BakPac invests in HP Indigo 200K
First UK production company to house the Indigo 200K.
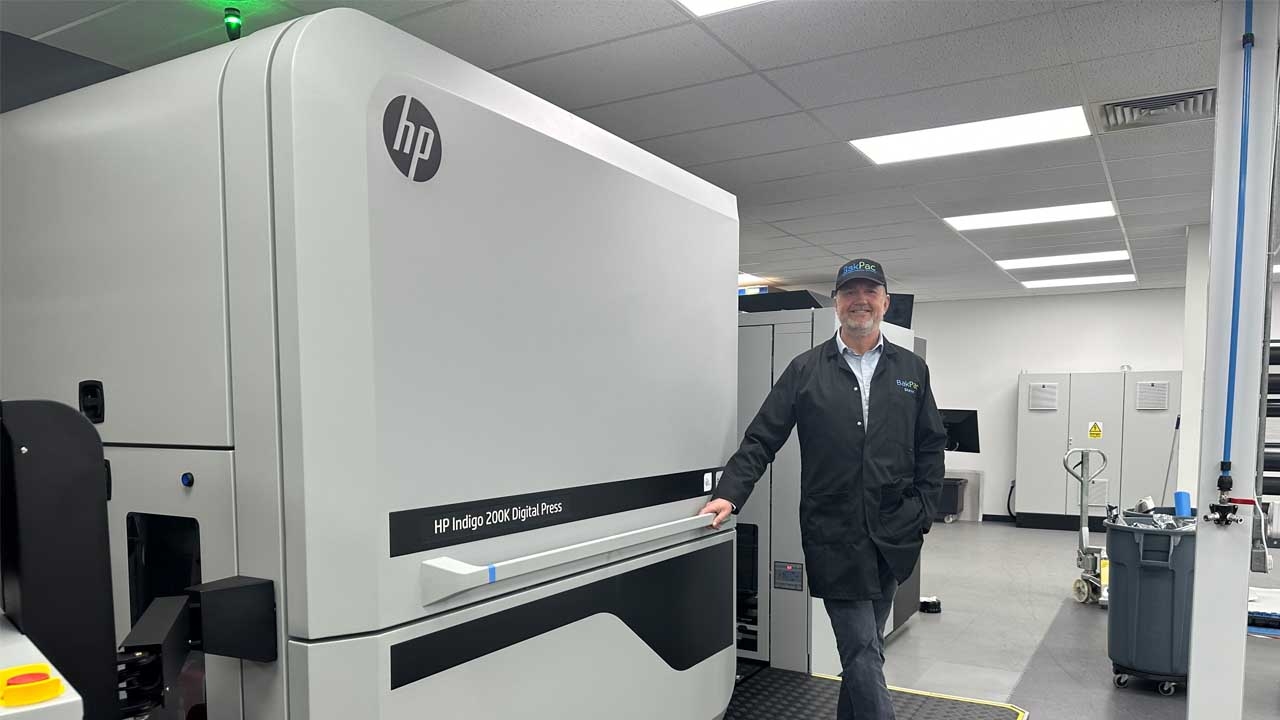
Steve Baker, MD, with his new HP Indigo 200K digital press
BakPac, the flexible packaging division of independent UK label printer, Bakers, has invested in the HP Indigo 200K digital press. The investment is part of BakPac's broader GBP 3 million expansion strategy, including the acquisition of two additional pouch makers and a new production facility in 2024.
This marks a significant step in solidifying BakPac's market share in the growing business of digitally printed flexible packaging.
Stepping into the heart of BakPac's operations, the HP Indigo 200K boasts a 30 percent increase in printing speed and a staggering 45 percent boost in expected productivity. The press enables the converter to achieve quicker turnarounds, efficiency, and the ability to handle diverse printing requirements with ease.
The press offers efficient energy consumption and improved corona treatment for a cleaner, greener footprint. It offers a new writing head laser system for high printing speed and bid motors for color uniformity, consistency, reliability, and lifespan.
The ink delivery system with five dual revolver stations supports 100 percent coverage and non-stop printing.
BakPac is said to be the first UK production company to house the Indigo 200K, also making it an exclusive HP reference site.
The converter can also offer high quantities to its customers with the new press. The ability to handle higher volumes faster extends BakPac's reach, moving the crossover point between digital and flexo and making larger orders more accessible. This strategic move opens doors to a broader customer base, positioning BakPac to offer short run, fast turnaround packaging.
In the era of digital packaging, global trends are reshaping the industry. Small brands are on the rise, demanding agility and responsiveness, while sustainability takes center stage. With the new press, BakPac is poised to meet these demands head-on, offering fast time-to-market, personalized packaging, and eco-friendly products.
Steve Baker, managing director, said: ‘We have been experiencing a growing demand for volume alongside price pressure. We needed a press that was more efficient, reliable and more cost effective. The 200K gives us all of these elements and will help the business grow at a faster rate.’
Baker’s partnership with HP began in 2006 with its first digital label press, the WS 4050. 18 years later and the Indigo 200K becomes Bakers’ 10th HP digital press. The Indigo 200K replaces the 20,000, a pivotal move following the success of BakPac's launch in 2020.
The 200K, while similar in technology, comes with increased capacity and uptime, emphasizing the commitment to the flexible packaging division of the company. The company’s Labels division currently produces with two HP Indigo 6900s and one HP Indigo 6K.
Peter Jolly, HP’s UK and Ireland manager, added: ‘BakPac's investment in the HP Indigo 200K is a testament to the continuous innovation and impact our digital print technology brings to the packaging industry. The HP Indigo 200K is designed to increase productivity and print speed which in turn fosters more opportunity for growth. We are proud to partner with BakPac on our tenth successive digital press together and continue to enable their journey as a pioneer for advancements in flexible packaging and setting standards for efficiency, reliability, and sustainability.’
The HP Indigo 200K also comes with certifications for food packaging compliance with EU and FDA regulations.
A CO2 neutral manufacturing press with third-party studies showing the lowest environmental impact by 40-80 percent, The HP Indigo is also a proud member of Ceflex, actively contributing to the Circular Economy for Flexible Packaging.
The deal for the new press was signed in December 2023. A swift installation in January 2024 marked a seamless transition for BakPac. As current users of HP Indigo technology, HP reported that the team found the shift to the 200K straightforward, keeping any disruptions to a minimum.
Stay up to date
Subscribe to the free Label News newsletter and receive the latest content every week. We'll never share your email address.