The great debate: digital versus flexo
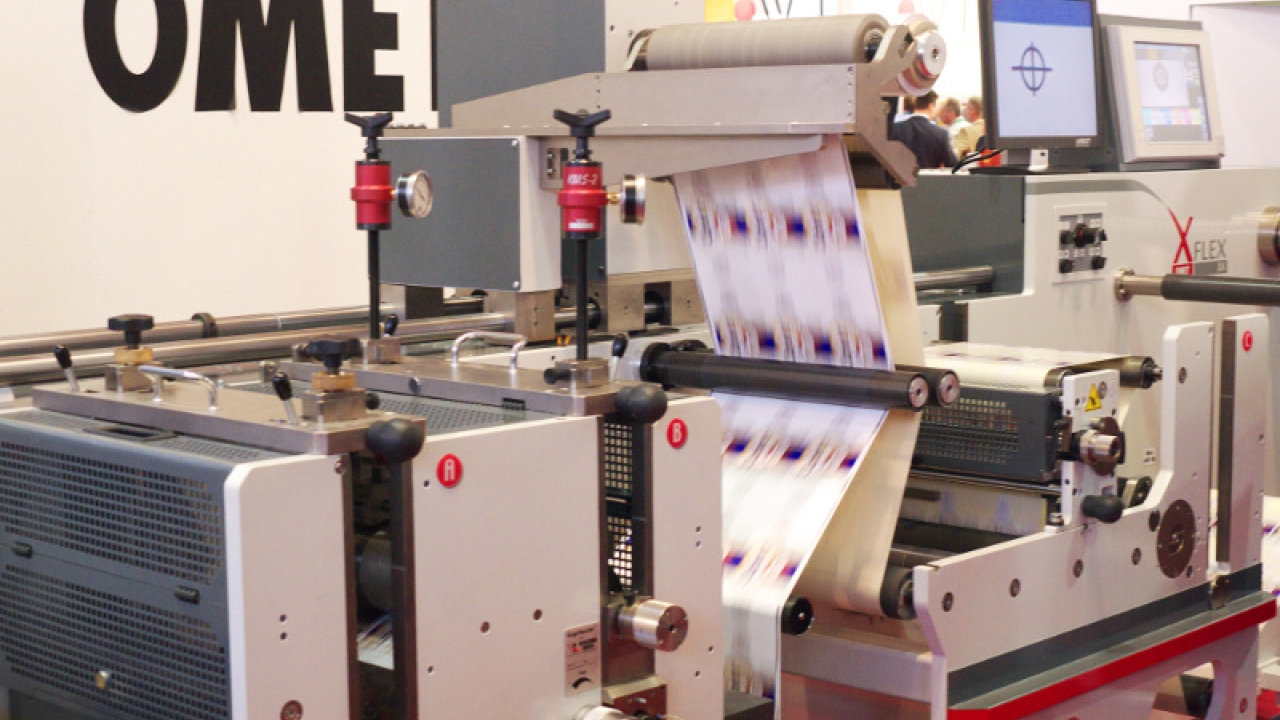
With the rapid rise of digital printing in the labels sector, what impact will there be on conventional printing technologies? Barry Hunt reports
Has digital printing reached a major turning point? Many people think it has, with the lower end of the flexo market being the prime target. Certainly its short-run advantages were well displayed at Labelexpo Europe 2011. The presence of a dedicated hall full of the latest digital printing and finishing equipment, supported by regular digital workshops, speaks for itself. But as seen later, flexo press makers are responding with a new generation of high performance presses designed to handle a wide mix of production runs to high quality levels. Of course, there are many hybrid installations involving one or more digital press running alongside existing flexo or offset presses.
Digital's growth may stem from its efficient handling of short runs, but the real point of differentiation lies with versioning, which is where the real money is. Brand owners and retailers not only want to reduce their label and packaging inventories, they also want a choice of versions, shapes and sizes for individual orders. As Sean Skelly of EFI Jetrion described it, 'Some of our customers often quote for quite large jobs which are broken down into many different Stock Keeping Units (SKUs). Versioning is therefore the “sweet spot” of our business and a source of huge opportunities for our customers.'
With over 1,200 label presses installed worldwide, HP indigo says it has installed more presses in the past two years than any other press manufacturer. Its latest offering, the 7-color WS6600, prints high quality, full-color labels and shrink sleeves at 40 m/min. The WS4600 entry-level version has an option for full-color throughput at half that rate. Alon Bar-Shany, vice president and general manager, said these high performance presses extend the economic break-even point between digital and flexo: 'Narrowing the gap with mid-level flexo could allow users to improve their margins over conventional methods when handling print jobs of 50,000 labels or more.'
With a 500mm web width, the Xeikon 3500 with an in-line DCoat500 finishing line, breaks new ground as part of a revamped 3000 Series. Xeikon showed the flexibility of digital printing with a new two-stage heat transfer process. As an alternative to direct printing or in-mold labeling, it decorates containers, flexible seamless tubes, aluminum closures and similar articles. The company also promoted some security-related applications for its dry toner technology. The new VariLane plug-in for the X-800 Digital Front End allows operators to quickly create imposition schemes for versioned jobs and avoid materials wastage.
The inkjet diversity
Single-pass CMYK inkjet printing adds another dimension to the digital debate, although with around 30 competing systems the picture is confusing. Products range from entry-level desktop devices to faster, industrial presses designed to challenge flexo in certain markets. The presence of around half-a-dozen leading OEM manufacturers of drop-on-demand printheads has injected valuable R&D support at all levels. 'Inkjet is now an accepted technology, with more refined printheads and improved UV-curable inks', said Mark Alexander, Xaar's marketing director. 'Based on current developments, we can look forward to wider substrates and improved productivity, while LED curing with its lower energy is another important development.'
