Maximizing specialty film production
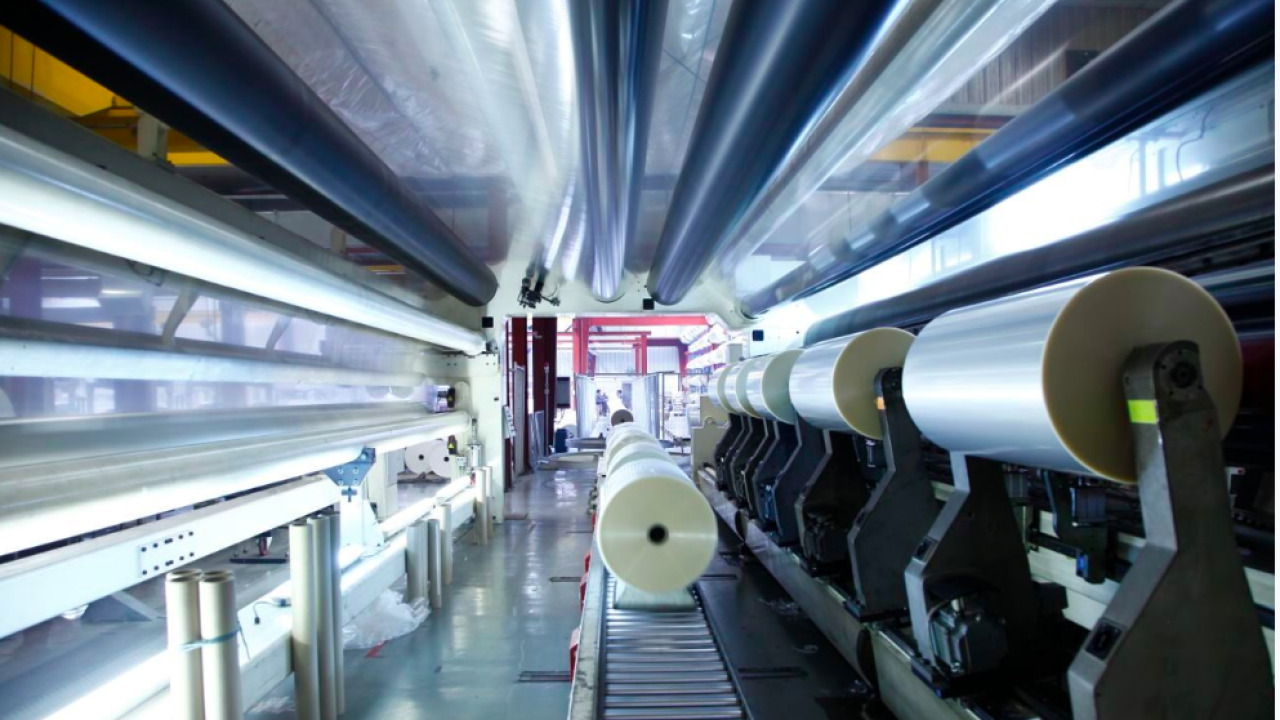
Ramneek Jain, CEO at Max Speciality Films, says: ‘We have had a significant improvement in capacity which is reflected in our growth. The new line will bear sweeter fruit as we develop and commercialize more specialty products.’
The fifth BOPP manufacturing line has almost doubled the company’s production capacity from 46.35 kilo tons per annum (KTPA) to 80.85 KTPA, while also reducing production cost per unit. Export to more than 45 countries contributes 30 percent of the company’s turnover.
Installed mid last year, it is claimed to be the first BOPP manufacturing line in the world with in-line coating, allowing the company to not only be more efficient in its production but also to reduce waste and be energy-efficient. More significantly, it allows the technical team flexibility to alter the chemistry of the product, as per market demand.
‘In-line coating is a key differentiator to this line,’ says Jain. ‘It is being done on polyester films but never on BOPP films. Thus, it opens new frontiers of possibilities for us. Coating on this line is different from the traditional process in the sense that it is done on the BOPP film in between machine direction orientation (MDO) and transverse direction orientation (TDO) sections and not on the melt. It therefore becomes an integral part of the chemistry of the product, making it a highly specialized product. Our films can be top-coated in-line without any further off-line coating.’
K Manohar, chief technical officer at Max Speciality Films, adds: ‘Designed to manufacture high barrier films for specialty segments with better print receptivity and recyclability, this line clearly indicates that we are specialty-driven. The new investment enables us to produce 12 to 90 micron films and even higher to be able to further cater to in-mold labeling and pressure-sensitive labeling segments.’
Another significant feature includes an in-line web inspection system so the entire roll of film gets inspected in real time. ‘Quality is increasingly becoming critical for developed as well as emerging economies, so we have invested heavily in that direction,’ Jain adds.
Production at MSF is supported by four BOPP manufacturing lines, three metallizers, two off-line coating lines and three thermal extrusion coating lines for thermal lamination.
According to Manohar, the estimated consumption of BOPP in India stands at 50 kilo tons per month or 600 KTPA, with industry growth estimated at 10 to 15 percent a year. ‘Our share is around 10 percent, of which about 50 percent is specialty,’ he says.
Innovation and sustainability
Further strengthening its foothold in the specialty segment, Max Speciality Films claims to be the first in the country to launch biaxially oriented polyethylene (BOPE) films. ‘Being PE, these films have better printability, metallized layer and sealable layer,’ says Jain. ‘The properties and performance of BOPE can reduce a layer in packaging. We can offer the entire structure made of PE which is easy to recycle. This innovation is gaining traction in the global market and we are in the process of commercializing it soon.’ MSF could look at diversifying into shrink sleeves with this film owing to its good shrinkage properties.
The company houses a DSIR- and NABL-approved R&D lab with 15 dedicated people working at developing new products.
While developing new products and technologies, MSF is focused at continuing to develop and innovate its core product, wraparound films. ‘The wraparound market is driven by innovations at high-speed bottling plants. The films undergo design improvement and requires to be sealed at lower temperatures. Some of these variables are driving this market,’ says Manohar.
With the new line, MSF is offering films that are recyclable. ‘We are manufacturing very high barrier films that replace aluminum foil, and thus makes a pack recyclable if all layers used are the same material,’ says Manohar.
While Max Speciality is reducing the amount of waste it generates, it also has its own recycling plant. The company has established a process for in-house recycled plastics consumption and segregates waste based on product segments in which it can be reused. This ensures the company is recycling almost all in-house waste, including metallized BOPP.
Further, MSF is exploring a partnership with a company in the US that has two patents for pyrolysis.
Stay up to date
Subscribe to the free Label News newsletter and receive the latest content every week. We'll never share your email address.