Yilpar invests in Bobst gravure technology
Turkish converting company Yilpar has selected two Bobst gravure printing presses, RS 6003 and RS 5003 to expand its flexible packaging operations.
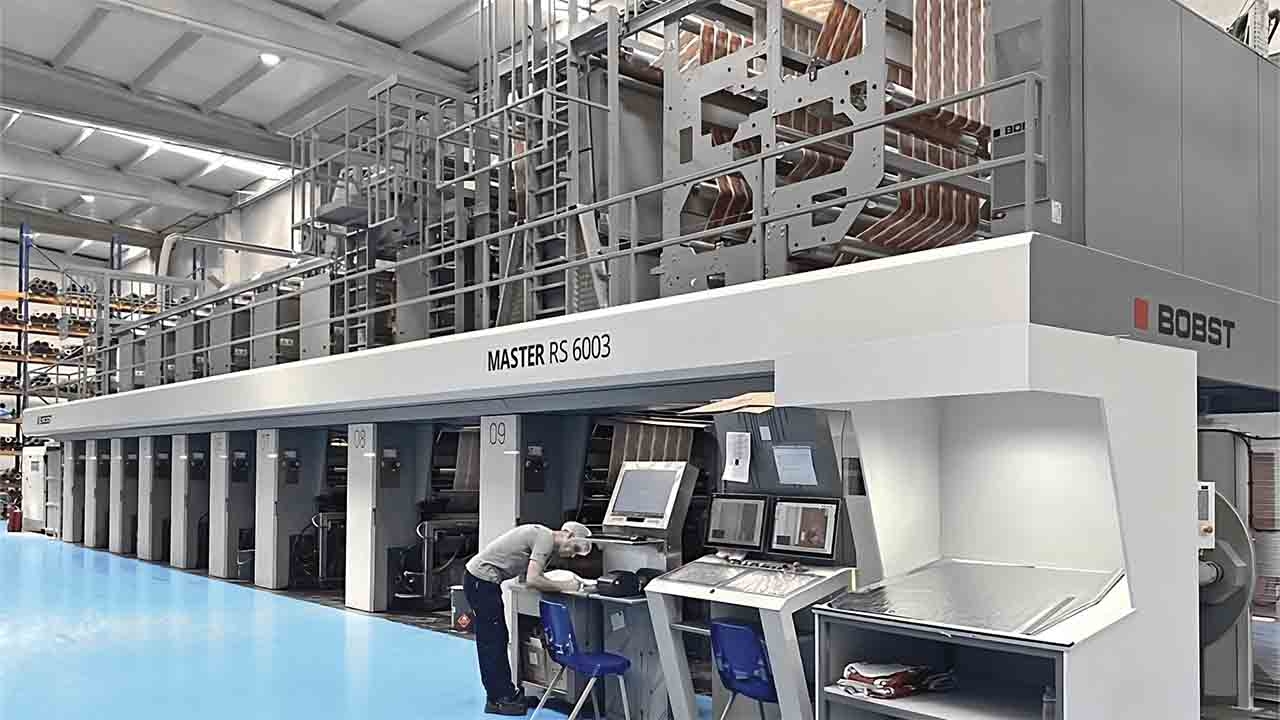
Istanbul-headquartered Yilpar has completed the installation of two Bobst gravure printing presses, a 9-color RS 6003 and a 9-color RS 5003. The installations were done in the company’s production facility at Kemalpaşa, in Izmir province.
Yilpar was established in 1959 by the Yilancioglu family. Paper production started in 1975 and the business grew over the following decades and paved the way for the company to move into flexible packaging manufacturing in 2007. The 2022 investment from Taxim Capital Fund helped the company to increase its capacity four times leading to a current production of 15,000 tons per year.
Yilpar is a major supplier to some of the blue-chip brands, such as Coca-Cola, Pepsi, Pladis and Jacobs, as well as to major private labels. Food and beverages, pet food and cosmetics are the main markets served. Label production is another core activity of the company serving a variety of markets with its very wide range of printed and unprinted labels and tags applications.
The recent installation of the Bobst gravure presses is part of Yilpar’s strategic plan.
‘Our policy has been centered on the principles of acquiring the most advanced technology and applying the most stringent quality controls and hiring the best people in their job,’ explained Berk Yilancioglu, COO of Yilpar. ‘Nowadays the main challenges we are confronted with are the economic uncertainties in the domestic market and the shortage of qualified personnel, while in terms of flexible packaging market requirements there has been an increase in the number of short run production, while the overall demand has not increased at the same rate.
‘These factors have had an influence on the choice of Bobst as our gravure press supplier. It is not just a matter of getting the equipment to extend production capacity and provide the kind of print quality required by the highly demanding and competitive food market segment, it must also feature the efficiencies required regarding overall machine operation irrespective of job lengths, which for gravure can be critical with short run production.'
Yilpar’s RS 6003 press entered production during summer 2023 and the company is satisfied with its performance. ‘Press speed and low waste are the main advantages, along with the ease of operation. This is our first Bobst gravure press, but the operators adapted to the machine comfortably. Ease of use and automation make set-ups and changeovers fast and minimize downtime, hence short runs do not impact are no longer considered the “bête noire” of productivity,’ concluded Yilancioglu.
Yilpar’s commitment to making its production facilities ready to fulfil the new demands for sustainable, recycle-ready packaging applications has also played in favor of their choice of Bobst gravure technology.
‘We need to ensure that our equipment can handle the new functional materials that are entering the market to replace non-recyclable multi-materials laminates,' added Altug Yilancioglu, CEO of Yilpar. 'These substrates, be they paper/fibre-based material, or thinner thermosensitive filmic substrates, that are coated with functional layers that need to preserve their barrier properties through the various printing and converting stages of production, present many criticalities.
'Bobst is very advanced in this field where it can offer solutions that have been tested at every stage of the end-to-end production cycle. This makes us confident that our gravure presses will be able to handle efficiently and qualitatively the Mdope and recyclable films that we are planning to print in the future.'
According to the company, the recent investments will help it to increase its current export rate and rank among the top three flexible packaging companies in Turkey within the next five years.
Stay up to date
Subscribe to the free Label News newsletter and receive the latest content every week. We'll never share your email address.