These, and existing developments have encouraged the industrial inkjet vendors to target key flexo markets. Uniquely, EFI Jetrion offers an end-to-end approach with the new 4900 press that includes dual-head laser cutting, backed by a web festoon, slitting and automatic turret rewinding. Its Xaar 1001 printheads print CMYK, plus an opaque white. Durst has gone for the eight color option with the new Tau 150-8C (CMYK, plus white, orange and violet). It prints at up to 48 m/min (157 ft/min) and has optional digital varnishing with different gloss levels. It is also fully integrated with Durst's Rotoworx 330 off-line finishing module with semi-rotary die cutting of all short-run labels.
Domino Printing Sciences also openly pitches the N600i inkjet press at flexo printers. It operates reel-to-reel or with an optional digital finishing station using a dancer roller web infeed. The 333-mm wide (13 inches) press uses Kyocera KJ4 piezo printheads to print paper or filmic labelstocks up to 50 m/min (164 ft/min) with four grayscale levels or 75 m/min (246 ft/min) with three grayscale levels.
Stork Prints' DSI press can run with its Rotary Screen Integration (RSI) technology. Printing at up to 720 sq/m hour it delivers resolutions of up to 1,000dpi, as well as 3D effects that resemble screen printing. Besides CMYK, users can add additional printheads to obtain digital white, digital primer to enable printing on machine-coated paper, and extend the color gamut.
Among the top-end machines, Epson's SurePress L-4033A is aimed at the premium label market using water-based CMYK, orange and green inks, with an overprint coating in widths from 80mm to 330mm. Epson's Micro Piezo variable-size droplet technology delivers a native resolution of 720 x 720dpi to give smooth vignettes and sharp text on textured and coated grades, with no surface priming required. However, multi-pass printing restricts speeds to five meters per minute.
Still room for analog
Flexo press makers have responded by automating the main press functions and simplifying the overall operation. Of course, unlike stand-alone digital presses, the die cutting, foiling, varnishing and other finishing processes are handled in a single pass. It is also possible to integrate variable data and encoding modules. Furthermore, installations are supported by prepress workflows, with options to include closed-loop inspection and job data reporting and storage to a MIS facility. Some presses can now run with plate cylinders with diameters of just 140mm to increase the range of repeat sizes and reduce ink costs.
The benefits of increased productivity levels with lower start-up waste were stressed during timed press demonstrations at Labelexpo. Omet, Mark Andy and Nuova Gidue for example featured impressively fast substrate changes, with plate and ink cylinder changeovers measured in just a few minutes. The facility to quickly achieve perfect color register from idling to speeds of 150-200 m/minute was another breakthrough.
Mark Andy is among those who maintain that the latest flexo presses can now handle the type of short-run jobs that were previously considered as uneconomic. It claims the web path design, plus advanced registration capabilities, in the P3, P5 and P7 Performance Series can reduce set-up waste by around 60 percent over conventional in-line flexo technologies. Set-up of a 4-color job takes just under two minutes and a single station set-up in less than 30 seconds. A load-and-lock inking system, self-positioning doctor blades, easy-to-operate controls and open access are said to contribute to simple operation, regardless of skill level.
Most of today's servo-driven flexo presses feature shorter web paths. An example is Gallus's redesigned EM 430S with an enhanced control center. The web path between print nips is halved to 2.2m to achieve faster response times when adjusting register, as well as reducing wastage. MPS's EC flexo series includes driven chill drums and a shorter web path, backed by MPS's Automated Print Control to automatically set print pressures, settings for the UV curing, corona treatment and web tension for storage in a job repeat memory.
New productivity features from Nilpeter for the servo-driven FB-3300S modular UV-flexo press include a new type of anilox system with an open/close doctor blade chamber to obtain clean and easy job changes. The company's Revolver Die System allows operators to load successive solid tooling, or magnetic flexible die plate cylinders, into the module and index them within seconds. It is also available for Nilpeter's MO-Line offset combination and FA-Line flexo presses.
Omet's new XFlex X4 flexo press, derived from the established XFlex X6, uses similar electronic set-up and register control features with conventional plate cylinders. UV lamps mounted on the chilled impression cylinders provide short and straight web paths (145cm between units). Inline finishing includes an interchangeable hot foil module and waste-extraction unit. A highlight of Labelexpo was a Varyflex V2 shown with an upgraded Vision-2 register control system. It now employs PC-controlled high-resolution color cameras on all print units instead of a single end-of-line head.
Interestingly, Nuova Gidue's new Master M5 flexo combination series for multi-substrate production offers interactive links with users' MIS/JDF systems. Its so-called Digital Flexo technologies include a HD digital camera for controlling register deviation and dot gain. Another version controls print pressure and register according to the PDF/TIFF file, supported by seven servo units for each print unit.
Edale's new servo-driven FL-350 typifies a new breed of fast UV flexo presses for producing film or paper labels, tickets and packaging in a caliper range from 30 to 450 microns at up to 200 m/min. The Pit Stop Colour Change facility allows plate changes in under two minutes per print unit.
As can be seen, press manufacturers are meeting a real or perceived threat from the latest digital presses with some innovative features. As with the development of UV flexo presses, this could mean machines with wider webs and faster production speeds in a few years time. That will stir things up even further. But no single technology offers all the answers, least of all inkjet. As always, it comes down to individual converters attempting to define their future objectives in meeting customers' demands and doing their best to ensure that the capabilities of any chosen technology can achieve them.
Pictured: Flexo press manufacturers are looking to reduce waste and changeover times to compete with digital, as with Omet’s new Xflex X4
This article was published in the L&L Yearbook 2012
Stay up to date
Subscribe to the free Label News newsletter and receive the latest content every week. We'll never share your email address.