Bobst closes gravure color loop
Bobst has launched an ECG technology which automates closed-loop color control of gravure printing.
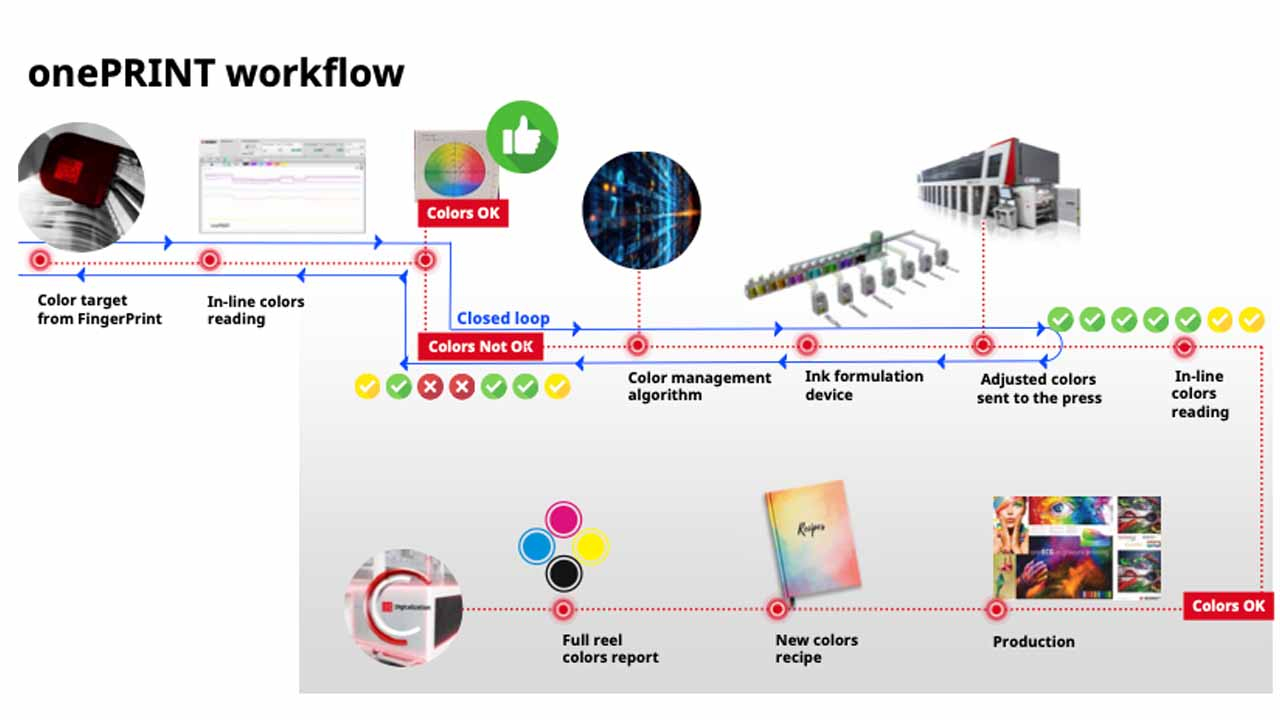
Bobst has unveiled its smartGravure technology, which brings digitized and automated closed-loop color control to the gravure process for the first time.
Bobst’s smartGravure-equipped Master RS 6003 press is the first gravure press on the market to be Pantone-certified.
At the heart of the smartGravure process is the oneECG extended color gamut system, which Bobst first developed for its digital and flexo presses. Pantone colors are matched from a fixed set of seven color inks (CMYK+OGV).
The exciting development is the ability to measure and adjust color automatically on the fly.
The process colors are continuously monitored using an Esko-AVT in-line spectrophotometer measuring optical density 9,500 times a second.
Measurement information is passed to the Bobst onePrint ink control system, which adjusts between base and color extenders to bring color to the target density. Ink temperature is maintained at a consistent 18-22 degrees C to keep ink viscosity stable. The onePrint workflow starts from a color target derived from a press fingerprint. If the in-line color reading is out of tolerance, a color management algorithm is activated and passed to the low-ink pan and formulation device, from where the adjusted colors are sent to the press.
Measurement information is passed to the Bobst onePrint ink control system, which adjusts between base and color extenders to bring color to the target density
If the next in-line color reading is within tolerance, a new color recipe is generated and stored. This is an important step that shows how to repeat the correct color.
OnePrint limits the amount of ink in the color circuit to the necessary minimum, reducing ink in the press by over 50 percent compared to a typical conventional gravure press. A standard gravure inking tank has 23L in the ink supply circuit, compared to 9L for this low ink technology.
This also means less solvent evaporation, which, according to Bobst, leads to over 20 percent savings in ink and solvent management costs.
The smartGravure setup process is fully automated through Bobst’s oneSet system.
After analyzing the PDF data, oneSet suggests optimal machine settings for the job. One click transfers the recipes to the press’ print queue.
Bobst says job changeover downtime is reduced by up to 70 percent compared with a traditional gravure press, with full job repeatability and color consistency.
Short runs
SmartGravure opens up new opportunities for gravure to compete in medium and short-run jobs, with Bobst estimating the crossover point at 5,000 sqm.
A demonstration job run during a recent open house in Italy showed the smartGravure Master RS 6003 press printing four different SKUs with multiple Pantones across the same web.
To print the same four jobs in a non-ECG workflow would require five printing units per color, plus white, along with the associated makeready and washdown waste.
Davide Rossello, Competence Center manager at Bobst Italia, states that extended color gamut printing is technically far easier to achieve with gravure than flexo because there are fewer variables: the engraved cylinder, doctor blade angle and ink viscosity.
Rossello says smartGravure is particularly effective where jobs are repeated more than twice.
‘The gravure process is more stable than flexo, so if you reach the target today, you can reach it in three weeks, as there are no additional variables in between. Cylinder costs can be divided by the number of repeat jobs. Flexo plates are generally not usable after two repeat jobs.’
In makeready mode, it takes less than eight minutes to measure a color, correct it, and be ready for production.
‘Compare this to a traditional gravure press, where it takes skilled operators a minimum of 15 minutes per print unit to bring color to target,’ says Rossello. The smartGravure system cuts in half the number of operators required for a gravure press.
Bobst estimates that ink costs are reduced by 11 percent due to using 1000L compared to 50L buckets, reflecting the fact that ink can be purchased in bulk and there is no handling of ink leftovers.
Esko input
Esko provided the color management expertise at the center of the smartGravure system. Esko’s AVT SpectraLab XF is connected to X-Rite ColorCert in the Esko S2 cloud. Specifi c job color target information is sent to the press, automatically setting up the SpectraLab XF with the correct values for each printing unit.
Bobst reports that 94.6 percent of the extended color gamut has been achieved using smartGravure. In one run on the RS 6003 press, 2,369 colors were achieved with a 92.1 percent rating.
Stay up to date
Subscribe to the free Label News newsletter and receive the latest content every week. We'll never share your email address.