Watershed Group drives out waste with Vivo Colour Solutions
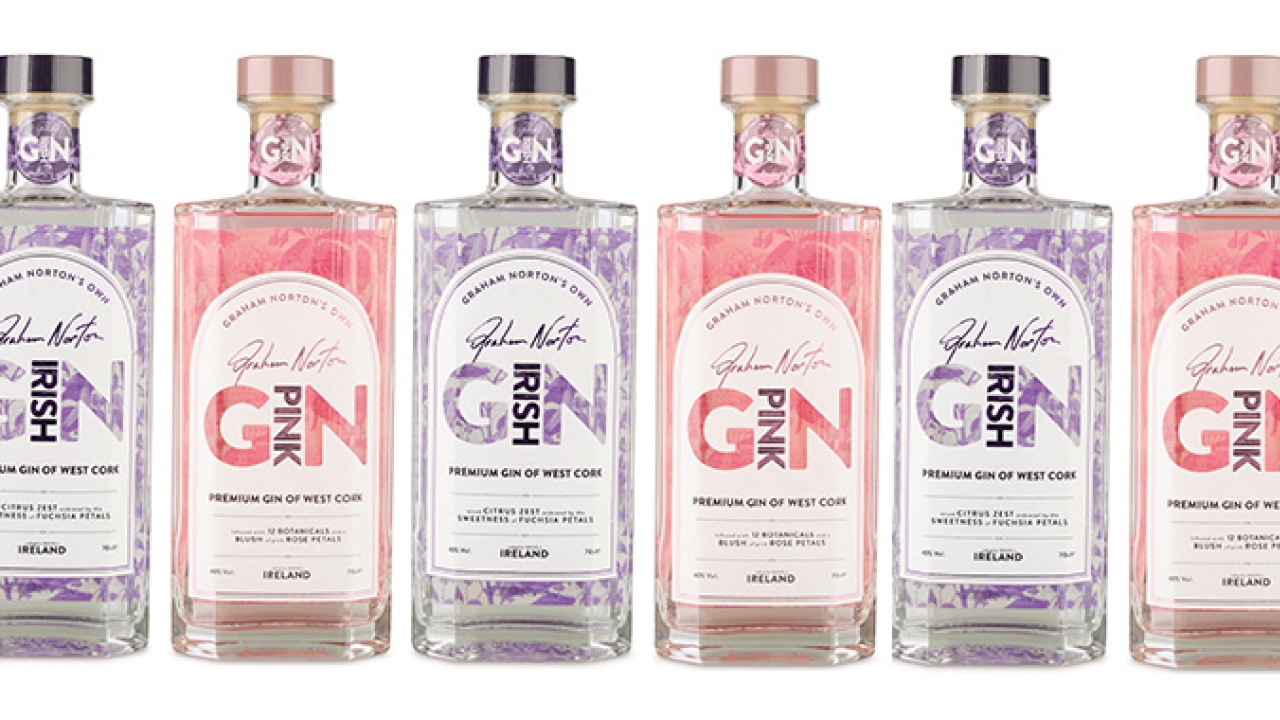
The Watershed Group is Ireland’s largest family-owned label converter with five production sites at locations including the UK, Poland and Germany. The company supplies a host of international brands including Nestlé, Reckitt Benckiser, Tesco, Lidl and Asda Walmart, and has built a reputation for excellence in the premium beverages sector.
‘From the beginning, we have seen ourselves as growing in the direction of a more complicated offering than being just a label or sleeve producer,’ says Liz Waters, CEO, Watershed Group. ‘The quality of the packaging or label is a prime consideration for those brand-owners. They expect not only a high degree of label sophistication, but a tight tolerance in color matching.’
With a HD flexo workflow at its locations, the company differentiates itself through award-winning design ingenuity and the ability to offer consistent quality at short notice, on both local and international scales – often competing in markets once considered the preserve of offset.
Workflows are the same across the group with inks from Flint Group, Esko Studio software, and a combined total of 11 Mark Andy P5 Performance series flexo presses, complete with in-line finishing options, including embossing, debossing, silkscreen and die-cutting. The company was the first to install the Mark Andy Digital Series hybrid flexo-inkjet press in Ireland and the UK.
‘Standardization brings us a big advantage because it means we can produce the same label to identical standards in any one of our plants,’ Waters says. ‘This provides the assurance of consistent quality from one job to the next and across locations.’
After installing Label Traxx MIS to monitor efficiencies at its new Dublin factory, Watershed discovered that its existing spot-color matching procedures were causing considerable material waste and production delays, and was an obstacle to assuring the repeatable quality expected by brand owners. For special colors, press operators were manually mixing recipes prescribed by their color guide, using eyesight to judge accuracy. This lacked objectivity and the recipes did not account for factors in flexo printing that also affect color results.
‘We would eventually achieve the desired result, after more than one attempt, but have no way of knowing how to achieve the same results on repeat runs,’ Waters says.
Spot colors ‘first time right’
Flint Group introduced the company to its newly developed Vivo Colour Solutions Service featuring a cloud-based database that translates the customer’s color target into an ink formulation to match the color target on the press.
Installed at the Dublin site in June 2019, Vivo Colour Solutions provides a digitalized and bespoke service. To get the perfect match from a library in the database of over 350,000 formulations developed by Flint, Watershed’s color makers enter measurable digital color targets, plus the job’s specifications, including substrate type and surface treatment, ink set, and anilox line count details. The recipe is then generated.
‘Flint Group’s Vivo Colour Solutions has helped considerably in our efforts to improve operational efficiency, taking human error out of our production chain and significantly reducing machine downtime, ink use and substrate waste,’ Waters says. ‘The formula for every job is in the Cloud so the makeready people can match it immediately and exactly. The speed, ease of use, and consistent precision of the database means we have assurance of meeting demanding color targets first time, time after time.
‘Based on our MIS measurements, we are saving five minutes per color and 25 linear meters of material per color. As we perform up to 300 jobs per week at our Dublin factory, this amounts to considerable savings.’
Customized database
To set up the search engine specially for Watershed’s Dublin factory, Flint conducted an audit of the aniloxes used and tested each of them on the Mark Andy press at the site, and added their characteristics to the database. This accounts for the relationship between anilox cell volume and ink density on the job. The system then automatically adjusts the ink formulation.
Implementing Vivo Colour Solutions led to ink preparation becoming the role of a dedicated team, so the presses can be swiftly set up, with no last-minute color-related delays. After the success at the Dublin site, Watershed plans to roll out the database to its Poland and Germany plants next, and avoid buying in ready-mixed inks.
Stay up to date
Subscribe to the free Label News newsletter and receive the latest content every week. We'll never share your email address.