, machine manufacturers are also working on new LED technology. However, if converters want to move to LED, they don’t need to buy the whole setup. They can buy lamps and inks. UV lamp manufacturers are also noticing the movement and working on bringing the costs down. With new LED UV lamp manufacturers coming out, it's not the dependency on just one or two suppliers,’ Singh concludes.
Stay up to date
Subscribe to the free Label News newsletter and receive the latest content every week. We'll never share your email address.